We are announcing today the winners and finalists of the third Protolabs Network Student Grant. The grant had another exceptional reception from students all around the world, submitting diverse projects spanning from engineering and product design to robotics and art.
The applicants competed in five categories: Product Design, Robotics, Sustainability, Transportation and Healthcare. The winners of each category will receive $1000 to further develop their project as well as technical support from Protolabs Network to turn their idea into a real product.
The Judging Panel
The Student Grant 2019 judging panel consisted of three industry experts with long experience in the area of 3D printing:
- Daniel Buening, Ph.D. (Chief Innovation Officer at BigRep and Managing Director of NOWLAB)
- Sarah Goehrke (Owner of Additive Integrity, Managing Editor at Fabbaloo and Board Director of Women in 3D Printing)
- Ben Redwood, Ph.D. (Director of Sales and Business Development at Protolabs Network and author of The 3D Printing Handbook)
The submissions were assessed based on three criteria: presentation, innovation and potential impact, and justification of the use of 3D printing. Sarah Goehrke commented on her experience judging this years’s submissions:
"I've long been a fan of the Protolabs Network Student Grant and the opportunities it affords to highlight and further student work. Some truly impressive projects have been boosted in previous years, and it was an honor for me to be asked to join the jury for this year's grant. The finalists made scoring a very difficult process, as so many high-quality submissions are very deserving of recognition. Initiatives like this grant are wonderful to put the next generation's work in the spotlight and encourage further development through their awards."
The breakdown
This year we received nearly 200 submissions from students from over 100 Universities and high schools from all around the world. The applicants were able to submit their project for consideration in up to two categories. Product Design was by far the most popular category collecting nearly 75% of all applications. It was followed by Sustainability (32%), Healthcare (25%), Robotics (19%) and Transportation (10%).
The 3D printing processes that the students used to bring their projects into life are broken down in the table bellow. The students were allowed to use a 3D printing service, the in-house manufacturing capabilities of their institutions or custom 3D printers developed specifically for their project.
3D Printing Process Used | Percentage of Total |
---|---|
FDM 3D Printing | 72% |
SLA 3D Printing | 24% |
SLS 3D Printing | 13% |
DMLS 3D Printing | 8% |
Polyjet 3D Printing | 6% |
As for the software the students used to create their designs, Solidworks and Fusion 360 were the most popular, chosen respectively by 33% and 28% of all applicants. They were followed by Rhino (19%), AutoCAD (11%) and Grasshopper (9%).
Product Design Winner

Project Name: ONE Shoe
Name: Davide Amorim
University: Eindhoven University of Technology (TU/e)
Project Description
People are all different. However, people with the same foot size, but with different body weight, or foot shape, often wear the same shoes. By making use of Mechanical Meta-materials Structures (MMS), it is possible to create a sole that not only fits a person foot’s needs but also makes it easy to recycle. MMS allows achieving multi-properties within one material compound (e.g stiff, soft or deformation). This results in benefits for both users (personalization) and society (sustainability).
Why did they use 3D printing?
Due to its complex geometry, MMS could only be fabricated through the use of 3D printing technology. In addition, combined with the parametric design while embedding users’ foot data through the process, it enables creating personalized shoe soles that follow the natural deformation of the user’s foot. MMS can also be explored in the use of many other products such as protective equipment, or prosthetics. 3D printing is the ultimate method of manufacturing that enables product personalization.
Honorable mentions
The following two projects received an almost identical score from the judges as the winner, and thus they deserve an honorable mention:
- Aero - Ajharul Choudhury - Brunel University
- Thrive Wireless Valve Switch - Seth Paulo Bangerter - Brigham Young University
Product Design Finalists
Here are the other finalists in this category (in no particular order):
- TypeCase - Dougie Mann - Imperial College London
- SENSEI - Oscar Oomens - HAW Hamburg
- UME, an emotive testing headset - Oliver Aldous - Loughborough University
- Twin Climbs - Nicholas Gilmore - UNSW Sydney
Robotics Winner
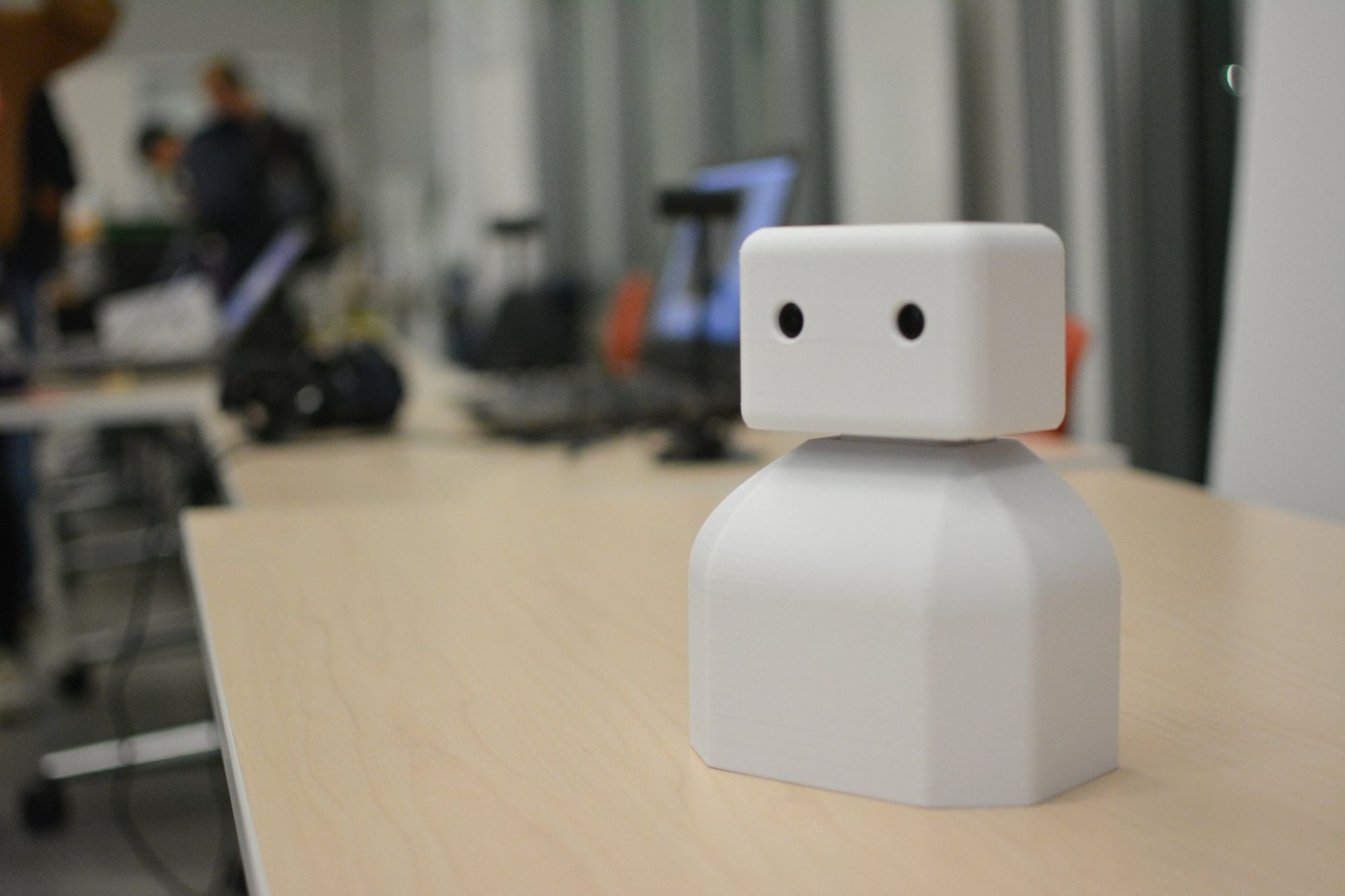
Project Name: Teleport
Name: Akhil Padmanabha, Rishi Upadhyay, Nicholas Liu, Steven Chen, Samuel Chen
University: University of California, Berkeley
Project Description
For a child suffering from a debilitating illness in a hospital, normalcy and crucial social interactions are taken away abruptly, leaving them emotionally vulnerable, anxious, and lonely. Teleport aims to tackle this problem by providing 3D printed robotic avatars. Unlike avatars on the market, Teleport facilitates customization and a virtual reality experience. We have finished a prototype and received the Berkeley Haas Social Venture Fund Resource Award, and are collaborating with NVIDIA.
Why did they use 3D printing?
FDM printing was the ideal process for Teleport due to our access to free Ultimaker 3’s at UC Berkeley. The Ultimaker’s allowed us to print quickly, while still maintaining high resolution. The rapid, cheap FDM printing will additionally make it easier to scale up and have a greater, widespread impact. We chose PLA, because as a bioplastic, it is 100% safe to young children and can also be easily painted on with non-toxic acrylics, which would allow children to personalize their robotic avatar.
Robotics Finalists
Here are the other finalists in this category (in no particular order):
- Gripper Tool for Surgical Collaborative Robot - Emma Andersson - KTH (The Royal Institute of Technology)
- Flexible Robotic Advanced Manufacturing Cell for 3D Metal Printing - Zachary Lewis - McMaster University
- Soft-Actuated Material: A flexible approach to architecture and its production - Lynn Kieffer - The Royal Danish Academy of Fine Arts
- The Meat Market - Barbara Schickermueller - University of Applied Arts Vienna
Sustainability Winner
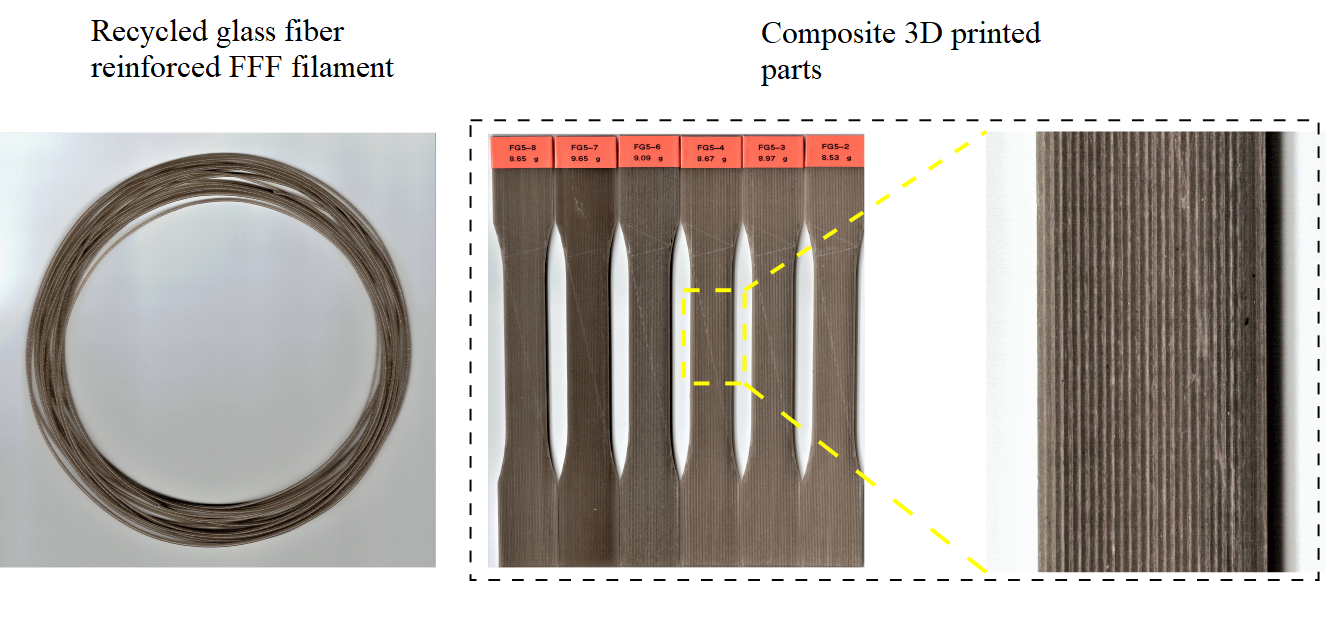
Project Name: Recycling Wind Turbine Blade Fiberglass into Reinforced Filaments
Name: Amirmohammad Rahimizadeh
University: McGill University
Project Description
Due to the limited lifespan of wind turbine blades, it is expected that the number of scrap blades will explode in the next two decades. This project aims to develop a new process that improves the 3D printed composite products and at the same time provides a sustainable recycling solution for scrap blades. With the growth of both the wind energy sector and 3D printing industry, it is expected that there would be great economic benefits resulting from the successful completion of this project.
Why did they use 3D printing?
The recycled glass fibers tend to retain a significant amount of epoxy residue on the surface. The epoxy resin is characterized by the possession of more than one 1,2-epoxy groups per molecule, which are highly reactive with many substances, particularly those that are known as proton donors such as PLA. Such reactions allow for molecular chain extensions, which can improve the interfacial strength between the PLA and the recycled fibers without the need for expensive thermal processes.
📍 Download our free engineering guide for 3D printing here
Sustainability Finalists
Here are the other finalists in this category (in no particular order):
- de gradus. - Joanna Maria Lesna - The Royal Danish Academy of Fine Arts
- Ina Lite - Obasogie Okpamen - Landmark University
- Santa's Workshop - Daniel Smothers - University of Memphis
- 3D Printable CO2 Absorption Column - Nick Kalogeropoulos & Pierre Walker - Imperial College London
Transportation Winner
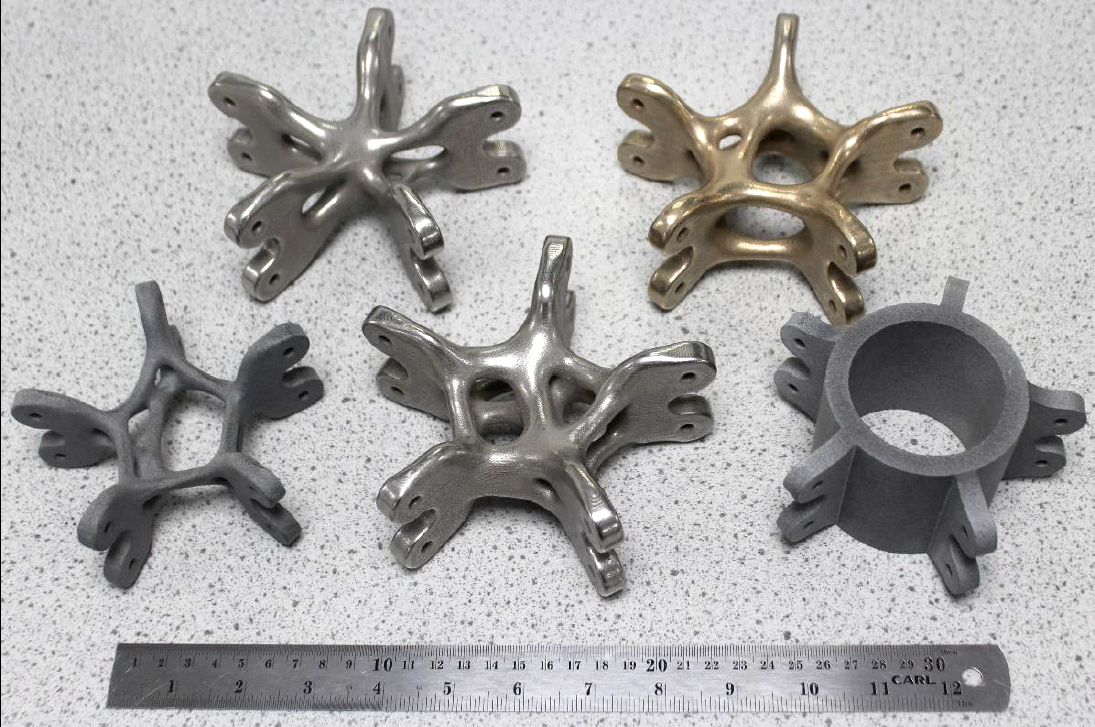
Project Name: Optimized Metallic Code-Connections for Reticulated Structures
Name: Moustafa Abdelwahab
University: University of Leeds
Project Description
This project used 3D printing to fabricate bespoke & intricate connection designs for 3D space structures which have shown their significance through obtaining substantial weight reductions for the same structural capacity as the typical ones. The overall vision of this research is to encourage the adoption of freeform, function-driven designs in the construction industry which could lead to weight reductions along with improved aesthetics, allowing for more nature inspired designs.
Why did they use 3D printing?
The fabrication of the connection prototypes using DMLS showcases the capability of 3D printing in producing intricate shapes and its advantage in eliminating many of the traditional manufacturing constraints. The 420 Stainless Steel alloy was adopted to allow for a direct comparison with the typical Stainless Steel connections and the FEA computer models, and to allow for future experimental testing of the bespoke 3D Printed connections.
Transportation Finalists
Here are the other finalists in this category (in no particular order):
- PTS - Personal Transportation System - Sunny Duseja - Strate School of Design
- Redesigning the AlfaRomeo Twin Spark CON ROD using topology optimization - Okpamen Obasogie - Landmark University
- Mazda Yajirushi - Nikita - Strate School of Design
- Micro Jet Engine (Gas Turbine Engine) - Gitesh Nayyar - NIT Jalandhar
Healthcare Winner
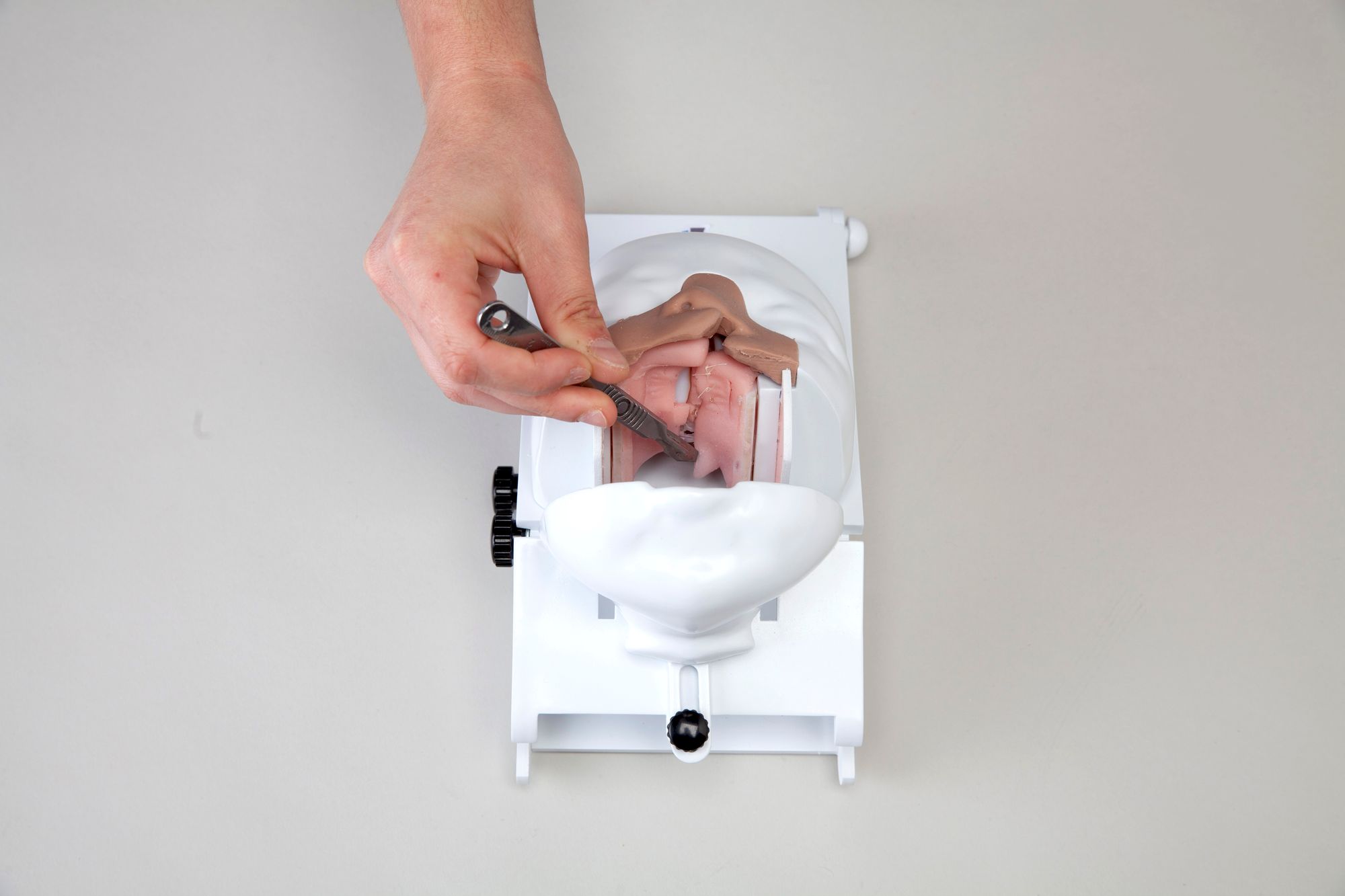
Project Name: ReCleft
Name: Rute Pereira Crespo Fiadeiro
University: Brunel University of London
Project Description
Cleft lip and/or palate (CLP) affects 1 in every 500-700 births. Errors in surgery may lead to complications with serious consequences for the patient. It is estimated 250,000 infants are born with CLP in low resource countries each year and it is estimated that a significant proportion are not repaired due to a lack of local cleft surgeons. ReCleft is a silicone and/or bioplastic re-usable training simulator that provides surgeons with moulds and materials to manufacture simulators in-situ.
Why did they use 3D printing?
3D printing was used to test and refine the anatomical structure of the model throughout the project. In each iteration, eight cleft palate with the different anatomical features would be printed. Following this, each part would be cast to make silicone moulds to produce the simulators. Polyjet (Object 500) printer with VeroWhite, printed in matt, proved to be the best printing choice due to the high definition, finishing and compliance with silicone. The head and bone were also 3D printed.
Healthcare Finalists
Here are the other finalists in this category (in no particular order):
- Fabrication of a Magnetic Rotablation Capsule for the Treatment of Arterial Stenosis - Christoff Marthinus Heunis - University of Twente
- Regrip - Jennifer Smyth - Birmingham City University
- Framed: stepless customization of transtibial prostheses - Pauline Temme - Bauhaus University Weimar
- 3D Printing Teeth for Teaching - Alexander Cresswell-Boyes - Queen Mary University of London
Thanks
The quality and breadth of the projects we received was once again impressive, making the job of our judges more difficult than ever. We would like to thank all students who participated in this year’s Student Grant and we are looking forward to supporting you in your next steps and future endeavours.
Filemon Schoffer, co-founder and CCO of Protolabs Network, commented:
“We are excited to support the efforts of ambitious students who want to turn their projects into reality. Our goal is to give them easy access to state-of-the-art manufacturing, so their ideas are not restricted. The Protolabs Network Student Grant showcases how engineering and design talent will push the industry forward in the years to come.”
Applications for the Protolabs Network Student Innovation Grant 2020 are now open to all registered students and recent graduates across the world. Start applying today via our submission form.
The deadline for submissions is on June 28, 2020, 23:59 CET.