Warwick Acoustics & Protolabs Network | |
---|---|
Organization | Warwick Acoustics |
Location | Nuneaton, UK |
Industry | Audio |
Product | Headphones |
Technology | CNC machining |
Materials | Aluminum alloy AZ31B, stainless steel 316L |
Why us? | Clearer, faster communication with the supplier |
Warwick Acoustics’ headphones are above and beyond today’s standard, turning the traditional speaker design on its head. Rather than taking the traditional approach of using a heavy magnet and a coil that alternately attract and repel, and making a cone vibrate in order to create sound, Warwick Acoustics has opted to build an electrostatic speaker.
It’s a system others have attempted, but in the past has resulted in large, heavy speakers with little control over low frequencies that deteriorate over time. Warwick Acoustics overcomes these issues by creating a patented cellular structure that produces sound reliably.
Next generation headphones
In the place of the magnet that moves backward and forward, Warwick Acoustics uses a very, very thin diaphragm film - thinner than a human hair.
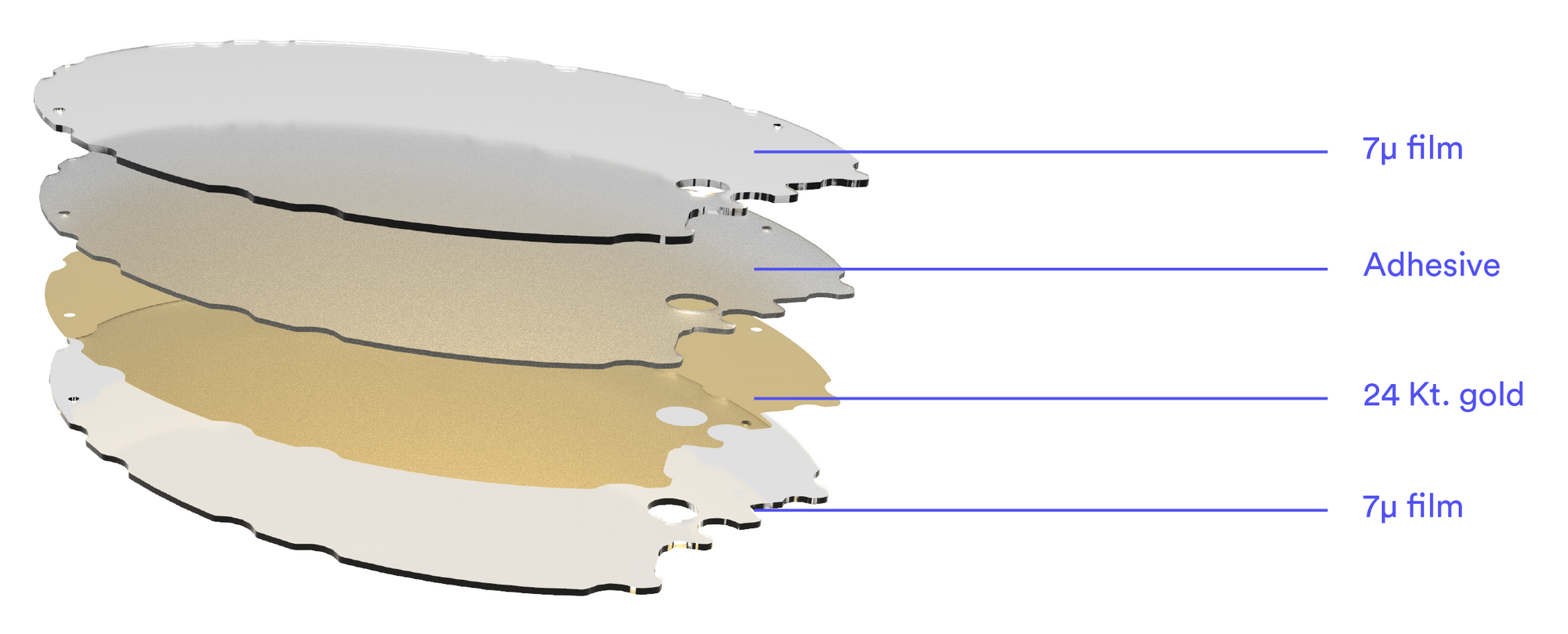
The light weight of this film means the speakers are more true to the sound. In a traditional speaker, the heavy magnet results in a slight delay, often blurring and smudging the sound. Because of the light membrane, Warwick Acoustics’ headphones produce a more “transparent”, cleaner sound.
“The example often used to describe this transformation is LEDs versus traditional light bulbs,” explains Ben Lisle, Principal Mechanical Engineer at Warwick Acoustics. “The LED is the next generation. It has all the advantages of a light bulb, but with lower power, brighter light, and no heat emitted. It’s the same with our headphones: they offer everything traditional headphones can but with a cleaner sound, much lower power, and low heat emission.”
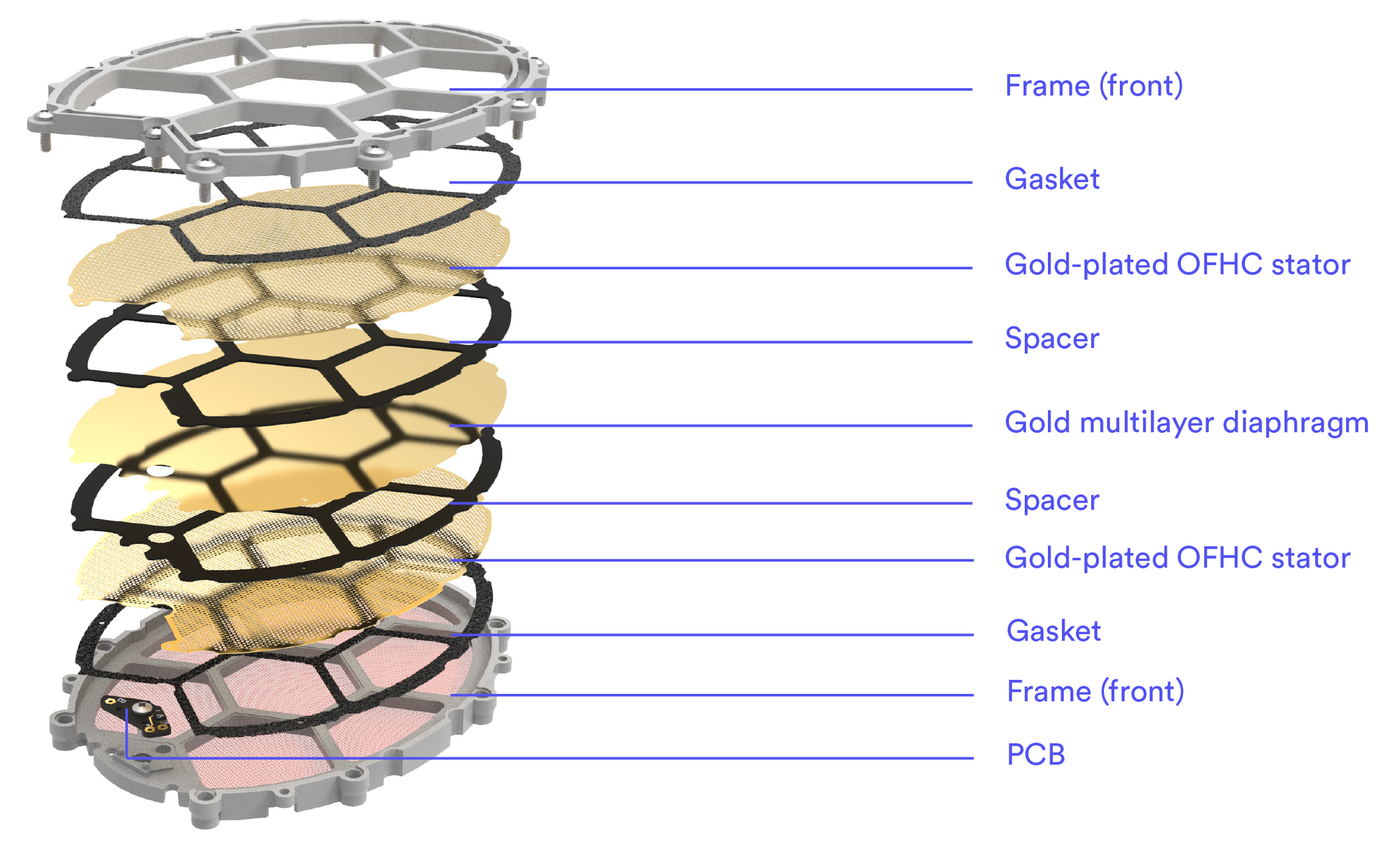
To make the electrostatic speakers reliable, Warwick Acoustics have created their self-coined Balanced-Drive High Precision Electrostatic Laminate (BD-HPEL). The diaphragm is centered between 2 thin, high-precision electrical stators using polymer spacers, laser-cut in house.
Each stator is made from oxygen-free copper (OFHC), which is subsequently gold-plated, materials selected for their high electrical conductivity, resistance to corrosion and premium aesthetics. The entire assembly is built into a high-precision frame, which ensures the assembled transducer is held completely flat and is invulnerable to warpage or bending.
Creating the outer casing
To produce the major structural components that form the body of the headphones, Warwick Acoustics largely used CNC machining through Protolabs Network.
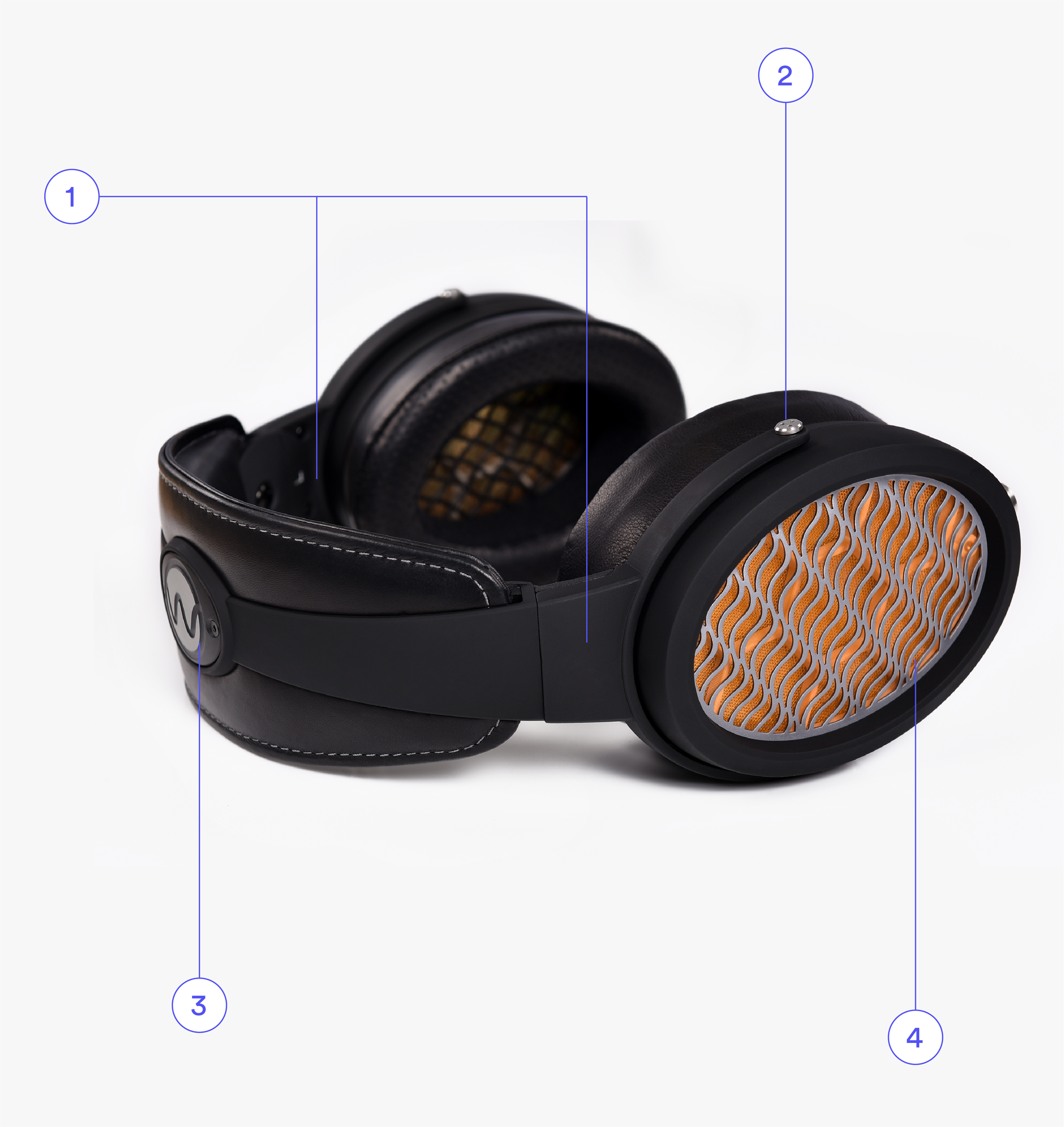
- The yoke and the parts where the L and R are written are manufactured using magnesium AZ31B alloy with a black powder coating. Magnesium was selected for its lighter weight. A lot of other premium headphones on the market weigh half a kilo or more, which can feel very heavy on someone’s neck over time. By using magnesium, you can take that weight down to around 400g.
- Key structural fasteners and screws are also made with stainless steel 316L for strength and durability.
- Aluminum 6061-T6 is used for the badge, a material chosen for how light and easy it is to machine, even into relatively complex forms, like Warwick Acoustics’ logo on a curved surface. The badge was bead blasted and anodized to create a stylish textured, matt finish.
- The S-shaped grills, produced in stainless steel 316L, feature complex curves that have been pressed to increase rigidity and aesthetics.
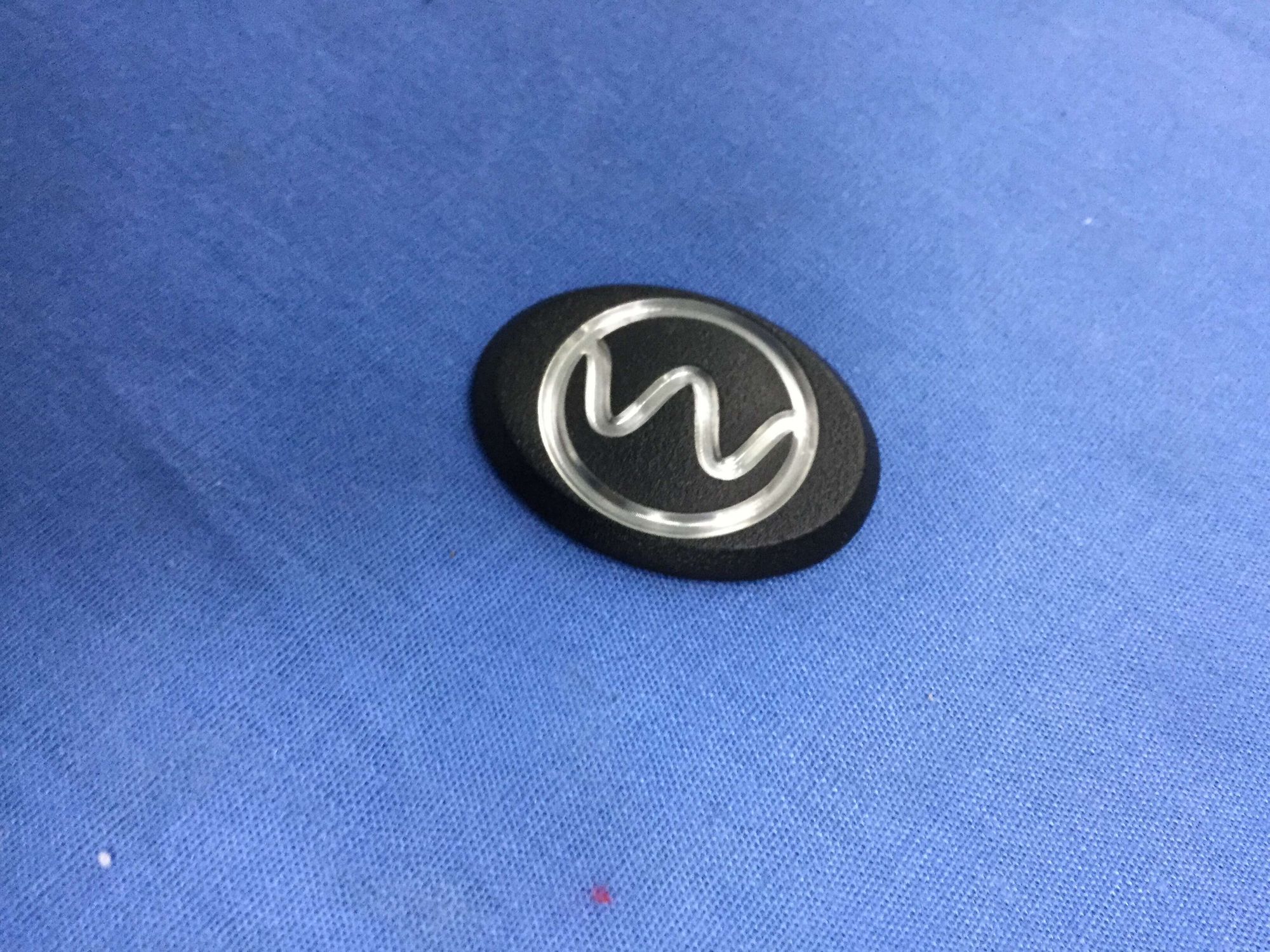
📍 Download our free engineering guide to CNC machining here
Getting parts cheaper, faster and with less headaches
Originally, Warwick Acoustics worked directly with suppliers to get out-of-house parts manufactured. But because of trade conflicts and difficulties in communication, Warwick Acoustics often experienced delays getting parts into production. Also as a smaller company, compared to huge enterprises ordering hundreds of thousands of parts, they had to fight to get to the top of the supplier’s priority list.
Because of these problems, Warwick Acoustics looked to switch to a supplier base located in Europe and came across our online manufacturing platform. With our network, the Warwick Acoustics team can easily communicate in English in the same time zone, track and trace their orders, and be confident their parts are being produced.
This means Warwick Acoustics can produce and iterate parts faster. “As a company we’re growing quickly,” shares Ben, “producing technology that’s cutting edge, and the network has been able to help us do that quicker, cheaper, and with far fewer headaches than before.”
“As a company we’re growing quickly, producing technology that’s cutting edge, and the network have been able to help us do that quicker, cheaper, and with far fewer headaches than before.”
- Ben Lisle, Principal Mechanical Engineer at Warwick Acoustics
Choosing the platform also had some added bonuses. “Where you’ve impressed us is the design verification stage you can add to an order,” says Ben, “with this prototyping service, we’re able to look and review one part at the same price as if we’d ordered it as a part of the full quantity. It’s been a real help validating the finish and fit of our components in a cost-effective manner.”
Read more customer stories:
- Manufacturing a fleet of drones to scale reforestation
- Learn how Kepler rapidly went from a sketch on a napkin to a satellite in space with our CNC machining
- How Skelex manufactures their industrial passive exoskeletons on-demand
Or upload a part to our platform to get an instant quote.