The challenge
Maritime vessels, from inland ships and dredging vessels to smaller navy boats and tugs, all face a similar challenge. Operators aboard these vessels have a lot of information to process and rely on audio and visual input. To make maritime operations safer and more efficient, Smart-Ship uses a different sensory channel. The company implements haptic feedback in consoles and levers to convey signals to improve navigation.
One of the key challenges is to find manufacturers that can produce pristine components for communicating with humans via vibration without fault. This is where we have been a big part of Smart-Ship’s voyage.
How we helped
We brought Smart-Ship from the prototyping stage effectively to market by providing high-quality, tightly toleranced parts to fulfill the company’s expectation of incredible precise haptic feedback. Throughout the design and production processes, Smart-Ship leveraged our quote builder to save time and money on each product iteration. Collaborating with us has helped Smart-Ship provide the maritime industry with a robust solution to operational safety and fuel efficiency.
Innovating for the Royal Netherlands Navy
Delft-based maritime tech startup Smart-Ship was founded in 2018 by brothers Brent and Roy Kok. As a student at the University of Delft, Roy was developing force feedback technology controls for ships as part of his master’s thesis. This was in response to a very unique challenge faced by the marines in the Royal Netherlands Navy.
The specific vessels they were focusing on could travel at speeds of 40 to 50 knots through high-wave conditions, which could significantly and adversely affect the crew. If an operator can’t act fast enough, their speedy vessel may hit a wave head-on, which is incredibly unsafe for operator and ship alike. So, marines consistently face injury aboard ships due to this dangerous mix of high speeds and choppy conditions.
Roy’s thesis posited that haptic feedback was a safer and more intuitive way to convey information to marines and ship operators. Based on the speed of the ship and data on incoming waves, haptic feedback could advise safer speeds, significantly improving the well-being of ship operators.
Seeing an opportunity in the market, Roy and Brent came up with the idea to transform this thesis concept into a startup, and not long after, Jelle Tiemensma joined as CTO. This case study takes a deep dive into how Smart-Ship transformed an academic concept into a functional prototype and how we were an active manufacturing partner from the beginning.
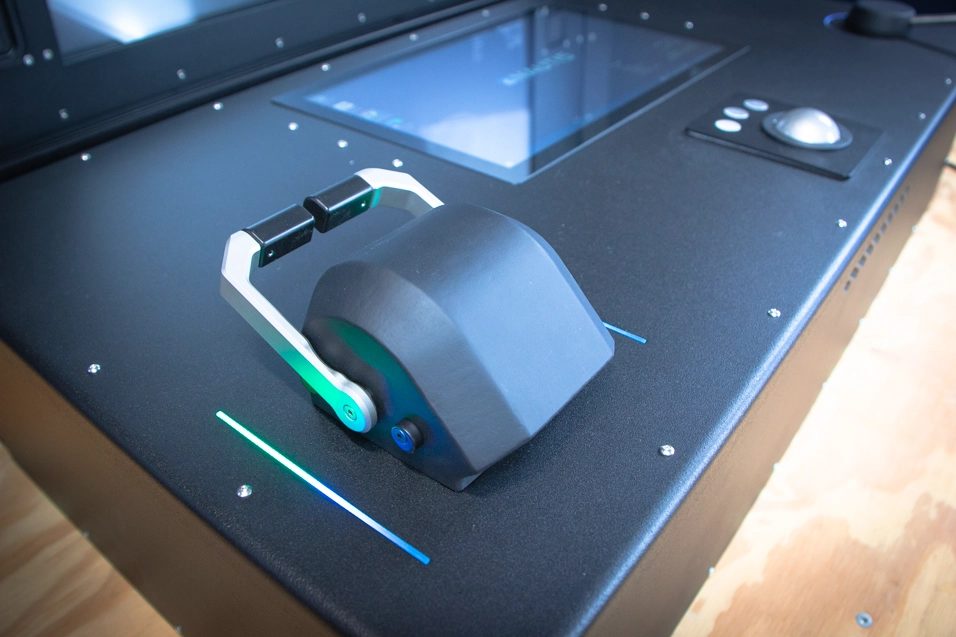
From simulator to onboard application
Smart-Ship’s original vision was to install its innovative haptic consoles and levers directly onto marine vessels. However, according to Tiemensma, the team soon discovered that this involves jumping through countless regulatory hoops.
“To get a lever aboard an actual ship, there are a lot of rules and regulations involved,” says Tiemensma. “It also involves a lot of testing to get it right for insurance and certification purposes.” This means that the Smart-Ship team needed a way to stay afloat while going through this lengthy process.
The solution that Smart-Ship landed on was to integrate its innovative levers and software into maritime training simulators. Marines in training, as well as any ship operator across various sectors, could use these simulators to get a feel for what it’s like to use haptic feedback to support safer, more efficient ship navigation.
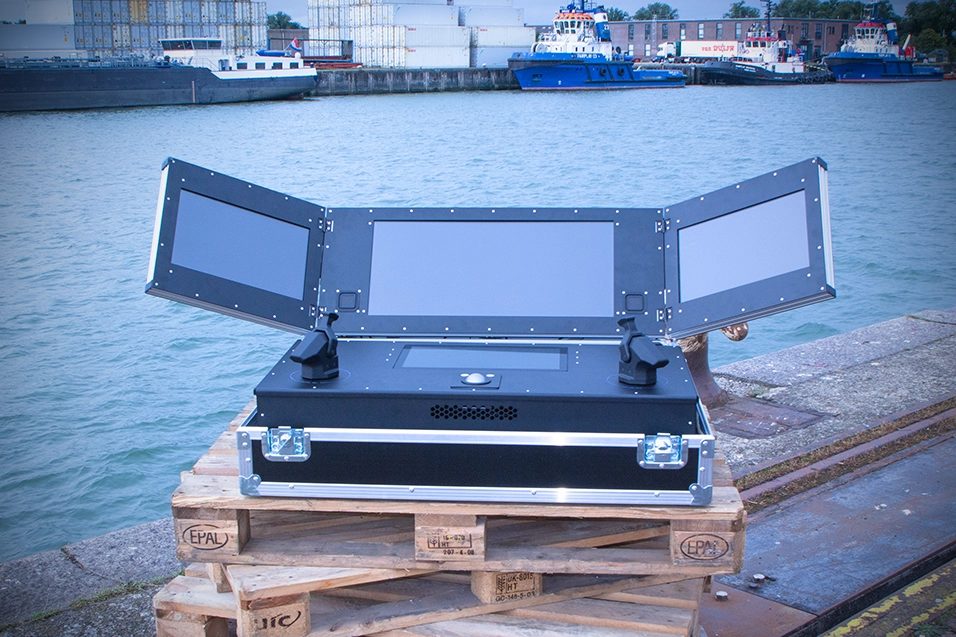
“Our product helps make this training better and more efficient,” says Tiemensma. “We give trainees all the missing sensory information you’d normally get on a ship.”
For both the onboard product and the simulator, parts comprising these technologies have to be incredibly precise to give trustworthy haptic feedback while being comfortable to operate over prolonged seafaring journeys (or simulations of them). To manufacture components fitting those tricky parameters, Smart-Ship found a partner in us.
Manufacturing for haptic precision
When Smart-Ship first started, the team had no hardware or software to speak of, equipped with only the idea of haptic controls. According to Tiemensma, “we had to develop everything from scratch.”
To prototype the levers, Smart-Ship wanted to 3D print components but didn’t have one in-house. So, the company approached us to support its rapid prototyping efforts. Tiemensma recalls, "It was a really good way to get a feel for how everything would fit together and if it was even going to work."
Starting with FDM-printed components from PLA and other more cost-efficient materials, Smart-Ship has gone through each of its development stages with us as its manufacturing partner. And while all the parts composing the product have to be machined to pass lengthy certification processes for seaworthiness, the trickiest components to produce are the ones that convey sensory information.
“Haptic feedback requires us to have really precise parts,” says Tiemensma. “Any bump or scrape on the physical component can mingle with the feedback we provide. We’re doing this at really high frequencies to make the operator able to respond reflexively and intuitively.”
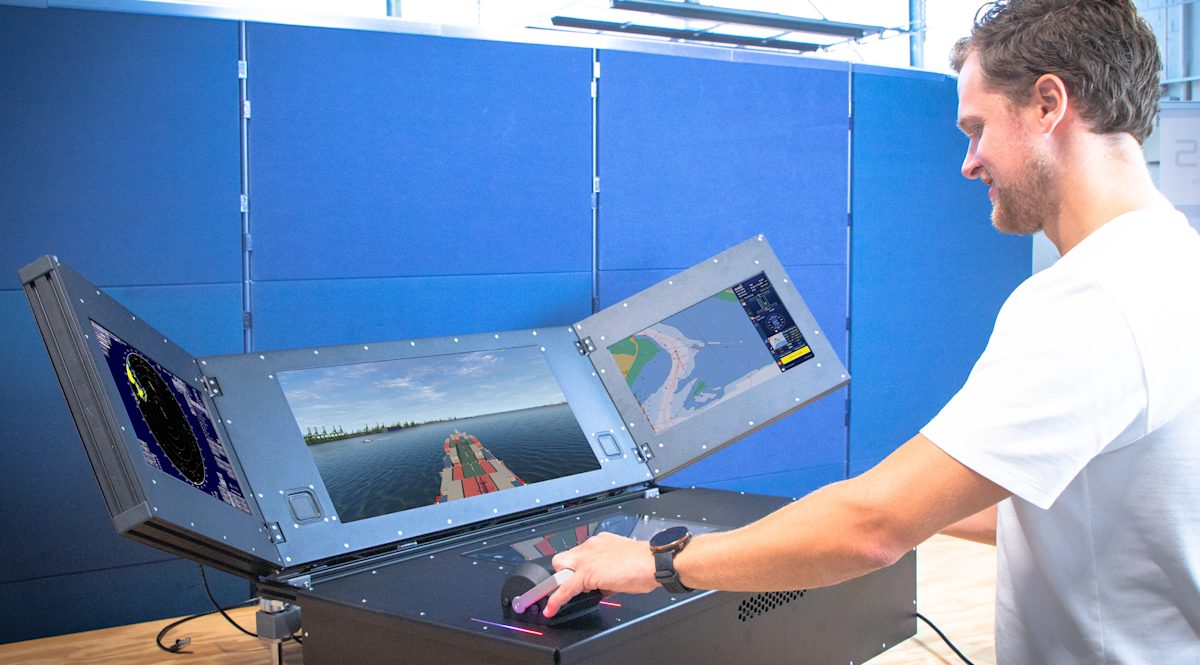
To achieve the precision and high tolerances required, we relied on SLS 3D printing. This technology can produce smooth surface finishes without any potentially distracting blemishes, which is optimal for this sort of handheld component. SLS parts are also quite robust, which means they fit together well with the rest of Smart-Ship’s components, mostly manufactured with CNC milling and turning.
Our network also produced a wide variety of high-mix and robust functional CNC-machined parts for the internal components of Smart-Ships console, levers and simulators. As Smart-Ship’s part orders were quite varied in the kinds of parts to be manufactured, the quote builder was especially useful as a tool to iterate on designs for price optimization.
Since the early stages of product development, we have helped Smart-Ship prove the efficacy of its solution quicker while providing parts that match nautical safety requirements.
“Working with the network has been really good so far,” says Tiemensma. “I really like that with the quoting tool you can see prices directly and how things affect those prices without having to constantly email back and forth with suppliers.”
In parallel to using the quote builder to swiftly check part pricing, Tiemensma and the team have also benefited from our DfM expertise and guidance. According to Tiemensma, “there’s always going to be something you miss when you’re focused on certain aspects of designing the product. Our DfM has been a great sanity check to ensure components are producible.”
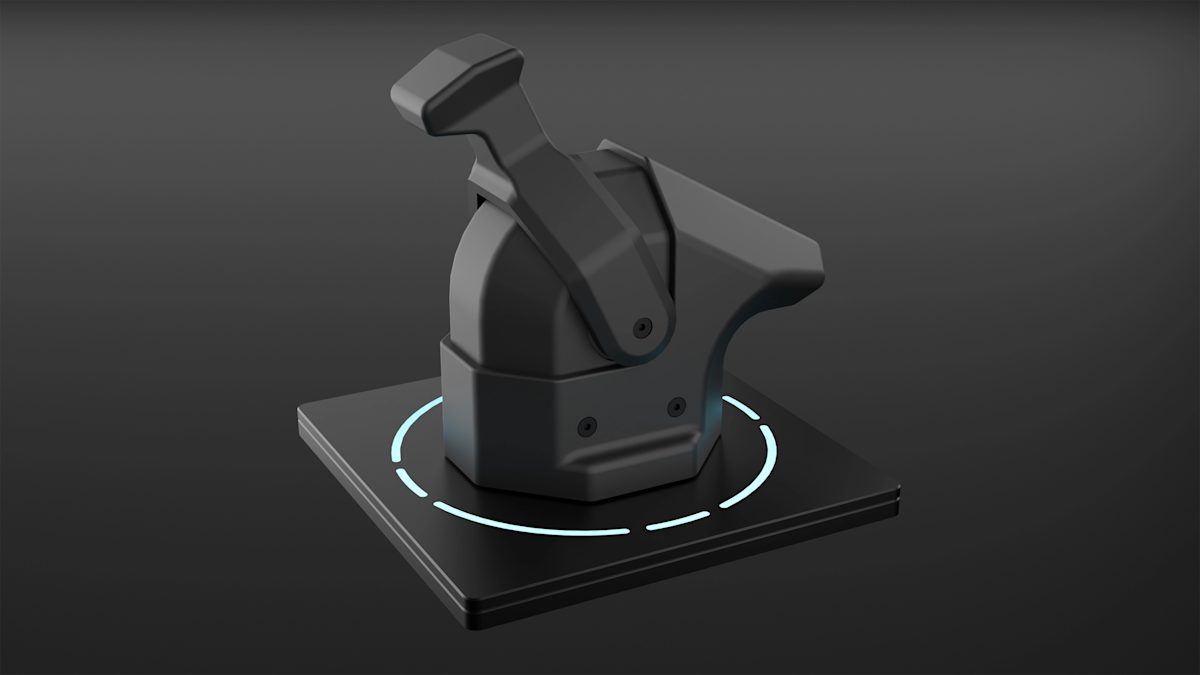
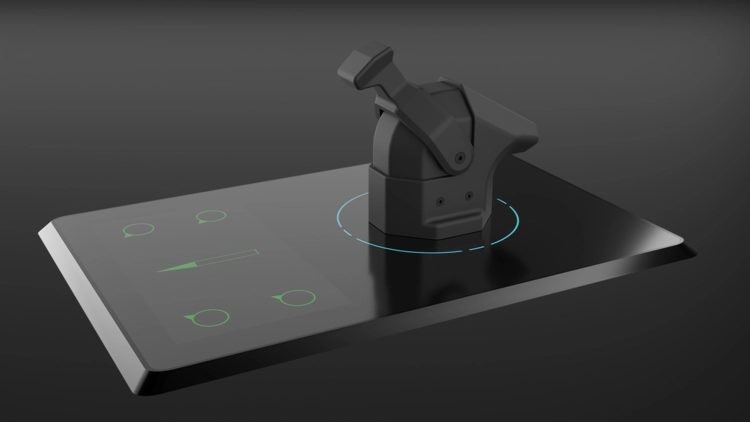
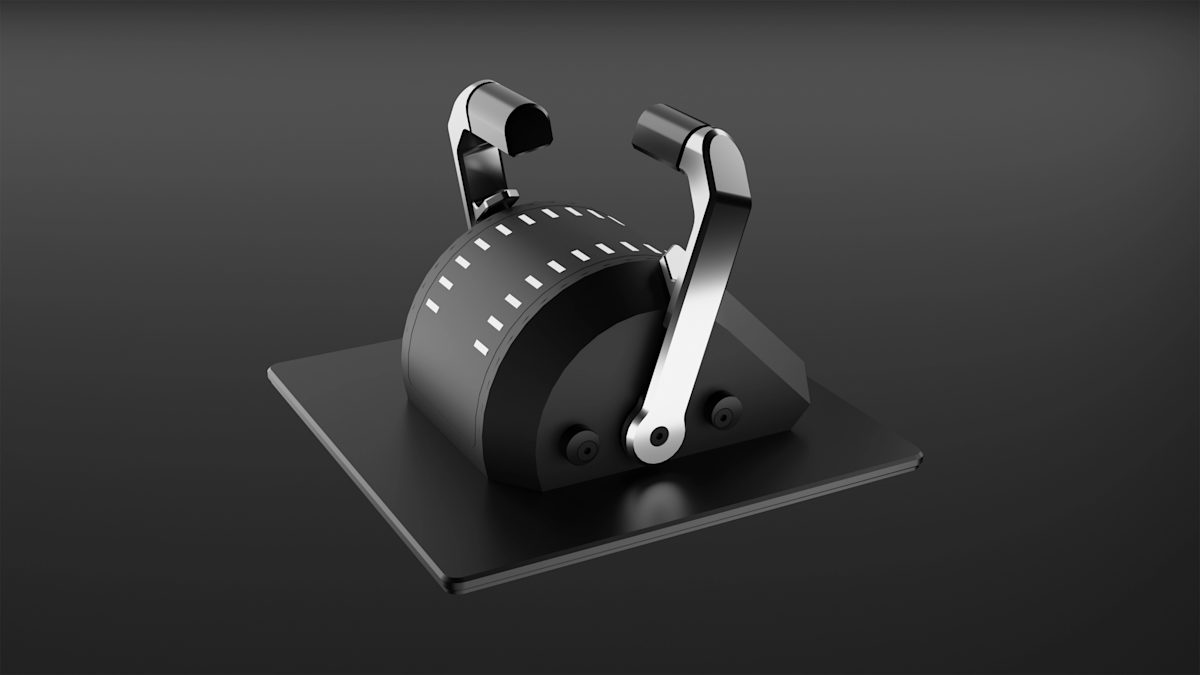
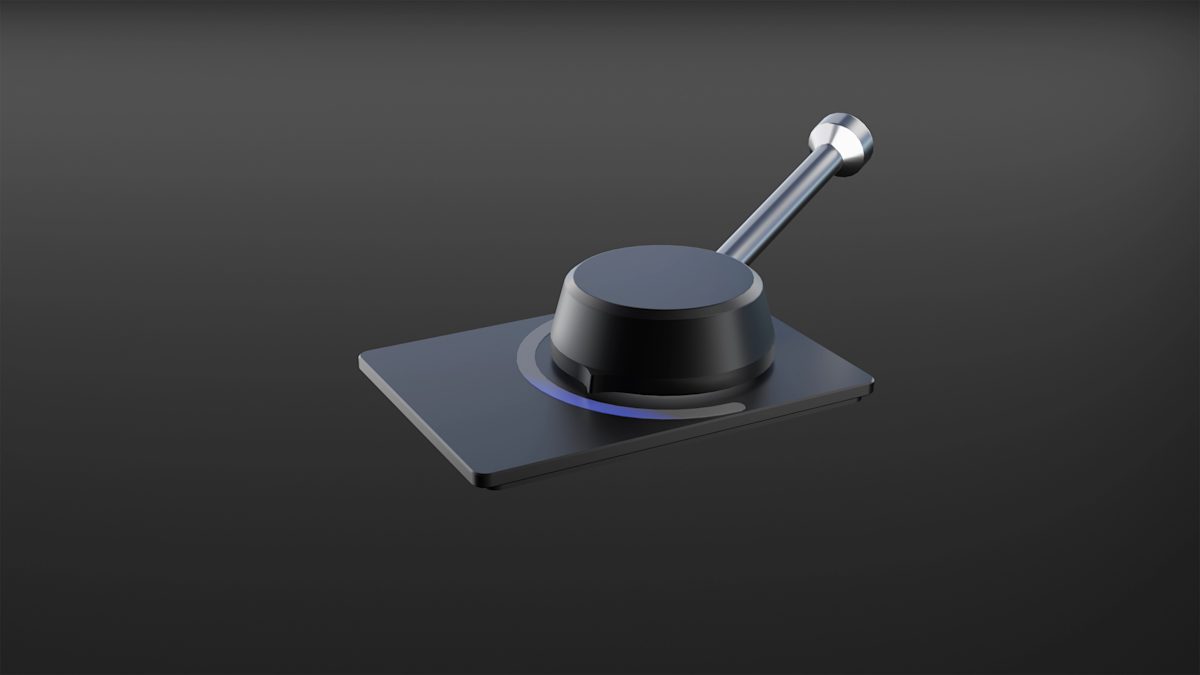
Bridging the innovation gap in maritime technology
Aside from having to leap through certification hoops to get its product on board ships, another hurdle Smart-Ship is encountering is the more conservative pace at which the maritime industry adopts new technologies.
“People already know what they’re doing very well, so they are often unaware of the benefits that new technologies, like ours, can bring,” says Tiemensma. However, with more companies like Smart-Ship emerging, this is slowly changing.
More and more sustainable shipping solutions and technologies are entering the market, especially with the fast-growing need to significantly reduce fossil fuel use. As well, remote shipping is becoming a more prominent trend, in part due to a lack of personnel. There will always be a gap between the amount of information gathered on board and presented to the operator and the amount of information that they can actually process. That’s why Smart-Ship makes sure that the crucial information is transferred to the operator in an intuitive way, allowing them to immediately act.
“We’re really trying to bridge that gap by making operators more aware of what a ship is doing and what it’s capable of doing,” says Tiemensma, “but also making use of the flexibility and skills of operators to improve upon what those ships are doing to make sure the maritime industry is always a safe environment.”
Safety is only one of the key benefits of the Smart-Ship model, which significantly aids the maritime industry’s push toward electrification. Many ships now use both a generator and an electrical drive system, as well as a fossil fuel engine as a backup for longer hauls. Operators can switch between a ship’s power source based on a number of situational factors along the journey.
Smart-Ships technology supports a more sustainable shipping industry by helping operators more intuitively switch between drive systems, ensuring that the most efficient energy source is being used in every conceivable nautical situation.
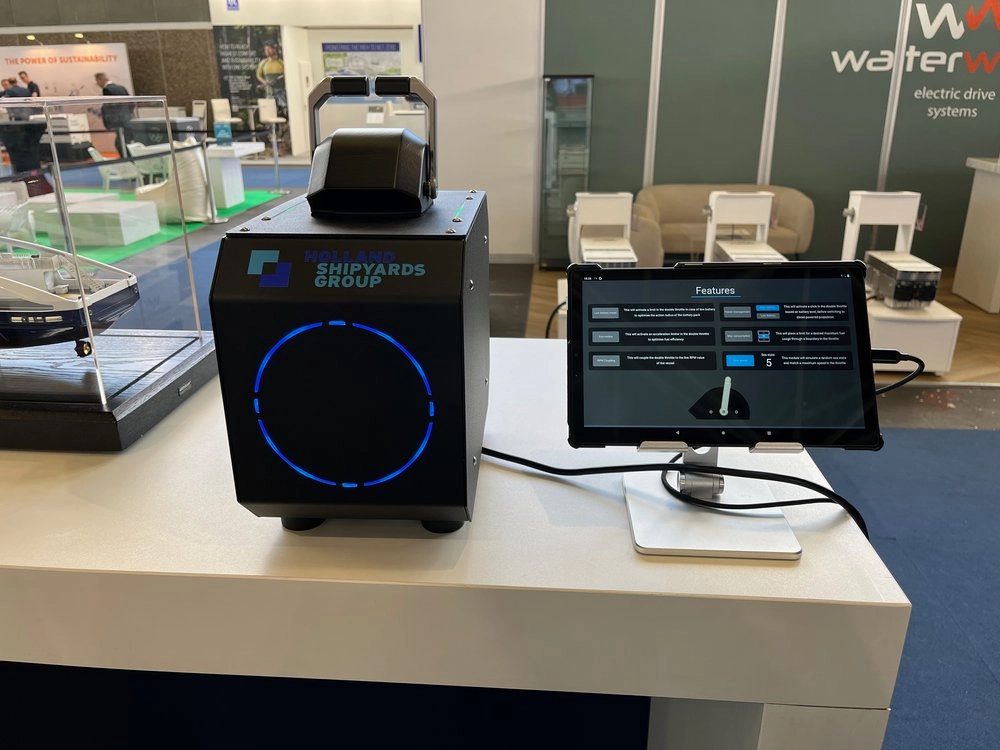
Charting a course for the future
In early 2022, Smart-Ship tested its products on Royal IHC’s dredging simulator to actual operators to improve operational efficiency and safety. As well, the company installed one of its throttle levers on an inland ship to provide feedback on an integral locking assistance system. Check out this video of the SciPPPer project here to see Smart-Ships levers in action.
In terms of the company’s sustainability aims, the drive system switching mechanism (a double throttle lever) is being tested as of mid-2022 in partnership with Holland Shipyards Group. The goal will be to implement it aboard hybrid and fully electric vehicles.
With these milestones boosting momentum, Smart-Ship is testing several levers and preparing to start selling products directly to shipping companies, in parallel to producing integrated training modules with the same software and levers. The company is gearing up to scale the production in collaboration with our network.
“I really look forward to working together with a partner that’s able to think along with us, that understands our situation and has the capabilities to grow along with us,” says Tiemensma.
Smart-Ship’s goal is to complete testing on products comprised of parts with the tolerances and dimensional accuracy as designed but also to assure that quality every time after getting the product onboard ships.
“You really have to be able to assure that you can supply constant quality and everything complies with the rules and regulations,” says Tiemensma. “We want to show that a small company, in collaboration with a manufacturing partner, can provide this quality.”
About the ongoing partnership between Smart-Ships and our network, Tiemensma simply says, “we’ve quoted parts from different suppliers, but we always go back to the platform.”
Ready to innovate faster with digital manufacturing?
Source custom 3D-printed parts Source custom CNC parts Get a free, instant quote