There is an increased focus on the development of specialized materials at production level. “We’re always looking at materials that need to actually work out in a field, in a factory, in a lab,” says DIVE’s Adam Hecht. While a few years ago, printing standard polypropylene was the order of the day, he says that “now, companies are designing blends actually tailored for 3D printing. They’re creating a lot of materials that are geared for very specific applications within 3D printing, whether that’s conventional thermoplastics that have been re-engineered for 3D printing, or resins that aren’t just for prototyping, but for very specialized, high temperature, high-elasticity types of applications. That’s been really exciting for us to see.”
Hecht names Carbon Fiber PP Filament by the 3D materials innovator Xtellar as an example. “Polypropylene has been notoriously challenging to print via FDM,” he says, “but new formulas address these challenges, while maintaining important qualities of polypropylene like chemical resistance, low density, and impact strength.” Another example for a highly specialized material is CPX by Filament Innovations, which makes machines and advanced materials specifically for custom prosthetics.
Traditionally, research and development in the 3D printing industry has leaned heavily on metal. “There’s a lot more money in industries utilizing metal, such as aerospace and medical,” says Hecht, “so they’ve been able to make a lot more progress on the side of research and investing.” Protolabs’ Eric Utley agrees: “There’s always a lot of research going on in metals,” he says. But now, there is also a real push for production-capable plastics, as well as more specialized materials such as ceramics and silicone. “Some markets, like automotive, consumer, healthcare, and industrial, are doing an amazing job showing the world what can be done when we approach manufacturing with a 3D mindset,” says HP’s François Minec. “Materials innovation will only lead to further disruption in these markets and beyond.”
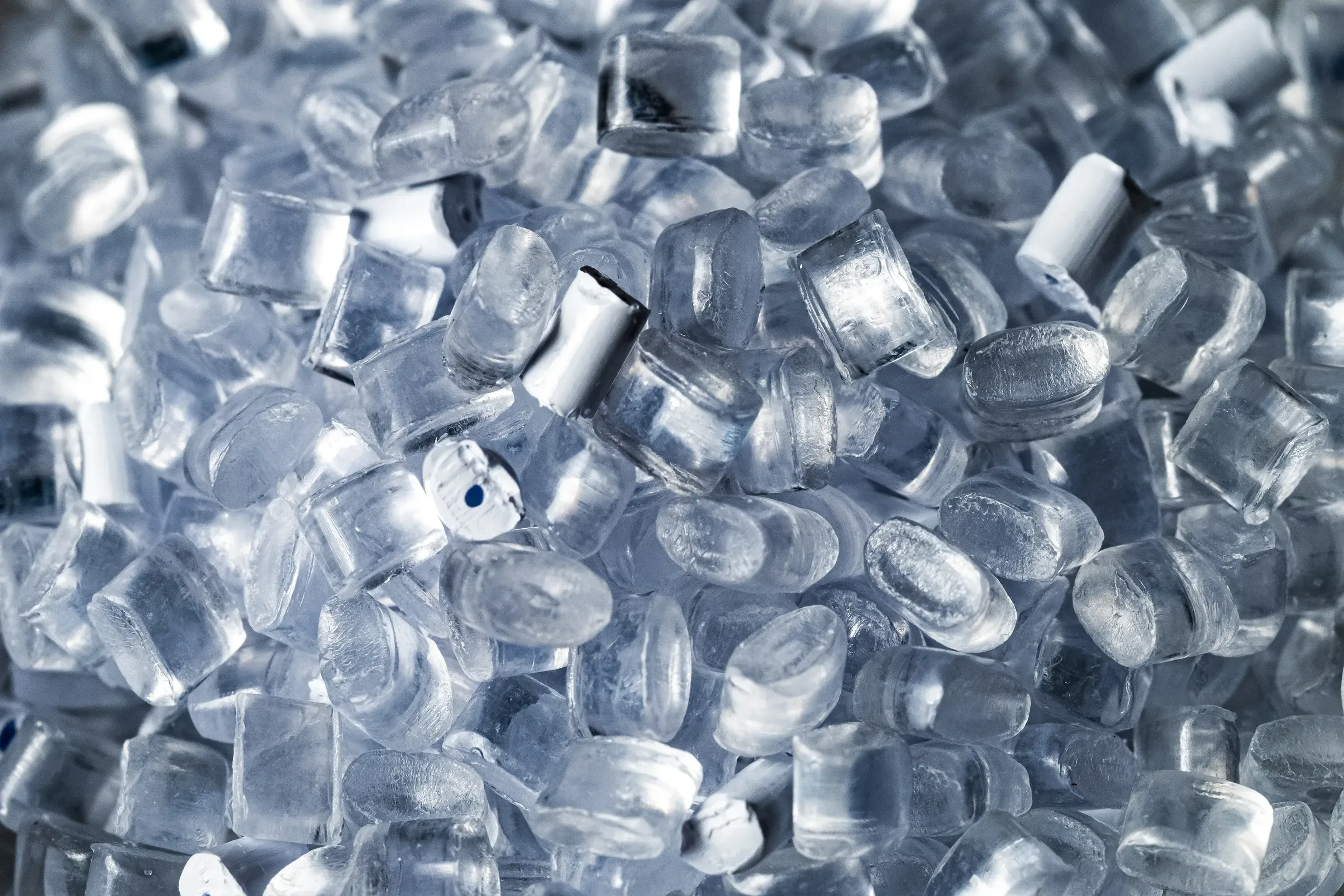
Materials with properties such as elasticity, conductivity, heat resistance, or improved stiffness, materials with dissipative properties, extra lightweight materials, biocompatible materials, and materials with reduced UV sensitivity are emerging and entering the market.
As they are becoming more accessible, they are set to transform 3D printing practices. “An important emerging property is heat resistance for high-temperature applications,” says Protolabs’ Grant Fisher. “We are starting to see ceramic 3D printing in the market—it has some technical challenges but is capable of making some unique parts with great thermal properties.” Another example is TPU — thermoplastic polyurethane — a relatively new material for powder-based printing technologies such as MJF and SLS that’s been described as a bridge between rubbers and plastics. With its flexibility and durability, it can be used for custom gaskets and seals, and the fact that it’s a skin-safe material means it’s also suitable for wearables and medical applications.
In addition, HP has announced a new nylon-based material for its widely adopted MJF printers that it says offer superior surface aesthetics and cost-efficiency in parts production. According to Minec, it has “reduced variable costs per part and a significantly lower total cost of ownership,” as well as the “sustainability benefit of the highest reusability ratio” of all PA 12 materials in the market.
The push for new, production-capable materials is something that’s happening industry wide. “There’s a number of companies throwing their hat in the ring,” Utley says. “There’s a lot of market competition going on.”
When used in production, plastic parts need a fire rating such as a UL rating in the US or the CE rating in the EU, so consequently, flame-resistance is one property that is in high demand. “Again, it demonstrates that maturation of the market,” says Utley. “There’s now enough production plastic printers out there for companies to start offering flame-rated plastic materials that can be used in production.”
Some sectors, particularly the medical industry, aerospace, and automotive, are highly reliant on certifications. “Working closely with standardization bodies and certification agencies to ensure new materials meet necessary criteria and regulations [is] key, in addition to compiling data and procedures that show the new material is consistent, reliable, and repeatable throughout the manufacturing process,” says Minec.
And while this is rarely a speedy affair, things are moving along, says Fisher. For example, “more and more materials get approved for use in aircraft interiors.” And new certifications tend to have a big impact on the industry as a whole. “As materials get approved for defense contract work and government work, it really opens up that area. So whenever a material gets approved for a specific kind of government application, it’s a big deal.” Indeed, in our survey, 64% of respondents stated that material and/or compliance certificates were either “very important” or “sometimes important” to their 3D printing projects.
In the same survey, only 10% named “material properties” as the main factor why they opted for 3D printing over other manufacturing methods—a figure that is likely to increase considering the exciting developments in this particular field.
For more insights on the 3D printing industry including market data and future trends, download a copy of our 3D Printing Trend Report 2024.