ReVibe Energy & Protolabs Network | |
---|---|
Organization | ReVibe Energy |
Location | Gothenburg, Sweden |
Industry | Electric power |
Product | Vibration energy harvesters |
Technology | CNC machining, 3D printing (MJF) |
Materials | Aluminum 6061-T6, nylon 11 |
Why us? | Getting CNC machined parts in less than 2 weeks |
Where there are continuous vibrations, ReVibe Energy can leverage this energy to power nearly every type of wireless sensor system, including vibration sensors, light sensors and GPS systems. These vibrations are mostly found in industrial sectors like railway, logistics, construction, mining, process manufacturing, shipping, and aviation.
ReVibe Energy reduces the costs of replacing batteries or cables in remote or hard-to-reach locations. The vibration harvesting device also enables expensive industry equipment never goes unmonitored, insusceptible to unforeseen breakages, by powering different types of condition monitoring systems
Harvesting vibrations from trains
One example where ReVibe excels is cargo trains. These trains are off-the-grid - disconnected from electricity and offline. In the past, if you wanted to track these trains through GPS monitoring, the only way possible would have been batteries.
“And, if you have one sensor per wagon, that translates to one battery,” explains Viktor Börjesson, CEO of ReVibe Energy, “There’s about 5 to 10 million cargo wagons globally, and that battery would run out every 2 years. You can imagine how high the costs get to replace those batteries.”
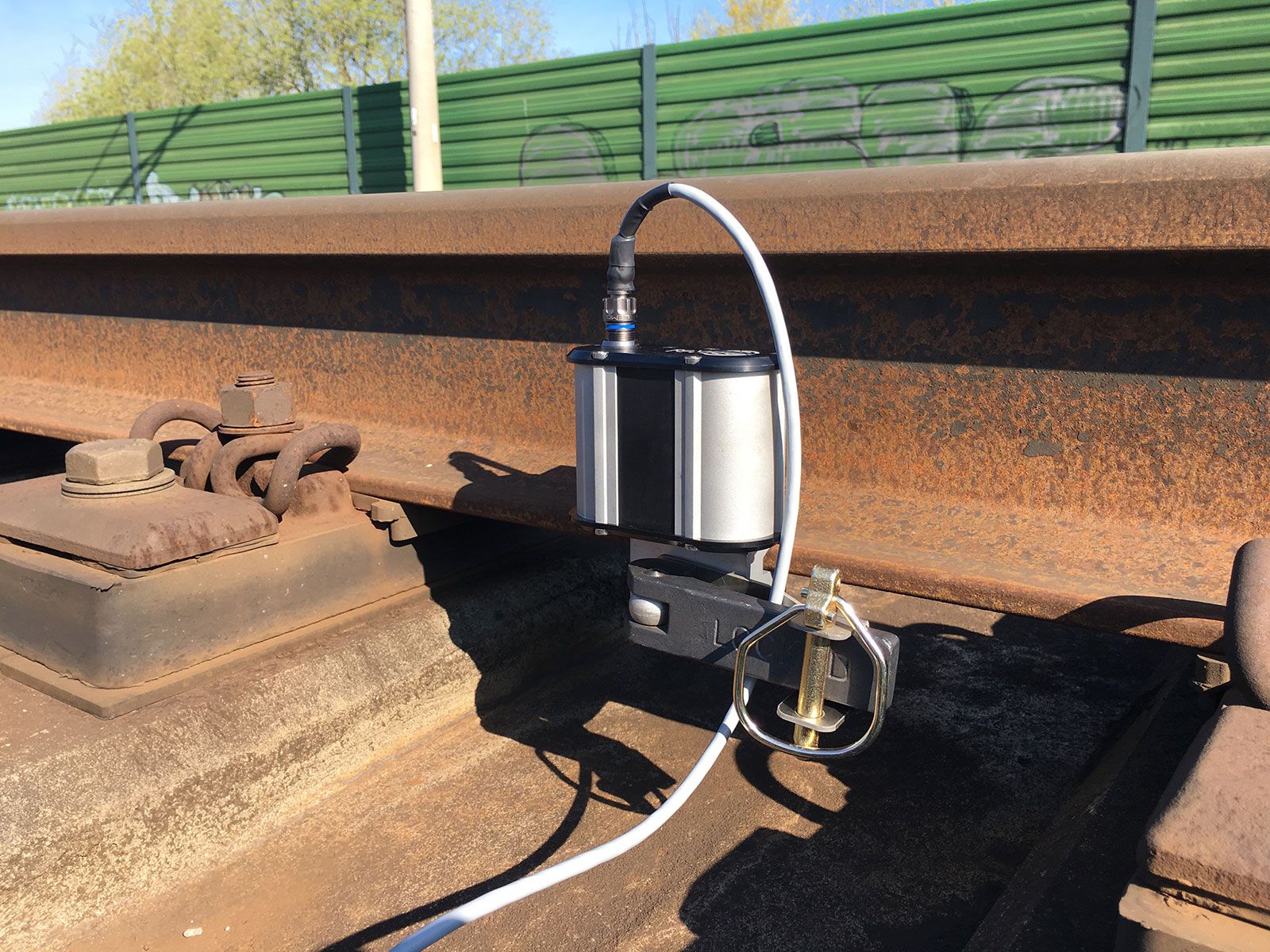
“Instead, we use vibrations created by the friction between the railway track and the wheel of the train when the train is moving,” shares Viktor, “and we use that vibration because that is, in all its simplicity, kinetic energy.”
With this technology, railway companies can keep track of their assets and understand where they need to perform maintenance on the wheels.
📕 Download our free engineering guide to CNC machining here
Custom builds for every environment
Every unit ReVibe makes has to be integrated into a different environment and therefore has different power and space requirements. Meaning for every customer, ReVibe needs to build bespoke parts.
The team starts by designing parts in a CAD software which they test for performance using a proprietary simulation software. If successful, they go on to test 3D printed, experimental parts which they test on a vibration table, in order to expose the parts to similar vibrations they will meet in the real environment. After making the necessary adjustments, ReVibe order CNC milled parts to test out in real life, and continue to repeat this process until the device harvests enough power and is fully integrated into the customers’ environment.
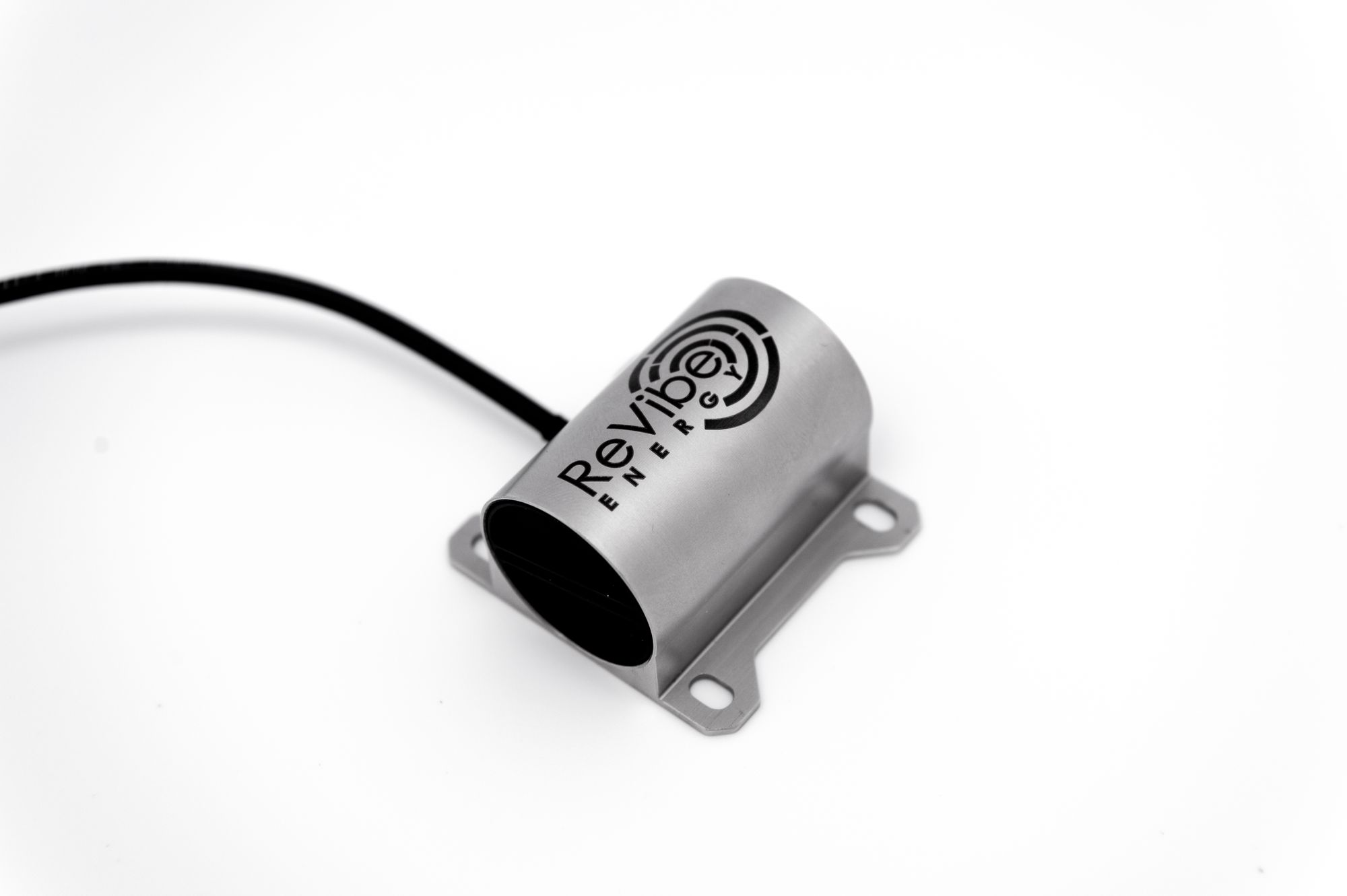
Although each project requires custom parts, certain design considerations remain consistent, including:
- Weight: light casing, heavy inside mass
Because the unit needs to be attached to different objects, the outer casing has to be as light and compact as possible. Which is why ReVibe manufactures it from aluminum and keeps it thin. However, the mass inside the unit needs to be heavy, as the weight affects the amount of electricity harvested. - Precision
As the units are usually quite compact, the individual pieces are small and need to be precise, especially when they need to fit into their customers’ existing products. This need for detail is why ReVibe energy chose to CNC machine the majority of parts.
Speed is essential
Core to the business is speed. “We’re a start-up, so we always try to excel when it comes to speed when working with our clients,” shares Viktor, “and as we’re a small organization, we will always be naturally faster than our larger enterprise clients.
“But one area where we would be equally as slow is if we used the same suppliers. That’s why we always try to choose suppliers that can deliver within a week or two maximum to be as quick as possible. We were having issues finding a company that could CNC machine fast at a reasonable price, until we found the network.”
“Plus the transparency in pricing is really big for us,” comments Viktor, “just uploading the STEP files and seeing the price and lead time straight away has been transformational.”
Read more customer stories:
- Building the fastest sailboats in the world
- Learn how Kepler rapidly went from a sketch on a napkin to a satellite in space with our CNC machining
- Headphones that deliver the highest level of audio performance possible
⚡Or upload a part to the Protolabs Network platform to get an instant quote.