Le guide technique complet
Moulage par injection

Prêt à obtenir vos pièces en impression?
Obtenir un devis
Ce guide couvre tout ce que vous devez savoir sur le moulage par injection. Passez en revue les principes fondamentaux de la technologie et apprenez rapidement des conseils de conception pratiques pour gagner du temps et de l’argent.
Part 1
Les bases en injection plastique
Qu’est-ce l’injection plastique ? Comment cela fonctionne-t-il ? À quoi cela sert-il ?
Dans cette section, nous répondons à ces questions et vous montrons des exemples courants de pièces moulées par injection pour vous aider à vous familiariser avec le fonctionnement et les applications de base de la technologie.
Qu’est-ce que l’injection plastique ?
L’injection plastique est une technologie de fabrication de forme : pour créer une pièce, le plastique est d’abord fondu puis injecté dans l’empreinte d’un moule. Lorsque le matériau refroidit, il se solidifie et prend la géométrie (forme) du moule. La pièce est ensuite éjectée et le processus recommence.
Il s’agit d’un mode de fabrication fondamentalement différent de celui des technologies additives (impression 3D) ou soustractives (usinage CNC). L’écoulement et la solidification du matériau pendant l’injection ont un impact significatif sur les principales restrictions de conception de cette technologie, plus d’informations à ce sujet ci-dessous.
Le processus de moulage par injection
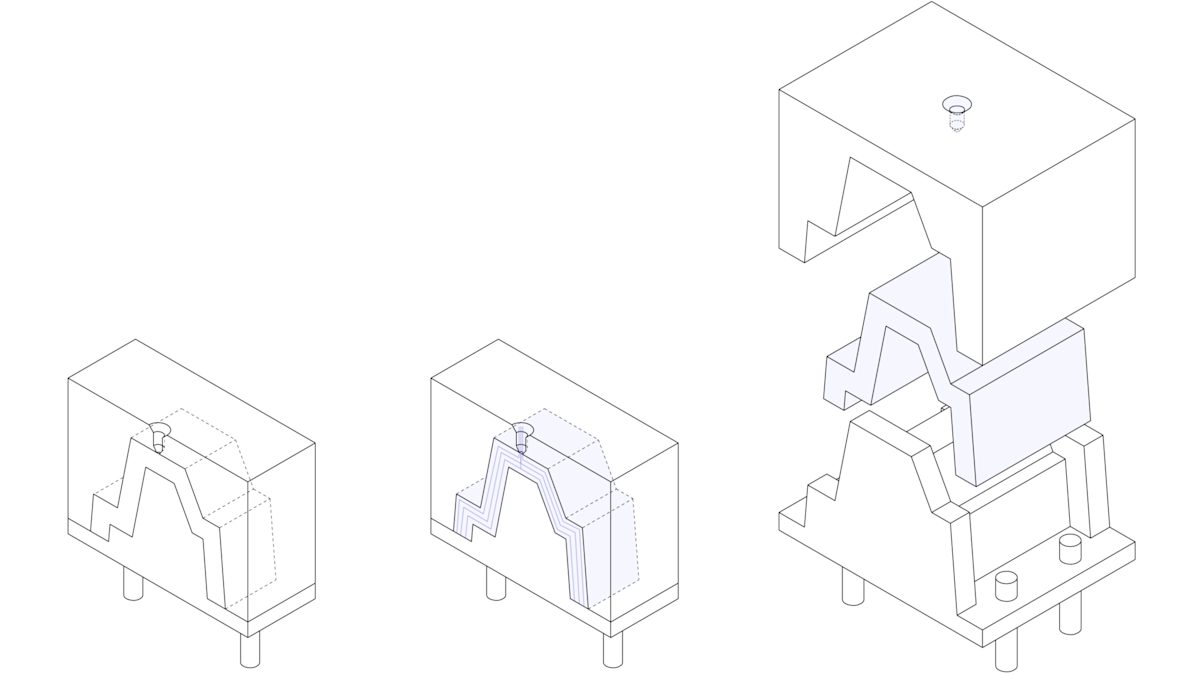
L’injection plastique est aujourd’hui largement utilisée pour les produits de consommation et les applications techniques. Presque tous les articles en plastique autour de vous ont été fabriqués en injection plastique. En effet, cette technologie est capable de produire des pièces identiques à des volumes très élevés (généralement de 1 000 à plus de 100 000 unités) à un coût par pièce très faible (généralement de 1 à 5 euros l’unité).
Par rapport à d’autres technologies, les coûts de mise en œuvre de l’injection plastique sont relativement élevés, principalement en raison de la nécessité d’un outillage sur mesure. Un moule peut coûter entre 3 000 € et 100 000 € et parfois même davantage, selon sa complexité, son matériau (alliage d’aluminium ou acier) et sa précision (prototype, moule de présérie ou moule de production en grande série).
Tous les matériaux thermoplastiques peuvent être moulés par injection. Certains types de silicone et autres résines thermodurcissables sont également compatibles avec le procédé d’injection plastique. Les matériaux les plus couramment utilisés dans le domaine de l’injection plastique sont :
- le polypropylène (PP) :__ ~38 % de la production mondiale,
- l’ABS : ~27 % de la production mondiale,
- le polyéthylène (PE) :__ ~15 % de la production mondiale,
- le polystyrène (PS) :__ ~8 % de la production mondiale.
Même si l’on tient compte de toutes les autres technologies de fabrication possibles, l’injection plastique avec ces quatre matériaux représente à lui seul plus de 40 % de toutes les pièces plastiques produites dans le monde chaque année !
Injection plastique: Un bref historique
Les plastiques remplacent l’ivoire
En 1869, John Wesley Hyatt invente le celluloïd, le premier plastique artificiel utile destiné à remplacer l’ivoire pour la production de… boules de billard ! Les premières machines utilisaient un baril pour chauffer le plastique et un piston pour l’injecter dans le moule.
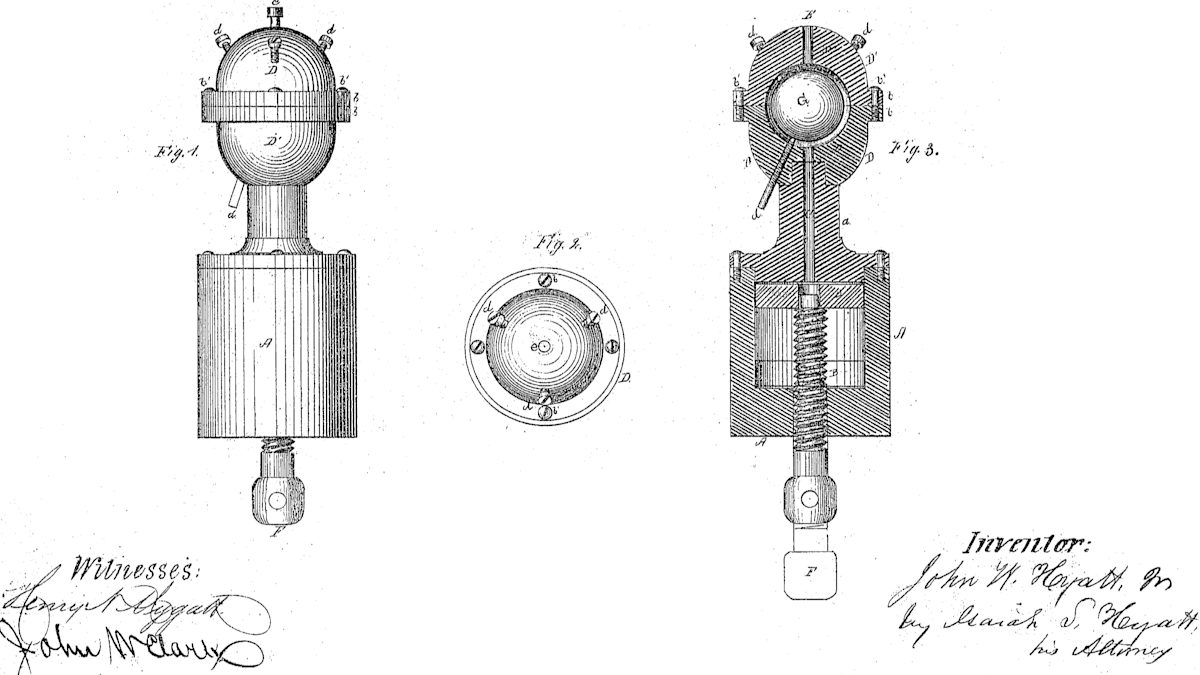
L’invention révolutionnaire
Au milieu des années 1950, l’invention de la vis de plastification révolutionne à elle seule l’industrie du plastique. La vis de plastification a permis de résoudre les [problèmes clés] (https://youtu.be/RMjtmsr3CqA?t=1m58s) de l’injection, en particulier le réchauffement inégal du plastique des systèmes précédents, et a ouvert de nouveaux horizons pour la production en série de pièces en plastique.

L’injection plastique aujourd’hui
Aujourd’hui, le moulage par injection est un marché de [300 milliards de dollars](https://www.grandviewresearch.com/industry-analysis/injection-molded-plastics-market « Marché de l’injection plastique »). Plus de 5 millions de tonnes de pièces en plastique sont produites chaque année dans le monde entier grâce à l’injection plastique. Récemment, la demande de matériaux biodégradables a augmenté pour des raisons environnementales.

Presses d’injection plastique : comment fonctionnent-elles ?
Une machine de moulage par injection se compose de trois parties principales : l’unité d’injection, le moule (le cœur de tout le processus) et l’unité de bridage/d’éjection.
Dans cette section, nous examinons l’objectif de chacun de ces éléments et la façon dont leurs mécanismes de fonctionnement de base influencent le résultat final du processus d’injection plastique.
Visionnez dans la vidéo ci-dessous une grande presse d’injection plastique en action alors qu’elle produit 72 bouchons de bouteilles toutes les 3 secondes.
L’unité d’injection

Le but de l’unité d’injection est de faire fondre le plastique brut et de le guider dans le moule. Il se compose de la trémie, du cylindre d’injection et de la vis d’injection.
La matière plastique brute se présente sous forme de granulés. Dans la trémie, les granulés peuvent être mélangés avec des pigments ou d’autres additifs (par exemple, de la fibre de verre). De cette façon, la couleur et les propriétés physiques des pièces moulées peuvent être adaptées aux besoins spécifiques de chaque application.
Ensuite, le matériau est introduit dans le fourreau, qui contient la vis de plastification.
La vis effectue deux tâches : elle transporte les granulés vers le moule et en même temps elle les comprime. En fait, les forces de cisaillement causées par le mouvement de la vis produisent de 60 % à 90 % de la chaleur nécessaire pour faire fondre les granules de plastique. Le reste est fourni par les colliers de chauffe qui sont enroulés autour du fût.
Une fois qu’il y a suffisamment de plastique fondu devant la vis, le vérin hydraulique plonge vers l’avant et injecte le matériau dans l’empreinte vide du moule (comme une seringue). L’ensemble de ce processus se déroule de manière continue, de sorte que le remplissage du moule ne prend que quelques secondes.
Fabrication du moule
Le moule est comme le négatif d’une photographie: sa géométrie et ça texture de suface est directement transféré sur la pièce moulée par injection.
Il représente la plus grande partie des coûts de démarrage dans le moulage par injection: le coût d’un moule typique démarre à environ 2000-5000$ pour une géométrie simple et des cycles de production relativement petits (de 1000 à 10000 unités) et peut aller jusqu’à 100000$ pour les moules optimisés pour une production à grande échelle (100000 unités ou plus).
Cela est dû au haut niveau d’expertise requis pour concevoir et fabriquer un moule de grande qualité qui peut produire avec précision des milliers ( ou des centaines de milliers) de pièces.
Les moules sont généralement usinés sur machine à commmande numérique en aluminium ou en acier à outils, puis finis selon la norme requise. Outre le négatif de la pièce, ils ont également d’autres caractéristiques, comme le circuit d’injection plastique qui facilite l’écoulement du matériau dans le moule et les canaux de refroidissement à eau internes qui facilite et accélère le refroidissement de la pièce.
En savoir plus sur l’usinage CNC. Lire le guide complet d’ingénierie
Les récents progrès dans les matériaux d’impression 3D ont permis la fabrication de moules adaptés au moulage par injection de petite série moulage par injection plastique en petite série (100 pièces ou moins) à une fraction du coût. Ces petits volumes n’étaient pas économiquement viables dans le passé, en raison du coût très élevé de la fabrication de moules traditionnels.
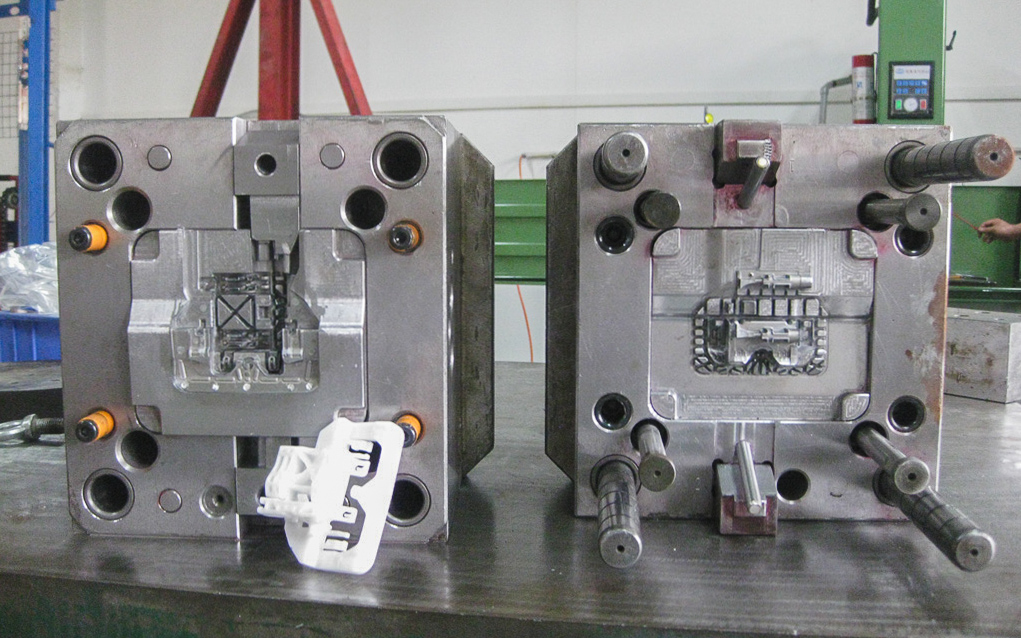
Les composants d’un moule

Le moule le plus élémentaire, le moule simple, sans tiroir, se compose de deux empreintes : la partie fixe et la partie mobile. Pour les pièces plus complexes avec des contre-dépouilles, il est également possible d’utiliser des tiroirs qui coulissent dans et hors de la pièce. Plus d’informations au sujet des tiroirs & contre-dépouilles dans une section suivante.
La partie fixe et la partie mobile ont des fonctions différentes. La première est l’empreinte du moule qui est la plus proche du système d’injection. Il forme le côté cosmétique de la pièce (côté A) qui nécessite un bon aspect visuel. La seconde est l’empreinte arrière du moule et forme le côté fonctionnel « caché » (côté B) qui comprend tous les éléments structurels de la pièce (nervures, bossages, etc.).
Les moules sont généralement usinés sur machine à commande numérique en alliage d’aluminium (pour 1 000 à 5 000 unités) ou en acier à outils (pour plus de 100 000 unités). Pour les petites séries (moins de 100 unités) les moules peuvent même être réalisés en impression 3D pour raccourcir les délais.
Outre le « négatif » de la pièce, un moule possède d’autres caractéristiques qui participent au processus d’injection. Par exemple, les moules comprennent souvent des canaux de refroidissement qui accélèrent le processus de solidification et des évents qui permettent d’évacuer l’air du moule vide.
Donnée intéressante : environ 50 % du cycle classique en injection plastique est consacré au refroidissement et à la solidification des pièces. Minimiser l’épaisseur d’un dessin est la clé pour accélérer cette étape &réduit les coûts.
Les 2 côtés du moule: côté A et côté B
Les pièces moulées par injection ont deux côtés: le côté A, qui fait face à la partie fixe du moule (moitié avant du moule) et le côté B, qui fait face à la partie mobile du moule (moitié arrière du moule). Ces deux côtés ont généralement des objectifs différents:
- Le côté A a généralement une meilleure apparence visuelle et est souvent appelé le côté esthétique. Les faces du côté A seront lisses ou auront une texture selon vos spécifications de conception.
- Le côté B contient généralement les éléments structurels cachés (mais très important) de la pièce (les bossages, les nervures, les encliquetages, etc.) fonctionnel. Le côté B aura souvent une finition plus rugueuse et des marques visibles des broches d’éjection.
Le système d’alimentation
Le plastique fondu entre dans le moule par le système d’alimentation. Il se compose généralement de trois sections principales : la *carotte (le canal principal), les canaux d’alimentation (les canaux secondaires) et les points d’injection (les seuils).
Différents types de seuils conviennent à différentes applications. L’illustration montre un points d’injection sur arête, tandis que les briques ci-dessous ont été fabriquées à l’aide d’un seuil à pointe chaude, plus d’informations sur les types de points d’injection ici.
Le système d’alimentation est détaché de la pièce après l’éjection. C’est le seul déchet de matière en injection plastique, dont 15 à 30 % peuvent être recyclés et réutilisés.

Différents types de seuil d’injection conviennent à différentes applications. Il existe 4 types de seuils utilisées dans le moulage par injection:
- Seuil en nappe injecte du matériau à la ligne de séparation des deux moitiés du moule. Ce sont les seuils les plus courants. Le système d’alimentation doit être retiré plus tard manuellement, laissant une petite imperfection au point d’injection.
- Seuil en tunnel injecte le matériau sous la ligne de séparation. Le système d’alimentation se détache lorsque la pièce est éjectée du moule, éliminant ainsi la nécessité d’un retrait manuel. Cela rend ce type de seuil idéal pour les très grands volumes.
- Seuil sous-marin injecte le matériau à l’arrière de la cavité, masquant la petite imperfection laissée par la rupture des autres types de seuils. Ces seuils sont utilisés pour les pièces qui nécessitent une excellente apparence visuelle.
- Seuil capillaire est directement connecté à l’éperon et injecte du plastique par le haut de la pièce. Aucun matériau n’est gaspillé de cette façon dans le système d’alimentation, ce qui les rend idéales pour une production à grande échelle, mais une fossette sera visible au point d’injection.
Les traces de seuils
À l’endroit où le système d’alimentation est relié à la pièce, une petite imperfection est généralement visible, appelée trace de seuil.
Si la présence de la trace de seuil n’est pas souhaitable à des fins esthétiques, alors on peut aussi la « cacher » dans la face B de la pièce.
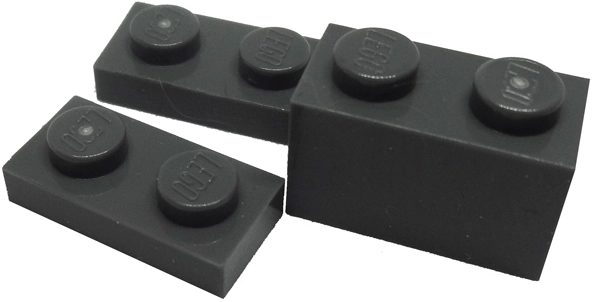
The clamping and ejection system
On the far side of an injection molding machine is the clamping system. The clamping system has a dual purpose: it keeps the 2 parts of the mold tightly shut during injection and it pushes the part out of the mold after it opens.
After the part is ejected, it falls onto a conveyor belt or a bucket for storage and the cycle starts over again.
Alignment of the different moving parts of the mold is never perfect though. This causes the creation of 2 common imperfections that are visible on almost every injection molded part:
-
Parting lines which are visible on the side of a part where the 2 halves of the mold meet. They are caused by tiny misalignments and the slightly rounded edges of the mold.
-
Ejector (or witness) marks which are visible on the hidden B-side of the part. They are created because the ejector pins are slightly protruding above or indented below the surface of the mold.
The image below shows the mold used to manufacture both sides of the casing for a remote controller. Quick quiz: try to locate the *core* (A-side), the *cavity* (B-side), the runner system, the ejector pins, the side-action core and the air vents on this mold.
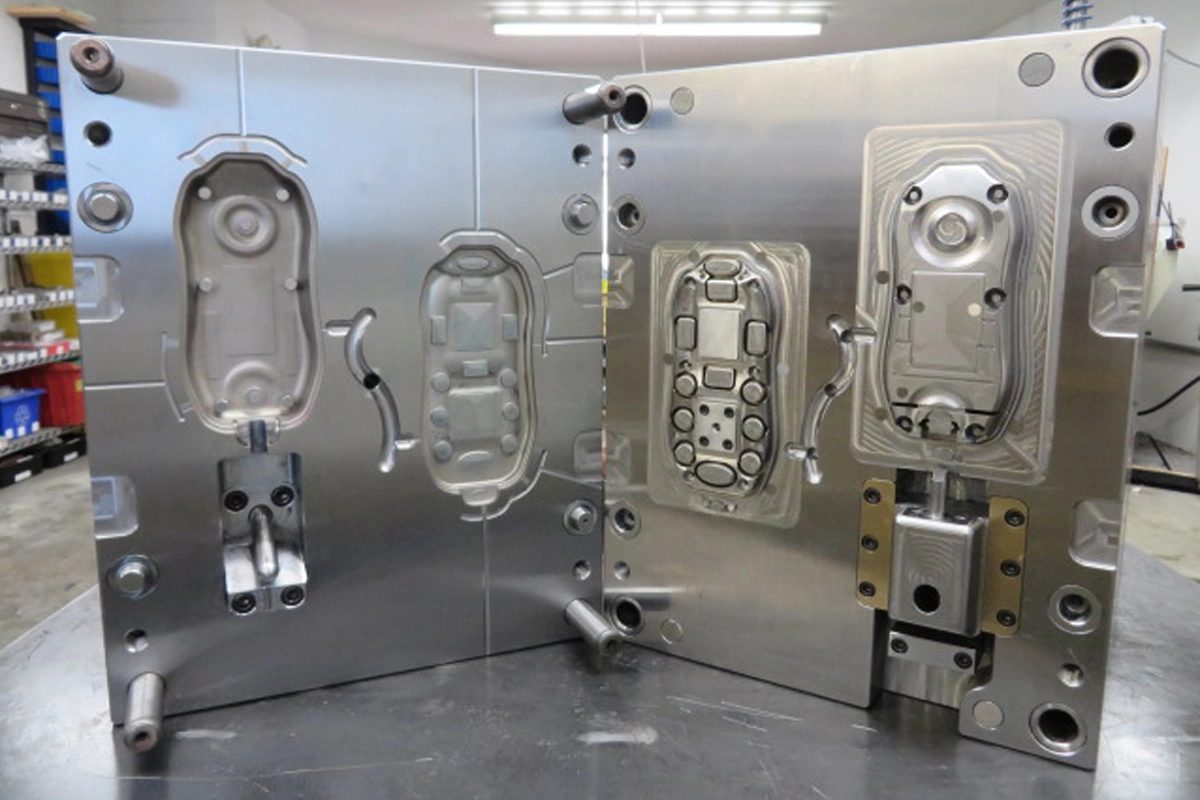
Avantages et limites de l’injection plastique
L’injection plastique est une technologie de fabrication établie de longue date, mais elle est constamment perfectionnée et améliorée grâce à de nouvelles avancées technologiques.
Vous trouverez ci-dessous un bref aperçu des avantages et des inconvénients de l’injection plastique pour vous aider à déterminer si c’est la bonne solution pour votre application.
Avantages de l'injection plastique
L’injection plastique est la technologie la plus compétitive en termes de coûts pour la fabrication de grands volumes de pièces plastiques identiques. Une fois le moule créé et la machine installée, des pièces supplémentaires peuvent être fabriquées très rapidement et à moindre coût.
Le volume de production minimum recommandé pour l’injection plastique est de 500 pièces. A ce stade, les économies d’échelle commencent à se faire sentir et les coûts initiaux relativement élevés de l’outillage ont un effet moins important sur le prix unitaire.
Presque tous les matériaux thermoplastiques (et certains thermodurcissables et silicones) peuvent être moulés par injection. Cela donne une très large gamme de matériaux disponibles avec des propriétés physiques diverses pour la conception.
Les pièces produites en injection plastique ont de très bonnes propriétés physiques. Ces propriétés peuvent être optimisées en utilisant des additifs (par exemple, de la fibre de verre) ou en mélangeant différents granulés (par exemple, des mélanges PC/ABS) pour obtenir le niveau de résistance, de rigidité ou de résistance aux chocs souhaité.
Le cycle classique d’injection plastique dure de 15 à 60 secondes, selon la taille de la pièce et la complexité du moule. En comparaison, l’usinage CNC ou l’impression 3D peut prendre de quelques minutes à quelques heures pour produire la même géométrie. De plus, un moule unique peut recevoir plusieurs pièces, ce qui augmente encore les capacités de production de ce procédé de fabrication.
Cela signifie que des centaines (voire des milliers) de pièces identiques peuvent être produites chaque heure.
Le procédé d’injection plastique est très reproductible et les pièces produites sont en principe identiques. Bien sûr, le moule s’use avec le temps, mais un moule en aluminium de série dure généralement de 5 000 à 10 000 cycles, tandis que les moules de production à grande échelle en acier à outils peuvent supporter plus de 100 000 cycles.
En général, l’injection plastique produit des pièces avec des tolérances de ± 0,500 mm. Des tolérances plus serrées jusqu’à ± 0,125 mm sont également possibles dans certaines circonstances. Ce niveau de précision est suffisant pour la plupart des applications et comparable à l’usinage sur machine à commande numérique et à l’impression 3D.
L’une des principales forces de l’injection plastique est qu’il s’agit d’un procédé capable de produire des produits finis qui n’ont besoin que de peu ou pas de finition supplémentaire. Les surfaces du moule peuvent être polies à un niveau très élevé pour créer des pièces à l’aspect miroir. Ou elles peuvent être grenaillées pour créer des surfaces texturées. Les normes SPI indiquent le niveau de finition qui peut être atteint.
[Consulter les recommandations de compatibilité finition/matériaux →] (https://www.hubs.com/knowledge-base/injection-molding-spi-surface-finishes “Recommandations de finition SPI pour l’injection plastique”)
Limites de l'injection plastique
La principale restriction économique de l’injection plastique réside dans le coût élevé de l’outillage. Puisqu’un moule sur mesure doit être réalisé pour chaque géométrie, les coûts au départ sont très élevés. Ceux-ci sont principalement liés à la conception et à la fabrication du moule et varient généralement entre 5 000 € et 100 000 €. Pour cette raison, l’injection plastique n’est économiquement viable que pour les productions supérieures à 500 unités.
Après la fabrication d’un moule, il est très coûteux de le modifier : les modifications de conception nécessitent généralement la fabrication d’un nouveau moule à partir de zéro. Pour cette raison, il est très important de concevoir correctement une pièce pour l’injection plastique.
Dans la Partie 2, nous énumérons les considérations de conception les plus importantes que vous devez garder à l’esprit lors de la conception d’une pièce qui sera réalisée en injection plastique. Dans la Partie 5, nous verrons aussi comment vous pouvez limiter le risque en créant des prototypes physiques de vos pièces.
Le délai de livraison classique en injection plastique varie de 6 à 10 semaines, 4 à 6 semaines pour la fabrication du moule, plus 2 à 4 semaines supplémentaires pour la production et l’expédition. Si des modifications de conception sont nécessaires au modèle, ce qui est assez courant, le délai de livraison augmente en conséquence.
En comparaison, les pièces fabriquées dans une imprimante 3D de bureau peuvent être prêtes à être livrées du jour au lendemain, alors que les systèmes d’impression 3D industriels ont un délai de livraison typique de 3 à 5 jours. Les pièces usinées sur machine à commande numérique sont généralement livrées dans les 10 jours ou parfois seulement 5 jours.
Exemples de produits réalisés en injection plastique
Si vous regardez autour de vous en ce moment, vous verrez au moins quelques produits qui ont été fabriqués en injection plastique. Vous en avez probablement un en ce moment même : le boîtier de l’appareil que vous utilisez pour lire ce guide.
Pour les reconnaître, prenez soin de remarquer ces trois choses : un plan de joint, des marques témoins sur la face cachée et une épaisseur de paroi relativement uniforme sur l’ensemble de la pièce.
Nous avons rassemblé ici quelques exemples de produits courants fabriqués en injection plastique pour vous aider à mieux comprendre ce qui peut être réalisé avec ce procédé de fabrication.
Briques Lego
Les briques Lego sont l’un des exemples les plus reconnaissables de pièces réalisées en injection plastique. Elles sont fabriquées à l’aide de moules comme celui sur la photo, qui a produit 120 millions de briques Lego (soit 15 millions de cycles) avant son retrait de la production.
Le matériau utilisé pour les briques Lego est l’ABS en raison de sa grande résistance aux chocs et de son excellente capacité de moulage. Chaque brique a été conçue à la perfection avec des tolérances allant jusqu’à 10 micromètres (ou un dixième de cheveu humain). Ceci est en partie réalisé en utilisant les meilleures pratiques de conception que nous examinerons dans la section suivante (épaisseur de paroi uniforme, angles de dépouille, nervures, texte en relief, etc).

Bouchons de bouteilles
De nombreux produits d’emballage en plastique sont moulés par injection. En réalité, l’emballage est le plus grand marché du moulage par injection.
Par exemple, les bouchons de bouteilles sont moulés par injection en polypropylène. Le polypropylène (PP) a une excellente résistance chimique et convient pour le contact alimentaire.
Sur les bouchons de bouteilles, vous pouvez également remarquer toutes les imperfections courantes de l’injection plastique (plan de joint, marques d’éjection, etc.) et les caractéristiques de conception courantes (nervures, contre-dépouilles, etc.).
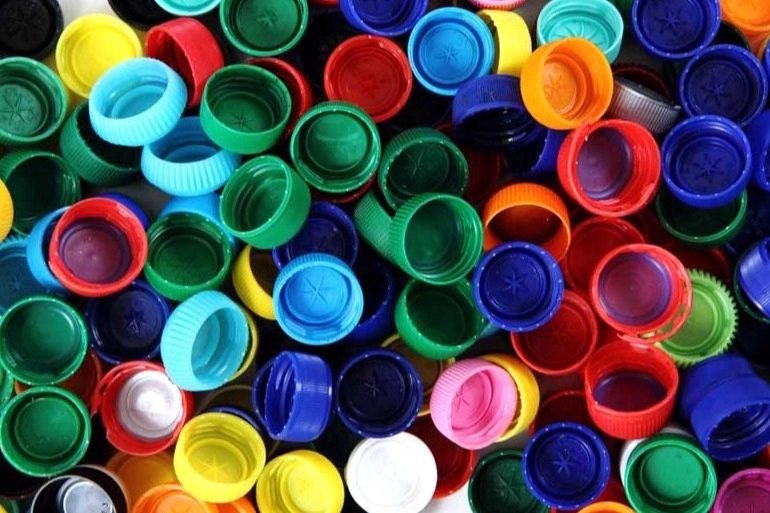
Modèle réduit d’avion
Les maquettes d’avions sont un autre exemple courant de pièces réalisées en injection plastique. Le matériau utilisé ici est principalement le polystyrène (PS), pour son faible coût et sa facilité de moulage.
Ce qui est intéressant avec les maquettes d’avion, c’est qu’elles sont livrées avec le système de canaux d’alimentation en matière plastique toujours attaché. Ainsi, vous pouvez voir le chemin que le plastique fondu a suivi pour remplir le moule vide.
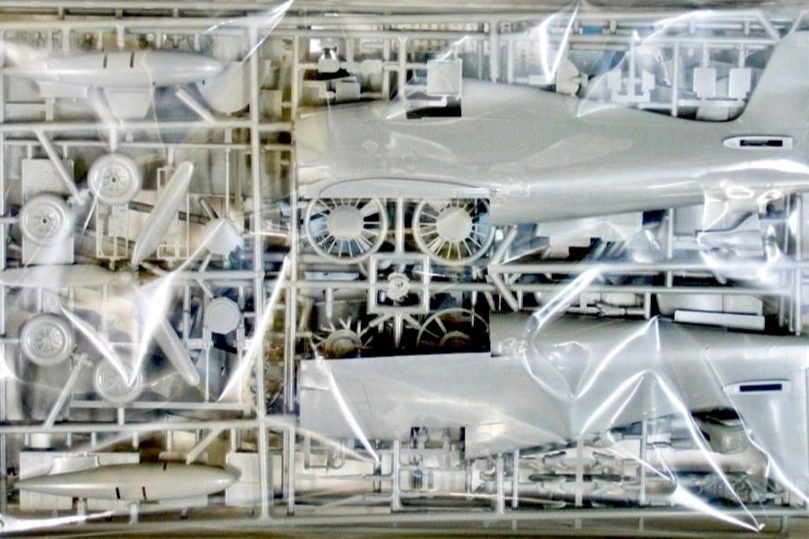
Pièces automobiles
Presque toutes les pièces en plastique à l’intérieur d’une voiture ont été moulées par injection. Les trois matériaux d’injection plastique les plus utilisés dans l’industrie automobile sont le polypropylène (PP) pour les pièces non critiques, le PVC pour sa bonne résistance aux intempéries et l’ABS pour sa grande résistance aux chocs.
Plus de la moitié des pièces en plastique d’une voiture sont fabriquées dans l’un de ces matériaux, y compris les pare-chocs, les pièces de carrosserie intérieures et les tableaux de bord.

Électronique grand public
Les boîtiers de presque tous les appareils électroniques grand public produits en série ont été moulés par injection. L’ABS et le polystyrène (PEHD) sont dans ce cas choisis pour leur excellente résistance aux chocs et leur bonne isolation électrique.

Appareils médicaux
De nombreux matériaux stérilisables et biocompatibles sont disponibles en injection plastique.
Le silicone de qualité médicale est l’un des matériaux les plus populaires dans l’industrie médicale. Cependant, le silicone est un thermodurcissable, ce qui nécessite des machines spéciales et un contrôle du processus, ce qui en augmente le coût.
Pour les applications avec des exigences moins strictes, d’autres matériaux, comme l’ABS, le polypropylène (PP) et le polyéthylène (PE), sont plus courants.
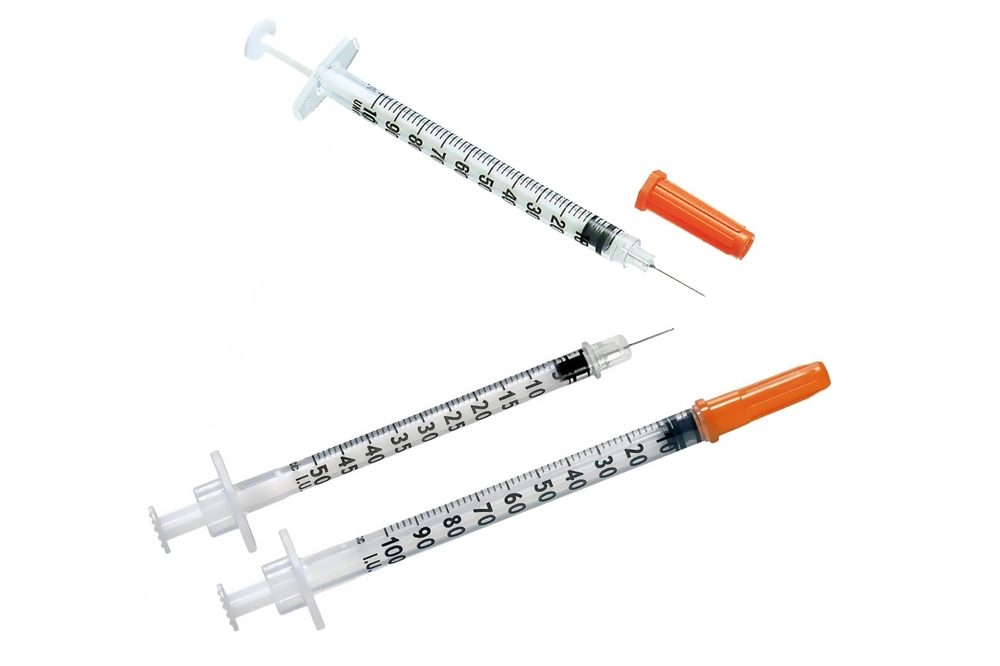
Part 2
Conception pour le moulage par injection
Dans cette section, vous apprendrez comment optimiser vos conceptions pour le moulage par injection.
Suivez les conseils suivants pour gagner du temps, réduire les défaillances et apprendre à créer des caractéristiques qui maximisent les fonctionnalités de vos conceptions.
Défauts courants de l’injection plastique
La plupart des défauts de l’injection plastique sont liés soit à l’écoulement du matériau fondu, soit à sa vitesse de refroidissement non uniforme pendant la solidification.
Voici une liste de défauts qu’un ingénieur devrait garder à l’esprit lors de la conception d’une pièce en injection plastique. Dans la section suivante, nous verrons comment vous pouvez les éviter en suivant de bonnes pratiques de conception.
Gauchissement
Lorsque certaines sections refroidissent (et par conséquent se rétractent) plus rapidement que d’autres, la pièce peut gauchir de façon permanente en raison de contraintes internes.
Les pièces dont l’épaisseur de paroi n’est pas constante sont les plus sujettes au gauchissement.

Retassures
Lorsque l’intérieur d’une pièce se solidifie avant sa surface, un petit creux, appelé retassure, peut apparaître sur une surface normalement plane.
Les pièces avec des parois épaisses ou des nervures mal conçues sont les plus sujettes aux retassures.

Rayures
Lorsque le plastique se rétracte, il exerce une pression sur le moule. Lors de l’éjection, les parois de la pièce glissent et frottent contre le moule, ce qui peut entraîner des rayures.
Les pièces à parois verticales (et sans angle de dépouille) sont les plus sujettes aux rayures.

Lignes d’injection
Lorsque deux flux se rencontrent, de petites décolorations ressemblant à des cheveux peuvent se développer. Ces lignes d’injection affectent l’esthétique des pièces, mais elles diminuent aussi généralement la résistance de la pièce.
Les pièces avec des changements brusques de géométrie ou des trous sont plus sujettes aux lignes d’injection.

Inclusions d’air
L’air emprisonné dans le moule peut empêcher l’écoulement du matériau pendant l’injection, ce qui entraîne une pièce incomplète. Une conception adaptée peut améliorer la fluidité du plastique fondu.
Les pièces avec des parois très minces ou des nervures mal conçues sont plus sujettes aux inclusions d’air.

Traitement des contre-dépouilles
Un aspect important à considérer lors de la conception de pièces en injection plastique réside dans les contre-dépouilles.
Les contre-dépouilles en injection plastique sont des caractéristiques de pièces qui ne peuvent pas être fabriquées avec un simple moule en deux parties, car le matériau gêne l’ouverture du moule ou lors de l’éjection de la pièce.
Chaque filet d’un filetage ou le crochet d’un assemblage par encliquetage sont des exemples de contre-dépouilles. Voici quelques solutions simples pour vous aider à faire face aux contre-dépouilles :
Démoulage naturel
Une autre façon de traiter les contre-dépouilles est d’enlever le matériau sous ou au-dessus de la zone problématique. De cette façon, la contre-dépouille est éliminée car la pièce entière peut être prise en charge directement par le moule.
Le démoulage naturel est une astuce utile pour traiter les contre-dépouilles sur les zones internes de la pièce (pour les encliquetages) ou sur les côtés de la pièce (pour les trous ou les poignées).

Voici quelques exemples de la façon dont les pièces moulées par injection peuvent être repensées pour éviter les contre-dépouilles: essentiellement, le matériau est retiré dans la zone sous la contre-dépouille, éliminant ainsi complètement le problème.
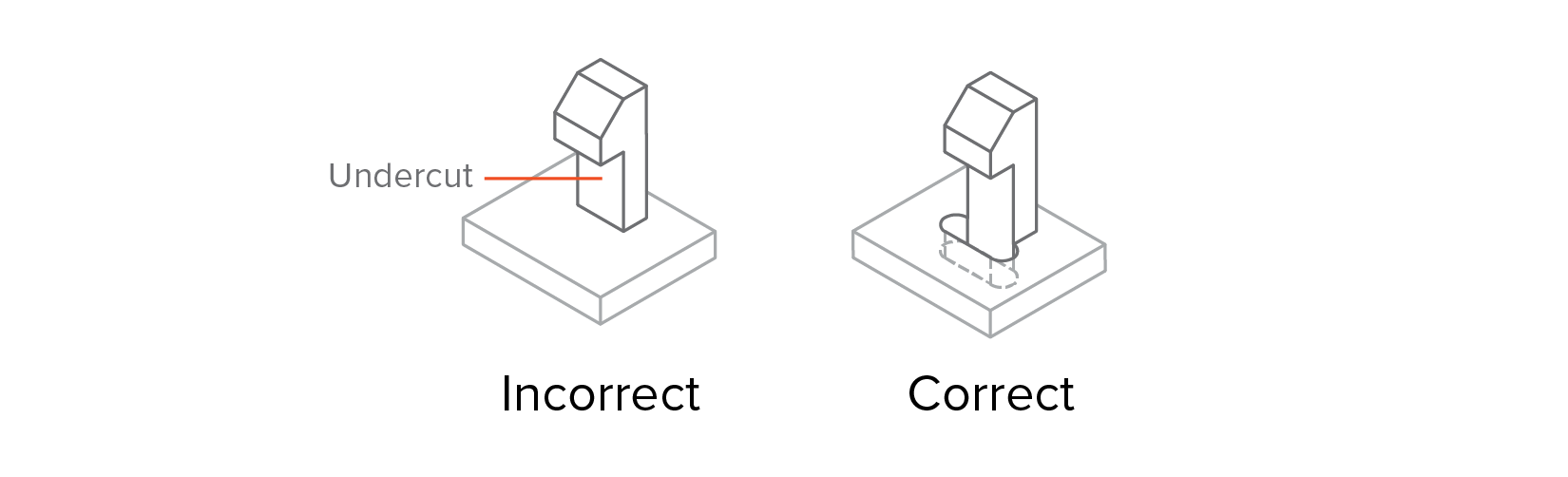
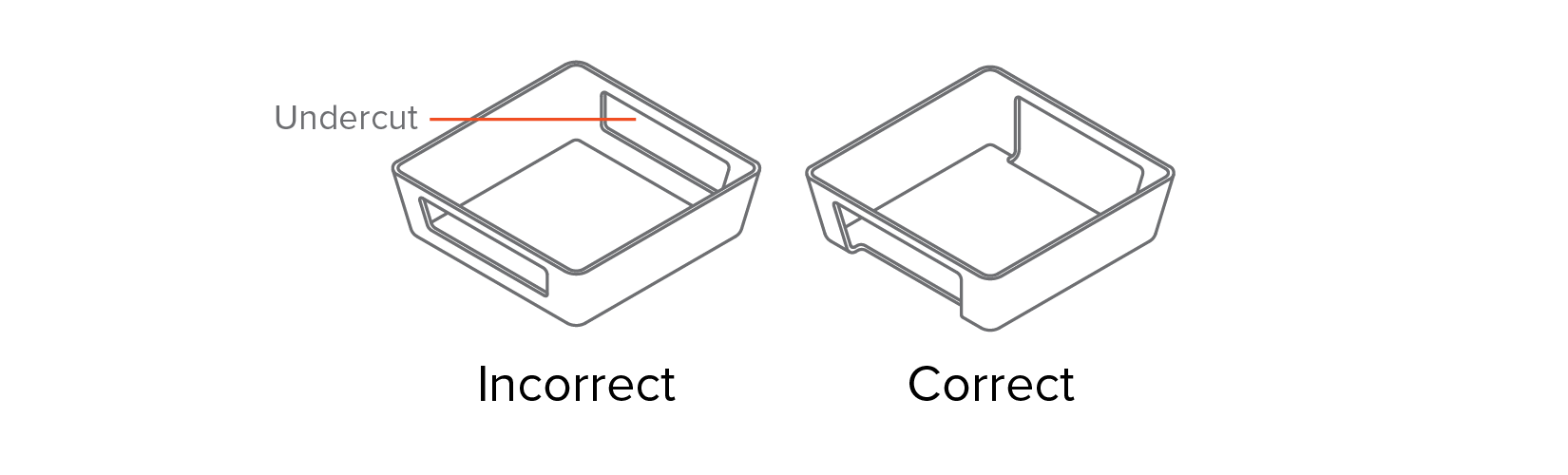
Déplacer le plan de joint
La façon la plus simple de faire face à une contre-dépouille est de déplacer le plan de joint du moule pour être en intersection avec celle-ci.
Cette solution convient à de nombreux modèles avec contre-dépouilles sur une surface extérieure. N’oubliez pas d’ajuster les angles de dépouille en conséquence.

Démoulage en force
Si la pièce est suffisamment flexible, il est possible de déformer la pièce pendant l’éjection. Le démoulage en force est utilisé pour les éléments internes, tels que les filetages des bouchons de bouteilles.
Utilisez ces conseils pour concevoir une pièce qui sera démoulée en force :
● Choisissez un matériau flexible tel que PP, PE ou Nylon (PA).
● La hauteur de la contre-dépouille doit être de 5% du diamètre du trou.
● Utilisez un angle de glissement de 30° à 45°.

Il est recommandé d’éviter de séparer les contre-dépouilles dans les pièces en plastique renforcé de fibres. En règle générale, les plastiques flexibles tels que le PP, le HDPE our le Nylon (PA) peuvent tolérer des contre-dépouilles jusqu’à 5% de leur diamètre.
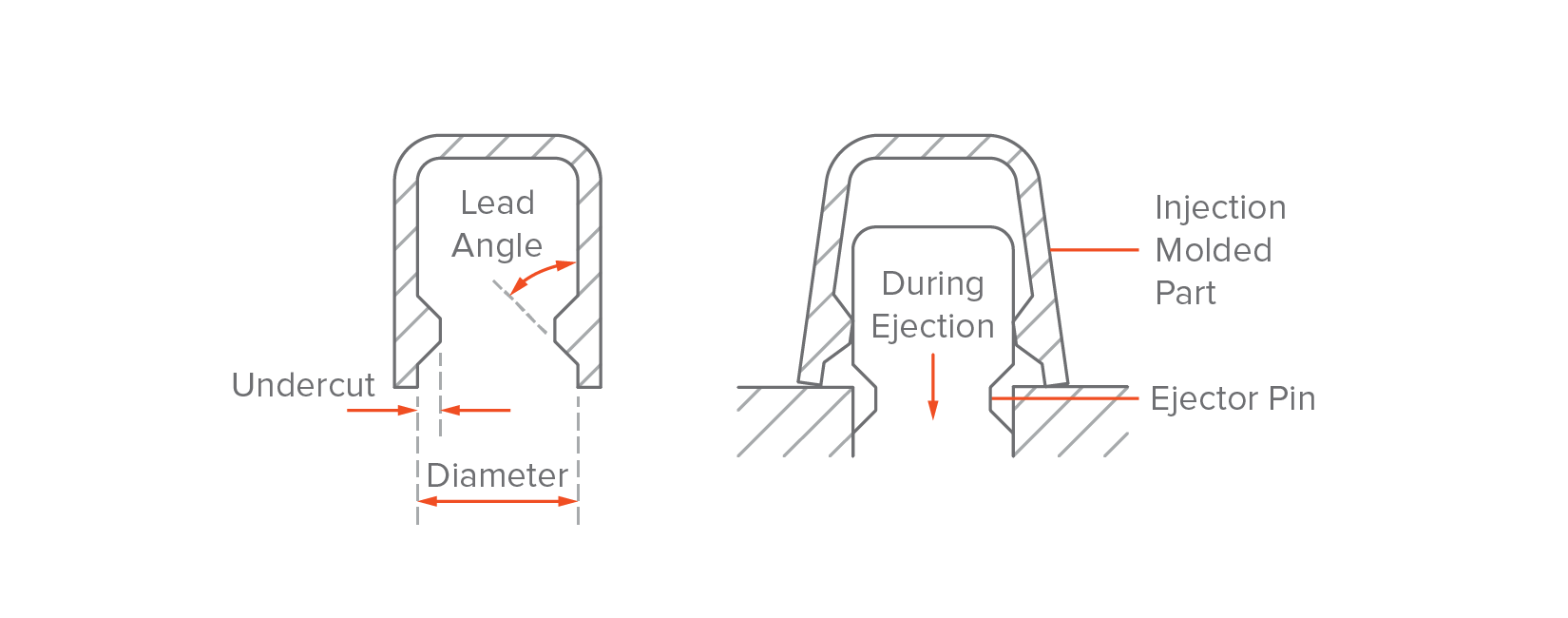
Tiroirs
Si aucune des solutions ci-dessus n’est viable, on peut utiliser des noyaux qui glissent hors de la pièce par le côté avant qu’elle ne soit démoulée.
Les tiroirs doivent être utilisés avec parcimonie car ils ajoutent de la complexité et augmentent le coût global d’un moule de 15 à 30 %.
Suivez ces conseils lors de la conception d’un tiroir :
● Le tiroir doit se déplacer dans une direction parallèle au plan de joint.
● Les angles de dépouille doivent être ajoutés comme d’habitude.
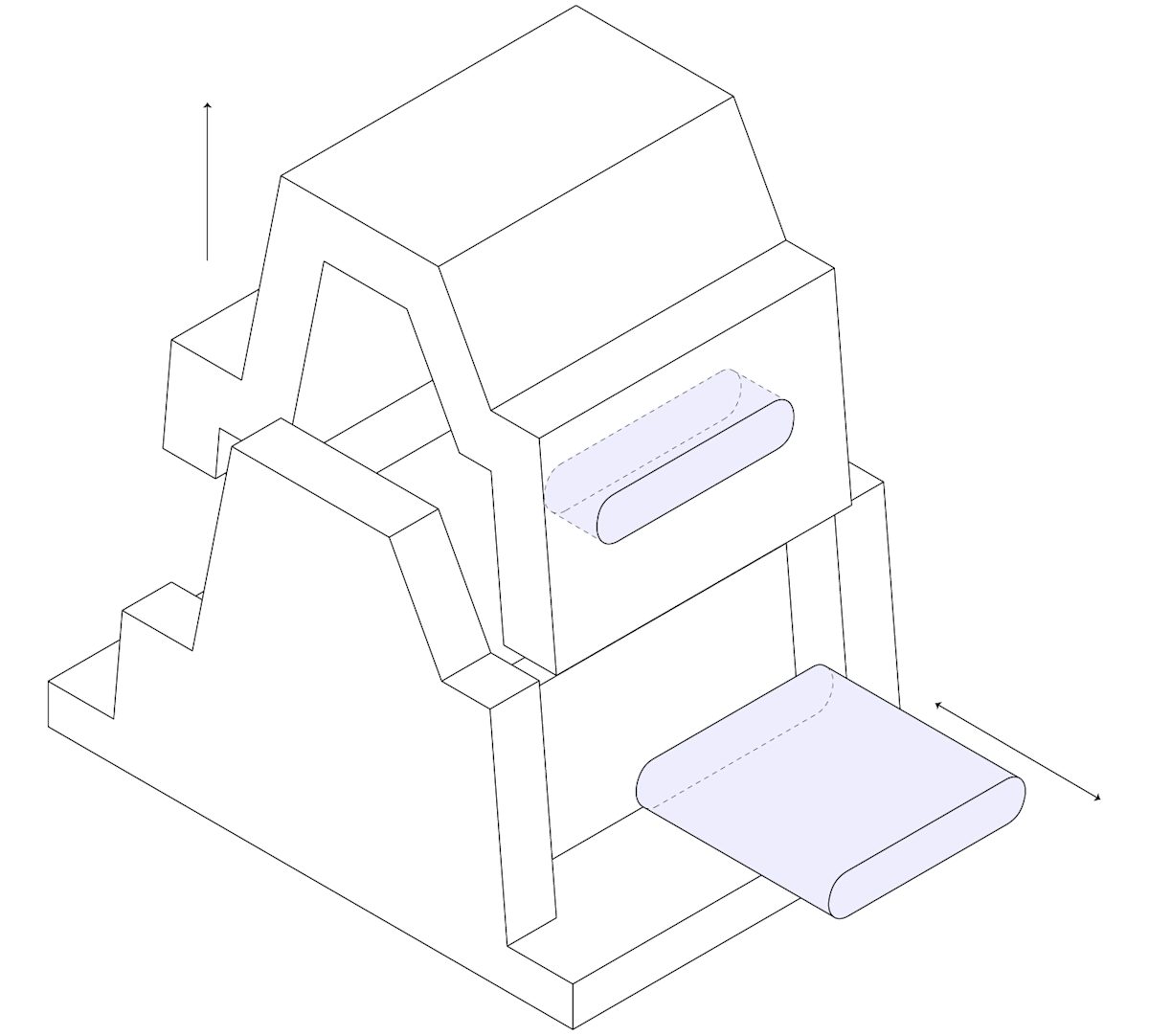
Caractéristiques de conception d’une pièce injectée
Nous énumérons ci-dessous des conseils pratiques sur la façon de concevoir les caractéristiques les plus communes rencontrées dans les pièces réalisées en injection plastique. Utilisez-les pour améliorer le caractère fonctionnel de vos conceptions, tout en respectant les règles de conception de base.
(Lire les conseils de conception complets pour l’injection plastique →) (https://www.hubs.com/knowledge-base/how-design-parts-injection-molding “Design for Injection Molding”)
Fixations filetées (puits et filetages)
Il existe 3 façons d’ajouter des fixations à une pièce moulée par injection: en concevant un filetage directement sur la pièce, en ajoutant un puits où la vis peut être fixée, ou en incluant un filetage.
La modélisation d’un filetage directement sur la pièce est possible, mais déconseillée, car les dents du fil sont essentiellement des contre-dépouilles, augmentant considérablement la complexité et le coût du moule (nous en parlerons plus en détail dans une prochaine section). Un exemple de pièce moulée par injection avec un filetage est le bouchon d’une bouteille.
Puits
Les puits sont utilisés comme points de fixation ou d’assemblage (en combinaison avec des vis auto-taraudeuses ou des inserts filetés).
Considérez les bossages comme des nervures circulaires, en effet, les mêmes conseils généraux de conception s’appliquent. Pensez également à ce qui suit :
● Évitez de concevoir des puits directement contre la paroi principale.
● Renforcez les puits avec des nervures ou connectez-les à une paroi principale.
Pour les puits avec inserts :
● Utilisez un diamètre extérieur égal à 2 fois le diamètre nominal de l’insert.

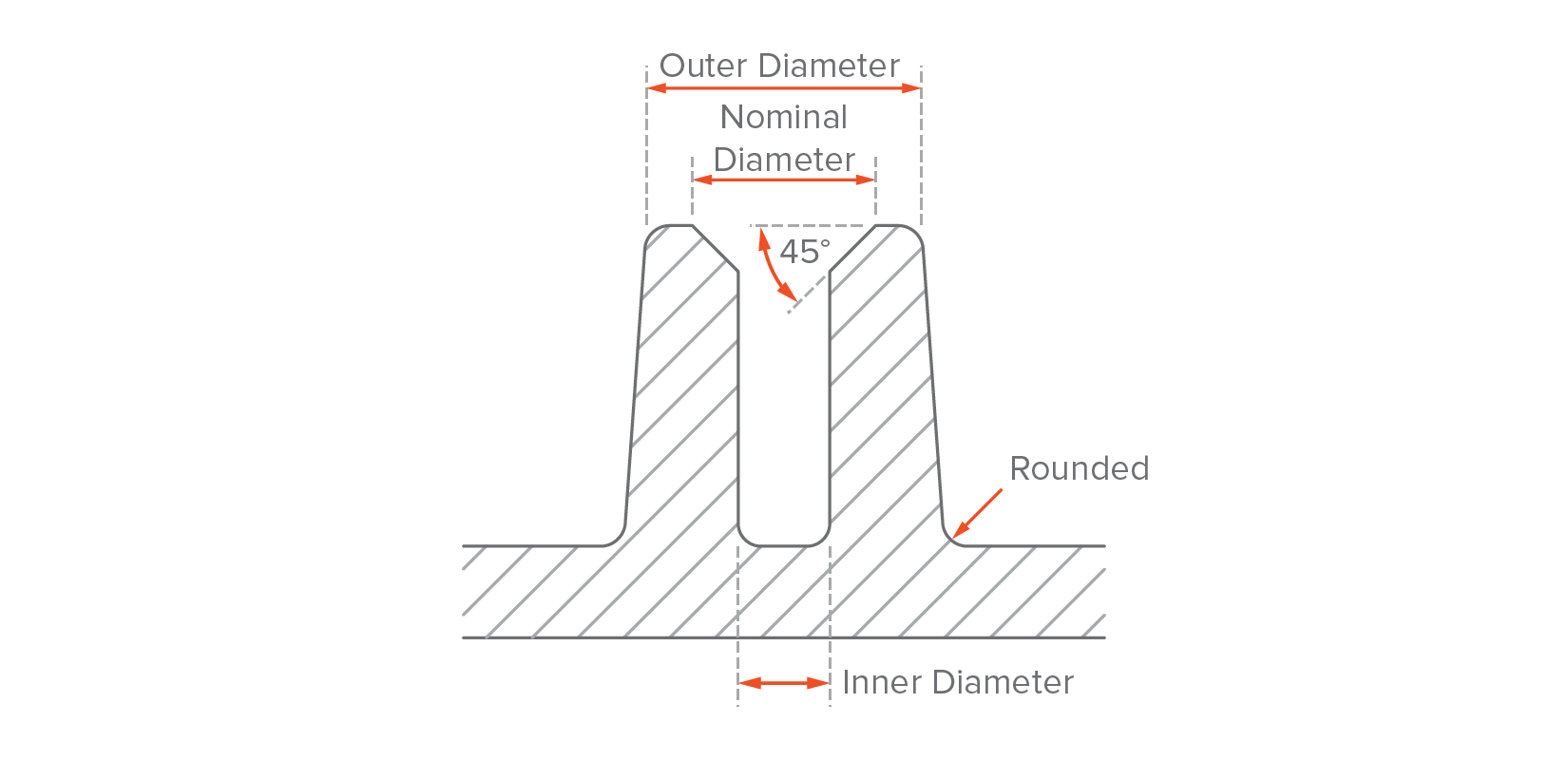
Lorsque des puits sont utilisés comme __points de fixation__, le diamètre extérieur du puits doit être 2x le diamètre nominal de la vis ou de l'insert et son diamètre intérieur égal au diamètre du centre de la vis. Le trou du puits doit s'étendre jusqu'au niveau de la paroi de base, même si la profondeur totale n'est pas nécessaire pour l'assemblage, afin de maintenir une épaisseur de __paroi uniforme__ dans tout l'élément. Ajoutez un chanfrein pour une insertion facile de la vis ou de l'insert..
__Pour de meilleurs résultats:__
Filetages
Les filetages peuvent être ajoutés directement à la conception de la pièce moulée, mais ils introduisent des contre-dépouilles. En remplacement, il est également possible d’utiliser des inserts filetés.
Suivez ces conseils lorsque vous concevez des pièces avec des filetages :
● Conservez une zone sans filetage de 0,8 mm à chaque extrémité de celui-ci.
● Utilisez un filetage avec un pas supérieur à 0,8 mm (32 filetages par pouce).
● Préférez l’utilisation d’un filetage trapézoïdal ou en dents de scie.
Pour traiter les contre-dépouilles créées :
● Pour les filetages intérieurs, envisagez l’utilisation de contre-dépouilles de démoulage.
● Pour les filetages extérieurs, placez-les le long du plan de joint.

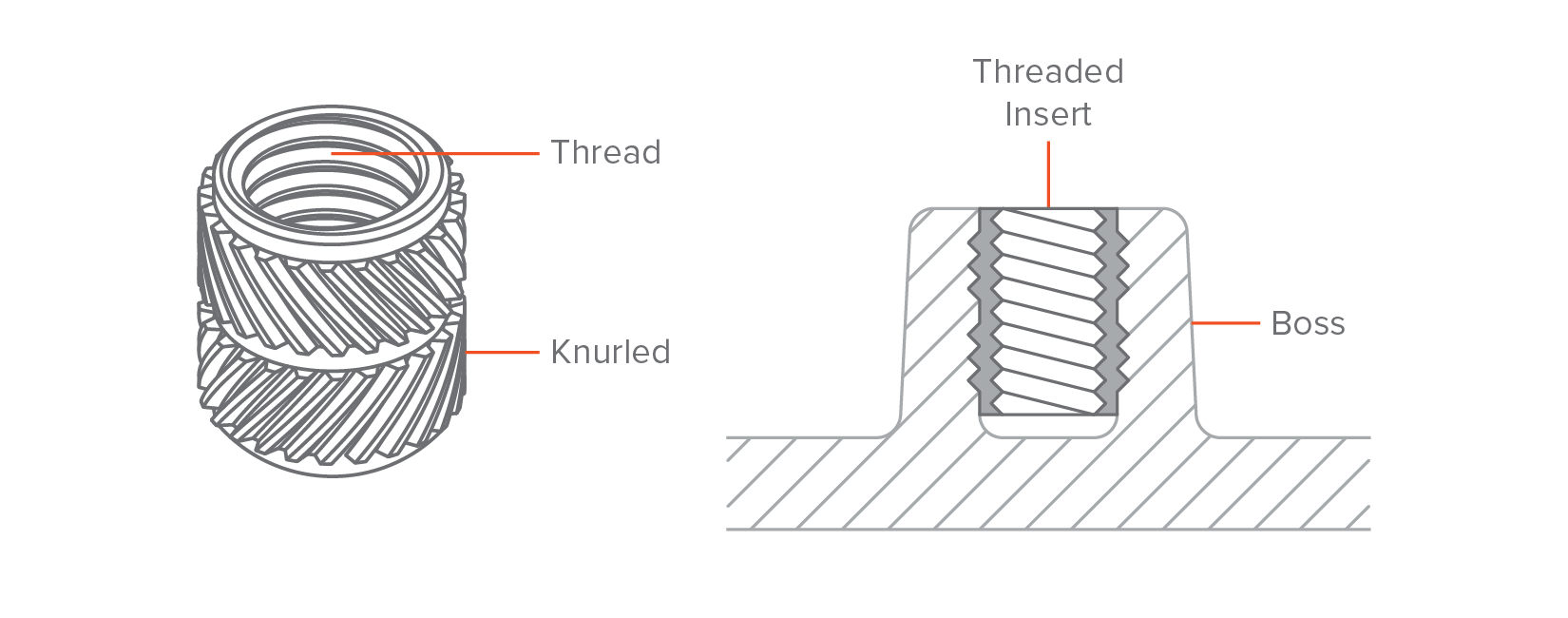
__Pour de meilleurs résultats:__
Meilleure façon de gérer les contre-dépouilles créées:
Nervures
Lorsque l’épaisseur de paroi maximale recommandée n’est pas suffisante pour répondre aux exigences fonctionnelles d’une pièce, des nervures peuvent être utilisées pour améliorer sa rigidité.
Lors de la conception des nervures :
● Utilisez une épaisseur égale à 0,5 fois l’épaisseur de la paroi principale.
● Définissez une hauteur inférieure à 3 fois l’épaisseur de la nervure
● Utilisez un congé de base dont le rayon est supérieur à ¼ de l’épaisseur de la nervure
● Ajoutez un angle de dépouille d’au moins 0,25° - 0,5°.
● Définissez une distance minimale entre les nervures et les parois de 4 fois l’épaisseur des nervures.

Clips
L’encliquetage est un moyen économique et rapide d’assembler deux pièces sans quincaillerie ni outils.
Lors de la conception de clips en injection plastique :
● Ajoutez une dépouille sur les parois latérales du clip.
● Utilisez une épaisseur de 0,5 fois l’épaisseur de la paroi principale.
● Ajustez la largeur et la longueur pour contrôler la flexion et la force.
● Pensez à la manière de traiter la contre-dépouille créée.
Pour des conseils détaillés, voir cet article du MIT.

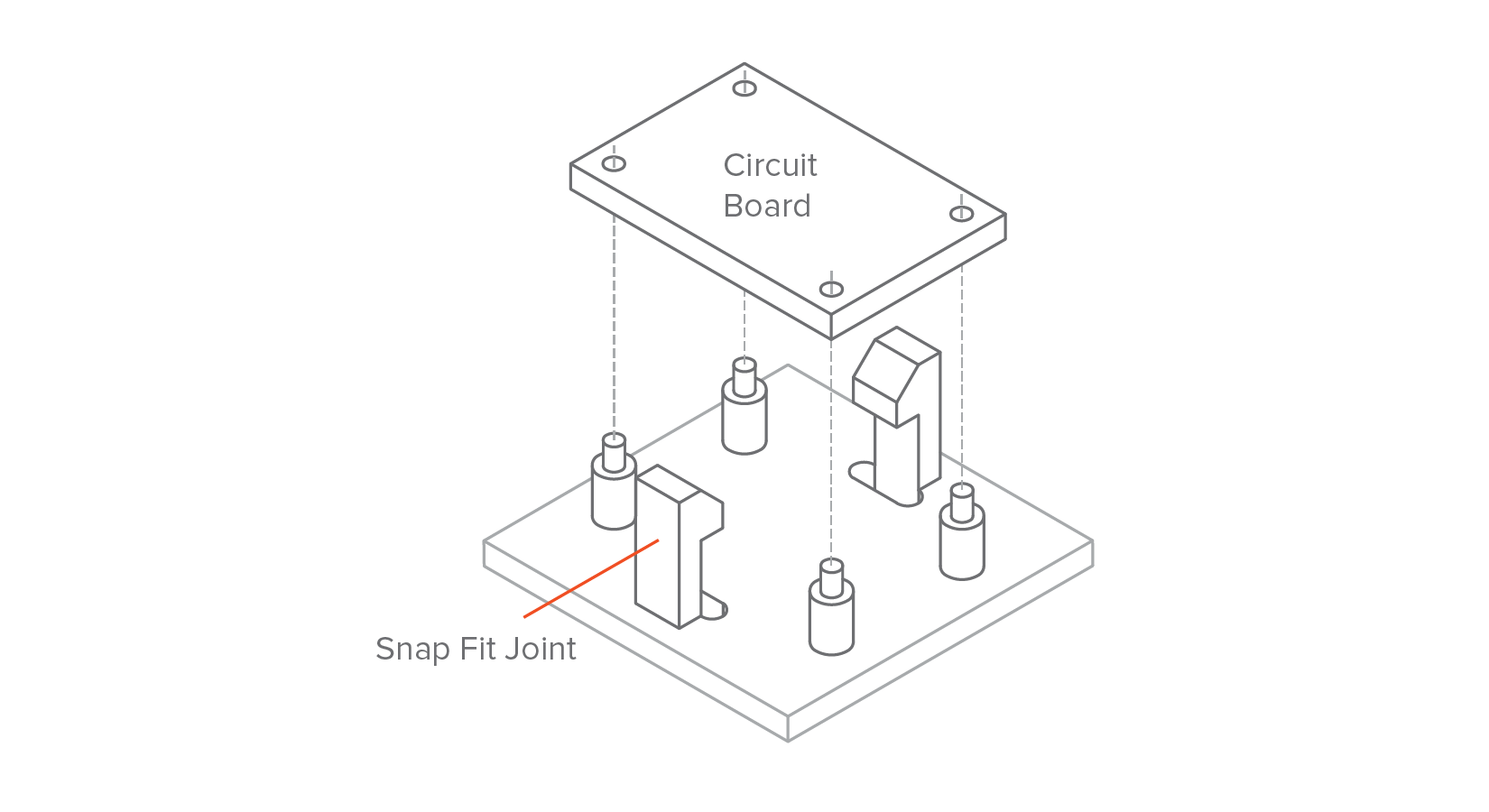
Dans l'exemple ci-dessus, la conception de joint à encliquetage la plus courante (connue sous le nom de __joint à enclenchement cantilever__) est illustrée. Comme pour les nervures, ajoutez un angle de dépouille à vos joints à encliquetage et utilisez une épaisseur minimale de 0.5 fois l'épaisseur de la paroi.
Des directives spécifiques sur la conception de joints à encliquetage sont un gros sujet qui dépasse le cadre de cet article. pour des informations plus détaillées, veuillez vous référer à cet article from MIT.
Pour de meilleurs résultats:
Charnières intégrées
Les charnières intégrées sont de minces sections de plastique qui relient deux segments d’une pièce et lui permettent de fléchir et de plier.
Voici quelques conseils pour vous aider à concevoir une charnière intégrée :
● Choisissez un matériau flexible (par exemple PP, PE ou Nylon)
● Concevez vos charnières avec une épaisseur comprise entre 0,20 et 0,35 mm
● Utilisez des parois de support d’une épaisseur égale à l’épaisseur de la paroi principale.
● Ajoutez des congés aussi grands que possible
Pour des conseils détaillés, veuillez vous référer à ce guide MIT.

A well-designed hinge is shown below. The recommended minimum thickness of the hinge ranges between 0.20 and 0.35 mm, with higher thicknesses resulting in more durable, but stiffer, parts.
{{img}}
*Example of a living hinge (left) and recommended design dimensions for PP or PE (right)*
Before going to full-scale production, prototype your living hinges using
CNC machining or
3D printing to determine the geometry and stiffness that best fits your application. Add generous fillets and design shoulders with a uniform wall thickness as the main body of the part to improve the material flow in the mold and minimize the stresses. Divide hinges longer than 150 mm in two (or more) to improve lifetime.
For detailed guidelines, please refer to this MIT guide.
For best results:
-
Design hinges with a thickness between 0.20 and 0.35 mm
-
Select a flexible material (PP, PE or PA) for parts with living hinges
-
Use shoulders with a thickness equal the thickness of the main wall
-
Add fillets as large as possible
Nervures d’écrasement
Les nervures d’écrasement se déforment et créent un frottement entre la pièce et le composant inséré, le maintenant en place.
Il s’agit d’une méthode rapide et peu coûteuse pour incorporer des roulements ou d’autres inserts dans vos conceptions. Pour les applications haut de gamme, envisagez plutôt d’utiliser un ajustement serré.
Lors de la conception des nervures d’écrasement :
● Utilisez trois nervures circulaires d’un rayon de 2 mm.
● Ajoutez un chevauchement minimal de 0,25 mm entre la nervure et l’insert.
● Ajoutez une dépouille au trou mais pas sur les nervures.

Un exemple de pièce avec des nervures d’écrasement est illustré ci-dessous. l’utilisation de trois nervures d’écrasement est recommandée pour assurer un bon alignement.La hauteur/rayon recommandée pour chaque nervure est de 2 mm. Ajoutez une interférence minimale de 0.25 mm entre la nervure d’écrasement et la pièce ajustée. En raison du petit contact de surface avec le moule, les nervures d’écrasement peuvent être conçues sans angle de dépouille.
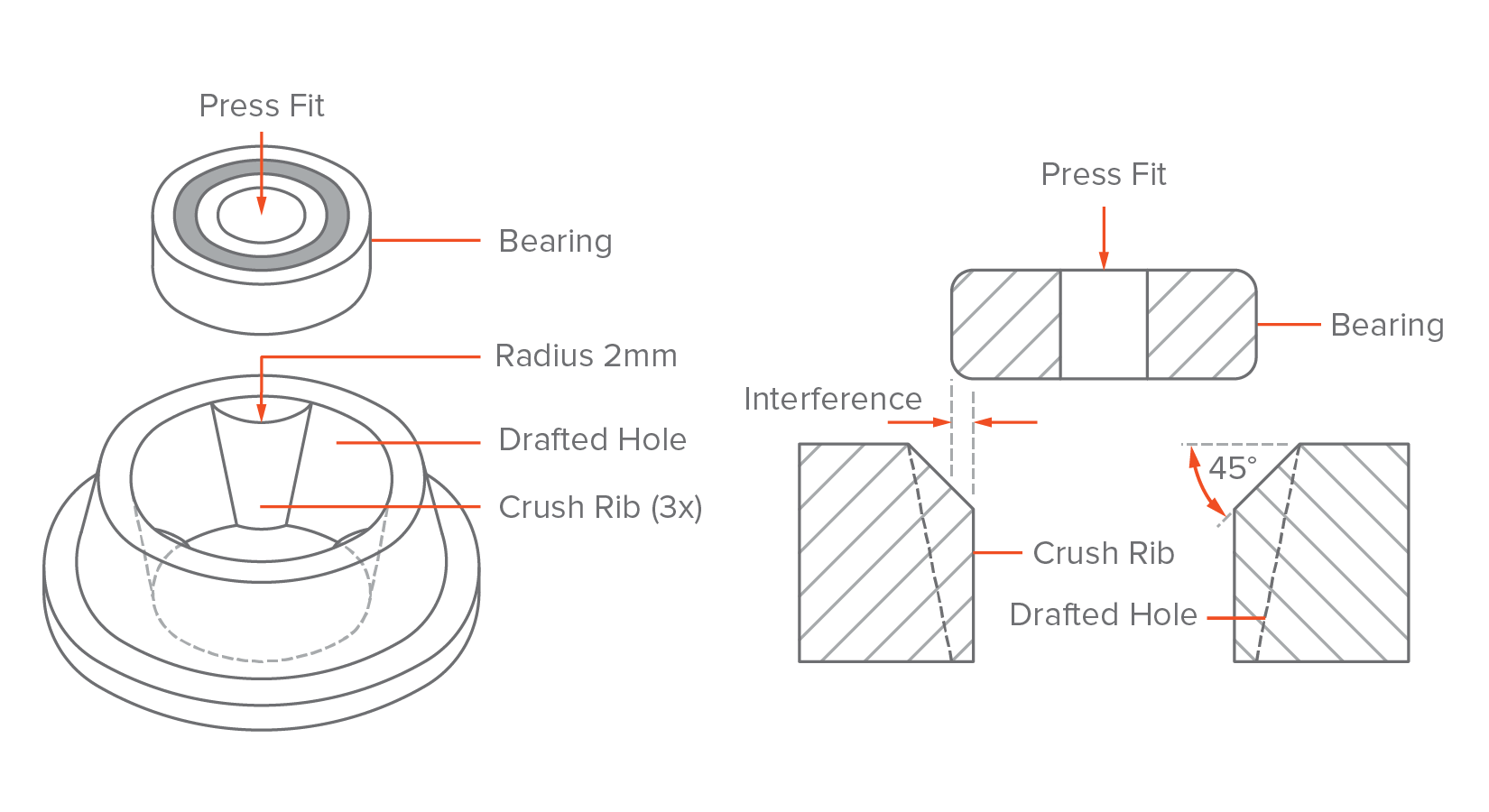
__Pour de meilleurs résultats:__
Lettrage et symboles
Le texte, les logos et autres symboles peuvent être marqués en creux ou en relief sur la surface des pièces moulées par injection.
Voici quelques conseils pour ajouter du texte :
● Préférez le marquage en relief au marquage en creux.
● Alignez le texte perpendiculairement au plan de joint.
● Utilisez une hauteur (ou une profondeur) supérieure à 0,5 mm.
● Utilisez une police de caractères d’une épaisseur uniforme.
● La taille de la police doit être d’au moins 20 points.

Pour de meilleurs résultats:
Tolérances
L’injection plastique produit généralement des pièces avec des tolérances de ± 0,500 mm.
Des tolérances plus serrées sont possibles dans certaines circonstances (jusqu’à ± 0,125 mm et même ± 0,025 mm), mais elles augmentent considérablement le coût.
Pour les petites séries ( < 10 000 unités), envisagez d’utiliser une opération secondaire (telle que le perçage) pour améliorer la précision. Cela garantit un assemblage correct de la pièce avec d’autres composants ou inserts (par exemple, lors de l’utilisation d’ajustements à la presse).

Règles de conception pour l’injection plastique
Voyons comment ces limitations liées au processus de fabrication peuvent être transformées en règles de conception applicables.
Dans les sections suivantes, nous résumons les règles de conception les plus importantes à suivre lors de la conception de pièces en injection plastique, ainsi que des conseils sur la façon de concevoir correctement les caractéristiques les plus courantes des pièces moulées par injection.
(Lire les conseils de conception complets pour l’injection plastique →) (https://www.hubs.com/knowledge-base/how-design-parts-injection-molding “Conception pour l’injection plastique”)
Utiliser une épaisseur de paroi constante
Épaisseur recommandée : 1 mm et 3 mm
Concevez toujours vos pièces avec l’épaisseur de paroi la plus petite possible (et constante), pour éviter les déformations et les retassures.
Si des sections plus épaisses sont nécessaires, évidez-les et utilisez des nervures pour ajouter de la rigidité. N’oubliez pas que chaque augmentation de 10 % de l’épaisseur de la paroi augmente la rigidité d’environ 30 %.
Voir les recommandations d’épaisseur de paroi spécifiques au matériau →

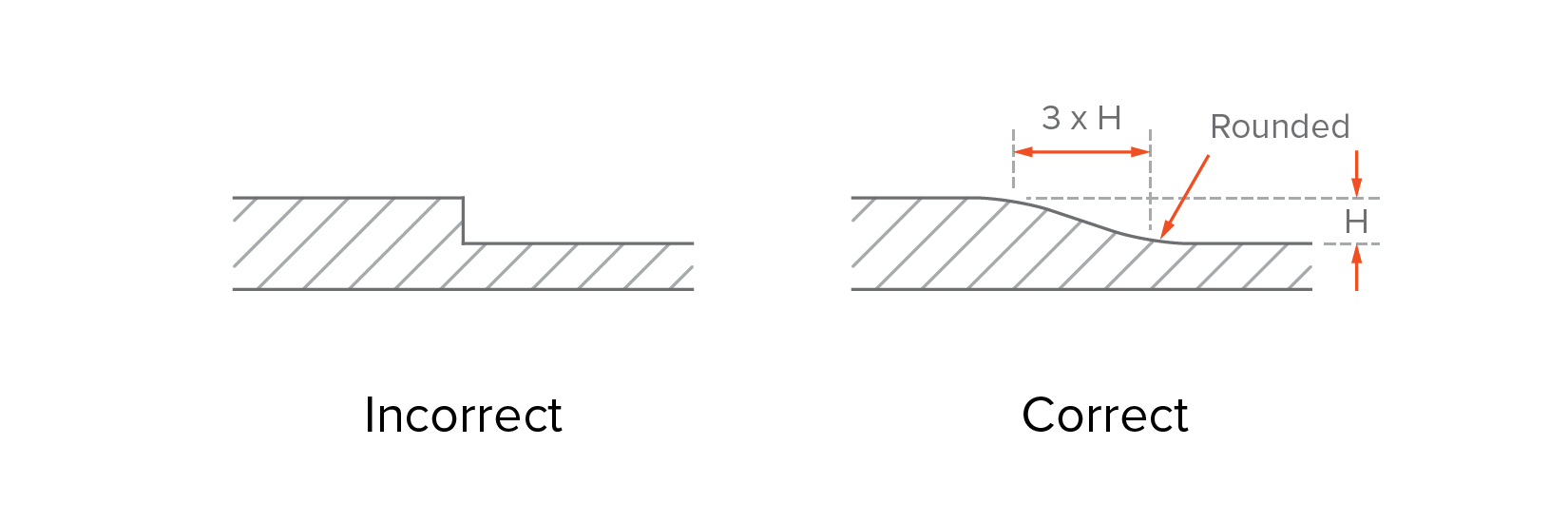
Une épaisseur de paroi comprise entre 1,2 mm et 3 mm est une valeur sûre pour la plupart des matériaux. Le tableau suivant résume __les épaisseurs de paroi spécifiques recommandées__ pour certains des matériaux de moulage par injection les plus courants:
Matériaux | Épaisseur de paroi recommandée [mm] | Épaisseur de paroi recommandée [pouces] |
---|---|---|
Polypropylene (PP) | 0.8 - 3.8 mm | 0.03'' - 0.15'' |
ABS | 1.2 - 3.5 mm | 0.045'' - 0.14'' |
Polyethylene (PE) | 0.8 - 3.0 mm | 0.03'' - 0.12'' |
Polystyrene (PS) | 1.0 - 4.0 mm | 0.04'' - 0.155'' |
Polyurethane (PUR) | 2.0 - 20.0 mm | 0.08'' - 0.785'' |
Nylon (PA 6) | 0.8 - 3.0 mm | 0.03'' - 0.12'' |
Polycarbonate (PC) | 1.0 - 4.0 mm | 0.04'' - 0.16'' |
PC/ABS | 1.2 - 3.5 mm | 0.045'' - 0.14'' |
POM (Delrin) | 0.8 - 3.0 mm | 0.03'' - 0.12'' |
PEEK | 1.0 - 3.0 mm | 0.04'' - 0.12'' |
Silicone | 1.0 - 10.0 mm | 0.04'' - 0.40'' |
Pour de meilleurs résultats:
Creuser les sections épaisses
Les sections épaisses peuvent entraîner divers défauts, notamment le gauchissement et l’affaissement. Il est essentiel de limiter l’épaisseur maximale de n’importe quelle section de votre conception aux valeurs recommandées en les creusants .
Pour améliorer la résistance de la section creuse, utilisez des nervures pour concevoir des structures de résistance et de rigidité égales mais avec une épaisseur de paroi réduite. Une pièce bien conçue avec des sections creuses est illustrée ci-dessous:
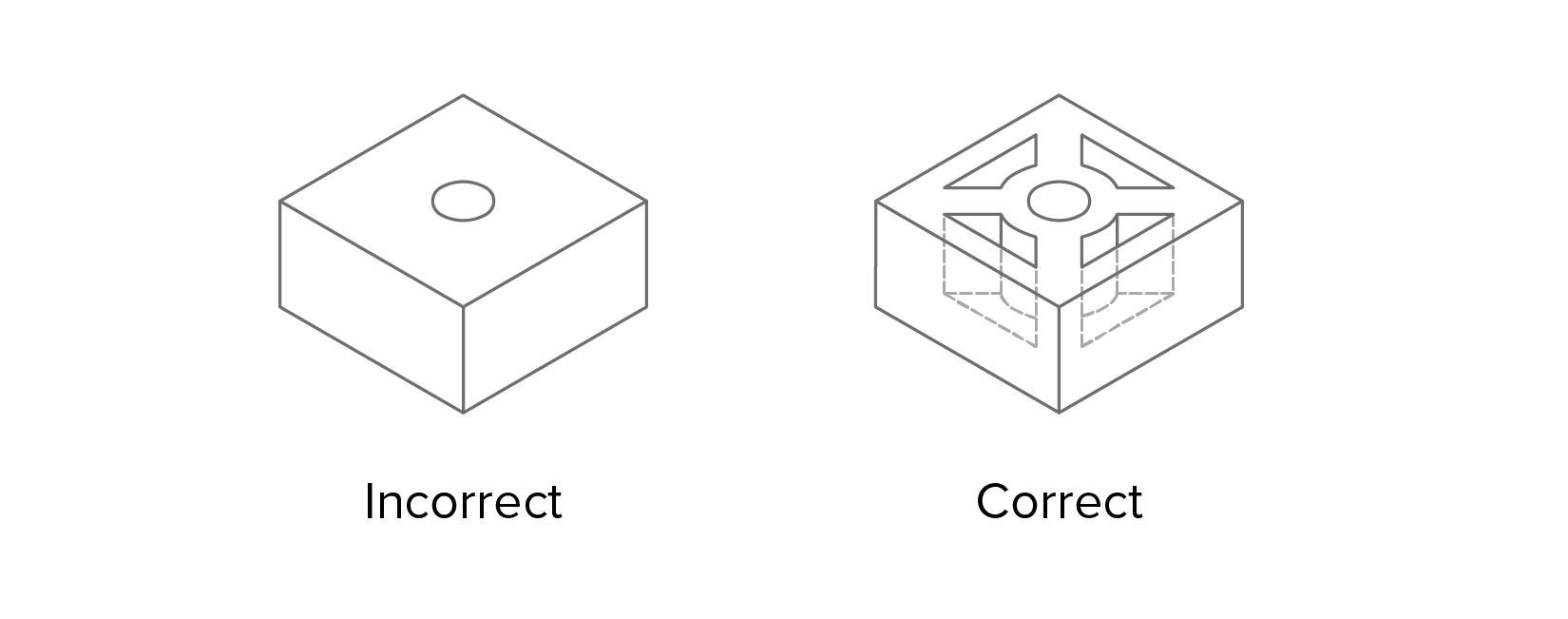
Les nervures peuvent également être utilisées pour améliorer la rigidité des __sections horizontales__ sans augmenter leur épaisseur. N'oubliez pas cependant que les limites d'épaisseur de paroi s'appliquent toujours. Le dépassement de l'épaisseur de nervure recommandée (voir ci-dessous) peut entraîner des marques de coulée.
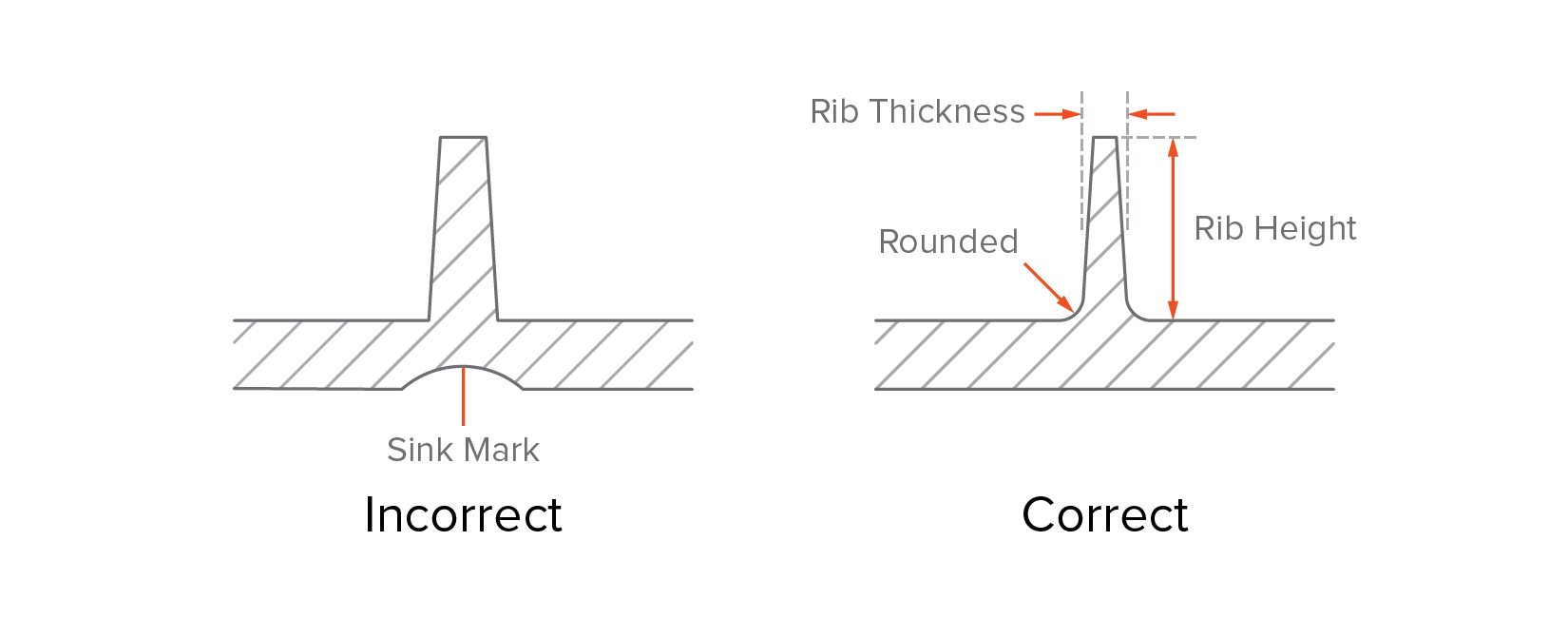
Pour de meilleurs résultats:
Ajouter des transitions douces
Recommandation : 3 fois la différence d’épaisseur de paroi.
Parfois, il est impossible d’éviter des sections avec des épaisseurs de paroi différentes. Dans ces cas, utilisez un chanfrein ou un congé pour rendre la transition aussi douce que possible.
De même, la base des éléments verticaux (comme les nervures, les bossages, les encliquetages) doivent toujours être dotées de congés.

Ajoutez des congés sur toutes les arêtes
Arêtes internes : > 0,5 × épaisseur de paroi
__Arêtes externes :__congé intérieur + épaisseur de paroi
La règle de l’épaisseur de paroi constante doit également être appliquée aux coins de la pièce. Ajoutez un congé avec un rayon aussi grand que possible sur toutes les arêtes internes et externes.

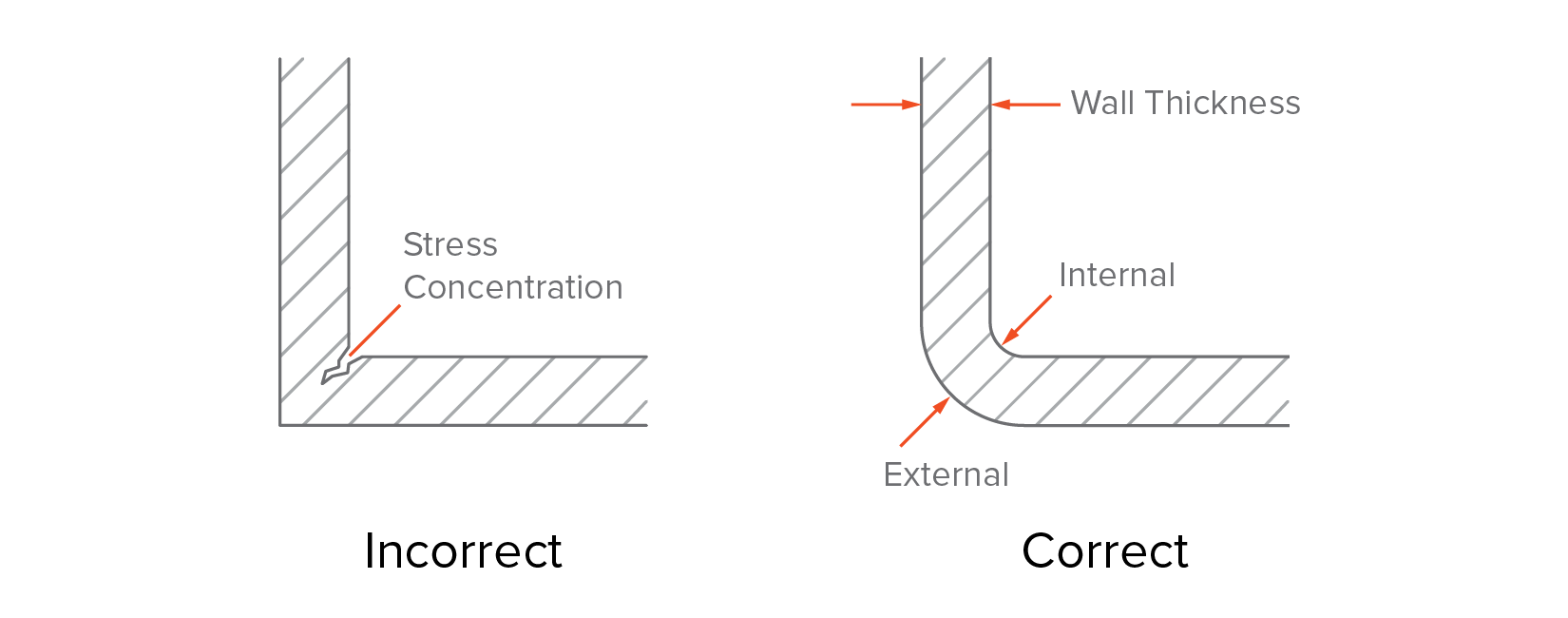
Pour de meilleurs résultats:
Ajouter des angles de dépouille
__Minimum recommandé : __ > 2°
Ajoutez une dépouille à toutes les parois verticales pour faciliter le démoulage de la pièce et éviter les rayures. Si elles sont fonctionnelles, les parois extérieures peuvent être laissées sans dépouille (voir les briques Lego).
Augmenter l’angle de dépouille au-delà de l’angle recommandé dans ces cas :
● Pour les pièces de plus de 50 mm de hauteur, augmenter la dépouille de 1° tous les 25 mm.
● Pour les pièces avec une finition texturée, augmenter la dépouille de 1° à 2° supplémentaire

Une règle empirique consiste à augmenter l’angle de dépouille d’un degré tous les 25 mm. Par exemple, ajoutez un angle de dépouille de 3o degrés à une entité de 75 mm de hauteur. Un angle de dépouille plus grand doit être utilisé si la pièce présente une finition de surface texturée. En règle générale, ajoutez 1o à 2o degrés supplémentaires aux résultats des calculs ci-dessus.
n’oubliez pas que les angles de dépouille sont également nécessaires pour les nervures. Sachez cependant que l’ajout d’un angle réduira l’épaisseur de la nervure, assurez-vous donc que votre conception est conforme à l’épaisseur de paroi minimale recommandée.
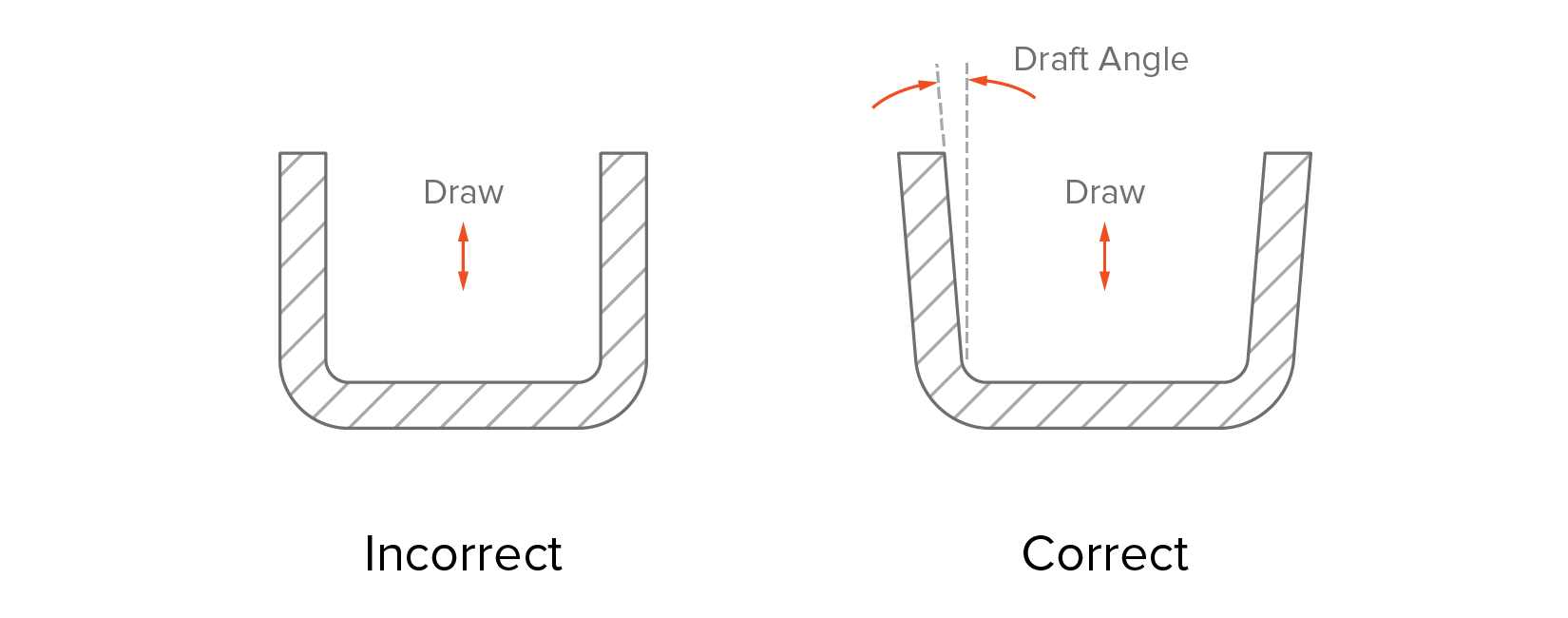
__Pour de meilleurs résultats:__
Part 3
Matières en injection plastique
L’injection plastique est compatible avec une très large gamme de plastiques. Dans cette section, vous en apprendrez davantage sur les caractéristiques clés des matériaux les plus populaires. Nous verrons également les finitions de surface standards qui peuvent être appliquées aux pièces moulées par injection.
Matériaux d’injection plastique
Tous les thermoplastiques peuvent être moulés par injection. Certains thermodurcissables et silicones liquides sont également compatibles avec le procédé d’injection plastique.
Ils peuvent également être renforcés avec des fibres, des particules de caoutchouc, des minéraux ou des agents ignifugés pour modifier leurs propriétés physiques. Par exemple, la fibre de verre peut être mélangée avec les granulés dans des proportions de 10 %, 15 % ou 30 %, ce qui donne des pièces plus rigides.
Un additif qui est couramment utilisé pour améliorer la rigidité des pièces moulées par injection est la fibre de verre. Les fibres de verre peuvent être mélangées aux pastilles à des rapports de 10%, 15% ou 30%, ce qui donne des propriétés mécaniques différentes.
Colorant peut être ajouté au mélange (dans un rapport d’environ 3%) pour créer une grande variété de pièces colorées. Les couleurs standard incluent le rouge, le vert, le jaune, le bleu, le noir et le blanc et elles peuvent être mélangées pour créer différentes nuances.
Finitions de surface et normes SPI
Les pièces moulées par injection ne reçoivent généralement pas d’opérations supplémentaires après la sortie du moule, mais le moule lui-même peut recevoir différents niveaux de finition.
De cette façon, les besoins esthétiques (par exemple, une surface au poli miroir ou mate) ou techniques (par exemple, une rugosité de surface spécifique ou des tolérances) peuvent être satisfaits.
La Société de l’industrie plastique (SPI) définit plusieurs procédures de finition standards qui permettent d’obtenir différents états de surface des pièces.
Finition | Description | Application |
---|---|---|
__Finition brillante __ Norme SPI : A-1, A-2, A-3 |
Le moule est poncé à la pâte diamant, et permet d’obtenir des pièces au fini miroir. | Convient pour les pièces dont la surface doit être la plus lisse possible à des fins esthétiques ou fonctionnelles (Ra < 0,10 μm) |
Finition semi-brillante Norme SPI : B-1, B-2, B-3 |
Le moule est poncé à l’aide d’un papier abrasif à grain fin, ce qui permet d’obtenir des pièces avec une finition de surface lisse. | Convient pour les pièces qui nécessitent un bon aspect visuel, mais pas un aspect très brillant. |
__Finition matte __ Norme SPI : C-1, C-2, C-3 |
Le moule est poncé à l’aide d’une pierre abrasive à grain fin, retirant toutes les traces d’usinage. | Convient pour les pièces avec des exigences esthétiques faibles, mais lorsque les marques d’usinage ne sont pas acceptables. |
Finition texturée Norme SPI : D-1, D-2, D-3 |
Le moule est d’abord poncé à l’aide d’une pierre abrasive à grain fin, et ensuite par sablage donnant ainsi une surface texturée. | Convient pour les pièces qui nécessitent un fini de surface satiné ou mat. |
Finition brute d’usinage | La finition du moule est à la discrétion du fabricant. Des marques d’outils peuvent être visibles. | Convient pour les pièces non cosmétiques, industrielles ou les composants cachés. |
Part 4
Conseils de réduction des coûts
Apprenez-en davantage sur les principaux inducteurs de coût de l’injection plastique et sur trois conseils pratiques qui vous aideront à réduire vos coûts tout en respectant votre budget.
Inducteurs de coûts dans l’injection plastique
Les principaux inducteurs de coût dans l’injection plastique sont :
- Les coûts d’outillage déterminés par le coût total de la conception et de l’usinage du moule.
- Les coûts des matières premières déterminés par le volume de la matière utilisée et son prix au kilogramme.
- Les coûts de production déterminés par le temps total d’utilisation de la presse à injecter.
Les coûts d’outillage sont constants (de 3 000 € à 5 000 €) et indépendants du nombre total de pièces fabriquées, tandis que les coûts des matériaux et de production dépendent du volume de production.
Pour les petites productions (1 000 à 10 000 unités), le coût de l’outillage a le plus grand impact sur le coût global (environ 50 à 70 %). Il vaut donc la peine de modifier votre conception en conséquence pour simplifier le processus de fabrication du moule (et donc son coût).
Pour les volumes plus importants jusqu’à la production à grande échelle (10 000 à 100 000 unités et plus), la contribution des coûts d’outillage au coût global est éclipsée par les coûts des matériaux et de production. Ainsi, vos principaux efforts de conception devraient se concentrer sur la réduction de la partie volumique et du temps du cycle d’injection.
Nous avons rassemblé ici quelques conseils pour vous aider à minimiser le coût de votre projet d’injection plastique.
Conseil n°1 : Utiliser un moule simple, sans tiroir

Les tiroirs et les autres mécanismes dans le moule peuvent augmenter le coût de l’outillage de 15 à 30 %. Cela se traduit par un coût additionnel minimal d’outillage d’environ 1 000 € à 1 500 €.
Dans une section précédente, nous avons examiné les moyens de [traiter les contre-dépouilles] (#dealing-with-undercuts “Traitement des contre-dépouilles en injection plastique”). Pour maintenir votre production dans les limites de votre budget, évitez d’utiliser des tiroirs et d’autres mécanismes à moins que cela ne soit absolument nécessaire.
Conseil n°2: Redessiner la pièce moulée par injection pour éviter les contre-dépouilles
Les contre-dépouilles ajoutent toujours des coûts et de la complexité, ainsi que de l’entretien au moule. Un redesign intelligent peut souvent éliminer les contre-dépouilles.
Conseil n°3: Rendre la pièce moulée par injection plus petite
Les petites pièces peuvent être moulées plus rapidement, ce qui entraîne une production plus élevée, ce qui réduit le coût par pièce. Des pièces plus petites entraînent également une baisse des coûts de matériaux et une baisse du prix du moule.
Astuce #2 : Mettre plusieurs pièces dans un seul moule

Nous avons vu dans une section précédente que le montage de plusieurs pièces dans le même moule est une pratique courante. Habituellement, six à huit petites pièces identiques peuvent tenir dans le même moule, ce qui réduit le temps total de production d’environ 80 %.
Des pièces de géométries différentes peuvent également entrer dans le même moule (n’oubliez pas l’exemple du modèle réduit d’avion). C’est une excellente solution pour réduire le coût global d’un assemblage.
Voici une technique avancée :
Dans certains cas, le corps principal de deux parties d’un assemblage est le même. Avec un design créatif, vous pouvez créer des points d’enclenchements ou des charnières à des endroits symétriques, en créant un miroir de la pièce. De cette façon, le même moule peut être utilisé pour fabriquer les deux moitiés, réduisant ainsi les coûts d’outillage de moitié.
Conseil n°5: Evitez les petits détails
Pour fabriquer un moule avec des petits détails, il faut des temps d’usinage et de finition plus longs. Le texte en est un exemple et pourrait même nécessiter des techniques d’usinage spécialisées telles que l’usinage par décharge électrique (EDM) entraînant des coûts plus élevés.
Conseil n°6: Utilisez des finitions de qualité inférieure:
Les finitions sont généralement appliquées à la main sur le moule, ce qui peut être un processus coûteux, en particulier pour les finitions de haute qualité. Si votre pièce n’est pas destinée à un usage cosmétique, n’appliquez pas une finition coûteuse de haute qualité.
Conseil n°3 : Minimiser le volume de la pièce en réduisant l’épaisseur de la paroi

Réduire l’épaisseur de la paroi de votre pièce est la meilleure façon de minimiser le volume de la pièce. De cette façon, non seulement on utilise moins de matière, mais le cycle d’injection plastique est aussi grandement accéléré.
Par exemple, réduire l’épaisseur de paroi de 3 mm à 2 mm peut réduire le temps de cycle de 50 % à 75 %.
Des parois plus minces permettent de remplir le moule plus rapidement. Plus important encore, les pièces plus minces refroidissent et se solidifient beaucoup plus rapidement. Rappelez-vous que la moitié du cycle d’injection plastique environ est consacrée à la solidification de la pièce, alors que la machine est à l’arrêt.
Il faut veiller à ne pas trop affecter la rigidité de la pièce, et diminuer ses performances mécaniques. Des nervures à des endroits clés peuvent être utilisées pour augmenter la rigidité.
Conseil n°8: Considérez les opérations secondaires
Pour les productions à faible volume (moins de 1000 pièces), il peut être plus rentable d’utiliser une opération secondaire pour compléter vos pièces moulées par injection. Par exemple, vous pouvez percer un trou après le moulage plutôt que d’utiliser un moule coûteux avec des centres à actions latérales.
Part 5
Commencer en injection plastique
Votre conception est prête et optimisée pour l’injection plastique, quelle est la prochaine étape ? Dans cette section, nous vous expliquons les étapes utiles pour commencer la fabrication en injection plastique.
Étape 1 : Commencer par une petite quantité et obtenir un prototype rapidement
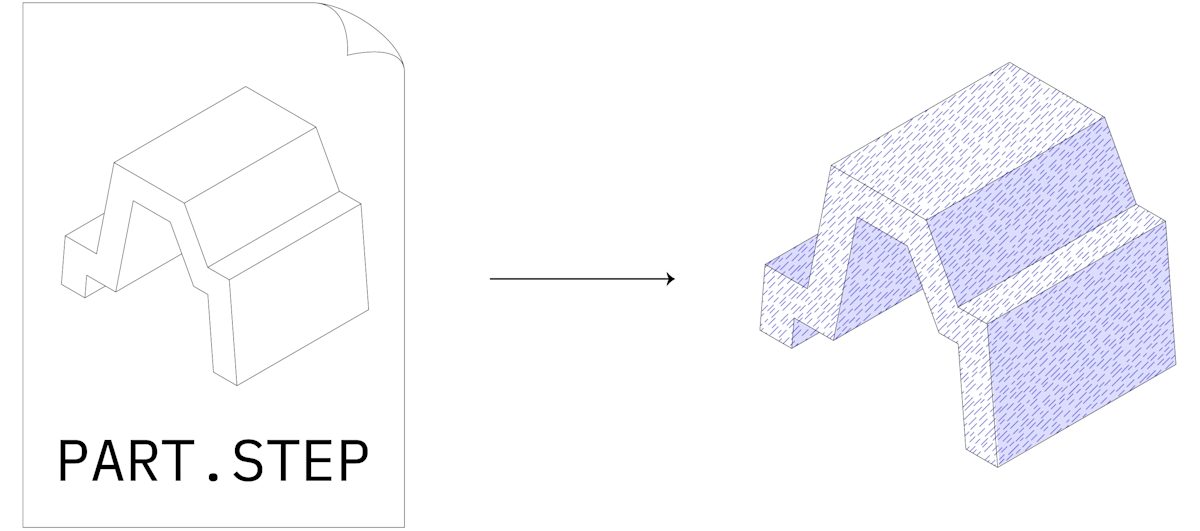
Avant de vous engager dans un outillage d’injection plastique coûteux, commencez par créer et tester un prototype fonctionnel de votre conception.
Cette étape est essentielle pour le lancement réussi d’un produit. De cette façon, les erreurs de conception peuvent être identifiées tôt, pendant que le coût des modifications est encore faible.
Il existe trois solutions pour le prototypage :
- Impression 3D (en SLS, SLA ou dépôt de matière).
- Usinage CNC en plastique.
- Injection plastique en petite série avec moules réalisés en impression 3D.
Ces trois procédés permettent de créer des prototypes réalistes en termes de formes et de fonctions qui ressemblent de près à l’apparence du produit final en injection plastique.
Utilisez les informations ci-dessous comme guide de comparaison rapide pour décider quelle solution convient le mieux à votre application.
Prototypage en impression 3D
__Quantité min. :__1 pièce
__Coût habituel :__20 € - 100 € par pièce
__Délai de fabrication :__2 - 5 jours
En savoir plus sur ce procédé →

Prototypage en usinage CNC
Quantité min. : 1 pièce
Coût habituel : 100 € - 500 € par pièce
Délai de fabrication : 5 - 10 jours
En savoir plus sur ce procédé →

Prototypage en injection plastique à petite série
Quantité min. : 10 - 100 pièces
__Coût habituel :__1 000 € - 4 000 € au total
Délai de fabrication : 5 - 10 jours
En savoir plus sur ce processus →
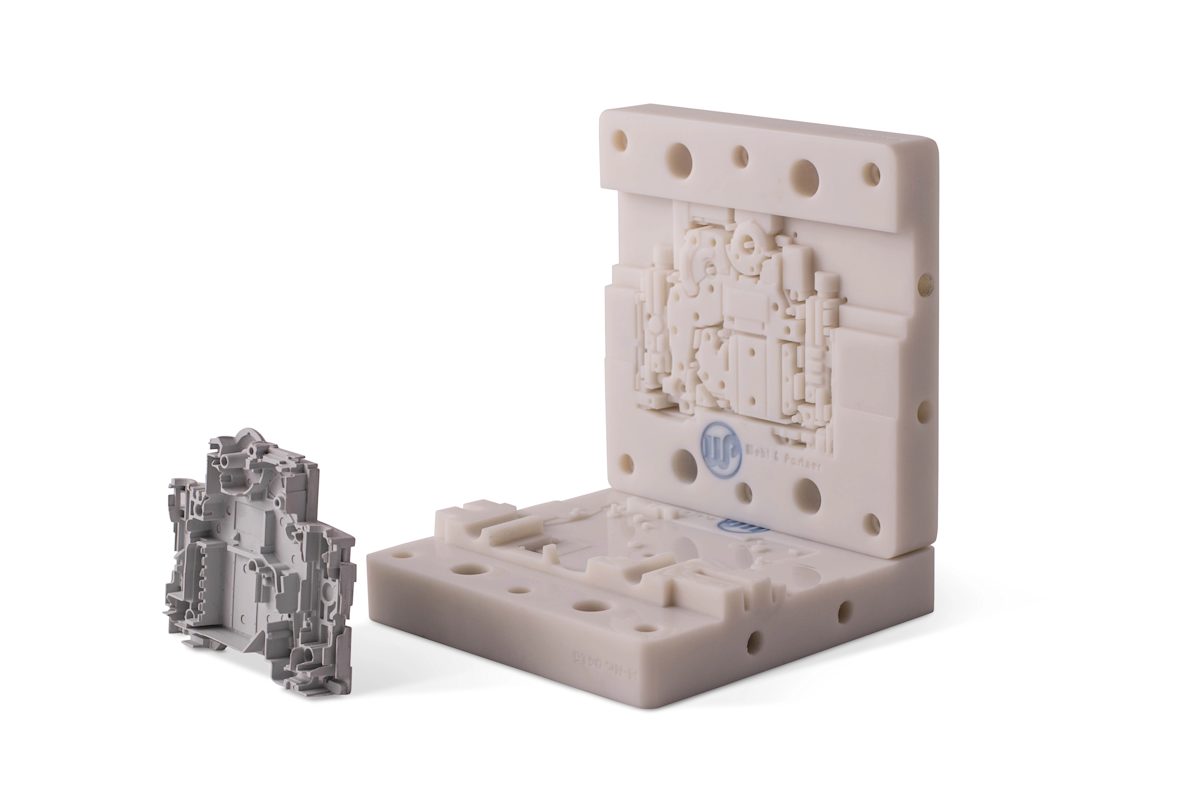
Étape 2 : Réaliser une « présérie » (500 - 10 000 pièces)

Une fois la conception finalisée, il est temps de commencer l’injection plastique avec une petite présérie.
Le volume minimum de commande pour l’injection plastique est de 500 unités. Pour ces quantités, les moules sont généralement usinés sur machine à commande numérique à partir d’aluminium. Les moules en aluminium sont relativement faciles à fabriquer et peu coûteux (de 3 000 € à 5 000 € environ), mais peuvent résister jusqu’à seulement 5 000 à 10 000 cycles d’injection.
À ce stade, le coût classique par pièce varie entre 1 € et 5 €, selon la géométrie de votre pièce et le matériau choisi. Le délai de livraison habituel pour de telles commandes est de 6 à 8 semaines.
Ne vous méprenez pas avec le terme « présérie ». Si vous n’avez besoin que de quelques milliers de pièces, il s’agit de votre dernière étape de production.
Les pièces fabriquées avec des moules « présérie » en aluminium ont des propriétés physiques et une précision identiques à celles des pièces fabriquées avec des moules « grande série » en acier à outils.
Étape 3 : Passer en production en grande série (plus de 100 000 pièces)

Lors de la production de pièces identiques en grandes quantités (de 10 000 à plus de 100 000 unités), un outillage spécial d’injection plastique est nécessaire.
Pour ces volumes, les moules sont usinés sur machine à commande numérique à partir d’acier à outils et peuvent résister à des millions de cycles de moulage par injection. Ils sont également équipés de fonctions avancées pour maximiser les vitesses de production, telles que les seuils à pointe chaude et les canaux de refroidissement complexes.
Le coût unitaire typique à cette étape varie de quelques centimes jusqu’à 1 € et le délai de fabrication habituel est de 4 à 6 mois, en raison de la complexité de la conception et de la fabrication du moule.
Part 6
Ressources utiles
Dans ce guide, nous avons abordé tout ce dont vous avez besoin pour vous familiariser avec l’injection plastique. Mais il reste beaucoup à apprendre.
Ci-dessous, vous trouverez la liste des ressources les plus utiles concernant l’injection plastique et d’autres technologies de fabrication numériques pour les personnes souhaitant approfondir leurs connaissances.
Base de connaissances
Ici, nous avons abordé tout ce dont vous avez besoin pour commencer en injection plastique. Il y a encore beaucoup à apprendre dans notre base de connaissances, une collection d’articles techniques sur toutes les technologies de fabrication, rédigés par des experts de Protolabs Network et de l’industrie manufacturière.
Voici une sélection de nos articles les plus populaires sur l’injection plastique :
Autres guides
Vous voulez en savoir plus sur la fabrication numérique ? Il y a d’autres technologies à explorer :