Which 3D printing method will shape your ideas best? In this article, we’ll break down the key differences between FDM and SLA to help you decide.
What is FDM 3D printing?
Fused Deposition Modeling (FDM) builds parts by melting thermoplastic filament and laying it down layer by layer. This method is simple and cost-effective, making it a favorite for both hobbyists and professionals. FDM is particularly effective for creating functional

prototypes, custom jigs, and durable end-use parts.
Materials used in FDM 3D printing
FDM 3D printing works with a wide range of thermoplastic filaments. Each one has different properties targeted to fulfill specific part requirements. Here’s an overview of some common options:
-
ABS: Tough and impact-resistant.
-
PLA: Biodegradable and easy to print, good for prototypes.
-
PETG: Somewhere in between, combining the ease of PLA with the strength of ABS.
-
Nylon: A durable and flexible choice for functional parts.
-
Carbon-fiber blends: High strength and rigidity for demanding applications.
Learn more about FDM 3D printing materials. Advantages and disadvantages of FDM 3D printing FDM has its own set of strengths, weaknesses and trade-offs to weigh. Here’s a quick look at its pros and cons: Advantages
-
Budget-friendly: Lower material and machine costs make it an economical choice.
-
Quick turnaround: Faster print times, especially for larger parts.
-
Material variety: A wide range of filaments available to meet different needs.
-
Durability: Perfect for functional parts that need to last.
Disadvantages
-
Visible layer lines: Post-processing may be needed for a smooth finish.
-
Precision: Tolerances aren’t as tight as SLA.
-
Post-processing: Support removal and smoothing might add extra steps.
What is SLA 3D printing?
Stereolithography (SLA) uses a laser to cure liquid resin into solid parts. It delivers smooth surface finishes and captures fine details. It’s the go-to process for applications like dental models, jewelry, and intricate prototypes where accuracy really matters.
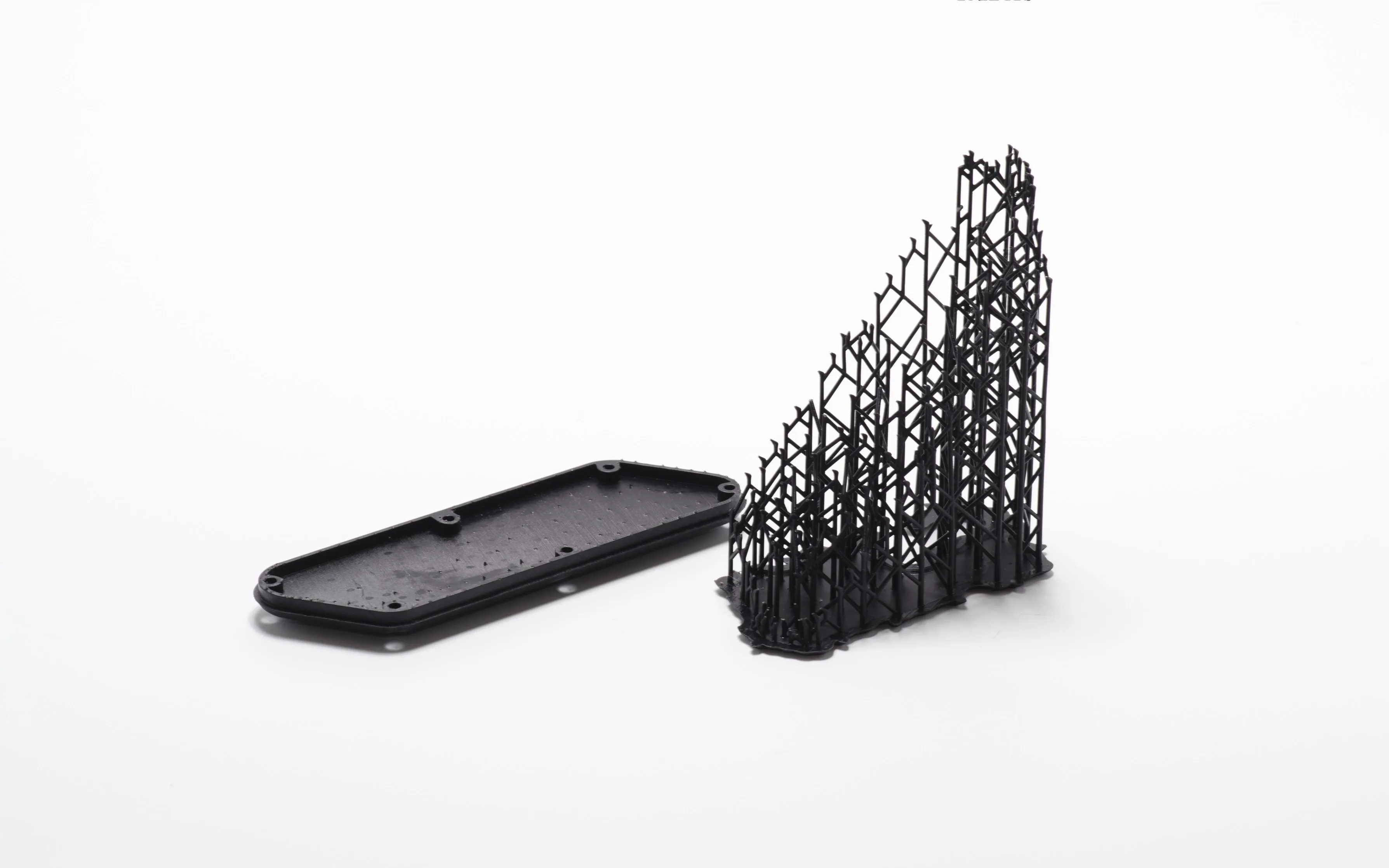
Materials used in SLA 3D printing
SLA printers use photo-reactive resins, which cure into thermoset polymers when exposed to a laser or UV light. These materials offer excellent detail and surface quality, ideal for high-precision applications.
-
Standard resins: Solid all-arounder for mid-level detail and surface finish.
-
Tough resins: Durable and impact-resistant.
-
High-temperature resins: For parts that need to take some heat.
-
Flexible resins: Can bend without breaking.
-
Engineering-grade resins: Specialized options for specific industrial applications.
Learn more about SLA 3D printing materials.
Advantages and disadvantages of SLA 3D printing
SLA stands out for its precision and finish, but no technology is perfect. Here’s what you need to know:
Advantages
-
High precision: Excellent dimensional accuracy and intricate detail.
-
Smooth surfaces: Looks good straight out of the printer.
-
Complex geometries: Capable of producing highly detailed and complex parts.
-
Aesthetic quality: Ideal for presentation models and parts that need a store-ready look.
Disadvantages
-
Cost: Often comes with a steeper price tag due to the higher material and processing costs associated with resin printing.
-
Size: Smaller build volumes could limit the size of individual parts. For jumbo projects, parts may need to be split and assembled post-printing.
-
Post-processing: You may need additional steps like support removal and UV curing to finish up the part, which can impact lead times.
-
Brittleness: Resins can be less impact-resistant than FDM materials.
FDM and SLA compared
Choosing between FDM and SLA depends on your project’s specific needs. Here’s how they stack up across key factors.
Feature | FDM | SLA |
---|---|---|
Typical materials | Thermoplastic filaments like ABS, PLA, PETG, and Nylon | Photo-reactive resins like standard, tough, high-temp, and flexible resins |
Layer thickness | ~0.1 – 0.4 mm | ~0.025 – 0.05 mm |
Build volume | Desktop: ~220 x 220 x 250 mm; Industrial: up to ~1000 x 600 x 900 mm | Desktop: ~145 x 145 x 185 mm; Industrial: up to ~570 x 320 x 650 mm |
Typical tolerances | ±0.2 mm or ±0.5% (whichever is greater) | ±0.15 mm or ±0.3% (whichever is greater) |
Surface finish | Visible layer lines. Smoothing/post-processing often required | Very smooth surface. Minimal post-processing needed |
Strength & durability | Excellent for functional prototypes with tough filaments | Specialized resins (tough, high-temp) improve durability, but standard resins can be brittle |
Speed & cost | Faster for larger volumes, lower material cost | Slower for high-resolution parts, higher resin and post-curing costs |
Applications | Functional prototypes, enclosures, custom jigs, fixtures | High-detail prototypes, aesthetic models, molds for casting |
Making parts with filament versus resin
The decision between when to use resin (SLA) and when to use filament (FDM) in 3D printing boils down to your project requirements. FDM is all about strength and speed, while SLA delivers precision and aesthetics. If FDM is the rugged SUV, built to get the job done, SLA is the sleek sports car, perfect for when appearance and accuracy matter most.
Industrial or desktop use of FDM or SLA
Desktop printers are great for small-scale projects, but industrial-grade systems are built for professionals. These machines handle larger parts, tighter tolerances, and advanced materials:
-
Bigger builds: Industrial FDM and industrial SLA machines manage complex designs in fewer pieces.
-
More precision: Tight tolerances for professional results.
-
Material options: Choose from engineering-grade filaments and high-performance resins.
Learn how industrial SLA compares to desktop SLA.
Frequently asked questions about FDM and SL
Which is better—FDM or SLA?
It depends on your project. FDM is ideal for durable, cost-effective parts, while SLA is better for intricate designs and smooth finishes.
What’s the lead time difference between FDM and SLA?
FDM parts can be ready in as little as one business day, while SLA takes about two days due to post-curing.
Can I combine FDM and SLA in one project?
Yes! Many engineers use FDM for structural components and SLA for detailed, aesthetic parts.
Do I need supports for SLA the same way I do for FDM? Yes, but SLA supports differ in removal and handling. They often require additional cleaning and UV curing to finalize the part.
Where to learn more about 3D printing technologies
Looking to dive deeper? Check out these helpful resources:
Get a quote
Ready to start your next project? Upload your FDM or SLA part now for a free, instant quote.
Frequently asked questions
Which 3D printing method is fastest?
On the Protolabs Network platform, SLS and MJF are efficient for producing many parts simultaneously, but both require a 48-hour heating and cooling cycle. Note that while SLS and MJF are stable in speed, FDM and SLA are advancing rapidly, with faster and more reliable machines being released each year.
At a glance:
-
SLS: Excels in creating complex geometries.
-
MJF: Offers high production speeds with excellent surface quality.
-
FDM: Produces parts quickly, especially simpler prototypes, due to non-100% infill and the ability for multiple machines to operate simultaneously. FDM parts can often come ready off the build plate, reducing post-processing.
Does faster printing mean lower quality?
Not necessarily. With the right design optimizations and material choices, you can achieve high-quality parts without slowing down the process.
How can I reduce lead times further?
Working with a network like Protolabs ensures your project is matched with the right supplier and technology to minimize delays.
Can I print large parts quickly?
Yes, 3D printing can be used for small and large parts with fast lead times but the technology and settings you choose will play a big role. SLS and binder jetting are often preferred for larger volumes.