What is a heat treatment?
In manufacturing, heat treatment refers to the process of heating then cooling a metal in a controlled manner. This allows you to change a part’s physical or mechanical properties, such as hardness, strength, and machinability.
Annealing
Annealing involves heating a metal to heated to a high temperature for a certain amount of time. After that, the metal is cooled slowly, to prevent the formation of new stresses. Annealing results in parts that are:
-
More machinable (easier to cut and shape)
-
More ductile
-
Less prone to warping or cracking
Nearly all metal alloys are annealed, as it allows them to be further modified more easily. Steel sheets and plates are a good example here, as they are often cold worked into various shapes. Annealed metals are also frequently used as parts in industrial machinery, as their ductility and machinability makes them well-suited to high-stress applications.
Normalizing
Normalizing involves heating the metal to a high temperature, then allowing it to slowly cool in room-temperature air. Because the metal cools slowly, its microstructure changes and results in parts with a more uniform and finer grain structure. Normalizing a metal results in parts with:
-
Reduced hardness
-
Increased ductility
-
Higher impact resistance
Normalized metals are used to create structural components like beams or girders for use in construction, axles and shafts in the automotive industry – or any other industrial application that requires a good balance strength, toughness, and ductility.
Quenching
Quenching involves heating metal to a high temperature, then rapidly cooling it in a quenching medium like water or oil. Quenching results in parts that exhibit:
-
High degrees of hardness
-
Improved strength and load-bearing capacity
-
Good wear resistance
Quenched metals are often used to create cutting tools, bearings, and gears.
Stress relieving
Stress relieving involves heating a metal to a relatively low temperature and holding it there. The metal is then cooled slowly to avoid introducing new stresses. Stress relieving creates parts with:
-
Minimal internal stresses
-
Less distortion
-
Improved dimensional stability
As such, stress relieving is used for parts like gear teeth, camshafts, and bearing races, all of which are typically put to use in hard-working applications that require durability and mechanical stability.
Case hardening
Case hardening includes processes like carburizing and nitriding, which are used to harden a metal’s surface but keep the core softer. To achieve this, the metal is heated in a carbon-rich (for carburizing) or nitrogen-rich (for nitriding) environment. The metal is then quenched so its surface hardens. Case hardening results in parts with:
-
Increase surface hardness
-
Improved wear resistance
-
Tough and flexible inner cores
Many gears, shafts, and bearings are case hardened, as they are still somewhat pliable for heavy-duty applications while maintaining good wear resistance.
Through hardening
With through-hardening, an entire part is uniformly heated to a high temperature. It is then rapidly quenched to achieve consistent hardness from surface to core. It’s typically used for steel parts. Through hardening results in parts that have:
-
Increased strength
-
Increased hardness
-
Increased toughness
The process is often used in the automotive and aerospace industries, as well as for parts for industrial equipment, as through-hardened parts withstand harsh conditions and have high wear resistance.
Precipitation hardening
Also known as age hardening, precipitation hardening involves heating the metal to a high temperature, quenching it, then heating it to a lower temperature for a prolonged period of time. Precipitation hardening creates parts with:
-
Increased yield strength
-
Drastically increased hardness
-
Drastically increased strength and durability
Precipitation hardened metals are used in aerospace and marine applications due to their high tensile strength and corrosion resistance. They are also often used in the medical industry for implants, as biocompatible alloys can be precipitation hardened.
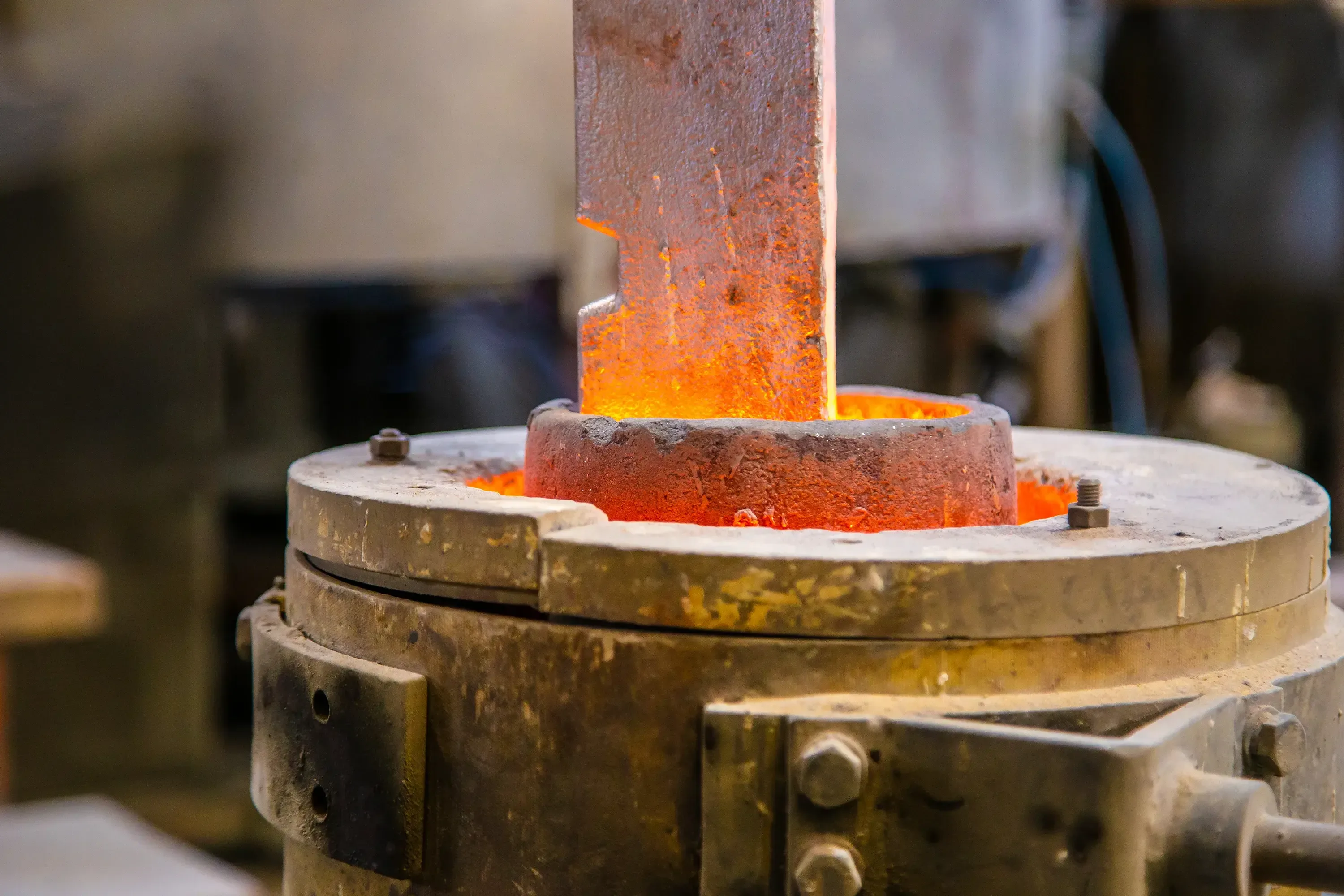
Tempering
Tempering is usually done after quenching to reduce a part’s brittleness. It’s compatible with mild steels (1045, A36) alloy steels (4140, 4240), and tool steels (A2). After it is quenched, the metal reheated and held to a temperature below its critical point, which is usually between 150°C and 700 °C. The benefits of tempering include:
-
Reduced brittleness,
-
Improved toughness and impact resistance
-
Adjustable hardness
Tempered metals are often used in automotive applications and to create parts like springs, where a balance between hardness, toughness, and flexibility is required.
The types of tempering
The temperature at which at metal is tempered will depend on its desired properties. Choosing the right tempering process allows engineers to optimize a part’s hardness without compromising its mechanical properties.
Low-temperature tempering (150-300 °C)
Low-temperature tempering results in parts with high hardness and strength, but with reduced brittleness. Applications of parts that have been low-temperature tempered including cutting tools and bearing surfaces – as both require metals with high hardness and good toughness.
Medium-temperature tempering (300-500 °C)
Medium-temperature tempering strikes a good balance between hardness, strength, and toughness. That’s why it’s used for automotive parts
High-temperature tempering (500-700°C)
High-temperature tempering results in lower hardness but significantly improved toughness and ductility. High-temperature tempered parts are used in structural components and industrial machinery.
Applications and combinations of heat treatments and tempers
When designing a part, you’ll need to consider both the type of heat treatment and temper it will receive. The combination of these two processes will be hugely influential on the part’s final properties. In this section, we’ll explore several commonly heat-treated and tempered applications, then offer tips on how you can combine them for the best results.
Tools and dies
Because they must exhibit high degrees of hardness while achieving reduced levels of brittleness for durability, we recommend quenching following by low-temperature tempering for tools and dies.
Automotive components
Automotive components require a balance of toughness, hardness, and ductility. As such, they’re often normalized, quenched, then tempered at medium temperatures.
Aerospace components
Precipitation hardening is often used for aerospace components, especially those made of aluminum alloys. However, for steel aerospace components, high-temperature tempering can be applied to enhance toughness and ductility.
Structural parts
Normalizing helps relieve stresses in structural parts, as well as refine their grain structure. Following this with high-temperature tempering results in parts with maximum toughness and ductility.
Shafts
Case hardening is commonly used for shafts to achieve high surface hardness. Afterwards, medium-temperature tempering is applied to relieve internal stresses and enhance the part’s core toughness. This helps reduce brittleness and ensure the shaft can withstand bending and torsional loads.
Bearings
Bearings are often through hardened to achieve uniform hardness. After that, they can be low-temperature tempered to reduce internal stresses and improve ductility – ultimately reducing brittleness and preventing cracking.
Axles
We recommend heating axles to a high temperature, then quenching them to achieve high surface hardness and strength. Medium-temperature tempering is then utilized to reduce brittleness while maintaining the required hardness for load-bearing capacity.
Order custom parts using heat treated materials
We can source a wide variety of heat-treated materials and tempers on request. Contact networksales@protolabs.com to discuss your project’s requirements with our experts.