How do you design parts for injection molding?
How do you optimize part design for injection molding? This complete guide to designing for injection molding provides basic and advanced design tips, including guidelines for creating snap-fits, living hinges and undercuts, and accounting for optimial surface finishes.
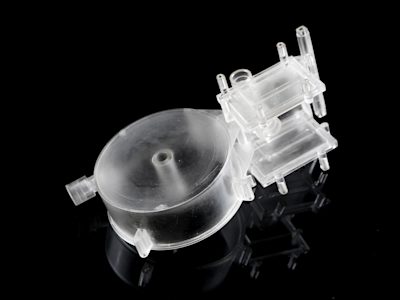
Introduction
Injection molding is the most popular manufacturing technology for the mass-production of plastic parts: almost every plastic part around you was manufactured using Injection Molding.
There are several factors that may affect the quality of the final product and the repeatability of the process. To yield the full benefits of the process, the designer must follow certain design guidelines.
In this article, we outlined basic and advanced guidelines that you should follow when designing parts for Injection Molding, including recommendation for keeping the cost of Injection Molding to a minimum.
The Injection Molding process
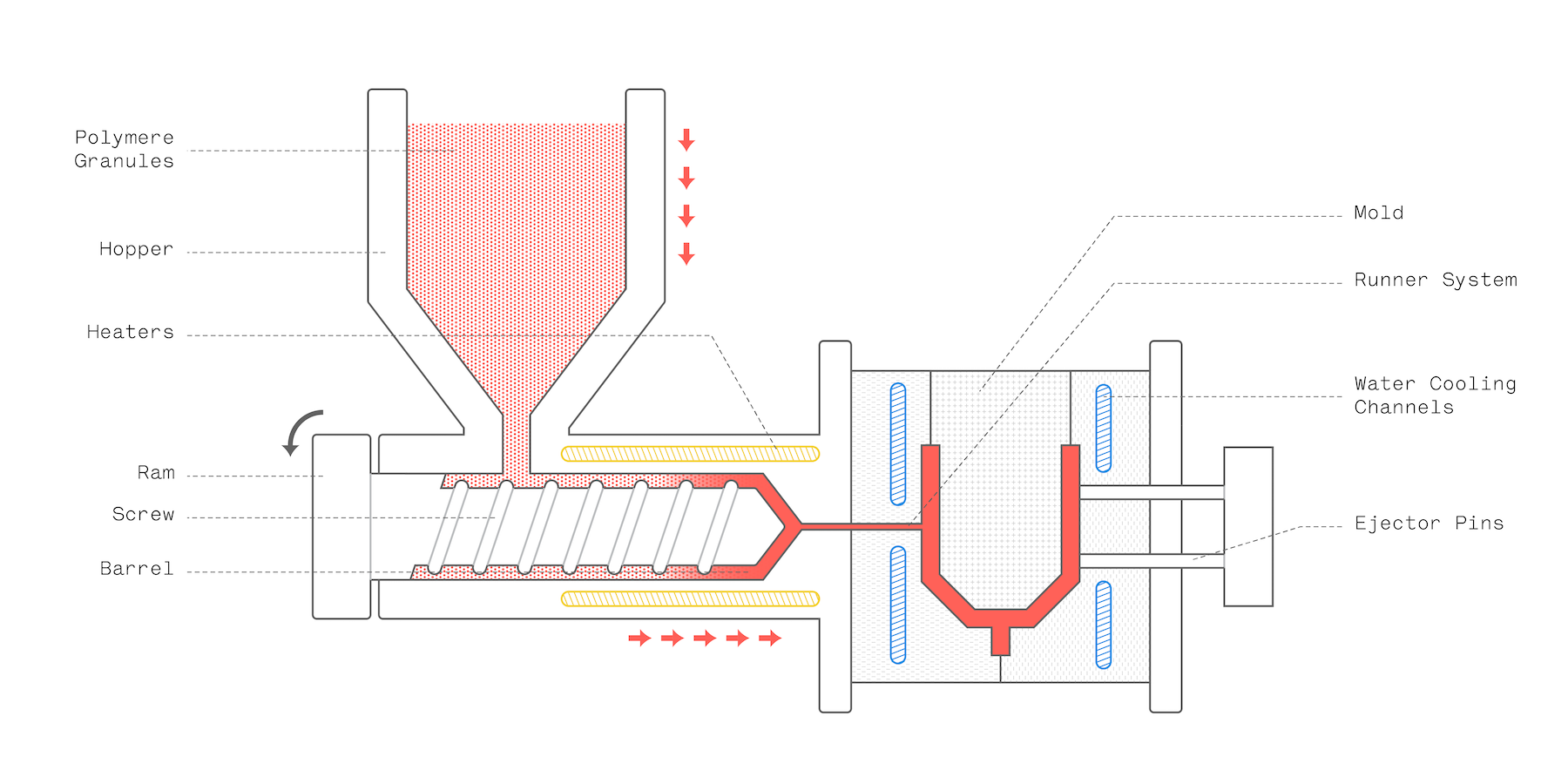
Injection Molding is a manufacturing technology that can be used to mass-produce identical plastic parts. In Injection Molding, polymer granules are first melted and then injected under pressure into a mold, where the liquid plastic cools and solidifies. The materials used in Injection Molding are thermoplastic polymers that can be colored or filled with other additives.
Injection Molding is so popular, because of the especially low cost per unit when manufacturing high volumes. Injection molding also offers high repeatability, good design flexibility and produces parts with good tolerances.
The main limitation of Injection Molding is its very high initial start-up cost. This is mainly connected to the design and manufacture of the mold: a mold can cost from $3.000 upwards to $100.000+ dollars, depending on the size and complexity of the part. In a later section, we will see how you can reduce this cost when you are designing on a budget.
An introduction to the basic mechanics, characteristics and key benefits and limitations of Injection Molding can be found in this article.
Do you need 1000+ plastic parts for your project?
Design rules for Injection Molding
One of the biggest benefits of Injection Molding is the ease with which the parts with complex geometries can be formed, allowing a single part to serve multiple functions.
Once the mold is manufactured, these complex parts can be reproduced at a very low cost. Changes to the mold design at later stages of development can be very expensive though, so achieving the best results on the first time is essential. Follow the guidelines below to avoid the most common defects in Injection Molding.
Use uniform wall thickness
Use a uniform wall thickness throughout the part (if possible) and avoid thick sections. This is essential as non-uniform walls can lead to warping or the part as the melted material cools down.
If sections of different thickness are required, make the transition as smooth as possible using a chamfer or fillet. This way the material will flow more evenly inside the cavity, ensuring that the whole mold will be fully filled.
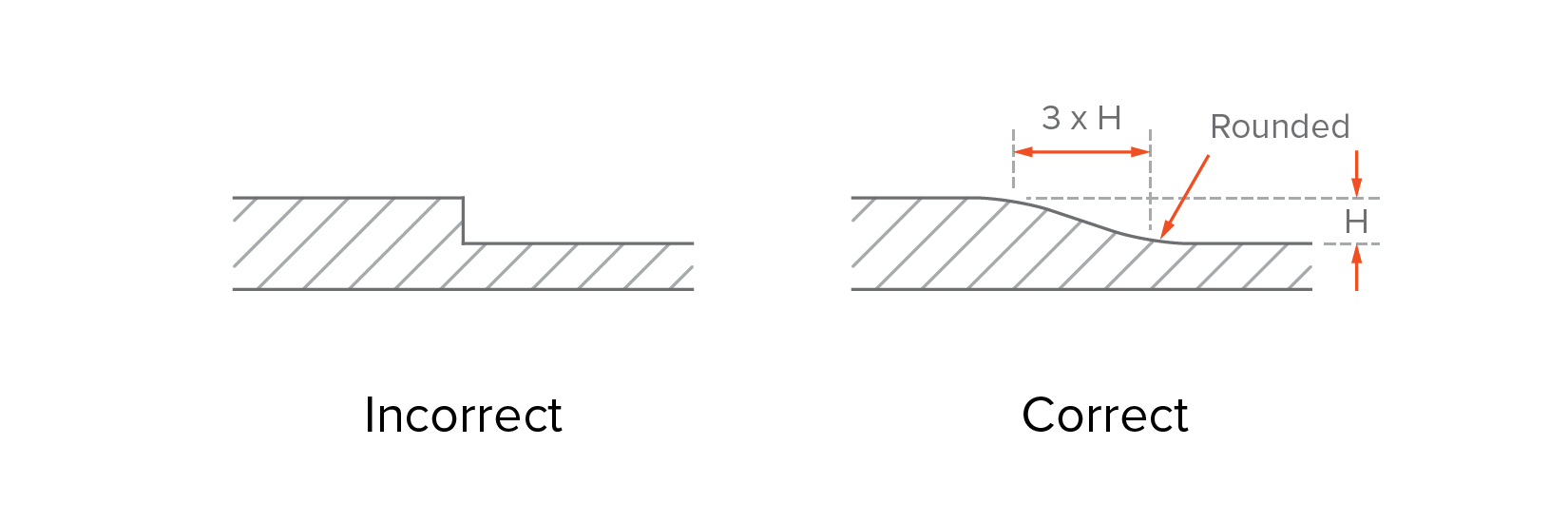
A wall thickness between 1.2 mm and 3 mm is a safe value for most materials. The next table summarises specific recommended wall thicknesses for some of the most common Injection Molding materials:
Material | Recommended wall thickness [mm] | Recommended wall thickness [inches] |
---|---|---|
Polypropylene (PP) | 0.8 - 3.8 mm | 0.03'' - 0.15'' |
ABS | 1.2 - 3.5 mm | 0.045'' - 0.14'' |
Polyethylene (PE) | 0.8 - 3.0 mm | 0.03'' - 0.12'' |
Polystyrene (PS) | 1.0 - 4.0 mm | 0.04'' - 0.155'' |
Polyurethane (PUR) | 2.0 - 20.0 mm | 0.08'' - 0.785'' |
Nylon (PA 6) | 0.8 - 3.0 mm | 0.03'' - 0.12'' |
Polycarbonate (PC) | 1.0 - 4.0 mm | 0.04'' - 0.16'' |
PC/ABS | 1.2 - 3.5 mm | 0.045'' - 0.14'' |
POM (Delrin) | 0.8 - 3.0 mm | 0.03'' - 0.12'' |
PEEK | 1.0 - 3.0 mm | 0.04'' - 0.12'' |
Silicone | 1.0 - 10.0 mm | 0.04'' - 0.40'' |
For best results:
Round all edges
The uniform wall thickness limitation also applies to edges and corners: the transition must be as smooth as possible to ensure good material flow.
For interior edges, use a radius of at least 0.5 x the wall thickness. For exterior edges, add a radius equal to the interior radius plus the wall thickness. This way you ensure that the thickness of the walls is constant everywhere (even at the corners).
Adding to this, sharp corners result in stress concentrations which can result in weaker parts.
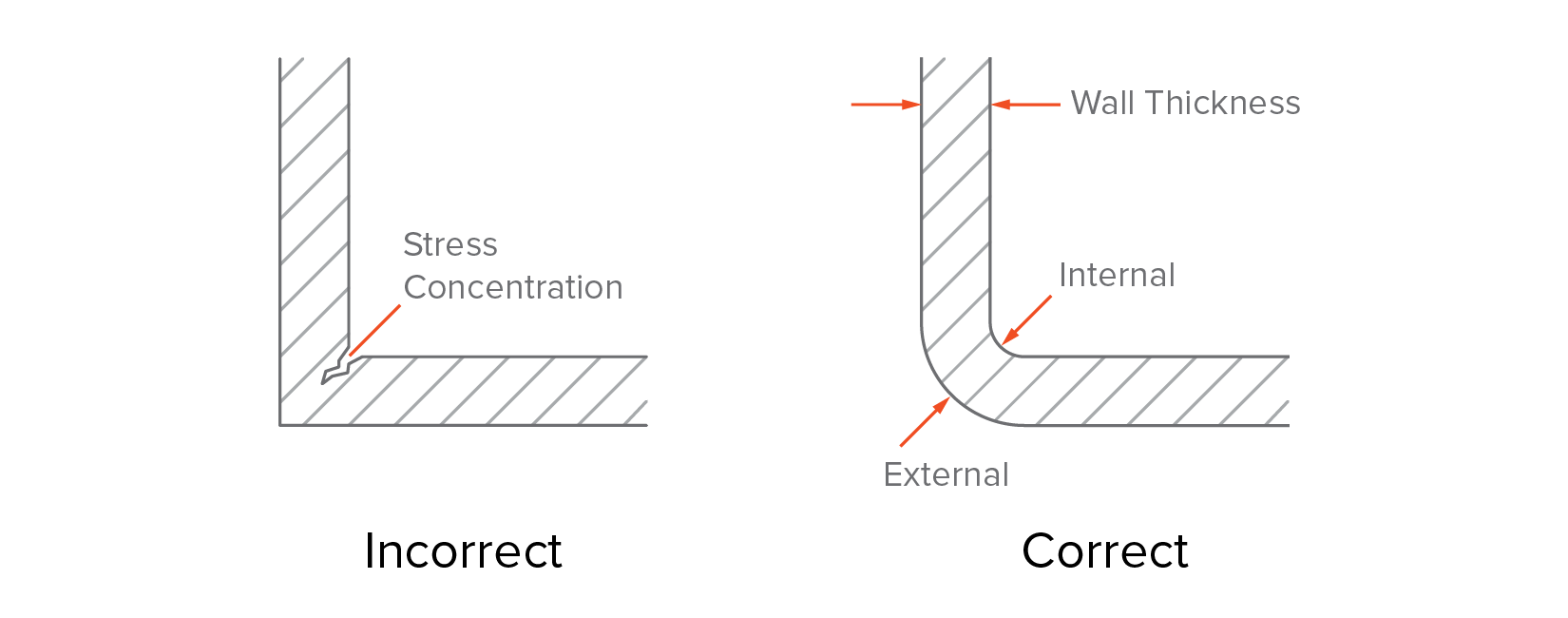
For best results:
Hollow out thick sections
Thick sections can lead to various defects, including warping and sinking. Limiting the maximum thickness of any section of your design to the recommended values by making them hollow is essential.
To improve the strength of hollow section, use ribs to design structures of equal strength and stiffness but reduced wall thickness. A well-designed part with hollow sections is shown below:
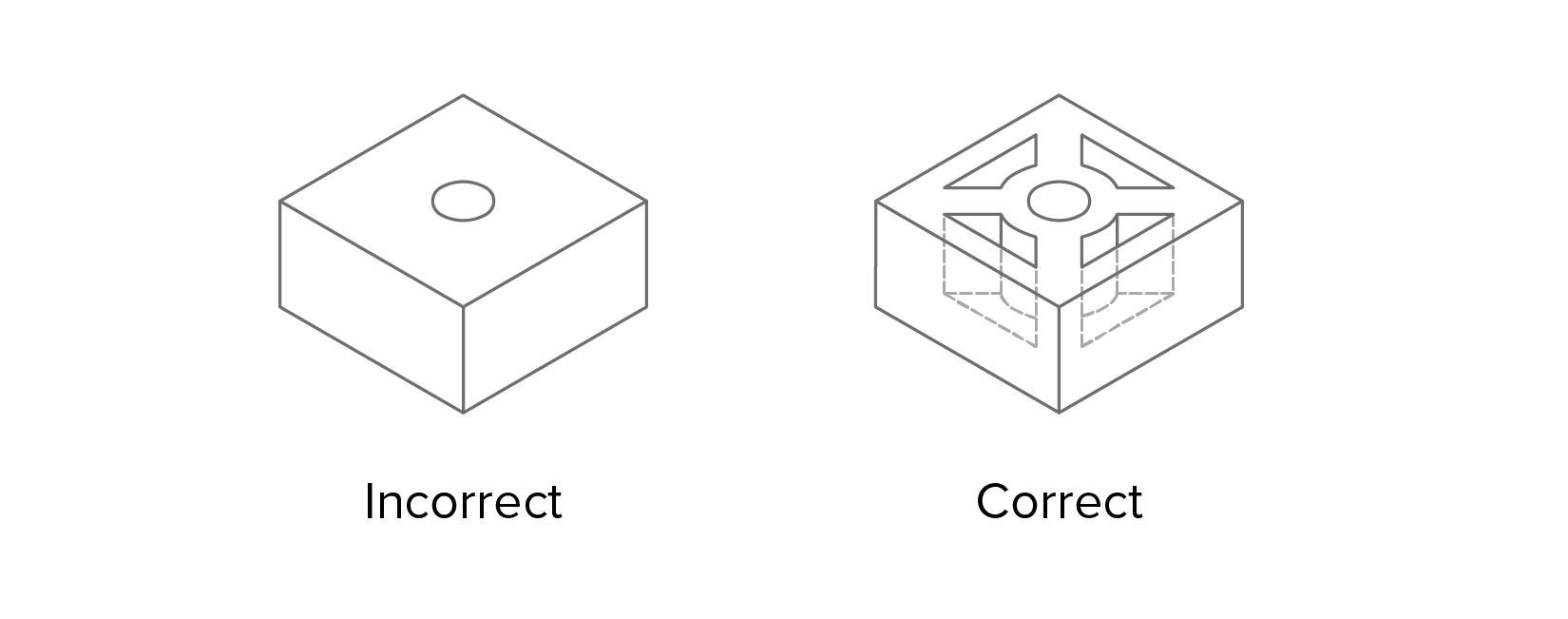
Ribs can also be used to improve the stiffness of horizontal sections without increasing their thickness. Remember though that the wall thickness limitations still apply. Exceeding the recommended rib thickness (see below) can result in sink marks.
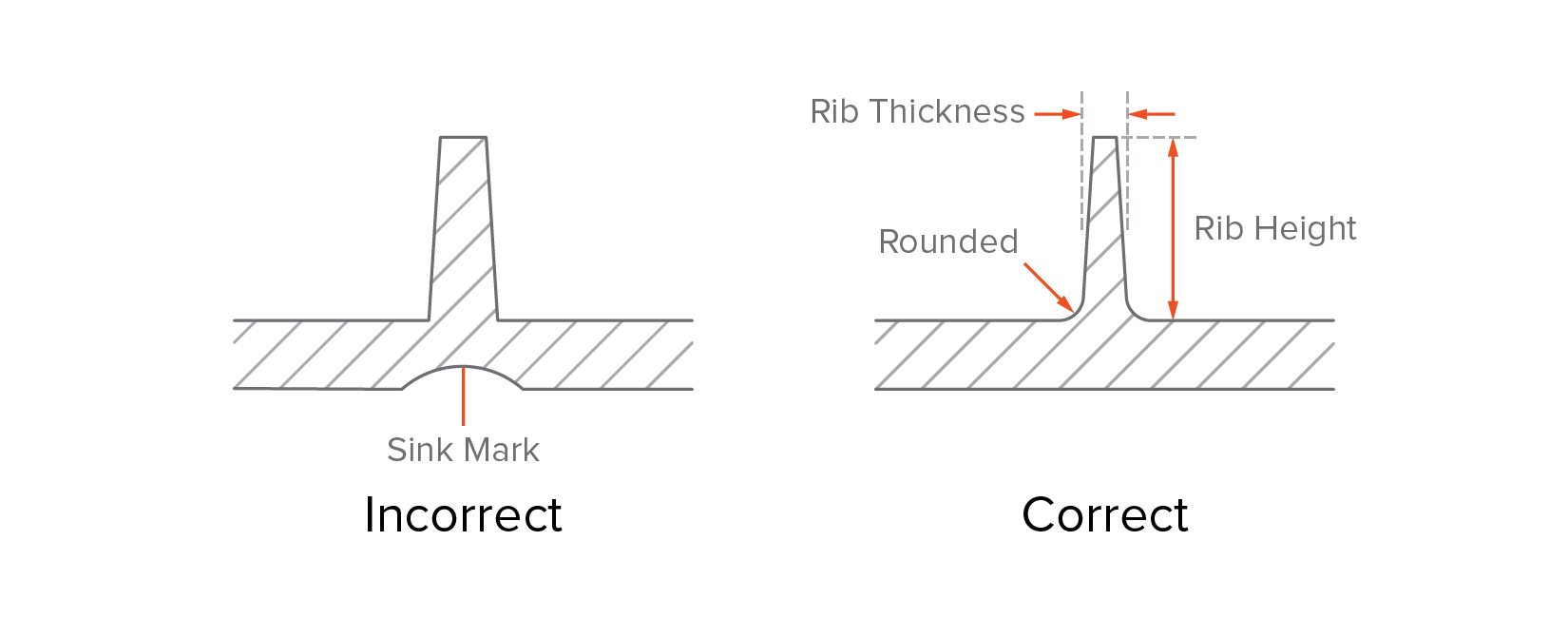
For best results:
Add a draft angle
To make the ejection of the part from the mold easier, a draft angle must be added to all vertical walls. Walls without a draft angle will have drag marks on their surface, due to the high friction with the mold during ejection.
A minimum draft angle of 2o degrees is recommended. Larger draft angles (up to 5o degrees) should be used on taller features.
A good rule of thumb is to increase the draft angle by one degree for every 25 mm. For example, add a draft angle of 3o degrees to a feature that is 75 mm tall. Larger draft angle should be used if the part has a textured surface finish. As a rule of thumb, add 1o to 2o extra degrees to the results of the above calculations.
Remember that draft angles are also necessary for ribs. Be aware though that adding an angle will reduce the thickness of the top of the rib, so make sure that your design complies with the recommended minimum wall thickness.
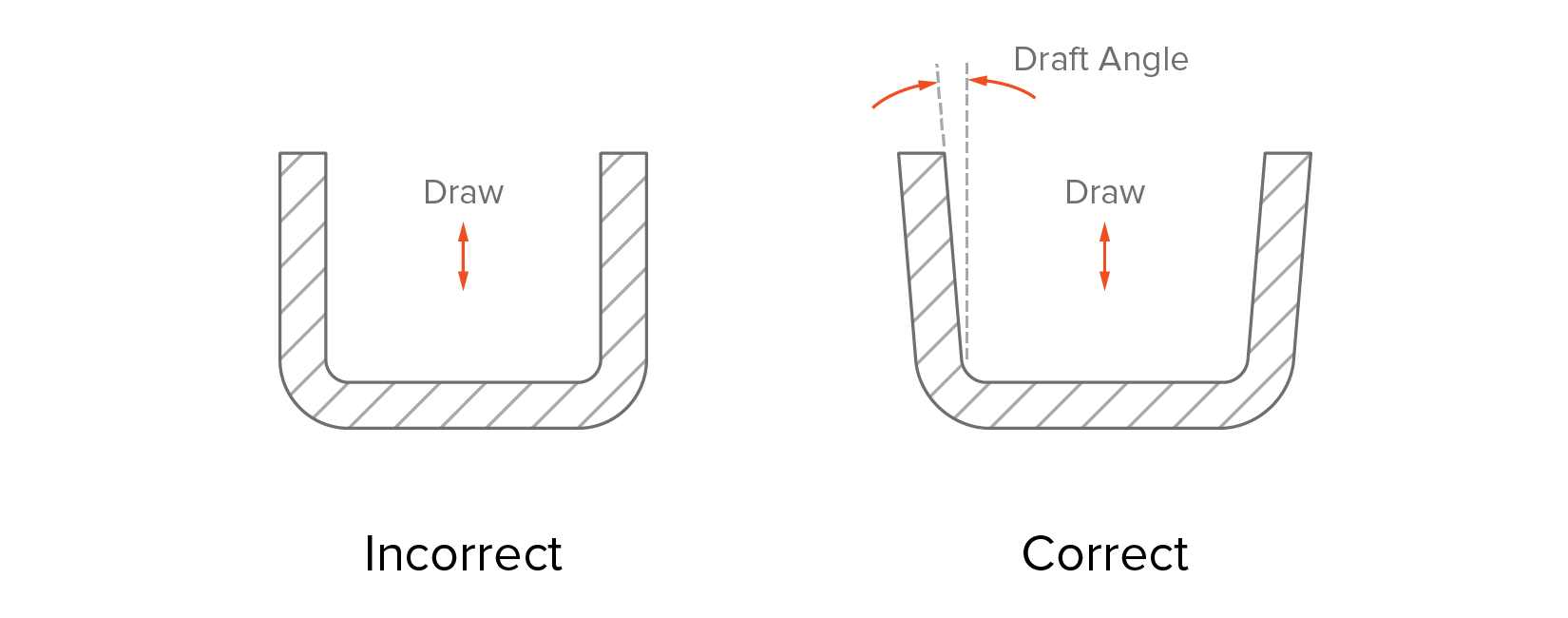
Add a draft angle (minimum 2o)to all vertical walls
For best results:
Need advice on your Injection Molding project?
Common design features
Threaded fasteners (bosses and inserts)
There are three ways to add fasteners to an injection molded part: by designing a thread directly on the part, by adding a boss where the screw can be attached, or by including a threaded insert.
Modelling a thread directly on the part is possible, but not recommended, as the teeth of the thread are essentially undercuts, increasing drastically the complexity and cost of the mold (we will more about undercuts in a later section). An example of an injection molded part with a thread are bottle caps.
Bosses are very common in Injection Molded parts and are used as points for attachment or assembly. They consist of cylindrical projections with holes designed to receive screws, threaded inserts, or other types of fastening and assembly hardware. A good way to think of a boss is as a rib that closes on itself in a circle.
When bosses are used as points of fastening, the outer diameter of the boss should be 2x the nominal diameter of the screw or insert and its inner diameter equal to the diameter of the core of the screw. The hole of the boss should extend to the base-wall level, even if the full depth is not needed for assembly, to maintain a uniform wall thickness throughout the feature. Add a chamfer for easy insertion of the screw or insert.
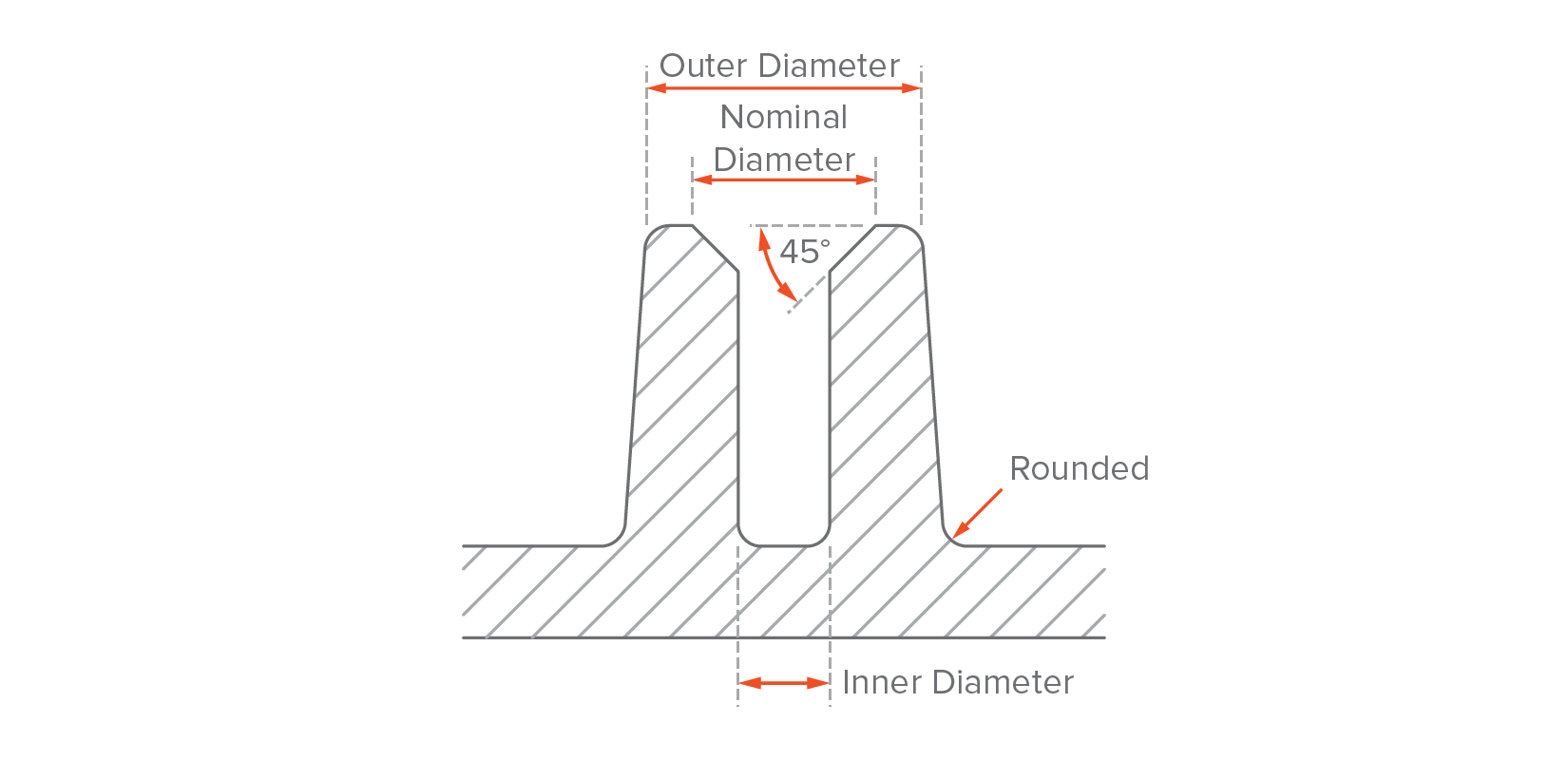
Metal threaded inserts can be added to plastic Injection Molded parts to provide a durable threaded hole for fasteners such as machine screws. The advantage of using inserts is that they allow many cycles of assembly and disassembly.
Inserts are installed in Injection Molded parts through thermal, ultrasonic or in-mold insertion. To design a boss that will receive a threaded insert, use similar guidelines as above, using the diameter of the insert as the guiding dimension.
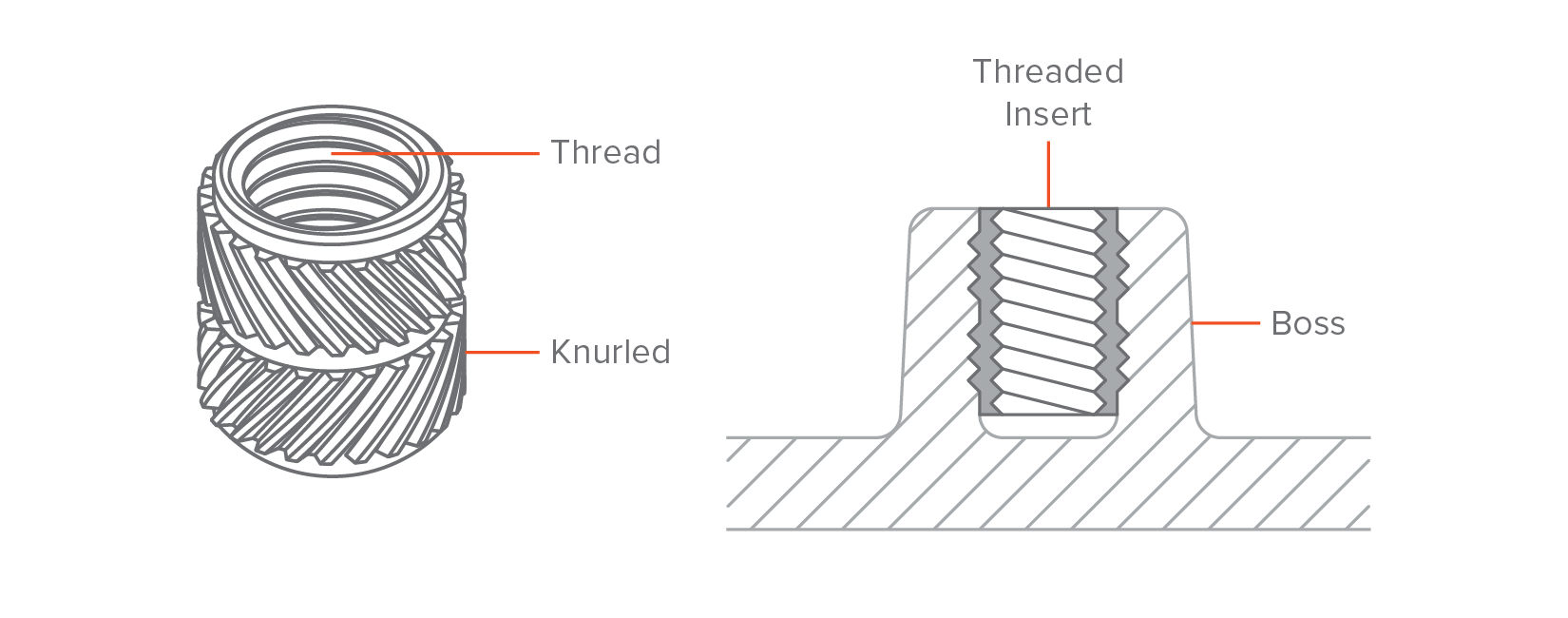
For best results:
Adding text
Text is a very common feature that can be useful for logos, labels, warnings, diagrams, and instructions, saving the expense of stick-on or painted labels.
Prefer to embossed text over engraved text, as it easier to CNC machine on the mold and thus more economical.
Raising the text 0.5 mm above the part surface will ensure that the letters are easy to read. It is advised to choose a bold, rounded font style with uniform line thickness, with a size of 20 points or larger. Some font examples include: Century Gothic Bold, Arial and Verdana.
For best results:
Snap-fit joints
Snap-fit joints are a very simple, economical and rapid way of joining two parts without fasteners or tools. A wide range of design possibilities exists for snap-fit joints.
In the example below, the most common snap-fit joint design (known as the cantilever snap-fit joint) is shown. As with ribs, add a draft angle to your snap-fit joints and use a minimum thickness of 0.5x the wall thickness.
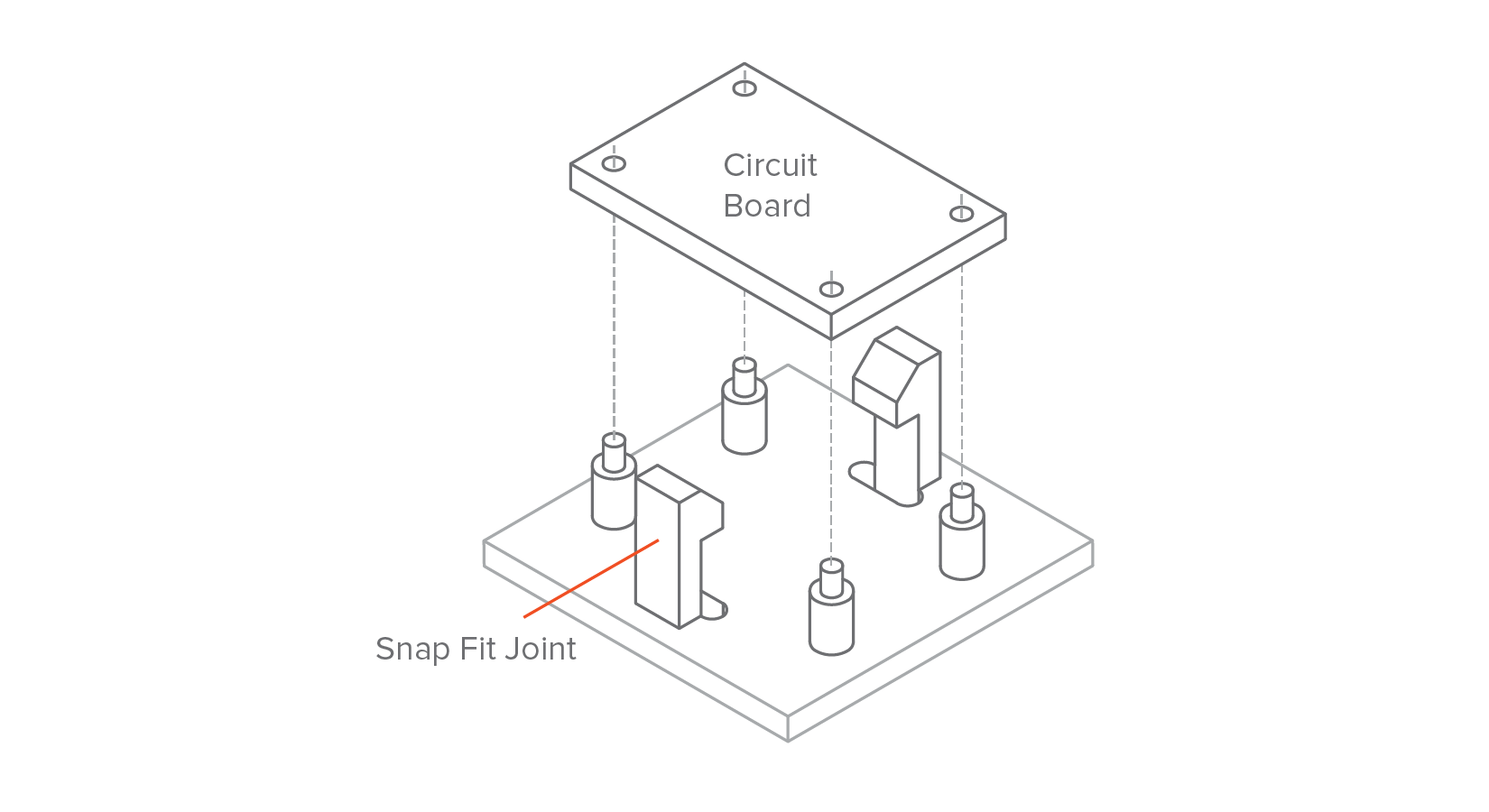
As a rule of thumb, the deflection of a snap-fit joint mainly depends on its length and the permissible force that can be applied on it on its width (since its thickness is more or less defined by the wall thickness of the part). Also, snap-fit joints is another example of undercuts (as we will see below).
Specific guidelines on designing snap-fit joints is a big subject that goes beyond the scope of this article. For more detailed information, please refer to this article from MIT.
For best results:
Crush Ribs
Crush Ribs are small protruding features that deform to create friction when different components are pushed together, securing their possition.
Crush ribs can be an economical alternative for manufacturing high tolerance holes for tight fits. They are commonly used to house bearings or shafts and other press fit applications.
An example of a part with crush ribs is shown below. Using three crush ribs is recommended to ensure good alignment. The recommended height/radius for each rib is 2 mm. Add a minimum interference of 0.25 mm between the crush rib and the fitted part. Because of the small surface contact with the mold, crush ribs can be designed without a draft angle.
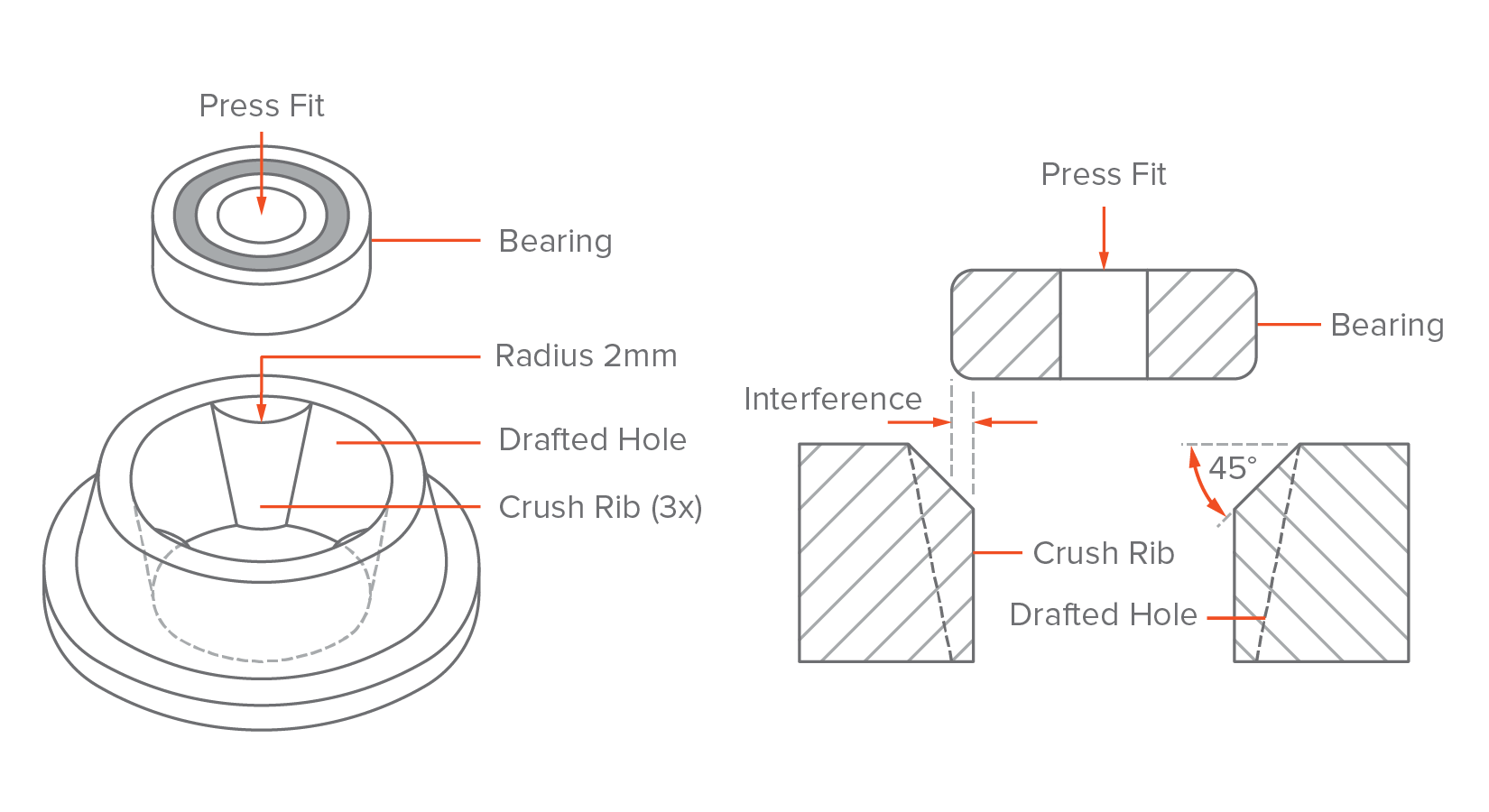
For best results:
Living Hinges
Living hinges are thin sections of plastic that connect two segments of a part and allow it to flex and bend. Typically these hinges are incorporated in mass-produced containers, such as plastic bottles. A well-designed living hinge can last for up to a million cycles without failure.
The material used to Injection Mold a living hinge must be flexible. Polypropylene (PP) and Polyethylene (PE) are good choices for consumer application and Nylon (PA) for engineering uses.
A well-designed hinge is shown below. The recommended minimum thickness of the hinge ranges between 0.20 and 0.35 mm, with higher thicknesses resulting in more durable, but stiffer, parts.
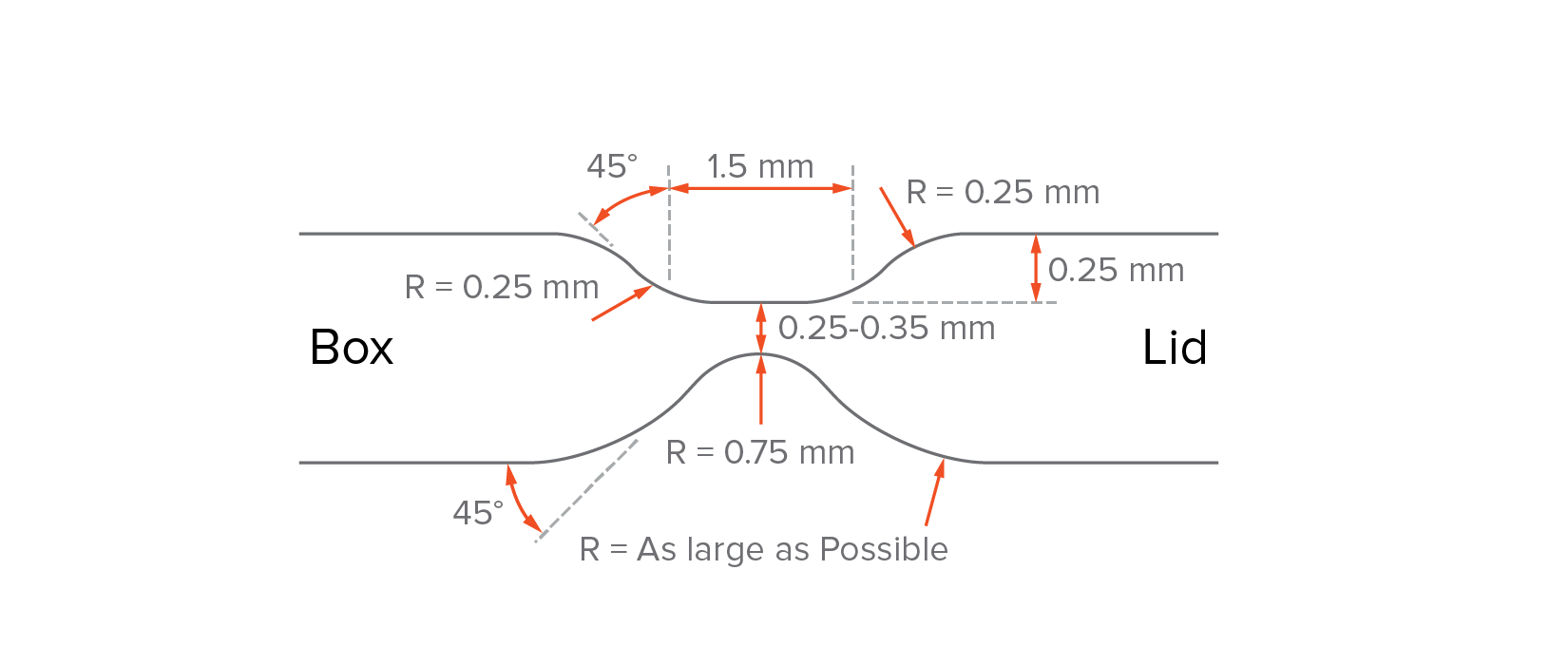
For more detailed information on the design of living hinges please refer here and here. Here are some useful design tips:
- Before going to full-scale production, prototype your living hinges using CNC machining or 3D printing to determine the geometry and stiffness that best fits your application.
- Add generous fillets and design shoulders with a uniform wall thickness as the main body of the part to improve the material flow in the mold and minimize the stresses.
- Divide hinges longer than 150 mm in two (or more) to improve lifetime.
For best results:
Dealing with undercuts
The simplest mold (the straight-pull mold) consist of two halves. Features with undercuts (such as the teeth of a thread or the hook of a snap-fit joint) may not be manufacturable with a straight-pull mold though. This is either because the mold cannot be CNC machined or because the material is in the way of ejecting the part.
Here some ideas to help you deal with undercuts:
Avoid undercuts using shutoffs
Avoiding undercuts altogether might be the best option. Undercuts always add cost, complexity, and maintenance requirements to the mold. A clever redesign can often eliminate undercuts.
Below are some examples of how Injection Molded parts can be redesigned to avoid undercuts: essentially, material is removed in the area under the undercut, eliminating the issue altogether.
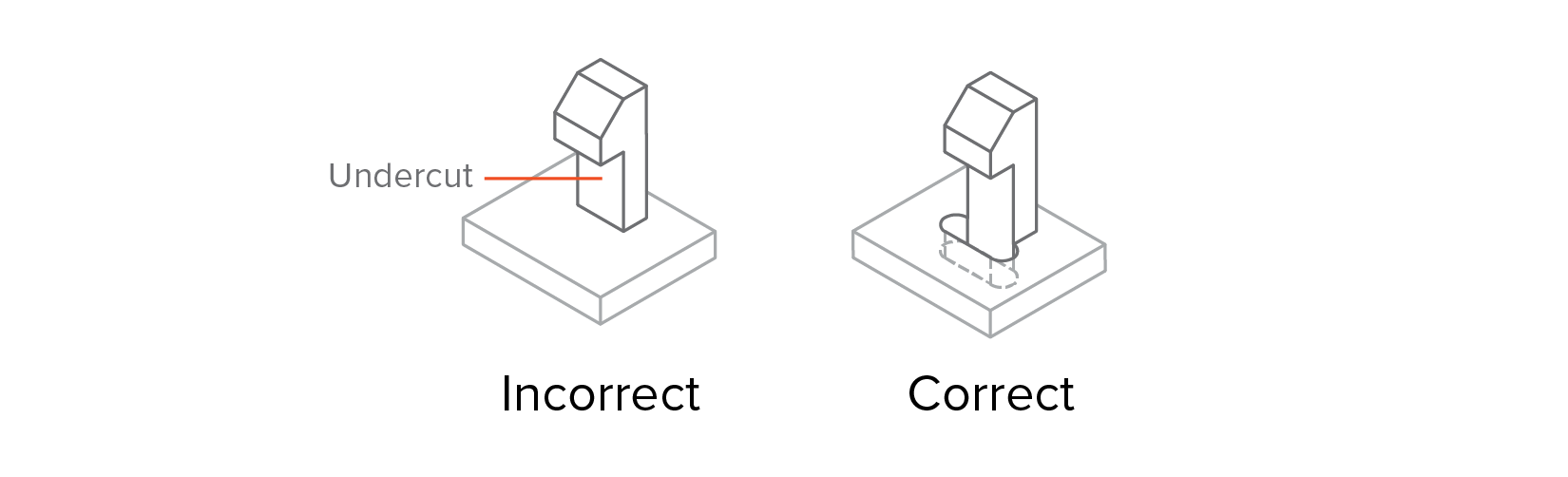
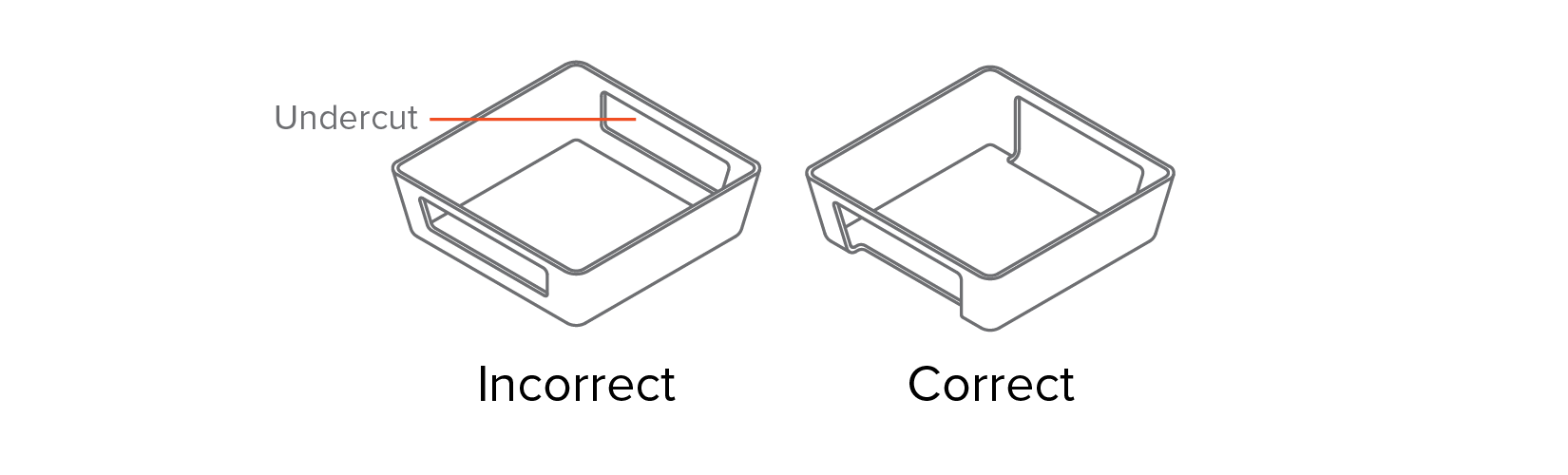
Use a stripping undercut (bumpoffs)
Stripping undercuts (also known as bumpoffs) can be used when the feature is flexible enough to deform over the mold during ejection. Stripping undercuts are used to manufacture the threads in bottlecaps.
Undercuts can only be used under the following conditions:
- The stripping undercut must be located away from stiffening features, such as corners and ribs.
- The undercut must have a lead angle of 30o to 45o degrees.
- The Injection Molded part must have space and must be flexible enought to expand and deform.
It is recommended to avoid stripping undercuts in parts made from fiber reinforced plastics. Typically, flexible plastics such as PP, HDPE or Nylon (PA) can tolerate undercuts of up to 5% of their diameter.
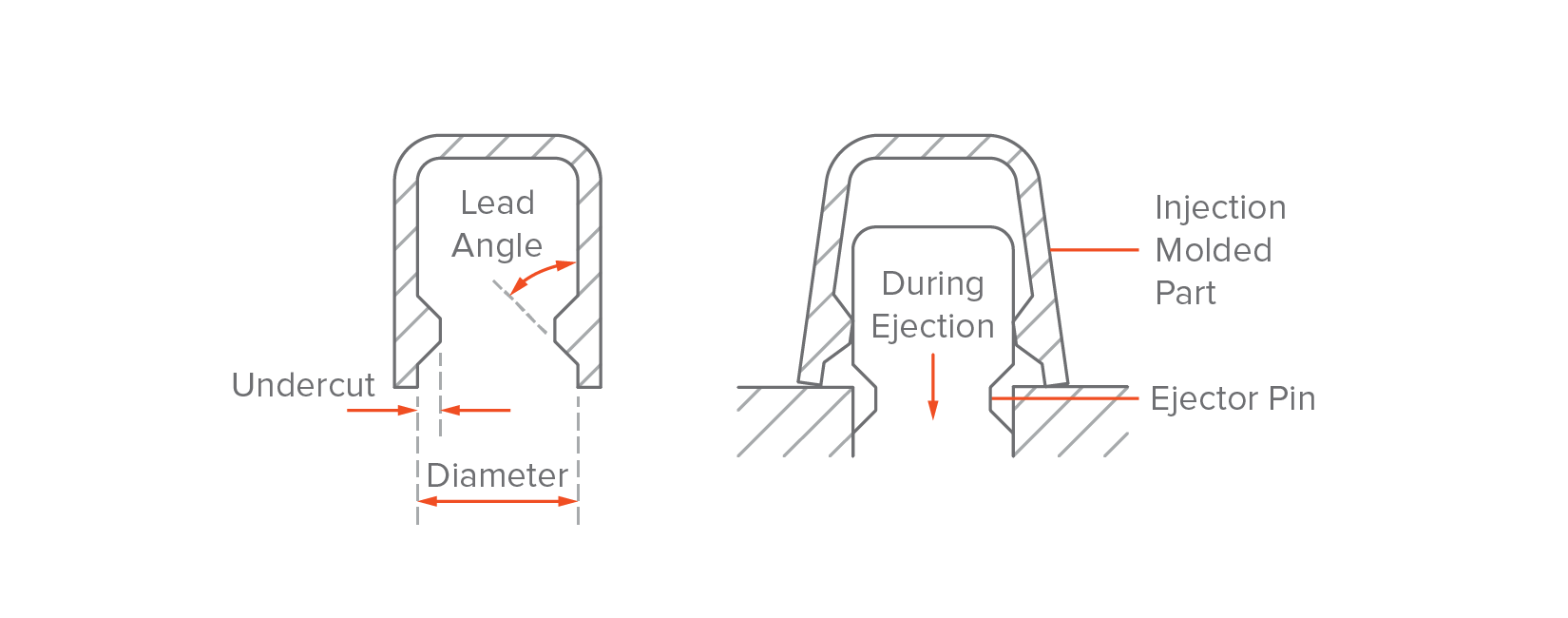
Example part with stripping undercuts. The part is deformed as it is pushed out of the mold
Sliding Side-actions and cores
Sliding side-actions and cores are used when it is not possible to redesign the Injection Molded part to avoid undercuts, due to esthetical or technical reasons.
Side-action cores are inserts that slide in as the mold closes and slide out before it opens. Keep in mind that these mechanisms add cost and complexity to the mold.
Here are some requirements that features designed for side actions must meet:
- There needs to be space for the core to move in and out. This means that the feature must be on the other side of the part.
- The side-actions must move perpendicularly. Moving at an angle other than 90o is more complicated, increasing cost and lead times.
- Do not forget to add draft angles to your design as usual, taking in consideration the movement of the side action core.
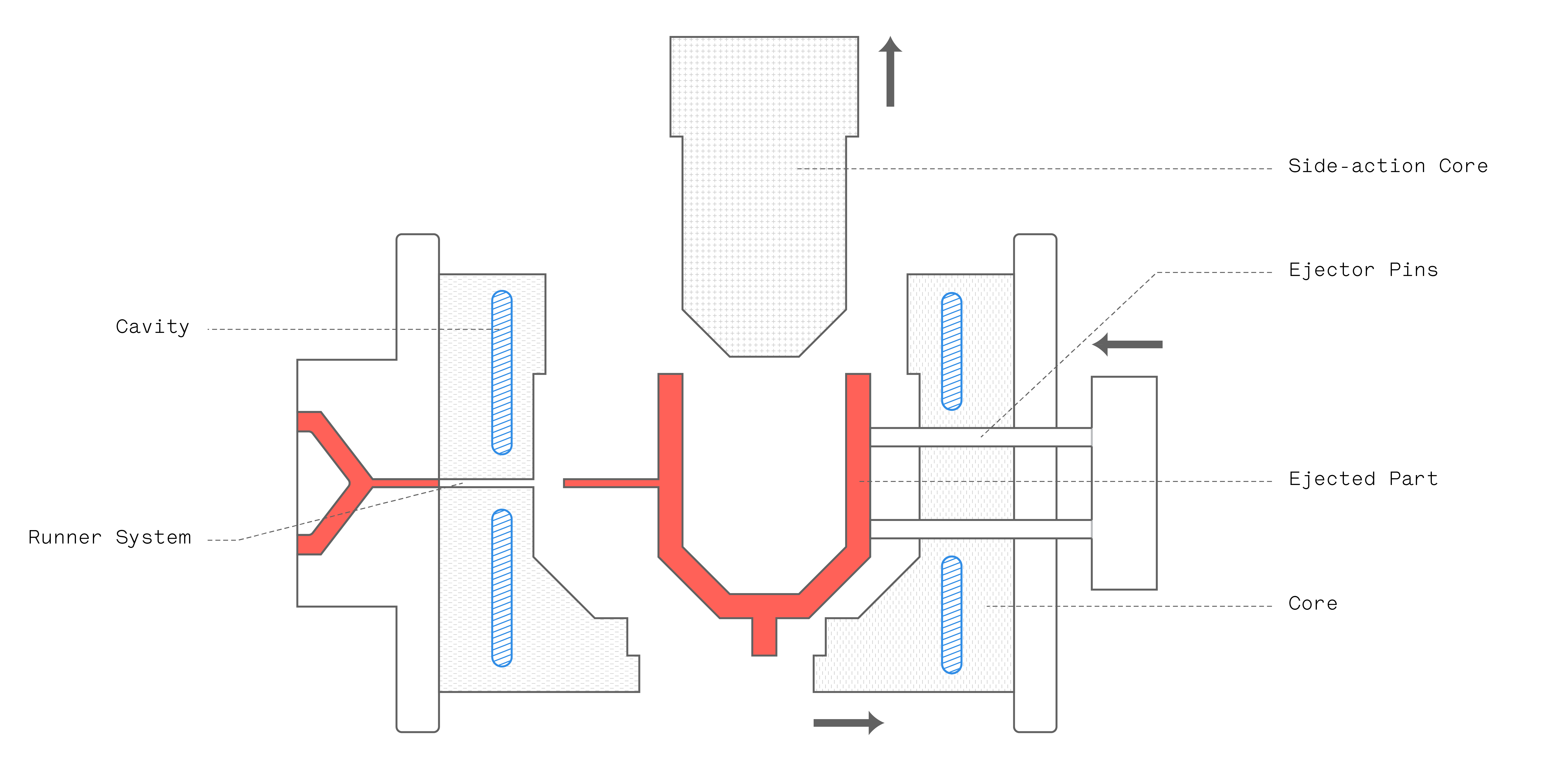
Need advice on your Injection Molding project?
Surface finish
Surface finishes can be used to give an injection molded part a certain look or feel. Besides cosmetic purposes surface finishes can also serve technical needs. For example, the average surface roughness (Ra) can dramatically influence the lifetime of sliding parts such as plain bearings.
Keep in mind that rough surfaces increase the friction between the part and the mold during ejection, therefore a larger draft angle is required.
Finish | Description | SPI standards* | Applications |
---|---|---|---|
Glossy finish | The mold is first smoothed and then polished with a diamond buff, resulting in a mirror-like finish. |
A-1 A-2 A-3 |
Suitable for parts that require the smoothest surface finish for cosmetic or functional purposes (Ra less than 0.10 μm). The A-1 finish is suitable for parts with mirror-like finish and lenses. |
Semi-gloss finish | The mold is smoothed with fine grit sandpaper, resulting in a fine surface finish. |
B-1 B-2 B-3 |
Suitable for parts that require a good visual appearance, but not a high glossy look. |
Matte finish | The mold is smoothed using fine stone powder, removing all machining marks. |
C-1 C-2 C-3 |
Suitable for parts with low visual appearance requirments, but machining mark are not acceptable. |
Textured finish | The mold is first smoothed with fine stone powder and then sandblasted, resulting in a textured surface. |
D-1 D-2 D-3 |
Suitable for parts that require a satin or dull textured surface finish. |
As-machined finish | The mold is finished to the machinist's discretion. Tool marks will be visible. | - | Suitable for non-cosmetic parts, such industrial or hidden components. |
* : SPI (Society of Plastic Industry) standards
For a detailed description of the SPI standards and the compatibillity of each materials with a specific surface finish, see the tables in the appendix.
When selecting a glossy surface finish, remember these useful tips:
- A high glossy mold finish is not equivalent to a high glossy finished product. It is significantly subject to other factors such as plastic resin used, molding condition and mold design. For example, ABS will produce parts with a higher glossy surface finish than PP. To find the recommended material and surface finish combination visit the appendix.
- Finer surface finishes require a higher grade material for the mold. To achieve a very fine polish, tool steels with the highest hardness are required. This has an impact on the overall cost (material cost, machining time and post-processing time).
Designing on a budget
Here are some tips to minimize the cost of Injection Molded parts. Keep in mind though that the startup costs for Injection Molding begin at $3000 to $5000.
- Redesign the injection molded part to avoid undercuts: Undercuts always add cost and complexity, as well as maintenance to the mold. A clever redesign can often eliminate undercuts. See the previous section for ideas to deal with undercuts.
- Make the injection molded part smaller: Smaller parts can be molded faster resulting in a higher production output, making the cost per part lower. Smaller parts also result in lower material costs and reduce the price of the mold.
- Avoid small details: To manufacture a mold with small details require longer machining and finishing times. Text is an example of this and might even require specialized machining techniques such as electrical discharge machining (EDM) resulting in higher costs.
- Use lower grade finishes: Finishes are usually applied to the mold by hand, which can be an expensive process, especially for high-grade finishes. If your part is not for cosmetic use, don’t apply a costly high-grade finish.
- Consider secondary operations: For lower volume productions (less than 1000 parts), it may be more cost effective to use a secondary operation to complete your injection molded parts. For example, you could drill a hole after molding rather than using an expensive mold with side-action cores.
Do you still have questions about optimizing your design for Injection Molding?
Summary table
Feature | Recommendation |
---|---|
Wall thickness |
Use a uniform wall thickness throughout the part. Recommended thickness: 1.2 mm and 3 mm. |
Edges |
Add a radius to all edges and corners. Recommended radius: 0.5x the wall thickness (for internal edges) 1.5x the wall thickness (for external edges) |
Thick sections |
Hollow out thick sections. Add ribs to improve strength. |
Ribs |
Recommended max. thickness: 0.5x the wall thickness Recommended max. height: 3x the wall thickness |
Draft angle |
Minimum draft angle: 2o degrees for all vertical walls For features taller than 50 mm: increase the draft angle by one degree every 25 mm |
Bosses |
Think of bosses as circular ribs (same design restrictions apply). For bosses with screws or inserts: Outer diameter: 2x the nominal diameter of the screw or insert |
Text |
Prefer embossed over engraved text. Recommended text height: 0.5 mm Recommended font size: 20 points |
Snap-fit joints | Recommended min. thickness: 0.5x wall thickness |
Crush ribs |
Omit the draft angle. Recommended min. height: 2 mm Recommended interference: 0.25 mm |
Living hinges |
Recommended materials: PP, PE or Nylon (PA) Recommended hinge thickness: 0.25 mm and 0.35 mm |
Undercuts | Redesign to avoid undercuts is recommended. |
Rules of Thumb
- Use 3D printing or CNC machining to prototype and finalize your designs before you go to production with Injection Molding.
- To avoid defects, keep wall thickness constant, add draft angles to vertical walls and round all corners.
- Add ribs to improve the strength and stiffness of thin sections, instead of increasing their thickness.
- Avoid expensive sliding side-core actions by redesigning your part to avoid undercuts altogether.
- When a certain surface finish is required, certain materials behave better than others.