Fused deposition modeling (FDM) 3D printing, also known as fused filament fabrication (FFF), is an additive manufacturing (AM) process within the realm of material extrusion. FDM builds parts layer by layer by selectively depositing melted material in a predetermined path. It uses thermoplastic polymers that come in filaments to form the final physical objects.
Composing the largest installed base of 3D printers worldwide, FDM is the most widely used technology across most industries, and likely the first process you think of when 3D printing comes up.
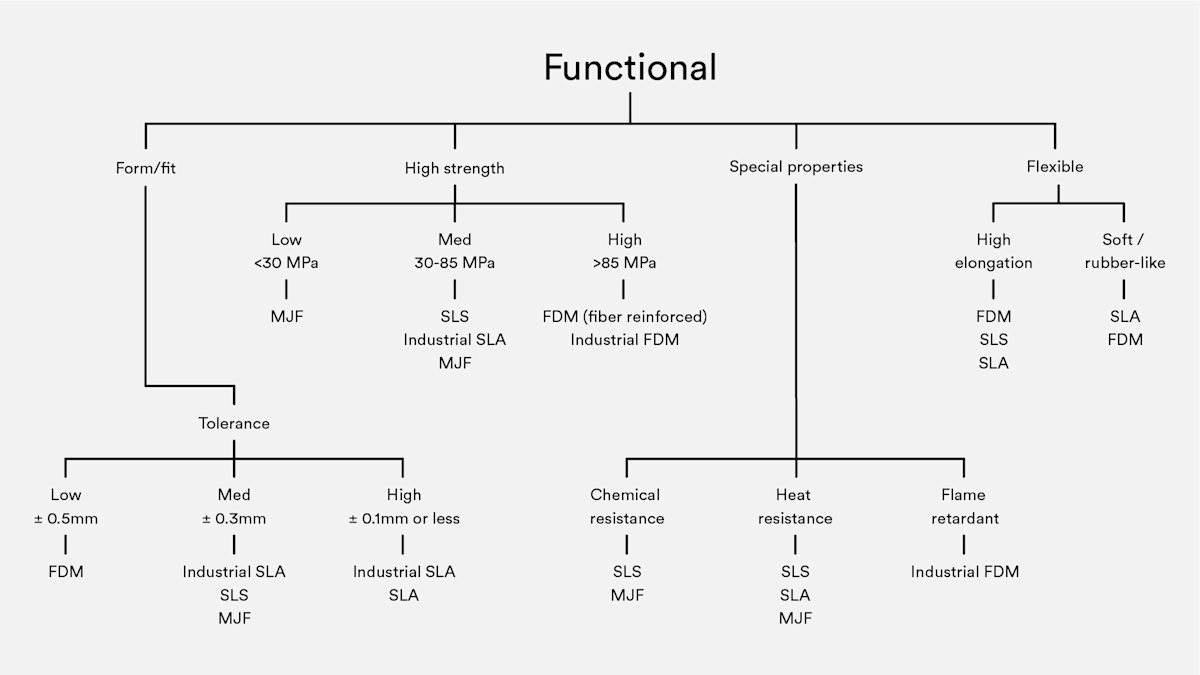
Curious about the price of FDM 3D printing?
Our FDM 3D printing services Upload a CAD for a free, instant FDM quote
In this article, we cover the basic principles and key characteristics of this popular additive technology. We also explore the differences between FDM machines built for prototyping (desktop) and industrial applications and provide tips and tricks for engineers to get the best results from FDM 3D printing.
Watch before you read: how to prototype like a pro with FDM 3D printing
This video breaks down how to use FDM 3D printing for rapid prototyping.
How does FDM 3D printing work?
An FDM 3D printer works by depositing melted filament material over a build platform layer by layer until you have a completed part. FDM uses digital design files that are uploaded to the machine itself and translates them into physical dimensions. Materials for FDM include polymers such as ABS, PLA, PETG and PEI, which the machine feeds as threads through a heated nozzle.
To operate an FDM machine, you first load a spool of this thermoplastic filament into the printer. Once the nozzle hits the desired temperature, the printer feeds the filament through an extrusion head and nozzle.
This extrusion head is attached to a three-axis system that allows it to move across the X, Y and Z axes. The printer extrudes melted material in thin strands and deposits them layer by layer along a path determined by the design. Once deposited, the material cools and solidifies. You can attach fans to the extrusion head to accelerate cooling in some cases.
To fill an area, multiple passes are required, similar to coloring in a shape with a marker. When the printer finishes a layer, the build platform descends and the machine begins work on the next layer. In some machine setups, the extrusion head moves up. This process repeats until the part is finished.
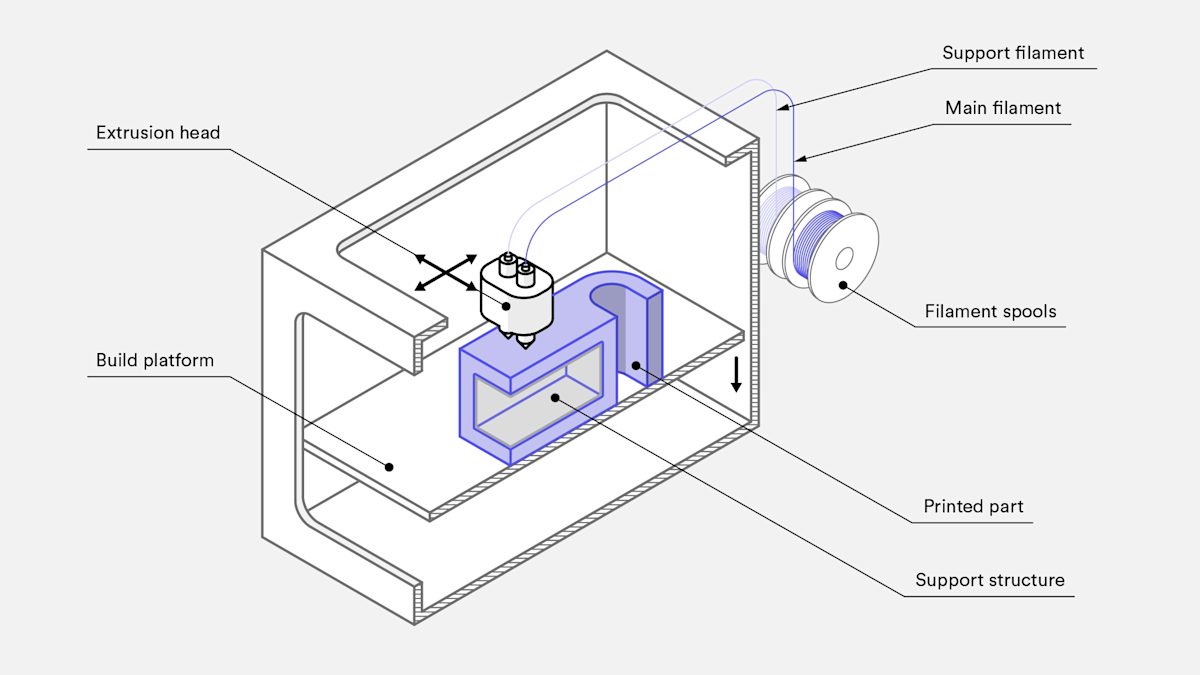
What are the print parameters for FDM 3D printers?
Most FDM systems allow you to adjust several process parameters. These include the nozzle and build platform temperatures, build speed, layer height and cooling fan speed. If you’re a designer, you normally don’t have to worry about these adjustments, as an AM operator probably already has that covered.
Factors that are important to consider, though, are build size and layer height. The common build size of a desktop 3D printer is 200 x 200 x 200 mm, while industrial machines can reach sizes of 1,000 x 1,000 x 1,000 mm. If you prefer to use a desktop machine to print your part, you can break down a big model into smaller parts and then reassemble it.
FDM’s typical layer height measures between 50 and 400 microns. Printing shorter layers produces smoother parts and more accurately captures curved geometries, though printing taller layers lets you create parts quicker and for a lower price tag.
Design tip: A smart compromise we recommend is to print layers 200 microns thick. Want to know more? Check out our article on the impact of layer height on 3D-printed parts.

Is there a difference between desktop and industrial FDM printers?
FDM printers generally fall into two main categories: industrial (professional) and prototyping (desktop) machines. Both printer grades have distinct applications and advantages, though the main difference between the two technologies is their scale of production.
Industrial FDM 3D printers, like the Stratasys 3D printer, are far more expensive than their desktop counterparts - desktop machines being mostly for at-home, consumer use - so using them for your custom parts will run up a higher tab. As industrial machines are more efficient and powerful than desktop FDM printers, they are more often used for tooling, functional prototypes and end-use parts.
As well, industrial FDM printers can complete larger orders much faster than desktop machines. They are designed for repeatability and reliability and can produce the same part over and over with minimal human intervention. Desktop FDM printers are not nearly as robust. With desktop machines, you have to perform frequent user maintenance and regular calibration.
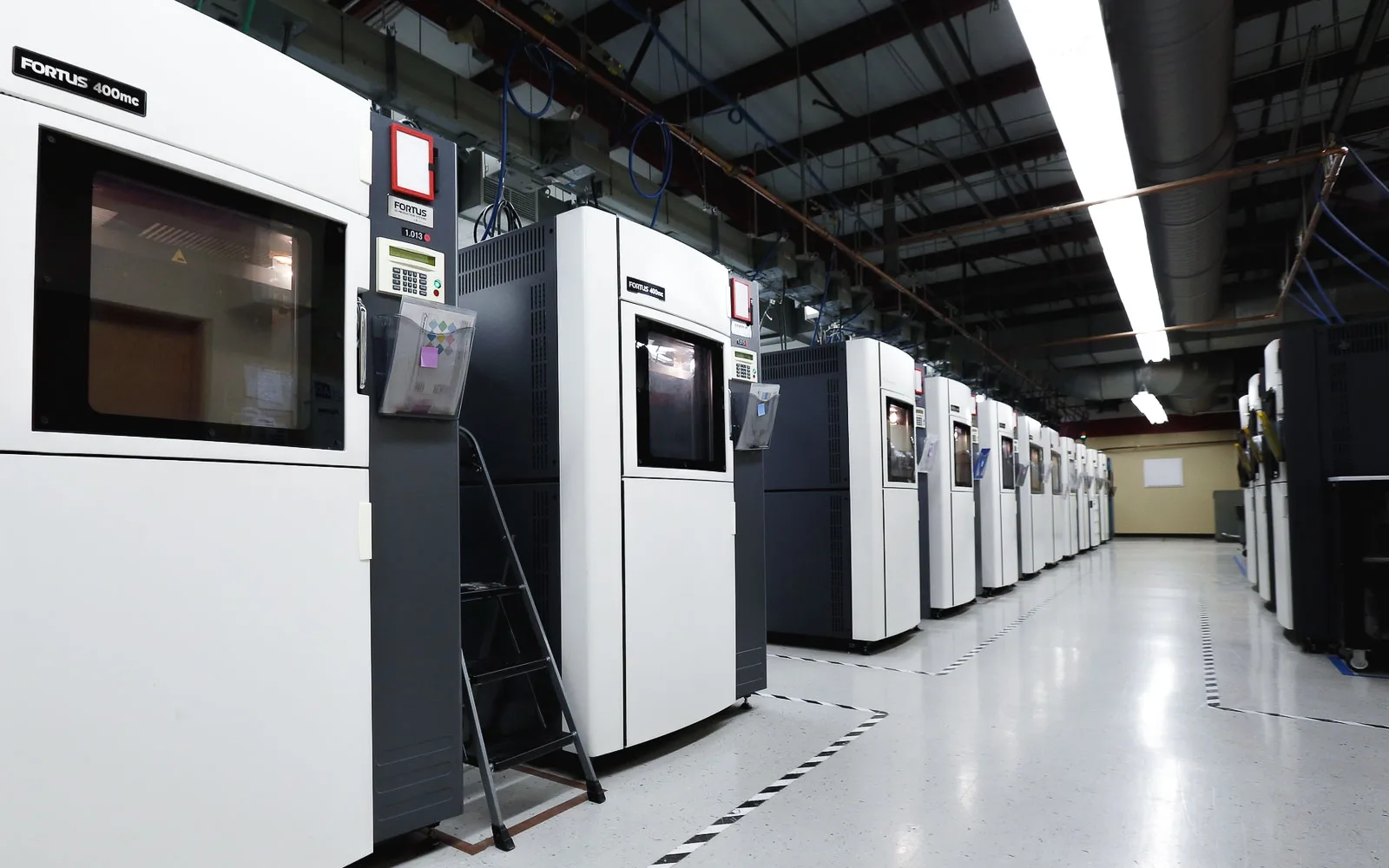
In the table below, we break down the main differences between a typical desktop FDM machine and an industrial one.
Property | Industrial FDM | Desktop FDM |
---|---|---|
Standard accuracy | ± 0.3% (lower limit: ± 0.2 mm) | ± 0.5% (lower limit: ± 1.0 mm) |
Typical layer thickness | 0.18 - 0.5 mm | 0.10 - 0.25 mm |
Minimum wall thickness | 1 mm | 0.8 - 1 mm |
Maximum build envelope | Large (e.g. 900 x 600 x 900 mm) | Medium (e.g. 200 x 200 x 200 mm) |
Common materials | ABS, PC, ULTEM | PLA, ABS, PETG |
Support material | Water-soluble/Break-away | Same as part (typically) |
Production capabilities (per machine) | Low/Medium | Low |
Machine cost | $50000+ | $500 - $5000 |
What are the characteristics of FDM 3D printing?
While FDM 3D printers vary in terms of their extrusion systems and the part quality you get from various machines, there are common characteristics that you can expect from every FDM printing process.
Warping
Warping is one of the most common defects in FDM. When extruded material cools during solidification, its dimensions decrease. Since different sections of the printed part cool at different rates, their dimensions also change at different speeds. Differential cooling causes the buildup of internal stresses that pull the underlying layer upward, causing it to warp.
There are several ways to prevent warping. One method is to closely monitor the temperature of your FDM system, especially the build platform and chamber. You can also increase the adhesion between the part and the build platform to mitigate warping.
Making certain choices during the design process can also reduce the likelihood of your part warping. Here are a few examples:
-
Large, flat areas - like you’d see on a rectangular box - are more prone to warping. Try to avoid these whenever possible.
-
Thin protruding features - think of the prongs on a fork - are also prone to warping. Adding extra guiding or stress-relieving material at the edges of thin features to increase the area that makes contact with the build platform helps to avoid this.
-
Sharp corners warp more often than rounded shapes, so we recommend adding fillets to the design.
-
Every material has its own susceptibility to warping. For instance, ABS is generally more sensitive to warping than PLA or PETG, for instance.
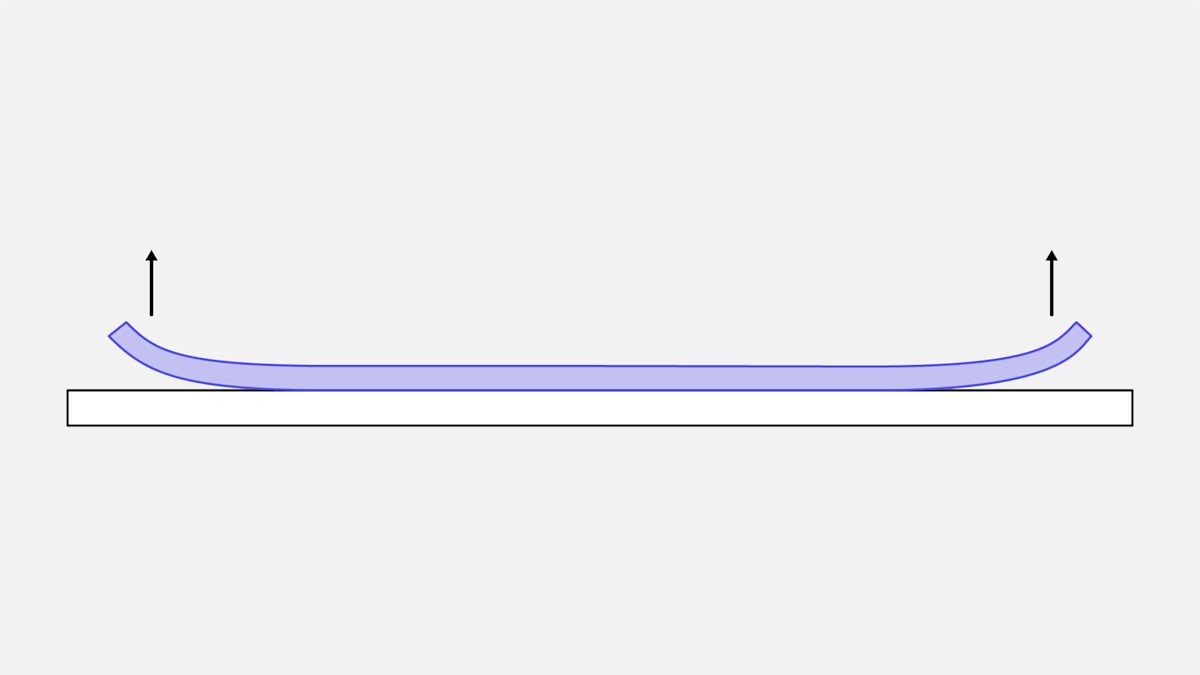
Layer adhesion
Secure adhesion between deposited layers of a part is critical in FDM. When an FDM machine extrudes molten thermoplastic through the nozzle, this material presses against the previously printed layer. High temperature and pressure cause this layer to re-melt and enable it to bond with the previous layer.
And since the molten material presses against the previously printed layer, its shape deforms to an oval. This means that FDM parts always have a wavy surface, no matter what layer height is used, and that small features, such as small holes or threads, may require post-processing.
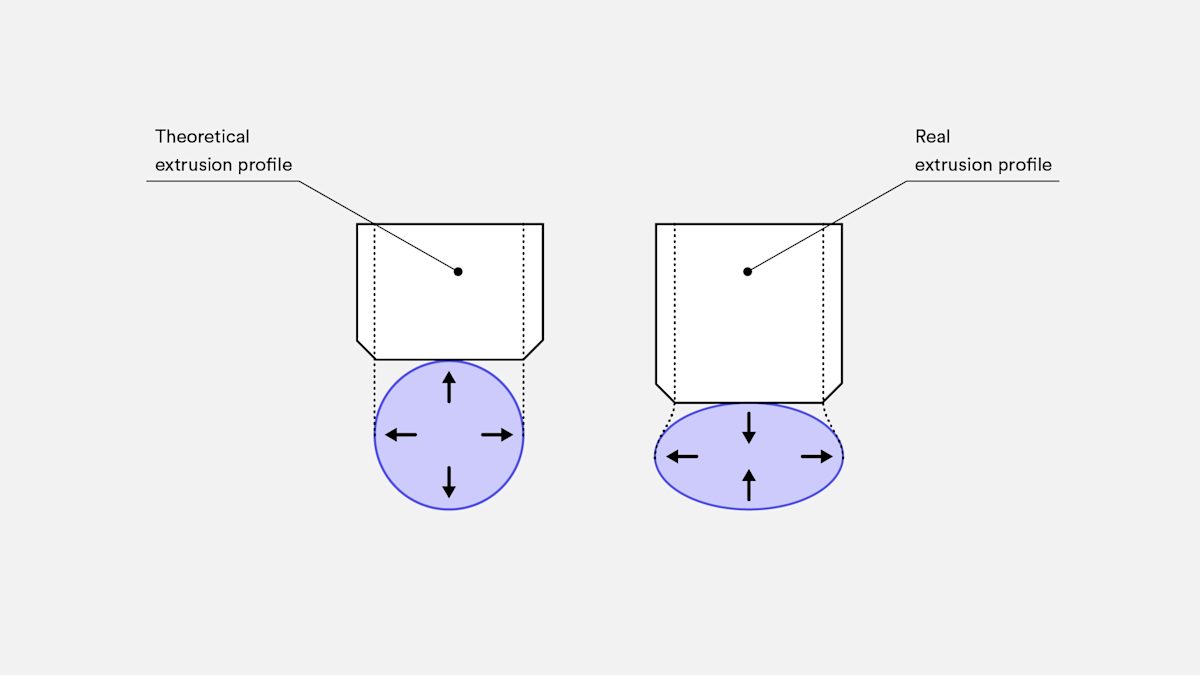
Support structure
FDM printers can’t feasibly deposit molten thermoplastic over thin air. Certain part geometries require support structures, which are usually printed in the same material as the parts themselves.
Oftentimes, removing support structure materials can be difficult, so it’s often far easier to design parts in such a way that minimizes the need for support structures. Support materials that dissolve in liquid are available, but you generally use them in tandem with higher-end FDM 3D printers. Be aware that using dissolvable supports will increase the overall cost of a print.
Infill and shell thickness
To reduce print time and save on materials, FDM printers usually don’t produce solid parts. Instead, the machine traces the outer perimeter - called the shell - over several passes, and fills the interior - called the infill - with an internal, low-density structure.
Infill and shell thickness significantly affect the strength of FDM-printed parts. Most desktop FDM printers have a 20% infill density default setting and 1 mm shell thickness, which provides a suitable compromise between strength and speed for quick prints.
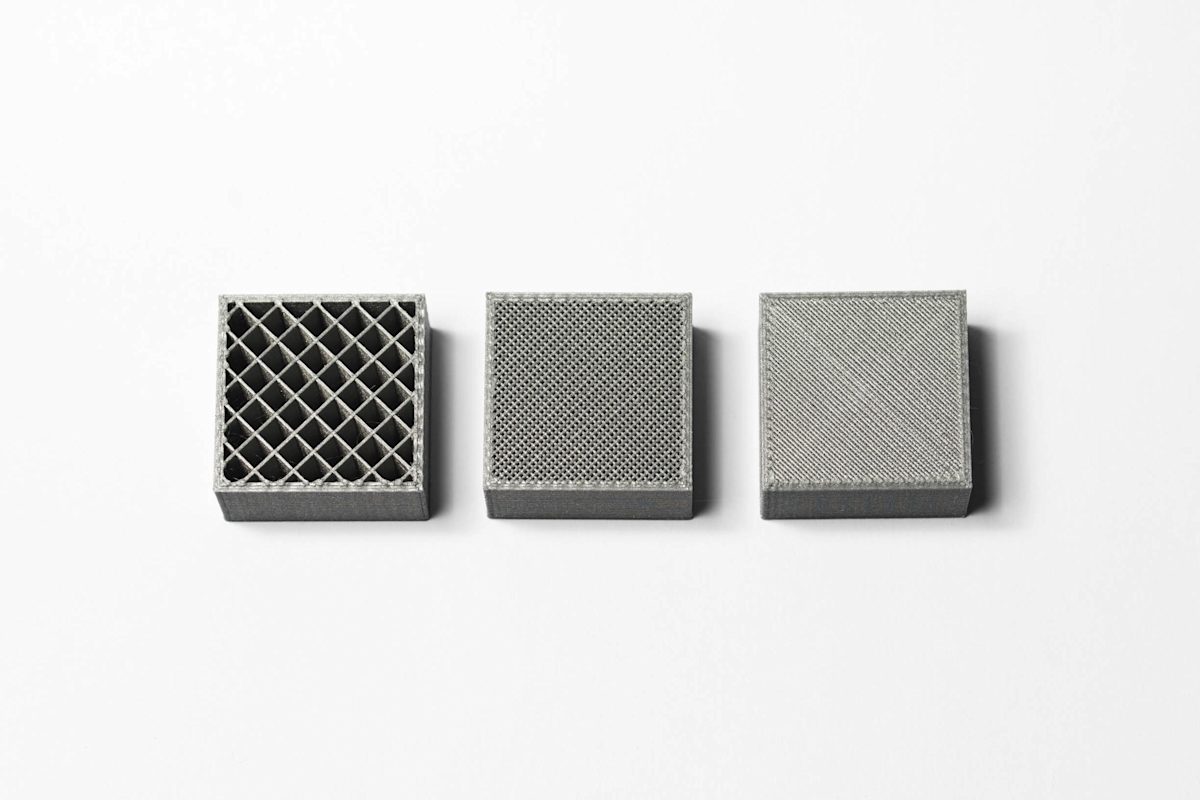
The table below summarizes the main characteristics of FDM 3D printing.
FDM | |
---|---|
Materials | Thermoplastics (PLA, ABS, PETG, PC, PEI etc) |
Dimensional Accuracy | ± 0.5% (lower limit ± 0.5 mm) - desktop ± 0.15% (lower limit ± 0.2 mm) - industrial |
Typical Build Size | 200 x 200 x 200 mm - desktop 900 x 600 x 900 mm - industrial |
Common layer thickness | 50 to 400 microns |
Support | Not always required (dissolvable available) |
What are common materials for FDM 3D printing?
One of the key advantages of FDM (both desktop and industrial) is the technology’s wide range of materials. This includes commodity thermoplastics such as PLA and ABS, engineering materials like PA, TPU and PETG, and high-performance thermoplastics, including PEEK and PEI.
PLA filament is the most common material used in desktop FDM printers. Printing with PLA is relatively easy and can produce parts with finer details. When you need higher strength, ductility and thermal stability, you normally use ABS. However, ABS is more prone to warping, especially if you are using a machine that doesn’t have a heated chamber.
Another alternative for desktop FDM printing is PETG, which is comparable to ABS in its composition and how easy it is to print with. All three of these materials are suitable for most 3D printing service applications, from prototyping to form, fit and function, to low-volume production of models or functional parts.
Industrial FDM machines, on the other hand, mainly use engineering thermoplastics, including ABS, polycarbonate (PC) and Ultem. These materials usually come with additives that alter their properties and make them particularly useful for industrial needs like high impact strength, thermal stability, chemical resistance and biocompatibility.
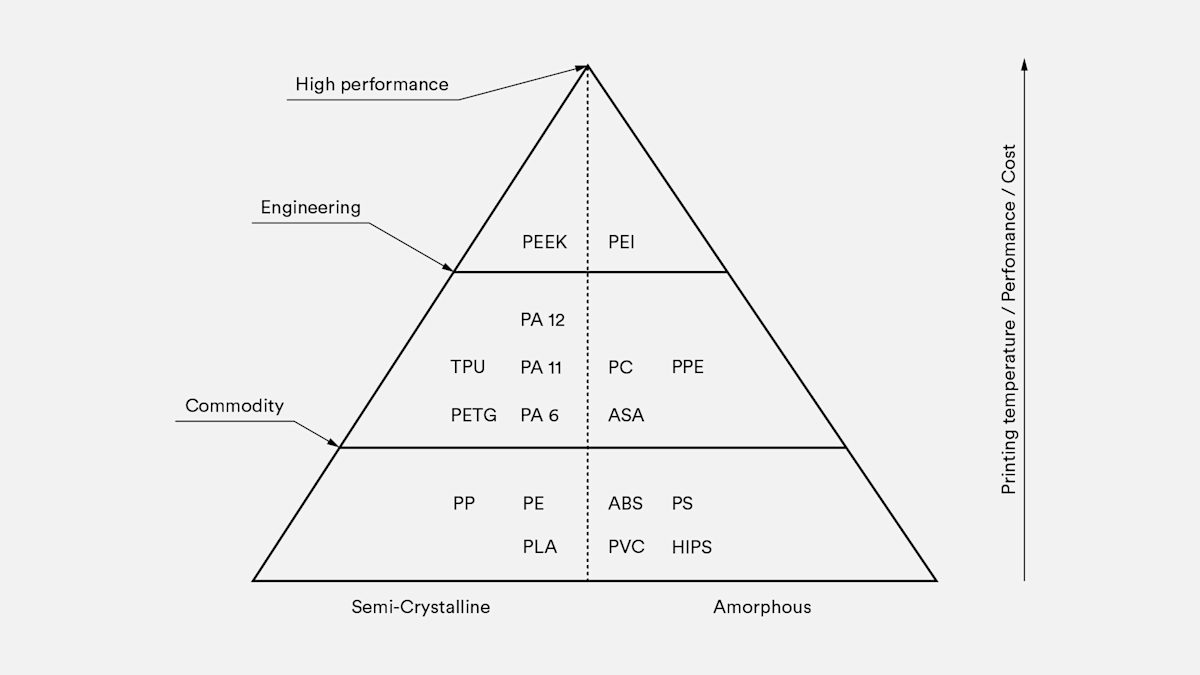
Printing in different materials will affect your part’s mechanical properties and accuracy, as well as its cost. We compare the most common FDM materials in the table below.
Material | Characteristics |
---|---|
ABS | + Good strength + Good temperature resistance - More susceptible to warping |
PLA | + Excellent visual quality + Easy to print with - Low impact strength |
Nylon (PA) | + High strength + Excellent wear and chemical resistance - Low humidity resistance |
PETG | + Food Safe* + Good strength + Easy to print with |
TPU | + Very flexible - Difficult to print accurately |
PEI | + Excellent strength to weight + Excellent fire and chemical resistance - High cost |
For more details, see this review of the main differences between PLA and ABS —the two most common FDM materials—and an extensive comparison of all common FDM materials.
Post-processing for FDM 3D printing
FDM 3D printed parts can be finished to quite a high standard via several post-processing methods, including sanding and polishing, priming and painting, cold welding, vapor smoothing, epoxy coating and metal plating.
Interested in exploring all the post-processing options for your next production run of FDM parts? Read our extensive guide to what’s available.
What are the best practices for printing with FDM?
-
FDM can produce prototypes and functional parts quickly and cost-effectively.
-
There is a wide range of materials available for FDM.
-
The typical build size of a desktop FDM 3D printer is 200 x 200 x 200mm. Industrial machines have a larger build size.
-
To prevent warping, avoid large flat areas and add fillets to sharp corners.
-
FDM is inherently anisotropic, so it is unsuitable for mechanically critical components.
-
The minimum feature size of FDM machines is limited by the diameter of the nozzle and the layer thickness.
-
Material extrusion makes it impossible to produce vertical features (in the Z direction) with geometry smaller than the layer height (typically 0.1 - 0.2 mm).
-
FDM typically can’t produce planar features (on the XY plane) smaller than the nozzle diameter (0.4 - 0.5 mm).
-
Walls have to be at least 2 to 3 times larger than the nozzle diameter (i.e. 0.8 - 1.2 mm).
-
If you’re looking to produce smooth surfaces and very fine features, you may need additional post-processing, like sandblasting and machining. Another AM technology like SLA may be more suitable in this case.
If you're ready to get your parts into production, you can head straight to the Protolabs Network platform to get an instant quote and explore our onboard DFM analysis. You can also reach out to networksales@protolabs.com for more information and get matched with a specialized account manager.
Frequently asked questions
What are the advantages of FDM 3D printing?
FDM is more cost-effective than any additive manufacturing technology and makes use of an extensive variety of thermoplastic materials. Manufacturing with FDM means shorter lead times, as well.
What are the disadvantages of FDM 3D printing?
While FDM is very cost-efficient, it also has the lowest resolution compared to other 3D printing technologies. This makes it a less viable option for parts with very small details.
Does FDM require post-processing?
Parts printed using FDM are likely to have visible layer lines, so post-processing is required to give parts a smooth finish.
How accurate is FDM?
In general, part accuracy depends on how you’ve calibrated your FDM printer and the complexity of your model. Industrial FDM printers produce parts more accurately than desktop machines, but home 3D printer technology is quickly catching up.
How expensive is FDM?
FDM is the most cost-effective way to produce custom thermoplastic parts and prototypes on the market today. Desktop FDM is the absolute most cost-efficient option, but produces lower quality parts than its industrial counterpart.
What materials are available for FDM?
A wide range of materials is available for FDM, including PLA, ABS, TPU, PETG and PEI.
How fast is FDM?
Producing custom parts with FDM is relatively quick, with lead times tending to be short (typically only a few days).
What is FDM mainly used for?
FDM technology tends to be most suitable for prototyping, modeling and low-volume manufacturing applications. Industrial-scale FDM can be used for functional prototypes and end-use parts, among other applications.
Why is FDM currently the most popular 3D printing technology?
FDM printers produce high-quality parts from durable materials, able to retain sound mechanical properties. Both types of FDM machines offer high dimensional accuracy, and even at the industrial level, FDM tends to be more cost-efficient than other AM processes.