SLA (Stereolithography) is a popular 3D printing technique and one of the leading resin printing technologies. It stands out in the additive manufacturing industry due to its ability to create highly accurate, isotropic, and watertight prototypes. It also excels in producing production-grade parts with smooth surfaces and intricate details.
While SLA offers numerous benefits, deciding if it’s the ideal solution for your specific parts can be challenging. This guide introduces the core principles of SLA to help you assess its suitability for your needs.
For further details on how Protolabs Network offers SLA, explore our SLA services or get in touch with us at networksales@protolabs.com.
What is SLA (stereolithography)?

Stereolithography (SLA) is an advanced additive manufacturing process that falls under the vat photopolymerization category. Commonly known as resin 3D printing, it is one of three main vat polymerization technologies alongside Digital Light Processing (DLP) and Liquid Crystal Display (LCD). While all three methods use a light source to cure liquid photopolymer resin, they differ in how the curing process is executed:
-
SLA: Uses a high-precision UV laser to selectively solidify layers of resin.
-
DLP: Employs a digital projector to flash entire layers of UV light onto the resin.
-
LCD: Uses an LCD screen to project specific light patterns for curing.
SLA remains one of the most widely used vat photopolymerization methods due to its ability to produce highly accurate parts with smooth surface finishes. It works by curing liquid thermoset polymers layer by layer using an ultraviolet (UV) laser, making it ideal for applications that demand fine details and precision.
Originally patented in 1986, SLA was the first 3D printing technology ever developed. Today, it continues to be one of the most cost-effective solutions for creating parts with exceptional accuracy and surface quality. To achieve optimal results, designers must fully leverage the strengths of SLA while accounting for its limitations.
Watch before you read: How to get the most out of SLA printing
Here's a short video that will teach you everything you need to know to get started with SLA 3D printing (in ten minutes or fewer).
How does SLA 3D printing work?
SLA 3D printing begins by submerging the build platform in a tank filled with liquid photopolymer resin, positioning it at a precise layer height above the surface. A high-precision UV laser then selectively cures and solidifies the resin, creating each layer of the model.
During the photopolymerization process, the UV laser activates the monomer carbon chains in the liquid resin, triggering a chemical reaction that forms solid, crosslinked bonds. This results in strong, durable parts with fine details and smooth surfaces. To accurately direct the laser, a system of mirrors—called galvos—guides the beam along a predefined path, ensuring the entire cross-sectional area of the model is cured into a fully solid structure.
Once printing is complete, the part remains in a partially cured state. Additional post-processing under UV light is often required to enhance its mechanical and thermal properties. Unlike thermoplastics used in fused deposition modeling (FDM), SLA materials are thermoset polymers, meaning the curing process is irreversible. SLA parts cannot be melted back into liquid form—when exposed to extreme heat, they will burn rather than soften.
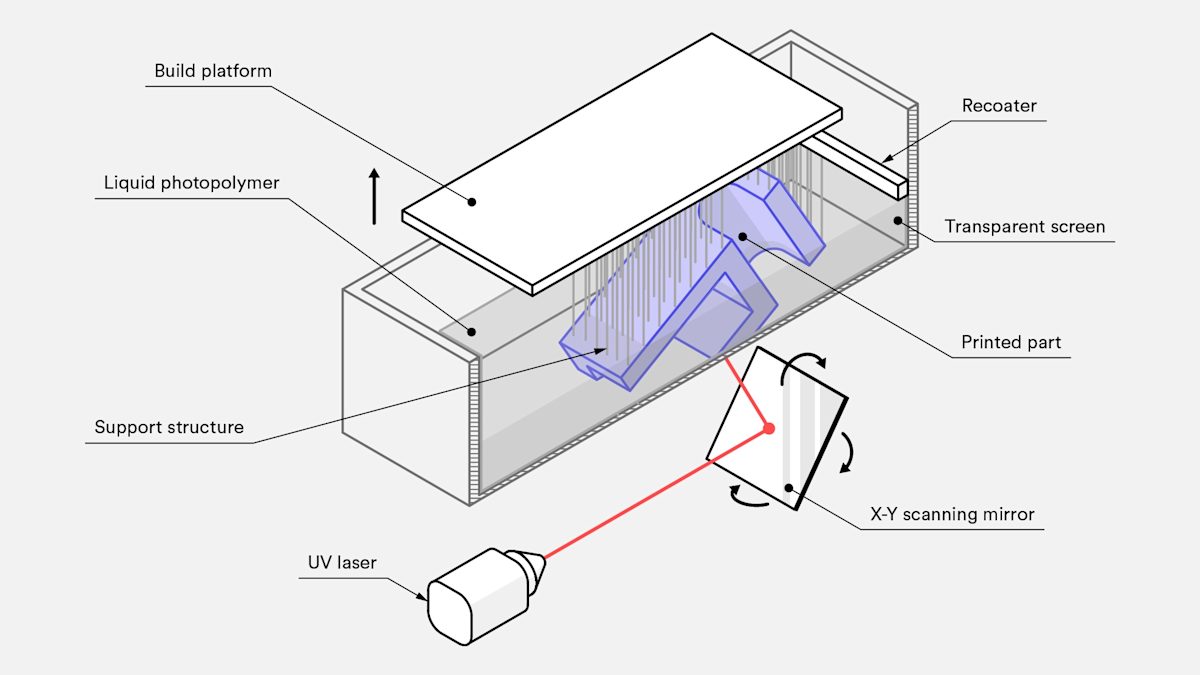
What are the print parameters of SLA?
Layer height: Ranges between 25 and 100 microns. Lower layer heights capture curved geometries more accurately but increase the build time and cost—and the probability of a failed print. A layer height of 100 microns is suitable for most common applications.
Build size: This is another parameter that is important for the designer. The build size depends on the type of SLA machine. There are two main SLA machine setups: the top-down orientation and the bottom-up orientation:
-
Top-down printers place the laser source above the tank and the part is built facing upwards. The build platform begins at the very top of the resin vat and moves downwards after every layer.
-
Bottom-up printers place the light source under the resin tank (see figure above) and the part is built upside down. The tank has a transparent bottom with a silicone coating that allows the light of the laser to pass through but stops the cured resin from sticking to it. After every layer, the cured resin is detached from the bottom of the tank, as the build platform moves upwards. This is called the peeling step.
The bottom-up orientation is mainly used in desktop printers, while the top-down is generally used in industrial SLA systems. Bottom-up SLA printers are easier to manufacture and operate, but their build size is limited. This is because the forces applied to the part during the peeling step might cause the print to fail. On the other hand, top-down printers can scale up to very large build sizes without a big loss in accuracy. The advanced capabilities of these systems come at a higher cost.
The following table summarizes the key characteristics and differences between the two orientations:
Bottom-up (Desktop) SLA | Top-down (Industrial) SLA | |
---|---|---|
Advantages | + Lower cost + Widely available |
+ Very large build size + Faster build times |
Disadvantages | - Small build size - Smaller material range - Requires more post-processing due to extensive use of support |
- Higher cost - Requires specialist operator - Changing material involves emptying the whole tank |
Popular SLA printer manufacturers | Formlabs | 3D Systems |
Build size | Up to 145 x 145 x 175mm | Up to 1500 x 750 x 500mm |
Typical layer height | 25 to 100 µm | 25 to 150 µm |
Dimensional Accuracy | ± 0.5% (lower limit: ± 0.010–0.250 mm) | ± 0.15% (lower limit ± 0.010–0.030 mm) |
What are the characteristics of SLA 3D printing?
SLA (Stereolithography) 3D printing is known for its high precision, smooth surface finish, and ability to create complex geometries. However, to achieve optimal results, certain factors must be considered—especially support structures, curling, and layer adhesion.
Support structures in SLA 3D printing
Support structures are essential in SLA printing and are always printed using the same resin material as the part. These supports must be manually removed after printing, and post-processing is necessary to achieve a flawless surface finish. Proper part orientation helps minimize the impact of supports on visually critical areas.
Support Differences: Top-Down vs. Bottom-Up SLA Printers
Top-down SLA printers
-
Support structures function similarly to those in FDM (Fused Deposition Modeling).
-
Necessary for overhangs and bridges, with a critical overhang angle of approximately 30°.
-
Parts can be oriented in any position and are often printed flat to minimize support and layer count.
Bottom-up SLA printers
-
Require more complex support structures due to peeling forces.
-
Minimizing cross-sectional area per layer is crucial to prevent detachment from the build platform.
-
Parts are typically oriented at an angle, prioritizing print stability over reducing support material.
The bottom-up orientation is mainly used in desktop printers, while the top-down is generally used in industrial SLA systems. Bottom-up SLA printers are easier to manufacture and operate, but their build size is limited. This is because the forces applied to the part during the peeling step might cause the print to fail. On the other hand, top-down printers can scale up to very large build sizes without a big loss in accuracy. The advanced capabilities of these systems come at a higher cost.
The following table summarizes the key characteristics and differences between the two orientations:
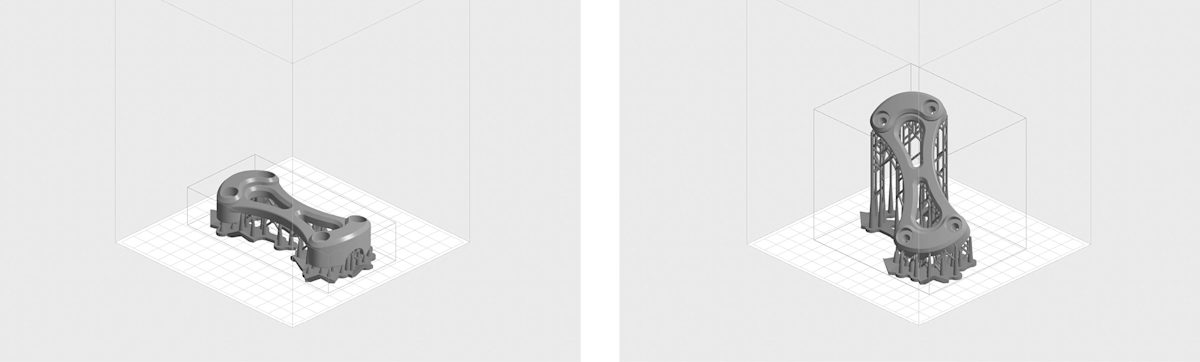
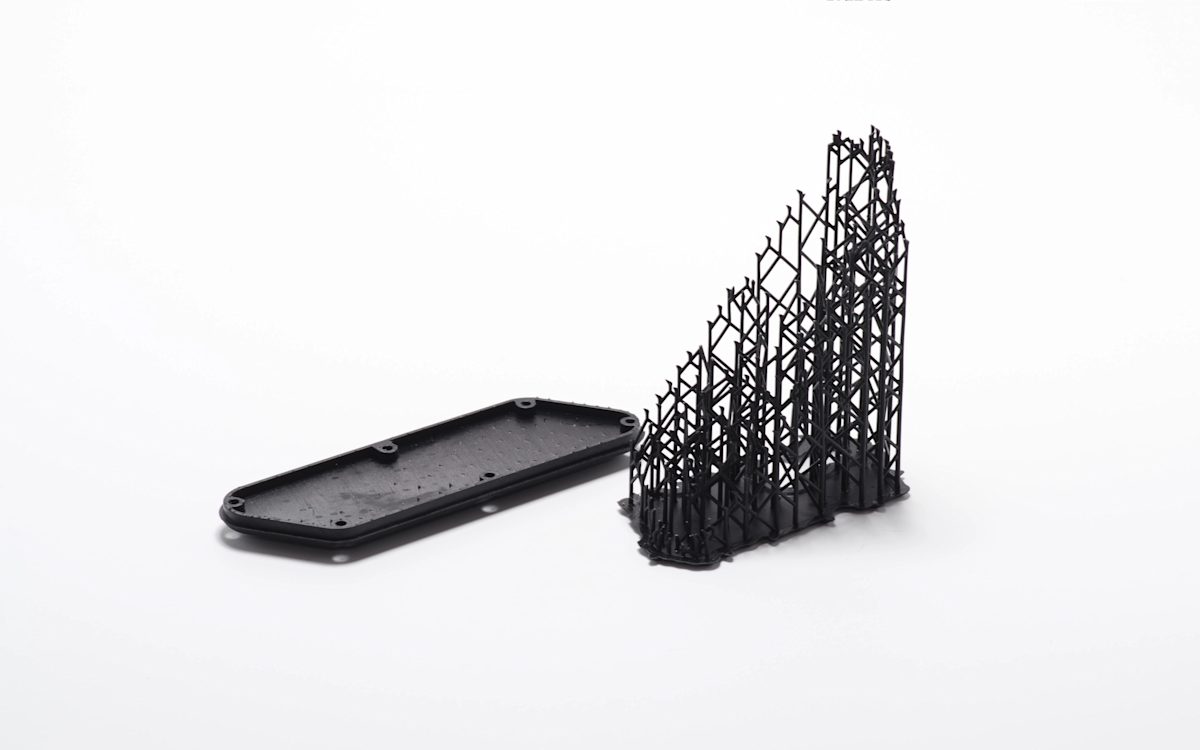
Curling in SLA printing
Curling is one of the most common accuracy-related issues in SLA 3D printing, similar to warping in FDM.It occurs due to resin shrinkage when exposed to the printer's UV light source, creating internal stresses that cause parts to lift or deform.
How to prevent curling:
-
Optimize Support Structures: Proper support anchors vulnerable sections and reduces curling risk.
-
Adjust Part Orientation: Avoid large, flat surfaces to distribute internal stresses more evenly.
-
Limit Over-Curing: Excessive UV exposure, such as direct sunlight post-printing, can exacerbate curling.
Layer adhesion & strength in SLA printing
Unlike FDM, SLA-printed parts exhibit isotropic mechanical properties, meaning they have uniform strength in all directions. This is because SLA does not fully cure each layer with a single UV laser pass—curing continues throughout the process as additional layers fuse together.
Post-curing for enhanced performance
SLA parts require post-curing in a UV light chamber (sometimes with heat) to achieve maximum strength and thermal resistance. However, this process increases hardness but reduces flexibility, making the part more brittle.
-
Tensile Strength: Increases significantly after post-curing (65 MPa vs. 38 MPa).
-
Heat Resistance: Post-cured parts can withstand up to 58°C, compared to 42°C before curing.
-
Elongation at Break: Drops from 12% to 6.2%, reducing flexibility.
Protecting SLA prints from UV damage
Extended exposure to UV light can cause brittleness, discoloration, and curling. To prevent degradation:
-
Store SLA parts away from direct sunlight.
-
Apply a clear UV-protective acrylic spray to shield parts from prolonged UV exposure.
By carefully managing curing, orientation, and post-processing, designers can maximize the durability and precision of SLA 3D-printed parts while minimizing defects.
Accuracy of SLA printing
SLA is one of the most precise 3D printing technologies, capable of achieving layer resolutions as fine as 25 microns and layer thicknesses as low as 10 microns. Industrial SLA printers generally offer higher accuracy than desktop models, with a typical dimensional precision of ±0.2%, down to ±0.13 mm (±0.005”).
The high accuracy of SLA printing allows for tight tolerances, intricate details, and complex geometries. However, several factors influence print precision:
-
Layer Thickness: Thinner layers capture finer details, improving overall accuracy but increasing print time.
-
Laser Spot Size: A smaller laser beam diameter results in sharper details and better precision.
-
Resin Properties: The viscosity and pigmentation of the resin impact dimensional accuracy. Low-viscosity resins with high pigmentation generally produce the most precise prints.
-
Print Orientation: The position of a part during printing affects accuracy due to support placement and resin flow dynamics.
Surface finish
One of SLA’s standout features is its exceptionally smooth surface finish, making it ideal for visual prototypes and high-detail models. The process of curing liquid resin layer by layer with a UV laser minimizes visible layer lines, resulting in near-polished surfaces straight from the printer.
To further refine the surface finish, designers can:
-
Choose a low-viscosity resin to enhance smoothness.
-
Use post-processing techniques such as sanding, polishing, or chemical smoothing to achieve a glossy, injection-molded look.
Because of SLA’s precision and surface quality, manufacturers can create parts that not only meet strict dimensional requirements but also offer aesthetic appeal for end-use applications.
Summary of the main characteristics of SLA 3D printing
The main characteristics of SLA are summarized in the table below:
Stereolithography (SLA) | |
---|---|
Materials | Photopolymer resins (thermosets) |
Dimensional Accuracy | ± 0.5% (lower limit: ±0.10 mm) – desktop ± 0.15% (lower limit ± 0.01 mm) – industrial |
Typical Build Size | Up to 145 x 145 x 175mm – desktop Up to 1500 x 750 x 500mm – industrial |
Common layer thickness | 25–100 µm |
Support | Always required (essential to producing an accurate part) |
What materials are used for SLA printing?
SLA 3D printing uses liquid photopolymer resins, selected based on mechanical strength, surface finish, and thermal resistance.
Industrial SLA printers offer a wider material selection compared to desktop SLA machines, providing designers with greater control over mechanical properties and functional performance.
Types of SLA resins & their properties
Unlike thermoplastics used in FDM and SLS printing, SLA resins are thermosetting polymers, making them more brittle and less suitable for high-load applications. However, advancements in resin technology are continuously improving impact resistance and durability, expanding SLA’s usability for functional prototyping and end-use parts.
The following table outlines the advantages and limitations of the most commonly used SLA resins, helping designers select the right material for their specific application.
Material | Characteristics |
---|---|
Standard resin | + Smooth surface finish - Relatively brittle |
High detail resin | + Higher dimensionally accuracy - Higher price |
Clear resin | + Transparent material - Requires post processing for a very clear finish |
Castable resin | + Used for creating mold patterns + Low ash percentage after burnout |
Tough or Durable resin | + ABS-like or PP-like mechanical properties - Low thermal resistance |
High temperature resin | + Temperature resistance + Used for injection molding and thermoforming tooling |
Dental resin | + Biocompatible+ High abrasion resistant- High cost |
Flexible resin | + Rubber-like material- Lower dimensional accuracy |
What are the options for SLA post-processing?
SLA-printed parts can be refined to achieve a high-quality surface finish using various post-processing techniques. These methods enhance smoothness, durability, and aesthetics, making SLA parts suitable for functional prototypes and end-use applications.
Common SLA post-processing techniques include basic support removal, sanding support nibs, mineral oil finishes, wet sanding, spray paint (clear UV protective acrylic) or polishing to a transparent finish.
For a detailed guide on SLA post-processing methods, check out our comprehensive article on post-processing for SLA parts.
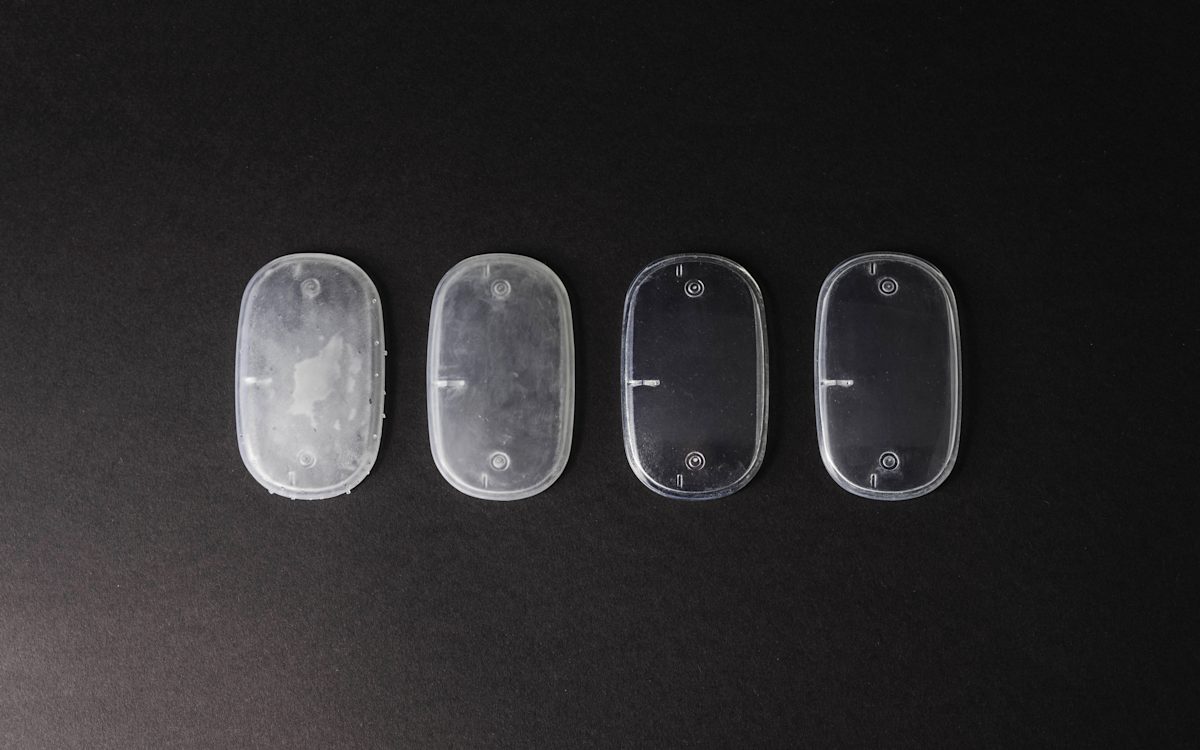
Applications of SLA 3D printing
SLA 3D printing is widely used across industrial and commercial sectors, thanks to its high resolution, precision, and ability to produce intricate geometries with tight tolerances. Below are some of the most common applications where SLA technology excels:
1. Rapid prototyping
SLA is ideal for creating high-fidelity prototypes with smooth surface finishes and fine details, making it perfect for evaluating design form, fit, and function before moving into full-scale production. Its fast printing speed also supports rapid iteration during product development.
2. Sacrificial patterns for casting & molding
SLA printing is commonly used for producing sacrificial patterns in investment casting, mold making, and die casting. These highly detailed patterns are burned out, melted, or dissolved, leaving behind a precise mold cavity for casting metal or other materials.
3. Dental & orthodontics
SLA technology plays a crucial role in digital dentistry, producing:
-
Highly accurate dental models for treatment planning.
-
Custom crowns, bridges, and dentures for patient-specific solutions.
-
Surgical guides for precise implant placement.
4. Medical & Healthcare
Medical professionals use SLA 3D printing to create:
-
Patient-specific anatomical models for pre-surgical planning.
-
Custom surgical guides for enhanced precision.
-
Biocompatible prosthetics and implants, particularly in orthopedics and reconstructive surgery.
5. Aerospace & defense
SLA 3D printing is used in aerospace for:
-
Lightweight, high-precision components for aircraft and spacecraft.
-
Custom tooling and jigs for streamlined manufacturing.
-
Functional prototypes for aerodynamic testing and validation.
6. Automotive industry
Automotive manufacturers use SLA for:
-
Rapid prototyping of vehicle components, including engine parts, interior panels, and exterior trim.
-
Custom molds and tooling for low-volume production.
-
Wind tunnel testing models for aerodynamics analysis.
7. Consumer electronics & product design
SLA enables manufacturers to develop:
-
High-detail electronic enclosures and casings.
-
Precision-engineered connectors and components.
-
Functional prototypes for ergonomic testing and user experience validation.
SLA’s superior accuracy, fine detail resolution, and smooth finish make it a go-to solution for industries requiring precision-engineered parts and high-quality prototypes.
What's the difference between desktop (prototyping) and industrial SLA 3D printers?
SLA 3D printing systems fall into two main categories: desktop (prototyping) printers and industrial SLA machines. While both use the same fundamental technology, they differ significantly in terms of accuracy, material compatibility, scalability, and application focus.
1. Precision & tolerances
-
Desktop SLA Printers: Achieve tolerances between 150 and 300 microns, making them suitable for high-detail prototyping but less ideal for large-scale, highly precise production.
-
Industrial SLA Printers: Offer tolerances as low as 30 microns, maintaining exceptional accuracy even at larger build sizes.
2. Material versatility
-
Desktop SLA: Supports a limited selection of resins, such as standard, tough, and flexible resins.
-
Industrial SLA: Compatible with a wider range of specialized materials, including high-temperature, biocompatible, castable, and clear resins with tailored mechanical properties.
3. Build volume & scalability
-
Desktop SLA: Best suited for small to medium-sized parts due to compact build volumes.
-
Industrial SLA: Capable of producing large parts or batch production runs with consistent quality.
4. Workflow & material handling
-
Desktop SLA: Uses a bottom-up approach, making it easier to swap resins and maintain the machine.
-
Industrial SLA: Often employs a top-down approach, requiring large resin tanks (100L+), making material changes more complex and increasing lead times.
5. Cost & maintenance
-
Desktop SLA: More affordable and accessible for small businesses, startups, and hobbyists. Requires frequent manual maintenance.
-
Industrial SLA: Higher upfront and maintenance costs but designed for repeatability, reliability, and large-scale production with minimal user intervention.
6. Best use cases
-
Desktop SLA: Ideal for visual prototypes, small-batch production, and product design testing where surface finish and detail matter more than engineering properties.
-
Industrial SLA: Best suited for functional prototypes, end-use parts, and high-performance applications requiring temperature resistance, transparency, or high-strength resins.
Overall, SLA’s unique ability to batch produce intricate, customized parts makes it a popular method of manufacturing small parts, low-run production.
What are the advantages of SLA 3D printing?
SLA 3D printing offers several unique benefits, making it a preferred choice for applications requiring precision, smooth finishes, and specialized materials.
1. High dimensional accuracy
SLA can achieve exceptionally tight tolerances and intricate details, making it ideal for functional prototypes, small components, and highly detailed models.
2. Superior surface finish
Unlike FDM or SLS printing, SLA produces parts with a smooth, almost injection-molded quality surface, reducing the need for extensive post-processing.
3. Wide material selection
-
SLA supports a range of specialty resins, including:
-
Clear resins for transparent parts
-
Flexible resins for rubber-like properties
-
Castable resins for jewelry and investment casting
4. Fast printing speed
Compared to other high-accuracy 3D printing methods, SLA is one of the fastest, making it well-suited for rapid prototyping and short production runs.
5. Minimal warping & shrinkage
SLA parts experience less distortion compared to other 3D printing technologies, ensuring consistent accuracy and structural integrity.
6. Low material waste
SLA printers use liquid resin efficiently, and uncured resin can often be reused, reducing overall material waste and making it a cost-effective option for production.
7. High resolution & uniformity
SLA maintains fine details and high resolution across the entire build volume, ensuring uniform quality and consistency, even for large or complex prints.
If you need highly detailed, smooth, and dimensionally accurate parts with a broad material selection and minimal waste, SLA 3D printing is one of the best choices available.
What are the disadvantages of SLA 3D printing?
While SLA 3D printing offers high precision and smooth surface finishes, it also comes with certain drawbacks:
-
Brittleness – SLA parts are generally brittle, making them less suitable for functional prototypes that require durability.
-
UV sensitivity – Exposure to sunlight over time can degrade the mechanical properties and appearance of SLA-printed parts.
-
Support structures – Every SLA print requires support structures, which must be removed post-printing. This can leave visible marks and necessitate additional finishing.
-
Limited build volume – SLA printers often have smaller build areas compared to other 3D printing technologies, restricting the size of individual parts.
-
Material handling challenges – SLA resins can be messy and require careful handling due to potential toxicity. Proper ventilation and protective measures may be necessary.
-
Post-curing requirement – To achieve optimal mechanical properties, SLA parts usually require additional UV curing, increasing post-processing time and costs.
-
Limited mechanical functionality – While SLA offers a variety of resin options, its materials may not match the mechanical strength or flexibility of FDM or SLS prints.
Despite these limitations, SLA remains a preferred choice for high-detail prototypes, aesthetic models, and specialized applications requiring precision.
Top tips & tricks for SLA 3D printing
Wondering if SLA 3D printing is the right choice for your parts or products? Here are some key insights to help you decide:
-
Best for visual prototypes – SLA excels at producing high-quality visual prototypes with smooth surfaces and intricate details.
-
Ideal for small, precise parts – Desktop SLA is a cost-effective solution for manufacturing small, injection-molded-like parts, typically no larger than a fist.
-
Industrial SLA for large-scale prints – Industrial SLA machines can create large parts, with build sizes reaching up to 1500 x 750 x 500 mm.
Want to learn more? Explore our guide to 3D printing or speak with a Protolabs Network engineer by contacting networksales@protolabs.com.
Get a quote
To manufacture your design using SLA 3D printing, upload a CAD file for instant pricing and lead times. You can also speak to our 3D printing experts at networksales@protolabs.com for personalized technical advice about your project.
Find out how SLA compares with DLP, 3D printing for industrial purposes, and all you need to get started with additive manufacturing on our Knowledge Base.
Frequently asked questions
What is needed to create a 3D SLA print?
The process involves an SLA 3D printer, a source of UV light for curing your print, and resin.
Is SLA printing a form of 3D resin printing?
Yes, SLA printing is a form of 3D resin printing.
What are the alternatives for SLA printing?
Common alternatives for SLA include FDM, SLS, and MJF 3D printing, each with different strengths depending on your application.
Does Protolabs Network offer a 3D SLA printing service?
Yes, Protolabs Network offers an SLA 3D printing service with a wide variety of prototyping and industrial resin materials to choose from.
What are the typical costs of SLA printing?
Exact costs will vary, depending what you are printing, but common factors that affect cost include resin, post-processing, the type of printer used, and other associated labor costs through the manufacturing process.