Selective Laser Sintering (SLS) is a type of additive manufacturing that falls under the powder bed fusion category. In the SLS 3D printing process, a high-powered laser selectively sinters particles of thermoplastic polymer powder, fusing them together layer by layer to create a solid, functional part. These materials are used in granular form and offer excellent mechanical properties.
One major advantage of SLS is its versatility. It’s an ideal alternative to injection molding when you want to avoid the high upfront tooling costs. SLS is particularly cost-effective for producing durable, high-quality components in low to mid volumes — typically fewer than 1,000 units — allowing you to test fit, function, and performance before investing in production tooling.
At Protolabs Network, our SLS 3D printing service supports both functional prototyping and small to medium production runs for end-use polymer parts. Want to learn how to get the most out of SLS for your application? Talk to one of our engineers by contacting networksales@protolabs.com.

How does SLS 3D printing work?
SLS 3D printing works by using a high-powered laser to selectively sinter small particles of polymer powder, fusing them together to form solid layers. Unlike other 3D printing methods, SLS scans and sinters the entire cross-section of each layer, resulting in strong, fully solid parts.
Here’s how the process works:
-
Preheating: The powder reservoir and build area are heated to just below the polymer's melting point.
-
Layering: A re-coating blade spreads a thin, even layer of powder over the build platform.
-
Laser Sintering: A CO₂ laser scans and sinters the shape of the layer, bonding powder particles precisely where the part geometry requires.
-
Layer-by-Layer Build: After each layer, the platform lowers slightly, and a new powder layer is applied. This process repeats until the part is fully formed.
-
Cooling Phase: Once printing is complete, the build chamber must cool down before parts can be removed—this step may take up to 12 hours.
-
Post-Processing: Printed parts are encased in unused powder, which is removed with compressed air or media blasting. The parts are then ready for use or additional post-processing.
Watch before you read: SLS 3D printing in action
See how the SLS process 3D prints impressive components in this 30-second video.
Can you use SLS 3D printing for rapid prototyping?
Yes, SLS 3D printing is an excellent choice for rapid prototyping, especially when developing functional polymer components. One major advantage of SLS is its ability to produce highly accurate parts with complex geometries—without the need for support structures. Unlike FDM or SLA, SLS delivers consistent mechanical properties throughout the part, allowing for prototypes that closely match the quality of end-use components. This makes it ideal for creating concept models, trial versions, and functional prototypes with confidence.
Can you use SLS 3D printing for low-production runs?
Absolutely. Thanks to its flexibility and design freedom, SLS is a smart and scalable solution for low-production runs. It’s a cost-effective alternative to injection molding when quantities are small (typically under 1,000 units) and tooling costs are a concern. With the ability to handle intricate geometries, multiple part finishes, and varying lead times, SLS supports everything from pilot production to small-batch manufacturing—without sacrificing quality or performance.
How does an SLS 3D printer work?
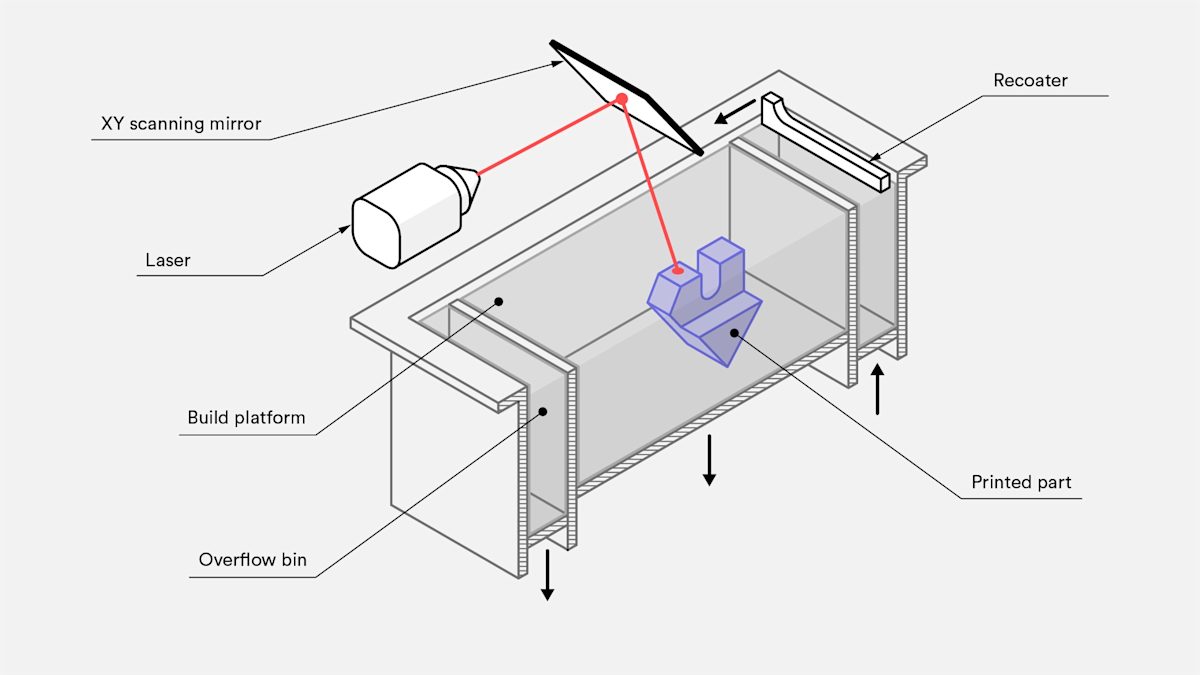
Preset parameters & layer height
Most SLS 3D printers come with predefined settings set by the manufacturer, ensuring consistent output and ease of operation. A typical layer height ranges between 100–120 microns, which offers a good balance between surface resolution and build speed.
No need for support structures
One of the most practical features of SLS is that it doesn’t require any support structures. The surrounding unsintered powder naturally holds parts in place during printing, allowing for intricate geometries and internal features that would be challenging—or even impossible—with other 3D printing methods.
Efficient use of build volume
Optimizing the build volume is essential, particularly for small production batches. Since laser scanning is fast, it's the re-coating step that determines the overall print time. Whether one or several parts are printed, the printer processes the same number of layers. As a result, build chambers are often packed efficiently before printing begins, which can influence lead time.
Layer Adhesion
SLS-printed parts show excellent layer bonding, leading to almost uniform mechanical properties in all directions. This makes them well-suited for functional prototypes and end-use parts.
Here’s how the mechanical properties of PA 12 (the most common SLS material) compare:
X-Y direction | Z direction | Bulk PA12 | |
---|---|---|---|
Tensile Strength | 48 MPa | 42 MPa | 35–55 MPa |
Tensile Modulus | 1650 MPa | 1650 MPa | 1270–2600 MPa |
Elongation at break | 18% | 4% | 120–300% |
While SLS parts offer strong tensile properties, they tend to be more brittle than injection-molded parts due to internal porosity.
Shrinkage & Warping
SLS parts typically shrink by 3 to 3.5% during cooling, which is accounted for during design and build preparation. Still, warping can occur—especially with large, flat surfaces. To help minimize distortion:
-
Orient flat features vertically
-
Reduce thickness in wide surfaces
-
Add ribs, fillets, or cutouts to relieve internal stress
These adjustments can also lower material usage and overall part cost.
Oversintering
Radiant heat from the laser can cause surrounding powder to fuse unintentionally, leading to a loss of detail in small features like holes or slots. As a general guideline:
-
Slots should be at least 0.8 mm wide
-
Holes should be ≥ 2 mm in diameter
Read our article on how to design parts for SLS 3D printing for more DFM tips.
Powder removal
ecause no support structures are needed, SLS can easily produce parts with internal cavities. Hollowing out parts can significantly reduce both weight and cost—but the leftover unsintered powder must be removed through escape holes.
We recommend including:
-
At least two escape holes
-
Minimum hole diameter of 5 mm
If a part needs extra stiffness, it can be left hollow without escape holes. The packed powder remains inside, adding weight and strength without extra build time. For an even better strength-to-weight ratio, a honeycomb lattice can be added internally, much like FDM infill patterns.

What are the characteristics of SLS 3D printing?
The main characteristics of SLA are summarized in the table below:
Selective Laser Sintering (SLS) | |
---|---|
Materials | Thermoplastics (usually nylon) |
Dimensional accuracy | ± 0.3% (lower limit of ± 0.3 mm) |
Typical build size | 300 x 300 x 300mm (up to 750 x 550 x 550mm) |
Common layer thickness | 100–120 µm |
Support | Not required |
What materials are used for SLS printing?
The most commonly used material for SLS 3D printing is Polyamide 12 (PA 12), also known as Nylon 12. This material is favored for its excellent balance of mechanical properties, cost-effectiveness, and ease of use. The typical price for PA 12 powder ranges between $50–$60 per kilogram.
Other materials, including Polyamide 11 (PA 11) and PEEK, are available, though they are less frequently used due to higher costs and more specialized applications.
Additives such as carbon fibers, glass fibers, and aluminum can be mixed into the polyamide powders to enhance specific properties like stiffness, thermal behavior, or wear resistance. However, materials filled with these additives tend to be more brittle and exhibit anisotropic mechanical properties, meaning their strength and flexibility vary depending on the direction of the print layers.
Material | Characteristics |
---|---|
Polyamide 12 (PA 12) | + Good mechanical properties + Good chemical resistance - Matte, rough surface |
Polyamide 11 (PA 11) | + Fully isotropic behavior + High elasticity |
Aluminium-filled nylon (Alumide) | + Metallic appearance + High stiffness |
Glass-filled nylon (PA-GF) | + High stiffness + High wear & temperature resistance - Anisotropic behavior |
Carbon-fiber filled nylon (PA-FR) | + Excellent stiffness + High weight-strength ratio - Highly anisotropic |
What are the options for SLS post-processing?
SLS 3D printed parts typically have a grainy, powdery surface that can be prone to staining. To enhance the appearance and functionality of these parts, various post-processing techniques can be employed. These methods can significantly improve the surface finish, durability, and aesthetic qualities of your parts:
-
Media polishing: Smoothens and refines the surface texture.
-
Dyeing: Adds color to the part, offering a variety of shades.
-
Spray painting & lacquering: Provides a glossy finish and additional protection.
-
Watertight coating: Seals the part for improved resistance to moisture.
-
Metal plating: Adds a metallic finish, improving strength and conductivity.
For more detailed insights, check out our extensive article on post-processing for SLS parts.
What are the advantages of SLS 3D printing
SLS is a highly versatile 3D printing technology with several key benefits:
-
Isotropic mechanical properties: SLS parts are robust and offer consistent mechanical performance, making them ideal for functional parts and prototypes.
-
No support structures: Unlike some other 3D printing methods, SLS doesn’t require support materials, allowing for complex geometries and intricate designs.
-
Efficient for small to medium batches: SLS is well-suited for low to medium production runs, offering cost-effective manufacturing without the need for molds.
-
Powder reusability: The unsintered powder leftover from the printing process can be collected and reused, reducing material waste and costs.
What are the disadvantages of SLA 3D printing?
While SLS offers many advantages, there are a few drawbacks to consider:
-
Longer lead times: Currently, industrial-grade SLS systems are the most widely available, which can result in longer lead times compared to other 3D printing technologies like FDM and SLA.
-
Grainy surface finish & porosity: SLS parts often have a rough, grainy surface and internal porosity, which may require post-processing if a smooth finish or waterproofing is needed.
-
Potential for warping & oversintering: Large, flat surfaces and small holes may not print as accurately due to warping or oversintering, which can lead to distorted features in the final part.
SLS best practices
Is SLS 3D printing the right choice for your part or project? Here are some key rules of thumb to help guide your decision:
-
Material Versatility: SLS can produce functional parts using a wide range of engineering plastics, with Nylon (PA12) being the most common material.
-
Typical Build Volume: Most SLS systems have a standard build volume of 300 x 300 x 300mm, which is suitable for medium-sized parts and small production runs.
-
Mechanical Properties: SLS parts exhibit strong mechanical properties and isotropic behavior, meaning they perform consistently in all directions. For components with special requirements (e.g., enhanced strength or thermal properties), additive-filled PA powders are available, such as carbon-fiber or glass-filled materials.
Get an instant quote
If you're ready to get your parts into production, you can head straight to the Protolabs Network platform to get an instant quote and explore our automatic DFM analysis. You can also reach out to networksales@protolabs.com for more information and get matched with a specialized account manager.
Frequently asked questions
What are the limitations of SLS 3D printing?
Some limitations include the grainy surface finish of SLS parts, potential for warping on large flat surfaces, and longer lead times compared to other 3D printing methods like FDM or SLA.
What is SLS 3D printing used for?
SLS is commonly used for creating functional prototypes, low-volume production parts, and parts with complex geometries that would be difficult or impossible to produce with traditional methods like injection molding.
Is SLS suitable for rapid prototyping?
Yes, SLS is ideal for rapid prototyping, as it allows for the creation of parts with complex geometries and functional properties, making it suitable for testing prototypes before mass production.