From copper's burnt-orange sheen to titanium's hard-edged reputation for endurance, these metals are as functional as they are distinct. Used in everything from electric vehicles and energy grids to aircraft, implants, and cutting-edge consumer tech, copper and titanium solve very different engineering problems. This guide compares them side by side so you can decide when to prioritize conductivity, corrosion resistance, strength, or cost.
What are the properties of titanium?
Titanium is a top pick for engineers who need a metal with high strength-to-weight ratio, excellent corrosion resistance, and ability to withstand extreme temperatures. It’s about 45% lighter than steel but maintains comparable strength. Titanium is also non-magnetic and biocompatible, making it useful in sensitive environments such as MRI-compatible medical devices or internal implants. It is most commonly used for CNC machining, but can also be processed with additive manufacturing techniques like Direct Metal Laser Sintering (DMLS) for complex or custom parts.
-
High strength-to-weight ratio
-
Excellent corrosion resistance
-
Biocompatibility
-
Low thermal and electrical conductivity
-
Moderate machinability
Titanium Grades
Titanium grades Titanium is available in various grades, typically categorized into commercially pure (CP) and alloyed forms. CP grades (1–4) vary mainly in strength and ductility, while alloyed grades like Grade 5 come with enhanced mechanical performance.
Grade | Description | Common applications |
---|---|---|
Grade 1 | Most ductile and corrosion-resistant, but lowest in strength | Chemical processing, marine systems |
Grade 2 | Balanced strength and ductility. | Marine, industrial, and aerospace components |
Grade 5 / Ti-6Al-4V | Alloyed grade with high strength and corrosion resistance | Aerospace, medical implants, high-performance parts |
What are the pros and cons of titanium?
Titanium offers impressive mechanical and environmental performance, but also brings some trade-offs. Here's a quick look at its advantages and limitations.
Titanium advantages
-
Exceptional strength-to-weight ratio
-
Excellent corrosion resistance
-
High fatigue resistance
-
Biocompatible for medical uses
Titanium disadvantages
-
Expensive material and processing costs
-
Challenging to machine
-
Lower thermal and electrical conductivity
Where is titanium used?
Titanium is widely used in sectors where reliable performance under pressure is critical—particularly when engineers need weight savings and resistance to harsh environments.
-
Aerospace: Used in structural components and engines for its strength-to-weight ratio and resistance to extreme conditions.
-
Medical: Chosen for implants and surgical tools thanks to its biocompatibility and corrosion resistance.
-
Automotive: Applied in exhausts and valves where heat resistance and low weight are top priorities.
-
Industrial machinery: Often used for chemical equipment due to its inertness and long-term durability.
-
Marine: Top pick in underwater components for its unmatched corrosion resistance in saltwater.
What are the properties of copper?
Copper is the go-to metal for conductivity, but it also brings excellent formability and natural antimicrobial properties. It's most commonly CNC machined due to its softness and precision, but can also be stamped or sheet metal fabricated into wiring, tubing, and intricate components for use in electronics, HVAC, and beyond.
Here's a closer look at what makes copper so versatile.
-
Excellent electrical and thermal conductivity
-
Good corrosion resistance
-
High ductility and malleability
-
Superior machinability
-
Antimicrobial properties
Copper Grades
Copper grades Copper is also available in different grades, generally classified by purity and intended use. The most common types in manufacturing are high-conductivity grades like C101 and C110, which vary slightly in application.
Grade | Description | Common applications | Offered at PLN |
---|---|---|---|
C101 | Oxygen-free, highest conductivity and purity | High-end electronics, vacuum tubes, semiconductor | ✅ |
C110 | Electrolytic tough pitch copper, high conductivity and ductility | Wiring, busbars, heat sinks, plumbing | ✅ |
C145 | Tellurium copper, excellent machinability but reduced conductivity | Machined electrical parts, connectors | ❌ |
C194 | High-strength alloyed copper with good conductivity | Automotive terminals, power connectors | ❌ |
C260 | Brass (copper-zinc alloy) with good strength and corrosion resistance | Decorative, hardware components | ❌ |
What are the pros and cons of copper?
Copper is easy to work with and great for thermal or electrical applications—but it's not the strongest metal around. Here are its main benefits and drawbacks.
Copper advantages
-
Superior thermal and electrical conductivity
-
Easy to machine and form
-
Naturally antimicrobial
-
Cost-effective compared to titanium
Copper disadvantages
-
Lower strength and stiffness
-
Less effective in extreme environments
-
Susceptible to surface oxidation without finishing
Where is copper used?
Copper stands out in applications where conductivity, machinability, and corrosion resistance are critical. Unlike metals like titanium or stainless steel, copper excels in environments where electrical or thermal performance is more important than mechanical strength.
-
Electronics: Used in wiring and motors for its unmatched electrical conductivity and easy formability.
-
HVAC: Chosen for heat exchangers and radiators thanks to its excellent thermal transfer and corrosion resistance.
-
Construction: Ideal for plumbing and cladding due to its corrosion resistance and long-term durability.
-
Medical: Frequently used on high-contact surfaces for its natural antimicrobial properties.
-
Automotive: Common in wiring harnesses where flexibility and conductivity are key.
Industry comparison: copper vs. titanium
While copper and titanium have standout characteristics, material choice ultimately depends on the demands of a specific part. The table below highlights common applications by sector, along with guidance on when one metal tends to offer the best performance.
Industry | Application | Best material | Why it’s a fit |
---|---|---|---|
Aerospace | Airframes, turbines, fasteners | Titanium | High strength-to-weight ratio, heat and corrosion resistance |
Medical | Implants, surgical tools | Titanium / copper | Titanium is biocompatible; copper is antimicrobial (used externally only) |
Electronics | Wiring, PCBs, motors | Copper | Excellent conductivity and ease of forming |
HVAC | Heat exchangers, radiators | Copper | Superior thermal conductivity |
Marine | Underwater fasteners, piping | Titanium | Outstanding corrosion resistance |
Automotive | Exhausts, wiring harnesses | Titanium / copper | Lightweight strength or conductivity needs |
Construction | Plumbing, cladding | Copper | Durable, corrosion-resistant, aesthetic |
Titanium and copper in the real-world These companies chose copper or titanium to solve specific challenges in weight, conductivity, and durability.
-
Helix Bikes, a folding bike startup, used Protolabs to CNC machine lightweight, ultra-durable titanium frame components that could withstand daily wear and tear without adding unnecessary bulk—similar to aerospace-level performance requirements.
-
Quantum Machines developed high-precision copper components via CNC machining to support advanced quantum computing systems, leveraging copper’s excellent thermal and electrical conductivity for delicate internal assemblies.
-
Supernode, an energy infrastructure company, used custom-machined copper parts to create highly efficient
thermal management systems for large-scale power distribution, maximizing conductivity while ensuring long-term durability.
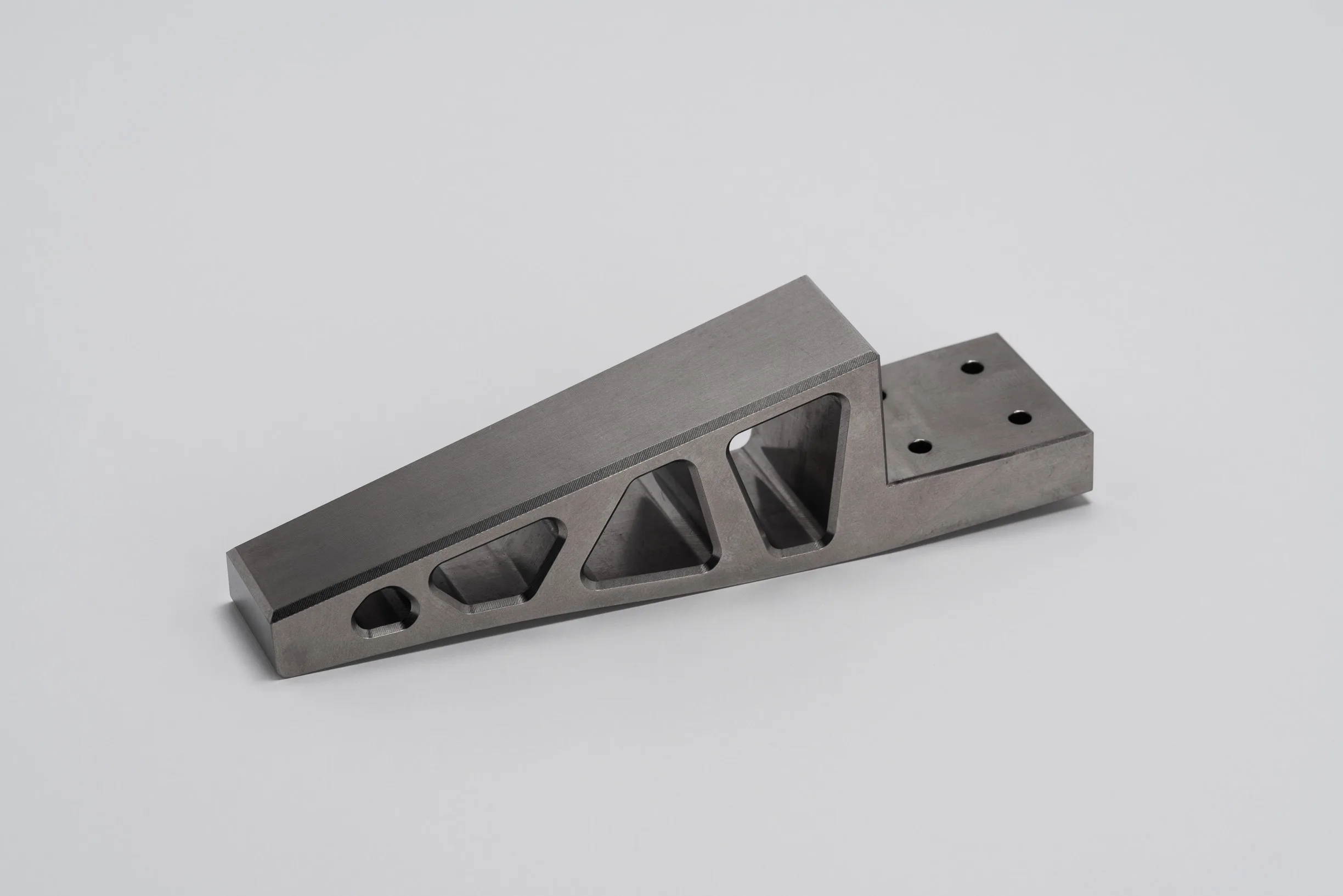
When should you use copper vs. titanium in manufacturing?
Copper and titanium both deliver serious performance—but in very different ways. Copper leads when electrical or thermal efficiency is a priority. It’s great for wiring, heat exchangers, and parts that need fast, reliable machining.
Titanium stands out when a part needs to be both strong and lightweight, especially in harsh or regulated environments. It's more expensive and harder to machine, but essential when durability, corrosion resistance, and biocompatibility can’t be compromised.
When in the prototyping stage, copper’s ease of machining makes it a practical choice for fast iterations, while titanium is often reserved for later-stage parts or production orders where strength or corrosion resistance is essential.
If you're trying to decide which is the better fit for your part, it often comes down to your priorities: strength vs. conductivity, weight vs. machinability, or even resistance vs. cost. Not sure which metal to choose? Here’s a quick guide:
-
Need lightweight strength and corrosion resistance in harsh conditions? → Choose titanium
-
Need excellent electrical or thermal conductivity? → Choose copper
-
Need to machine small, precise parts easily? → Choose copper
-
Need strong, biocompatible material for medical or aerospace applications? → Choose titanium
Upload your CAD file now for instant pricing and design feedback.
Get an instant quoteAlternative material options
If copper or titanium aren’t quite the right fit—whether due to performance limitations, cost, or ease of fabrication—there are several materials that can offer similar benefits. Here’s a quick breakdown by use case:
Substitutes for copper
-
Brass: Easier machinability, decent conductivity
-
Aluminum: Lightweight and cost-effective
-
Phosphor bronze: Durable and often used for springs/connectors
Substitutes for titanium
-
Stainless steel: Strong and corrosion-resistant
-
Inconel: Withstands extreme environments
-
Aluminum 7075: Lightweight with moderate strength (compare to titanium)
Metal properties comparison
If you are still weighing which properties matter most for your application, this chart can help you compare metals based on key performance factors.
Material | Strength:weight | Conductivity | Corrosion resistance | Machinability | Cost |
---|---|---|---|---|---|
Titanium | Excellent | Low | Excellent | Poor to Moderate | High |
Copper | Poor | Very high | Good | Excellent | Moderate |
Aluminum | Good | High | Good | Excellent | Low |
Brass | Moderate | Good | Good | Excellent | Moderate |
Stainless steel | Good | Low | Excellent | Moderate | Moderate |
Inconel | Excellent | Low | Excellent | Poor | Very High |
Material considerations for manufacturability
To select the right material, it is helpful to understand how the different options behave during manufacturing. Here's what engineers should consider when working with copper and titanium:
1, Machining behavior
Copper is highly machinable and produces clean, burr-free cuts. Its softness, however, means copper can stick to cutting tools at high speeds—causing tool wear over time.
Titanium is notoriously challenging to machine. It requires slower speeds, aggressive cooling, and sharp tools—otherwise it can harden as you cut and wear down your equipment.
2, Welding and joining
Copper can be welded, but its high thermal conductivity makes the process difficult, so soldering or brazing is usually preferred.
Titanium can be welded too, but it has to be done in an inert atmosphere (argon or helium), often with glove boxes or trailing shields.
3, Formability
Copper is soft and flexible, so it’s easy to bend, stretch, or shape into wires and sheets without cracking.
Titanium is trickier—it’s brittle at room temperature, so it usually needs to be heated before shaping.
4, Surface finishing
Copper is usually left bare or plated (e.g., with nickel, tin, or black oxide) to enhance corrosion resistance or electrical contact. It can also develop a protective patina.
Titanium can be anodized for color-coding or additional corrosion resistance, or bead blasted for surface texture in aerospace or medical applications.
Frequently asked questions
Is titanium stronger than copper?
Yes—titanium has a significantly higher strength-to-weight ratio.
Which is more conductive?
Copper has far better electrical and thermal conductivity.
Can copper be used instead of titanium?
Only if the application requires conductivity over strength, weight, corrosion resistance, or durability. Copper is not a structural replacement for titanium in most load-bearing or harsh-environment applications.
Is titanium harder to machine than copper?
Yes—titanium work hardens quickly and requires slower cutting speeds and specialized tooling.