3D printing is an additive technology used to manufacture parts. It is ‘additive’ in that it doesn’t require a block of material or a mold to manufacture physical objects, it simply stacks and fuses layers of material. It’s typically fast, with low fixed setup costs, and can create more complex geometries than ‘traditional’ technologies, with an ever-expanding list of materials. It is used extensively in the engineering industry, particularly for prototyping and creating lightweight geometries.

See chapters
See chapters
Select chapter
What is 3D printing?
3D printing and additive manufacturing
‘3D printing’ is commonly associated with maker culture, hobbyists and amateurs, desktop printers, accessible printing technologies like FDM and low-cost materials such as ABS and PLA (we’ll explain all those acronyms below). This is largely attributable to the democratization of 3D printing through affordable desktop machines that sprung from the RepRap movement, like the original MakerBot and Ultimaker, which also led to the explosion of 3D printing in 2009.
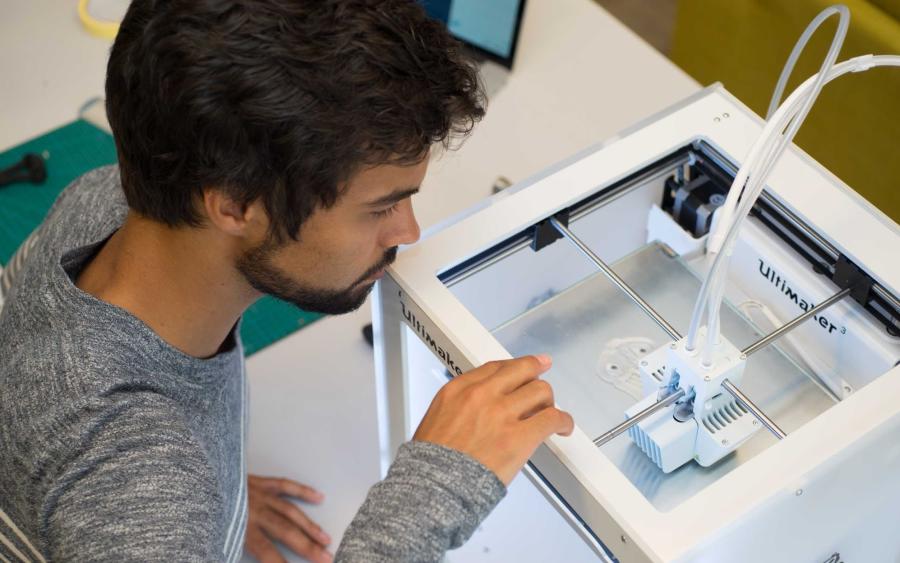
By contrast, additive manufacturing (AM) is almost always associated with commercial and industrial applications.
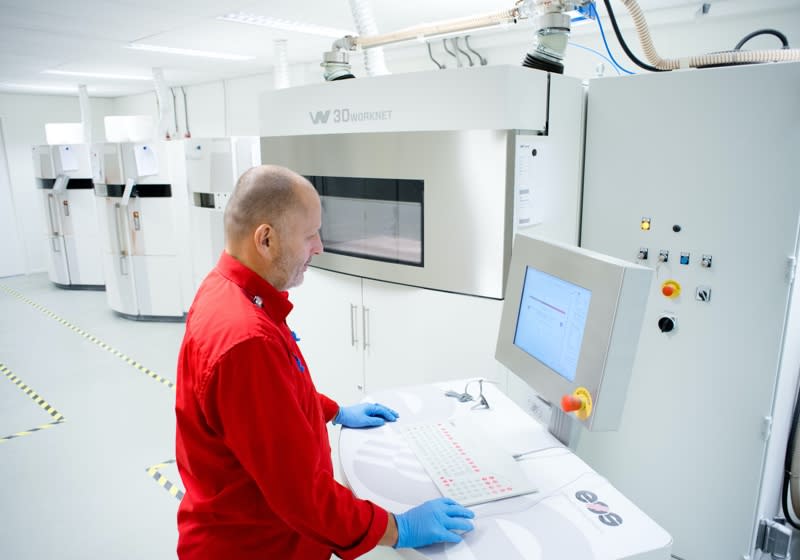
3D printing and rapid prototyping
‘Rapid prototyping’ is another phrase that’s sometimes used to refer to 3D printing technologies. This dates back to the early history of 3D printing when the technology first emerged. In the 1980s, when 3D printing techniques were first invented, they were referred to as rapid prototyping technologies because back then the technology was only suitable for prototypes, not production parts.
In recent years, 3D printing has matured into an excellent solution for many kinds of production parts, and other manufacturing technologies (like CNC machining) have become cheaper and more accessible for prototyping. So while some people still use ‘rapid prototyping’ to refer to 3D printing, the phrase is evolving to refer to all forms of very fast prototyping.
When was 3D printing invented?
3D printing began as an idea for accelerating industrial product development through faster prototyping. Even though there were a few patents beforehand, Chuck Hull is typically credited with the invention of the 3D printer via his Stereolithography Apparatus (SLA), patented in 1984.
Foundations
Despite Chuck’s fame, multiple technologies were being developed in parallel in the late 1980s, and there were several companies founded in this period that was critical to the development of the technology.
- 1981 - the first patent for a device using UV light to cure photopolymers was awarded to Hideo Kodama in Japan. He designed it for ‘rapid prototyping’ as it was intended for making models and prototypes, but there was no interest and the patent was abandoned.
- 1984 - French inventors Alain Le Mehaute, Olivier de Witte, and Jean Claude André submitted a patent in which, like Hideo’s, UV light was used to cure photopolymers. General Electric abandoned the patent citing a lack of significant business potential.
- 1984 - only a few weeks after Le Mehaute, American Charles ‘Chuck’ Hull filed his own patent for an ‘Apparatus for Production of Three-Dimensional Objects by Stereolithography’, thus also coining the term ‘stereolithography’ (SLA).
- 1987 - Hull invented the STL file, and in the same year founded 3D Systems.
- 1987 - American Carl Deckard filed a patent for Selective Laser Sintering (SLS), and in the same year co-founded Desktop Manufacturing (DTM) Corp. (acquired by 3D Systems in 2001).
- 1989 - American S. Scott Crump submits a patent for Fused Deposition Modeling (FDM), and in the same year founded Stratasys with his wife.
Commercialization
From the late 1980s to the early 1990s the industry underwent very rapid commercialization. The first machines were big and expensive and their makers competed for industrial prototyping contracts with mass-market manufacturers in the automotive, aerospace, health, and consumer goods industries.
- 1987 - 3D Systems released the first commercial SLA printer, the ‘SLA-1’.
- 1992 - The FDM patent was finally granted to Stratasys, which led them to release the first FDM printer, the ‘3D Modeler’.
- 1992 - DTM released the first commercial SLS printer, the ‘Sinterstation 2000’
- 1994 - German company Electro Optical Systems (EOS), founded in 1989, unveiled its ‘EOSINT M160’, the first commercial metal 3D printer
Democratization
In the early 2000s the fierce competition for profits, developments in material science, and the ending of many patents created an environment in which 3D printing finally became affordable for the masses. This was the decade that 3D printing took off in the popular imagination - manufacturing, which had always been the domain of heavy industry and big money, came to the people.
- 2005 - The open-source RepRap Project (for ‘Replicated Rapid Prototyper’) launched with the aim of creating self-replicating 3D printers capable of printing their own parts, causing popular interest in the technology to skyrocket.
- 2009 - Key FDM patents fell into the public domain and MakerBot launched their desktop 3D printer, the ‘Cupcake CNC’. It cost hundreds of dollars, not thousands, and all components were downloadable from Thingiverse, a website dedicated to the sharing of user-created digital design files.
- 2012 - Formlabs release the ‘Form 1’, the first affordable SLA printer, through a record-breaking Kickstarter campaign that raised $2.95 million in funding.
- 2013 - Protolabs Network launches as a peer-to-peer 3D printing service, allowing mass transactions between people buying prints and people with machines. It quickly grew to be the single biggest 3D printing platform in the world with over 50,000 printing ‘hubs’, before pivoting to focus on helping its business customers by making all forms of custom manufacturing more accessible.
- 2014 - Key SLS patents fell into the public domain, leading to a whole crop of companies making smaller and more affordable SLS printers.
Maturity
From 2018 the hype around 3D printing had largely disappeared from mass media, but interest in commercial applications for businesses of all sizes has never been higher. Today there are thousands of companies producing printers and offering all sorts of services leveraging 3D printing technology.
Learn more about the history of 3D printing
There are many articles out there, most are just fun reads. For those looking to really delve deep into history, Wikipedia and Wohler Associates are the best resources.
How does 3D printing work?
Additive vs traditional manufacturing
Additive manufacturing has only been around since the 1980s, so the manufacturing methods developed before it are often referred to as traditional manufacturing. To understand the major differences between additive and traditional manufacturing, let’s categorize all methods into 3 groups: additive, subtractive and formative manufacturing.
Additive manufacturing
Additive manufacturing builds up 3D objects by depositing and fusing 2D layers of material.
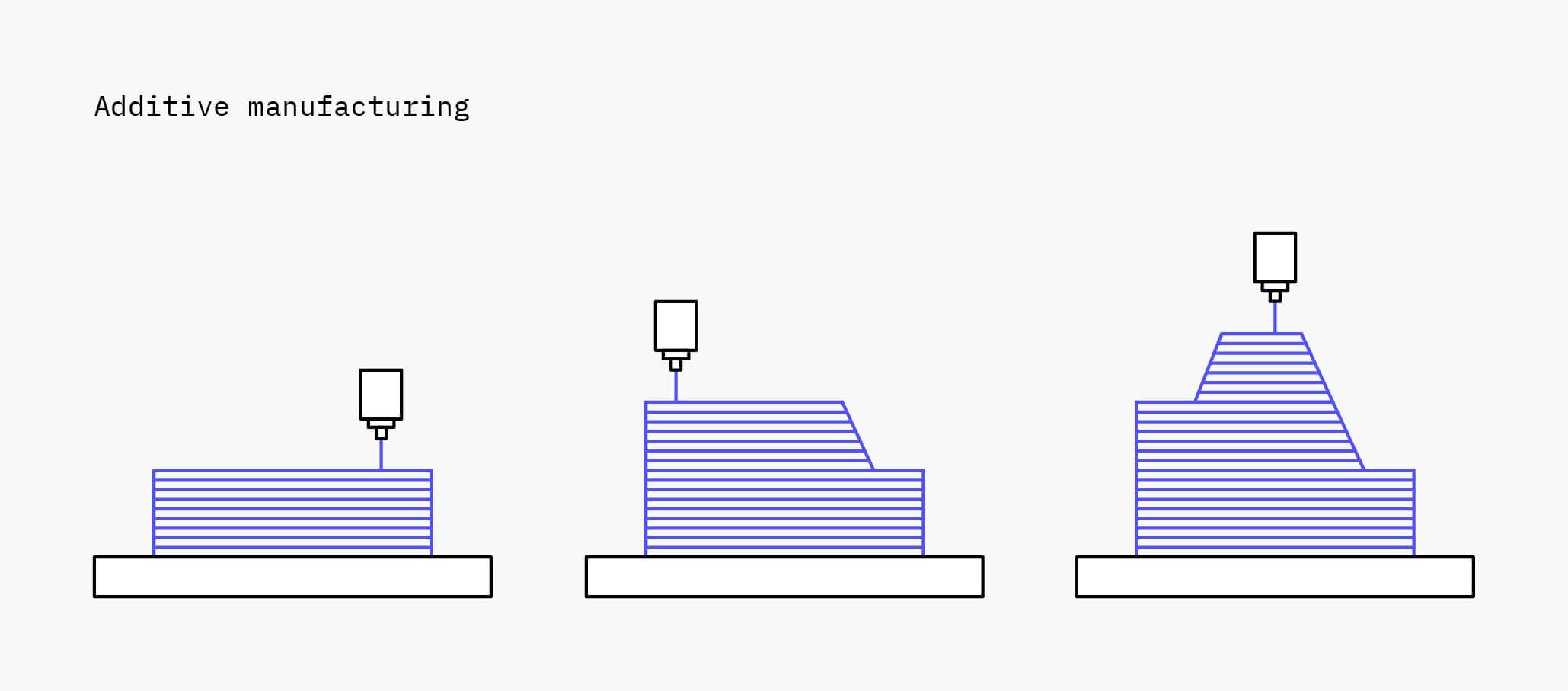
This method has almost no startup time or costs, making it ideal for prototyping. Parts can be made rapidly and discarded after use. Parts can also be produced in almost any geometry, which is one of the core strengths of 3D printing.
One of the biggest limitations of 3D printing is that most parts are inherently anisotropic or not fully dense, meaning they usually lack the material and mechanical properties of parts made via subtractive or formative techniques. Due to fluctuations in cooling or curing conditions, different prints of the same part are also prone to slight variations, which puts limitations on consistency and repeatability.
Subtractive manufacturing
Subtractive manufacturing, such as milling and turning, creates objects by removing (machining) material from a block of solid material that’s also often referred to as a ‘blank’.
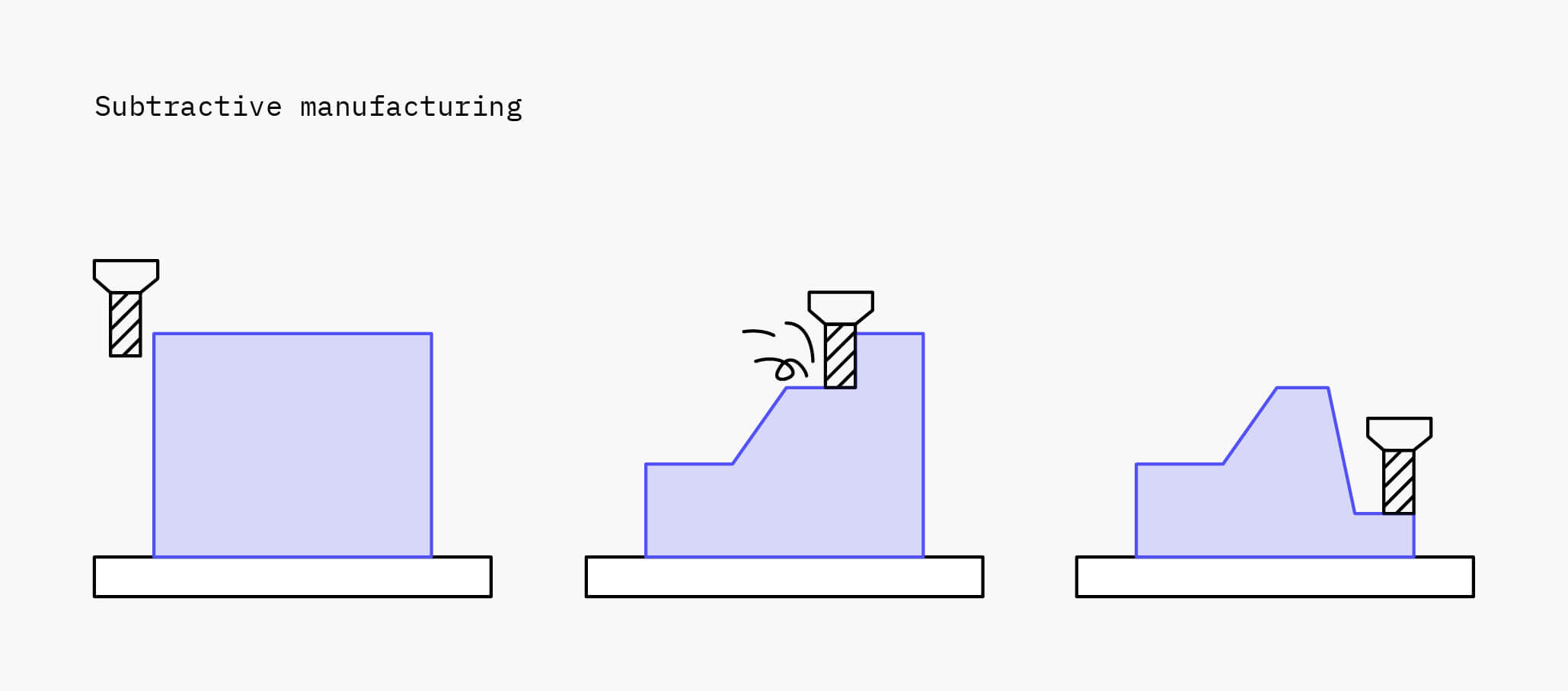
Almost any material can be machined in some way, making it a widely used technique. Because of the amount of control over every aspect of the process this method is capable of producing incredibly accurate parts with high repeatability. Most designs require Computer Aided Manufacturing (CAM) to plot customized tool paths and efficient material removal, which adds setup time and costs, but for the majority of designs, it’s the most cost-effective method of production.
The major limitation of subtractive manufacturing is that the cutting tool must be able to reach all surfaces to remove material, which limits design complexity quite a lot. While machines like 5-axis machines eliminate some of these restrictions, complex parts still need to be re-orientated during the machining process, adding time and cost. Subtractive manufacturing is also a wasteful process due to the large amounts of material removed to produce the final part geometry.
Formative manufacturing
Formative manufacturing, such as injection molding and stamping, creates objects by forming or molding materials into shape with heat and/or pressure.
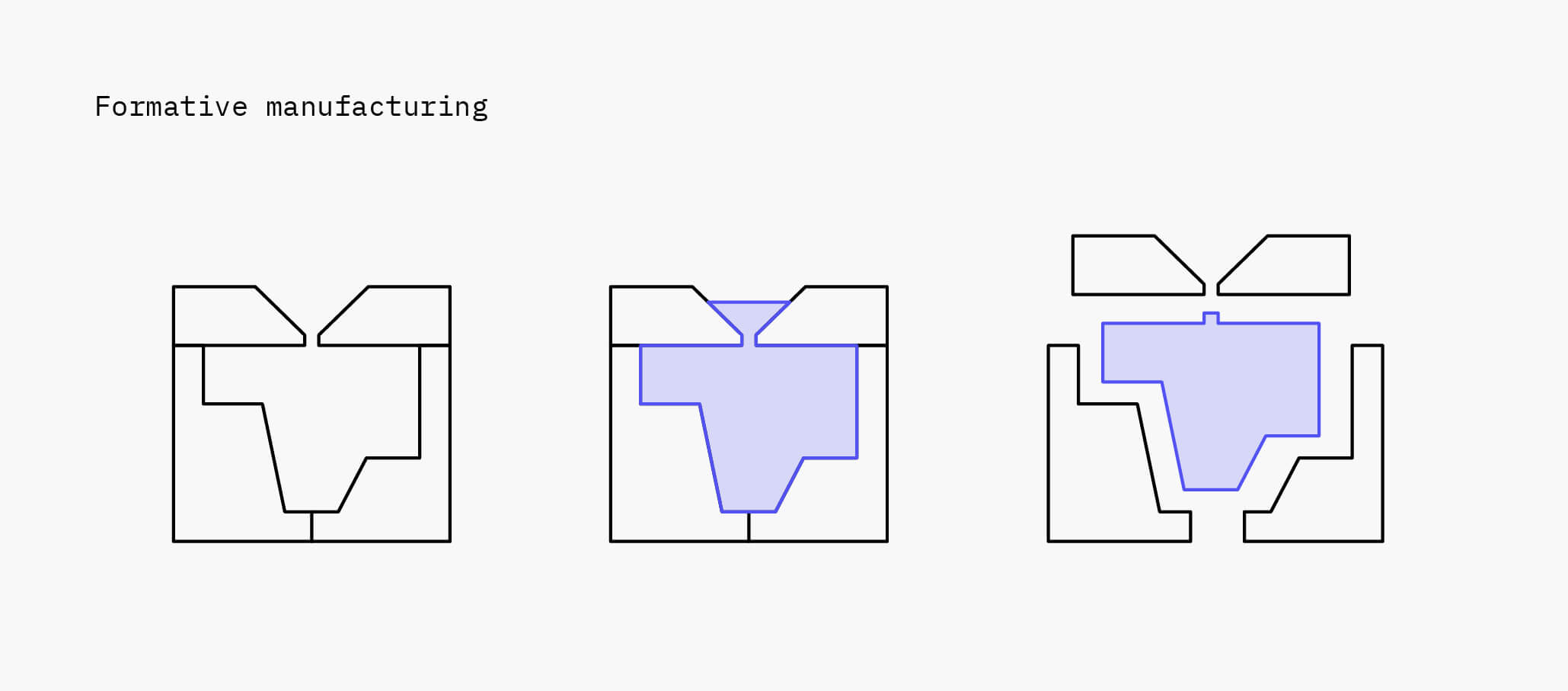
Formative techniques are designed to reduce the marginal cost of producing individual parts, but the creation of unique molds or machines used in the production process means setup costs are very, very high. Regardless, these techniques can produce parts in a large range of materials (both metals and plastics) with close to flawless repeatability, so for high volume production order, they’re almost always the most cost-efficient.
How these methods compare
Manufacturing is complex, and there are too many dimensions for comprehensively comparing each method against all others. It is near impossible to optimize all at once for cost, speed, geometric complexity, materials, mechanical properties, surface finish, tolerances, and repeatability.
In such complex situations heuristics and rules of thumb are more valuable:
- Additive manufacturing is best for low volumes, complex designs, and when speed is essential.
- Subtractive manufacturing is best for medium volumes, simple geometries, tight tolerances, and hard materials
- Formative manufacturing is best for the high-volume production of identical parts.
Cost per part is usually the governing factor determining which manufacturing process is best. As a rough approximation the unit costs per method can be visualized like this:
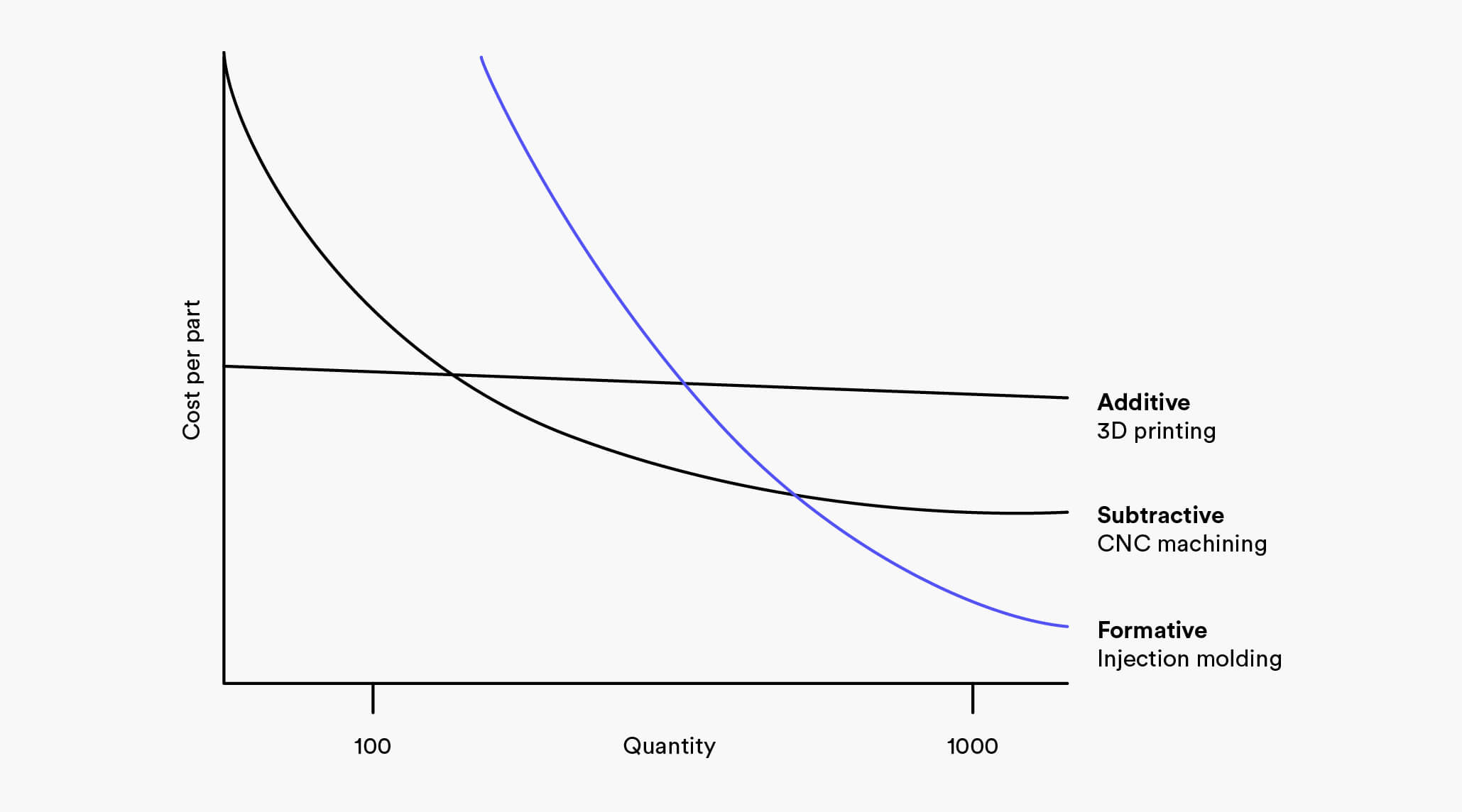
Learn more about 3D printing vs CNC machining.
3D printing is becoming cheaper every year and in some instances, it is starting to compete with injection molding for cost efficiency. However it’s usually 3D printing and CNC machining that are considered interchangeable for particular jobs, so we’ve written a thorough guide comparing them side by side. Read more about 3D printing vs CNC machining.
3D printing technology
With so many different 3D printing technologies on the market, it can be hard to understand the whole landscape. The International Organization for Standardization created the ISO/ASTM standard 52900 to standardize the exploding terminology around 3D printing and we’ve pulled together the most-used language into this glossary of 3D printing terms.
The different types of 3D printing
3D printers can be categorized into one of several types of processes:
- Vat Polymerization: liquid photopolymer is cured by light
- Material Extrusion: molten thermoplastic is deposited through a heated nozzle
- Powder Bed Fusion: powder particles are fused by a high-energy source
- Material Jetting: droplets of liquid photosensitive fusing agent are deposited on a powder bed and cured by light
- Binder Jetting: droplets of liquid binding agent are deposited on a bed of granulated materials, which are later sintered together
- Direct Energy Deposition: molten metal simultaneously deposited and fused
- Sheet Lamination: individual sheets of material are cut to shape and laminated together
3D printing processes
There are seven main 3D printing processes. Within each type of process there are unique technologies, and for every unique technology there are also many different brands selling similar printers.
Vat photopolymerization
Photopolymerization is the process of a photopolymer resin being exposed to certain wavelengths of light and becoming solid.
Stereolithography (SLA), direct light processing (DLP) and continuous direct light processing (CDLP) are additive manufacturing processes that fall under the category of vat photopolymerization. In SLA, an object is created by selectively curing a polymer resin layer-by-layer using an ultraviolet (UV) laser beam. DLP is similar to SLA but uses a digital light projector screen to flash a single image of each layer all at once. CDLP is a lot like DLP but relies on the continuous upward motion of the build plate. All vat photopolymerization processes are good for producing fine details and smooth surface finishes, making them ideal for jewelry and medical applications.
Benefits
- Smooth surface
- Fine details
- Good for prototyping of IM
Limitations
- Brittle
- Usually requires supports
- UV sensitive
- Extensive post processing required
Powder bed fusion
Powder bed fusion (PBF) technologies use a heat source to induce fusion (sintering or melting) between the particles of a plastic or metal powder one layer at a time. SLS printing service, electron beam melting (EBM) and multi jet fusion (MJF) all fall within this technology. The metal 3D printing processes selective laser melting (SLM) and direct metal laser sintering (DMLS) also use powder bed fusion to selectively bind metal powder particles.
Benefits
- Strong parts (nylon)
- Complex geometry
- Scalable (fits size)
- No support
Limitations
- Longer production time
- Higher cost (machines, material, operation)
Material extrusion
Material extrusion technologies squeeze a material through a nozzle and onto a build plate, layer by layer. Fused deposition modeling (FDM) falls under this category and is the most widely used 3D printing technology.
Benefits
- Fast
- Low cost
- Common thermoplastics
Limitations
- Rough surface finish
- Anisotropic
- Usually requires supports
- Not scalable
- Limited accuracy
Material jetting
Material jetting technologies use UV light or heat to harden photopolymers, metals or wax, building parts one layer at a time. Nano particle jetting (NPJ) and Drop-on-demand (DOD) are two other types of material jetting.
Benefits
- Realistic prototypes
- Excellent details
- High accuracy
- Smooth surface finish
Limitations
- High cost
- Brittle mechanical properties
Binder Jetting
Binder jetting uses an industrial printhead to deposit a binding adhesive agent onto thin layers of powder material. Unlike the other 3D printing technologies, binder jetting does not require heat.
Benefits
- Full-color options
- Range of materials
- No support
- No warping or shrinking
Limitations
- Low part strength
- Less accurate than material jetting
Direct energy deposition
Direct energy deposition (DED) creates 3D objects by melting powder material as it is deposited. It is mostly used with metal powders or wire and is often referred to as metal deposition. Laser engineered net shape (LENS) and Electron Beam Additive Manufacture (EBAM) also fall within this category.
Benefits
- Strong parts
- Range of materials
- Larger parts
Limitations
- High cost
- Poor surface finish
Sheet lamination
This technology stacks and laminates thin sheets of material to make parts. There are a few different types of lamination to choose from: bonding, ultrasonic welding or brazing.
Benefits
- Fast
- Low cost
- No support structures necessary
- Multi-material layers
Limitations
- Post processing is required
- Limited materials
- Finishing may vary
The whole landscape of additive manufacturing technologies can be summarized in a simple tree-diagram:
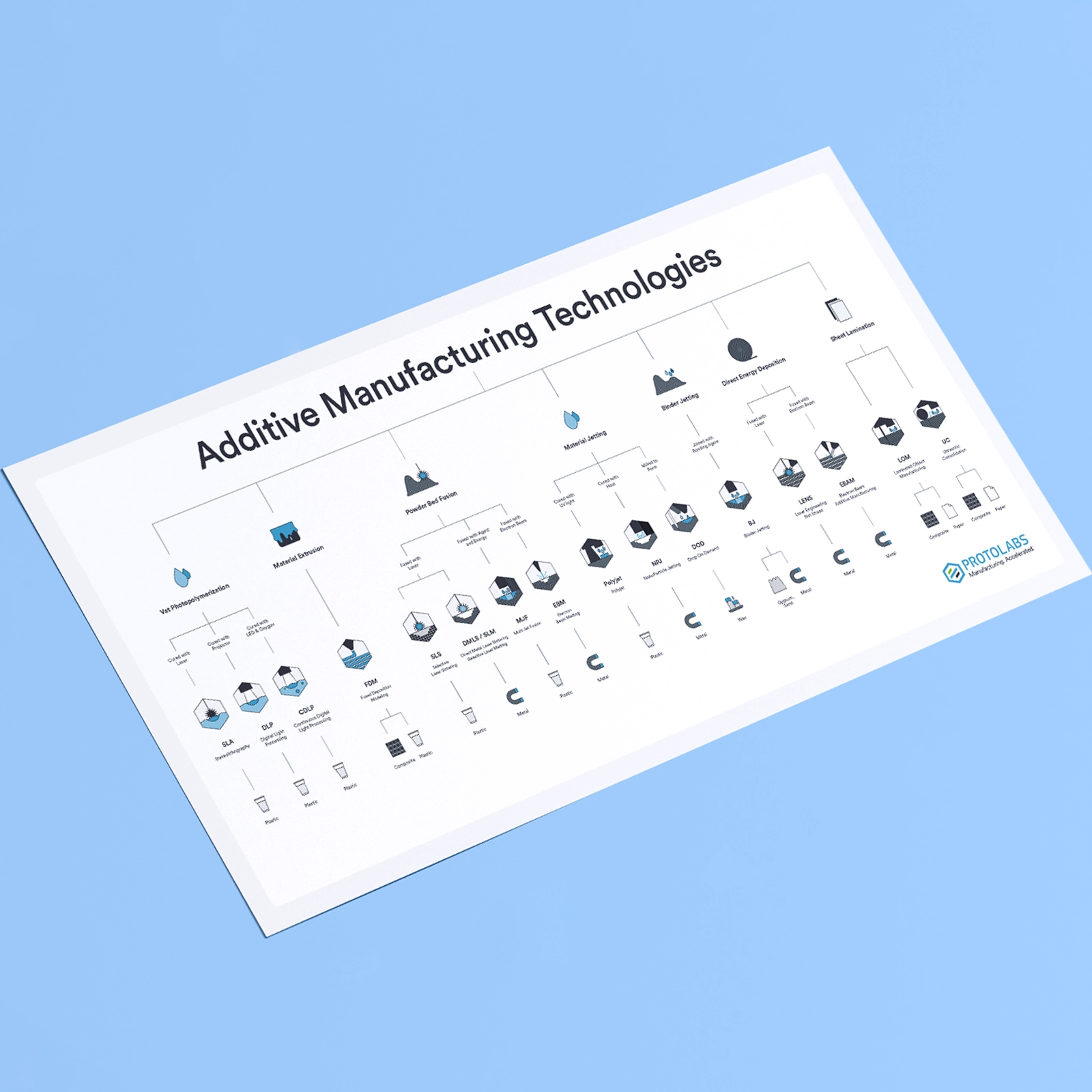
Click here to download a high-resolution version of this poster.
Our article on The Seven Official Types Of 3D Printers gives a broad overview of how each type of printer works, the materials available, the price and speed of printing, geometric properties (size, complexity & resolution), mechanical properties (accuracy, strength & surface finish) and common applications.
Looking for more in-depth information on the topic? We also wrote a handbook on 3D printing. If you’re a professional looking to truly master the key aspects of 3D printing, this book is for you.
Selecting the right 3D printing processes
Selecting the optimal 3D printing process for a particular part can be difficult as there’s often more than one suitable process but each one will produce subtle variations in cost and output. Generally there are three key aspects to consider:
- The required material properties: strength, hardness, impact strength, etc.
- The functional & visual design requirements: smooth surface, strength, heat resistance, etc.
- The capabilities of the 3D printing process: accuracy, build size, etc.
These correspond to the three most common methods for selecting the right process:
- By required material
- By required functionality or visual appearance
- By required accuracy or build size
For an in-depth look at how to use these methods read our complete guide to Selecting the right 3D printing process. The following comparison guides will also help inform your decision.
- HP MJF vs. SLS: A 3D printing technology comparison
- Industrial SLA/DLP vs. desktop SLA/DLP
- Industrial FDM vs. desktop FDM
3D printing materials
A complete 3D printing material overview
The number of available 3D printing materials grows rapidly every year as market demand for specific material and mechanical properties spurs advancements in material science. This makes it impossible to give a complete overview of all 3D printing materials, but each 3D printing process is only compatible with certain materials so there are some easy generalizations to make.
Thermoplastic and thermoset polymers are by far the most common 3D printing materials, but metals, composites and ceramics can also be 3D printed.
Another way of categorizing materials is by their properties: cheap, chemically resistant, dissolvable, flexible, durable, heat resistant, rigid, water resistant, UV resistant. Many industrial applications require durable plastics such as Nylon 12, and most hobbyist applications use either PLA or ABS, which are the most common materials used in FDM 3D printing.
For a more thorough overview of each of the main 3D printing materials see these articles.
- FDM 3D printing materials compared
- PLA vs. ABS: What’s the difference?
- SLA 3D printing materials compared
- 3D printed injection molds: Materials compared
Post processing 3D prints
Smooth layer lines and improve perfomance
There are a variety of post-processing options for finished 3D prints. The post-processing technique you choose will depend on the desired effect for your part.
For example, you can polish parts created with resin 3D printing, so you can achieve a glossy or reflective finish. Certain materials can also be vapor smoothed – which involves exposing a print to a chemical vapor so that its top layer melts into a smooth, glossy surface.
By sanding your part, you can remove layer lines and rough surfaces to achieve a smoother finish. Priming and painting is also a common method of post-processing a finished 3D print, should you need your part to be a certain color for aesthetics or safety purposes.
You can also polish parts created with resin 3D printing, so you can achieve a glossy or reflective finish. Certain materials can also be chemically smoothed, which involves exposing a print to a chemical vapor so that its top layer melts into a smooth, glossy surface.
You can also use several post-processing techniques, such as heat treatment and electroplating, to improve a part’s mechanical properties. However, the possibility of using a post-processing technique like electroplating will depend on the material you’ve chosen to use, so be sure to consult with your manufacturing provider.
If your 3D printed part was designed for a functional application, you might need to consider adding metal inserts for reinforcements or creating threads for screws so you can more easily assemble or attach your part to other parts.
3D printing software
3D printing starts with software and there are many different programs to aid with each stage of the design and printing process, from 3D modelling, to print simulations and slicer programs.
What software should you use for 3D printing?
The two main methods of 3D modelling are ‘solid modelling’ and ‘surface modelling’, and there are different CAD software packages for each approach. Solid modelling refers to the creation of virtual objects through defining and joining 3D shapes that are usually predefined and to which refined surface details are added later. Surface modelling is similar except the designer starts with 2D surfaces and shapes them in ‘freeform’ to create 3D shapes.
Both approaches can produce exactly the same output, but solid modelling is faster for simple and non-organic shapes, whereas surface modelling is faster for more organic shapes. SolidWorks, Fusion 360 and Rhino 3D are the most popular software with professionals, and there are many free programs for amateurs.
Other useful 3D printing software include print simulation tools and file error fixers.
3D printing design guidelines
The exact best practices and rules of thumb vary between the different 3D printing technologies, but there are certain features you always need to pay attention to:
- Supported wall thickness
- Unsupported wall thickness
- Supports and overhangs
- Embossed and engraved details
- Horizontal bridges
- Holes
- Connecting or moving parts
- Escape holes
- Minimum feature size
- Minimum pin diameter
- Maximum tolerance
The process-specific design rules for each of these features are summarized in the graphic below:
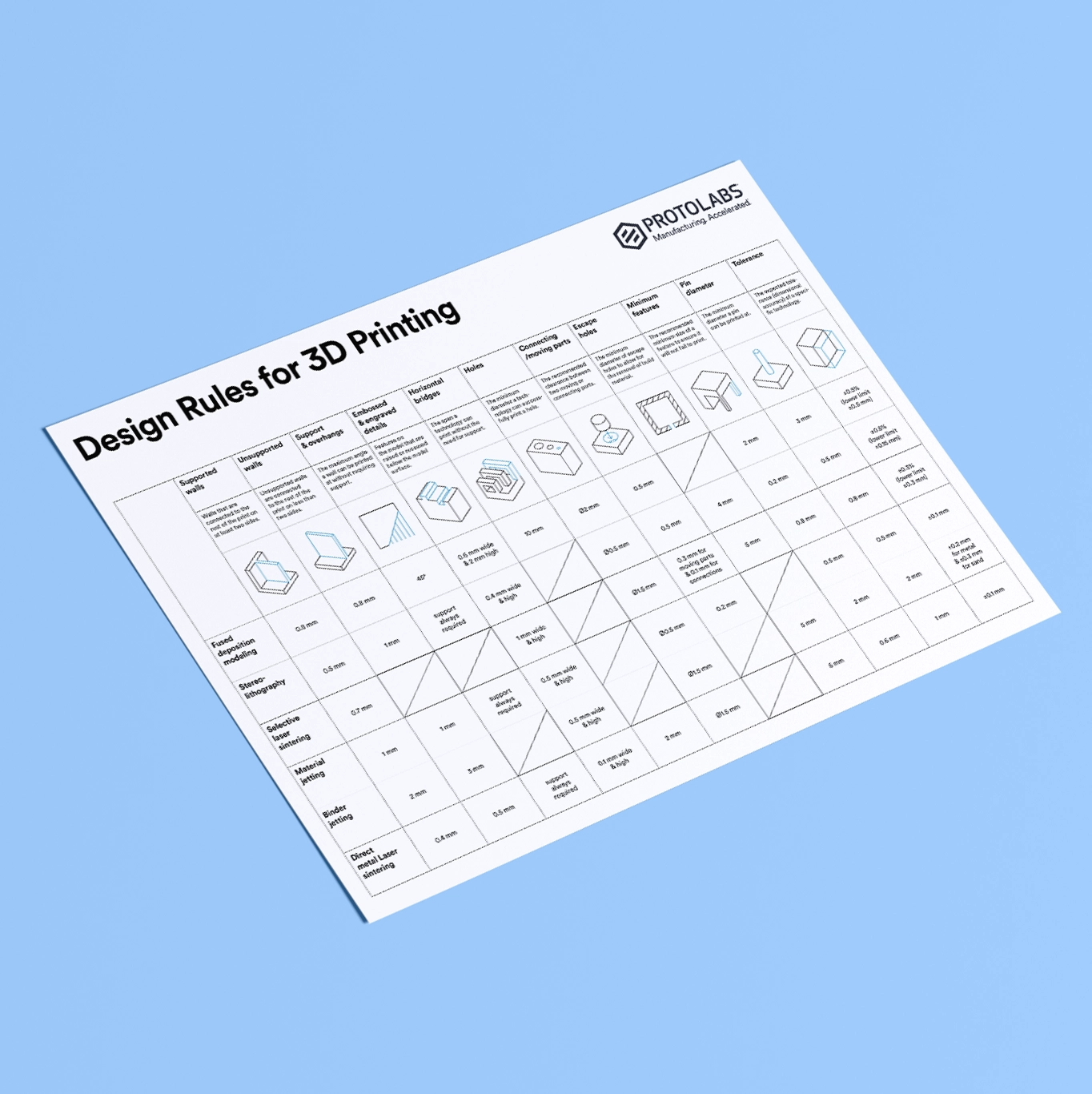
Click here to download a high-resolution version of this poster.
Design guidelines applicable for all 3D printing processes
Design guidelines for specific processes
Design guidelines for specific parts
Health and safety
Precautions to take when 3D printing
3D printing is generally a safe manufacturing method, but there are several precautions our manufacturers take to ensure their – and your – health and safety.
Some 3D printing materials, for example, can emit harmful particles or fumes while printing. That’s why our manufacturers always place and use their 3D printers in areas that are properly ventilated, as well as make use of exhaust fans, fume hoods, or enclosures. Personal protective equipment (PPE) can also help decrease exposure to harmful emissions from hazardous materials.
The high temperatures that 3D printers reach, as well as the exposed moving parts they have, can pose fire risks or cause injury not safely handled or regularly maintained. Our manufacturers train their employees to do this.
The noise 3D printers create may also cause issues, depending on the type – and number – of 3D printers being used. Our manufacturers use hearing protection to avoid such issues, especially if their 3D printers are contained in a small, indoor space.
Legal and ethical considerations
Regulations that might affect your project
Many of the legal and ethical considerations for 3D printing align rather closely with those for other, more traditional forms of manufacturing.
For example, you must respect intellectual property (IP) rights of a design or part by having the right license to use it. This means you should not reproduce a copyrighted part without permission from the original creator.
If you create or sell 3D printed parts, you are usually responsible for those parts’ safety and quality. This means you may be held liable should they not meet the safety or quality standards for certain industries or use cases.
Ethical considerations of 3D printing predominantly center around the environment and sustainability.
You can also consider using biodegradable materials when possible, which can help you reduce waste and operate more sustainably – and potentially help you reduce costs along the way.
Applications of 3D printing
3D printing is exceptionally useful for prototyping. Speed is everything in prototyping, and the ability to move from CAD to print with close to zero set up costs means 3D printers can produce parts fast and have great unit economics for single-part and small runs.
For printing production parts, speed and price are also important, but the characteristics most commonly exploited are design freedom and ease of customization. In aerospace and automotive, topology optimized structures with a high strength-to-weight ratio are used for high-performance parts, and components that previously required assembly can be consolidated into a single part. In healthcare, customization is critical - most hearing aids manufactured in the US are made almost exclusively using 3D printing. In manufacturing, low-run injection molds can be 3D printed from stiff, heat-resistant plastics instead of machined from metal, making them much cheaper and faster to produce.
Aerospace & aviation
3D printing can help you create stronger, lighter, and complex parts for aerospace and aviation applications, including jigs and fixtures, surrogate (or placeholder) parts, mounting brackets, and detailed, visual prototypes.
You can create these parts with several types of 3D printing technologies, including Fused Deposition Modeling (FDM), Stereolithography (SLA), Selective Laser Sintering (SLS), and Multi Jet Fusion (MJF).
3D printing is also helping way designers and engineers approach aerospace and aviation-related challenges in innovative ways, because they can use advanced engineering materials and complex geometries, consolidate assemblies into single parts, and achieve specific surface finishes or tight tolerances for applications ranging from part validation to medium-sized production runs.
Industrial machinery
Protolabs Network’s customers often use 3D printing to create prototypes, low-volume production runs, and parts with complex geometries for industrial machinery applications.
You can also use 3D printing to create specialized jigs and fixtures that can streamline machinery assembly – or even create durable components that are fit for hard-working, industrial environments.
You can also use 3D printing to create on-demand replacements for industrial machines, which can greatly improve efficiency on the production floor. What’s more, 3D printing allows for the creation of custom tools you can use to efficiently service or operate your industrial machines.
Consumer electronics
In the consumer electronics industry, Protolabs Network’s customers often use 3D printing to create prototypes of a part’s, component’s, or product’s design before it moves into full-scale production.
Our customers also use 3D printing to create durable housings for sensitive electronic parts that boast resistances to a variety of elements, such as heat and water. Additionally, 3D printing technology is a great choice to create small, custom batches of parts for consumer electronics, or to rapidly print spare parts on demand. This has the added bonus of simultaneously helping you work with reduced inventory and increase part availability to your customers.
Medical 3D printing
The medical industry is increasingly using 3D printing technology for applications like surgical guides, orthopedic implants, prosthetics, and patient-specific replicas of bones, organs, and blood vessels.
In fact, a 2015 study from Wohlers revealed that 13% of 3D printing revenue originates from medical-related organizations. There are also more than 20 different FDA-approved implants that are created with various types of 3D printing. This spotlights 3D printing’s growing role in an industry that relies on continuous innovation to provide patients with the best possible care.
Automotive 3D printing
In the automotive industry, automakers use 3D printing to test form and fit, to experiment with aesthetic finishes and make sure that all parts operate and interact as intended. It also provides a flexible solution for the quick turnaround of jigs, fixtures and grips; creating bellows; engineering complex ducting; and rapidly manufacturing complex, lightweight mounting brackets.
3D printing jewelery
There are a few reasons that so many designers use 3D printing to create jewelry. The technology allows jewelers to produce very complex, highly customizable designs, sidestepping some of the limitations of previously popular jewelry making techniques such as CNC machining, handcrafting and lost-wax casting. Today, precious metals can be 3D printed in a variety of patterns and designs quickly and cost effectively.
To learn more about the many different applications of 3D printing, check out these articles.
What are the benefits of 3D printing?
3D printing is an exceptional tool for custom parts and rapid prototyping with a unique set of advantages but also lags behind traditional manufacturing in some ways. The key benefits and limitations can be summarized as follows:
Benefits
- Very low start-up costs
- Very quick turnaround
- Large range of available materials
- Design freedom at no extra cost
- Each and every part can easily be customized
Limitations
- Less cost-competitive at higher volumes
- Limited accuracy & tolerances
- Lower strength & anisotropic material properties
- Requires post-processing & support removal
For a more thorough overview read our article about the benefits and limitations of 3D printing
The future of 3D printing
So where is 3D printing today? Is the hype over? Yes, and now the technology is reaching maturity. We’ve produced a 3D Printing Trend Report every year since 2017. Over those years we’ve watched the technology reach the height of the hype cycle, drop through the ‘trough of disillusionment, and bounce back to where it is now - on the ‘slope of enlightenment.
The hype of the previous years was based on the idea of widespread consumer adoption. This was a misleading interpretation of where the technology could add value to the world. The most promising applications of 3D printing are in very specific roles in the world of manufacturing.
To understand where 3D printing is headed in the next few years, consult the most recent version of our annual 3D printing trend report.
How to get something 3D printed
3D printing has come a long way since its inception and it’s now very easy to get something 3D printed quickly and affordably.
Buy a printer or use a 3D printing service?
3D printing has come a long way since its inception and it’s now very easy to get something 3D printed very fast for pretty cheap.
Should you buy your own 3D printer or use an online service? It’s an important decision to make, so we’ve collected arguments for both sides to help you make the right choice.
Buy a 3D printer if… | Use an online service if… |
---|---|
You need to print regularly, but not in huge volumes (10-25 times a week) | You will need only a few (less than 10) or large volumes (25+) of parts printed per week |
You have one specific application in mind for the printer | You want to print using multiple processes and materials, including industrial printers |
You are ready to make a sizeable investment | You want to access the latest technologies at all times |
You are prepared to set up, tinker and optimize your machine | You prefer to focus your time on designing and perfecting your models |
You have the necessary space and time to install and operate the printer | You want to test and learn first before deciding what printer to buy |
How to decide which 3D printer to buy
If you’ve decided it’s a good idea to buy your own 3D printer, you may be overwhelmed by the range of choices now available. To help people make sense of the 3D printer market, we reached out to our entire customer base and our global network of 3D printing service providers to find out about the 3D printers they own and their experiences in using them.
With reviews from more than 10,000 3D printer owners, who’ve completed about 1.48 million prints on 650+ different 3D printer models, our research is the most comprehensive 3D Printer Guide available.
How to use a 3D printing service
At Protolabs Network, we’re building the smartest manufacturing solution on the planet. One of our main offerings is our 3D Printing service.
When you upload a part to our online 3D printing service our proprietary pricing algorithm gives you a quote in a matter of seconds. As you specify your requirements the price will update automatically, and if you’re happy with the price and the lead times you can submit the order in just a few minutes.
Further reading
If you have more questions about 3D printing, check out our Knowledge Base and filter on ‘3D printing’ to see everything all at once.
The 3D printing handbook
If you’re interested in diving deeper into any of the topics covered above, we literally wrote the book on 3D printing. If you’re a professional looking to truly master the key aspects of 3D printing, this book is for you. It provides practical advice on selecting the right technology and how-to design for 3D printing, based upon the first-hand experience from the industry’s leading experts.
Here’s what Tony Fadell (creator of the iPod and founder of Nest) had to say about it:
“The Handbook” will help to guide you on your own path as you look to leverage 3D printing and its potential to create your own breakthrough products, that hopefully will change the world. Every designer and engineer should keep it close as it paves your way into new manufacturing technologies that will spur your creativity and unlock your ideas as they become reality. Creation is changing, manufacturing is changing and design is changing, turn the page, it’s time to stay ahead…
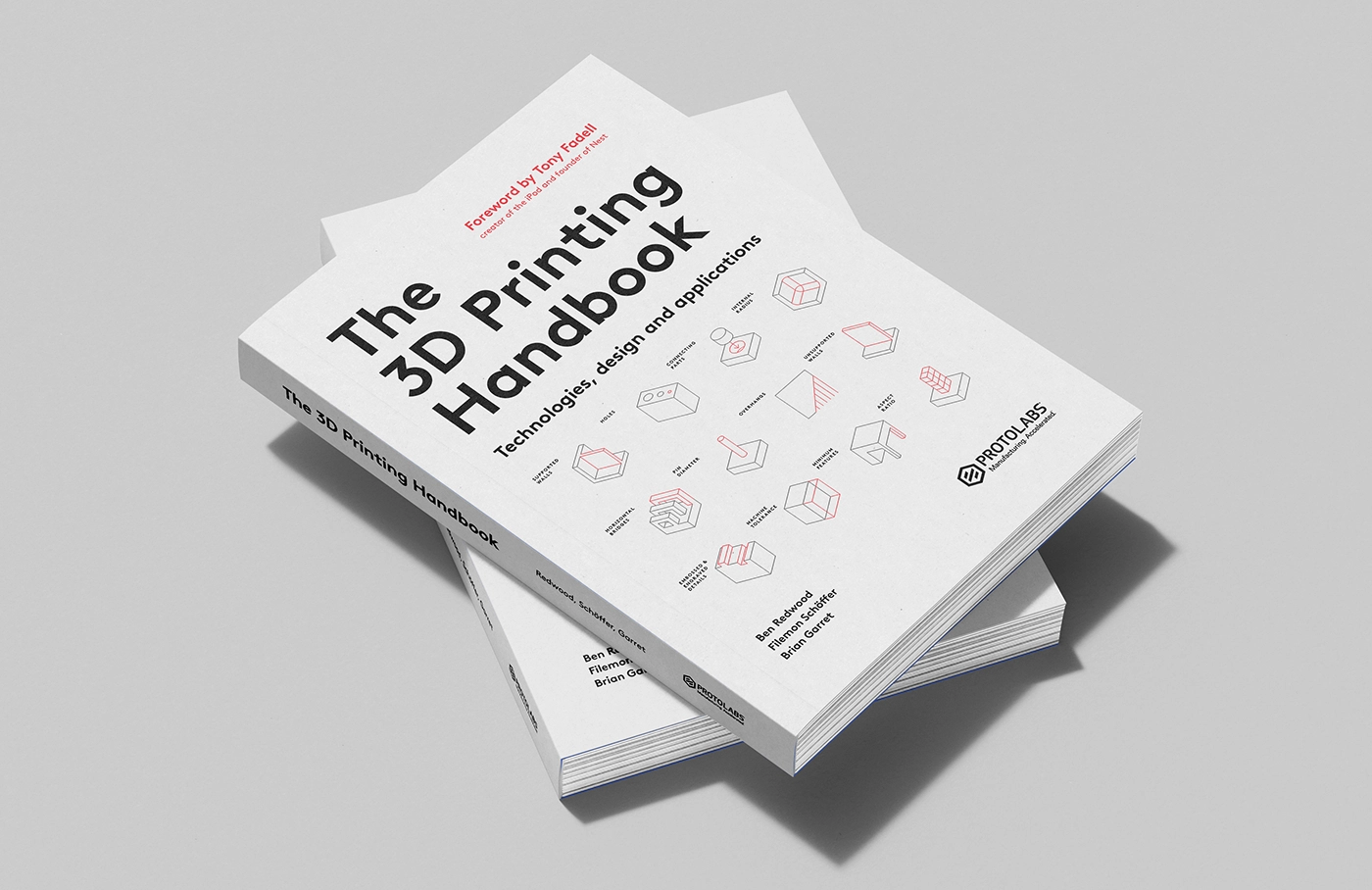
If you’re ready to purchase, The 3D Printing Handbook is available on Amazon. Or, if you like, you can download the first two chapters for free first.
Guides to other manufacturing technologies
Protolabs Network’s online manufacturing service offers more than just 3D printing. We also offer CNC machining, injection molding, and sheet metal fabrication, and to try to help our customers understand all these technologies we’ve written guides similar to this one for each of them.
Learn more about other manufacturing technologies
FAQs
How much does 3D printing an object cost?
3D printing a part or object can cost anywhere from a few dollars to thousands of dollars. Your design’s complexity, the material you want to create your part from, any necessary post-processing, and the time it takes to complete are all factors that can influence its cost.
How easy is 3D printing actually?
3D printing’s difficulty depends on how complex the part you want to create is, as well as the materials you use. Intricate or finely detailed designs, for example, are often more difficult to print than simpler ones. Additionally, some materials, like carbon fiber composites, are more difficult to work with than something more common, like PLA.
How often do 3D prints fail?
Incorrect print settings, poor bed adhesion, filament jams, design flaws, power interruptions, and other similar errors can cause a 3D print to fail. That said, you can take many steps to avoid 3D printing failures, such as using DFM techniques, working with an experienced manufacturer, and making sure that you are using the right type of 3D printing technology to create your part.
What is the biggest disadvantage of 3D printing?
3D printing can be relatively slow compared to other methods of manufacturing. This means it is not always as well-suited to large-batch production. However, 3D printing can be a great manufacturing method for custom parts and prototypes. As long as you pay attention to your part’s application – and choose a manufacturing method accordingly – you can avoid many of the disadvantages of the technology.