Let's start with the basics
Additive manufacturing (often referred to as rapid prototyping or 3D printing) is a method of manufacturing where layers of material are built up one at a time to create a solid object. While there are many different additive manufacturing and 3D printing technologies out there, this article will focus on the general process from design to the final part.
Whether the final part is a quick prototype or an end-use functional part, the general process does not change significantly. Let's get into it.
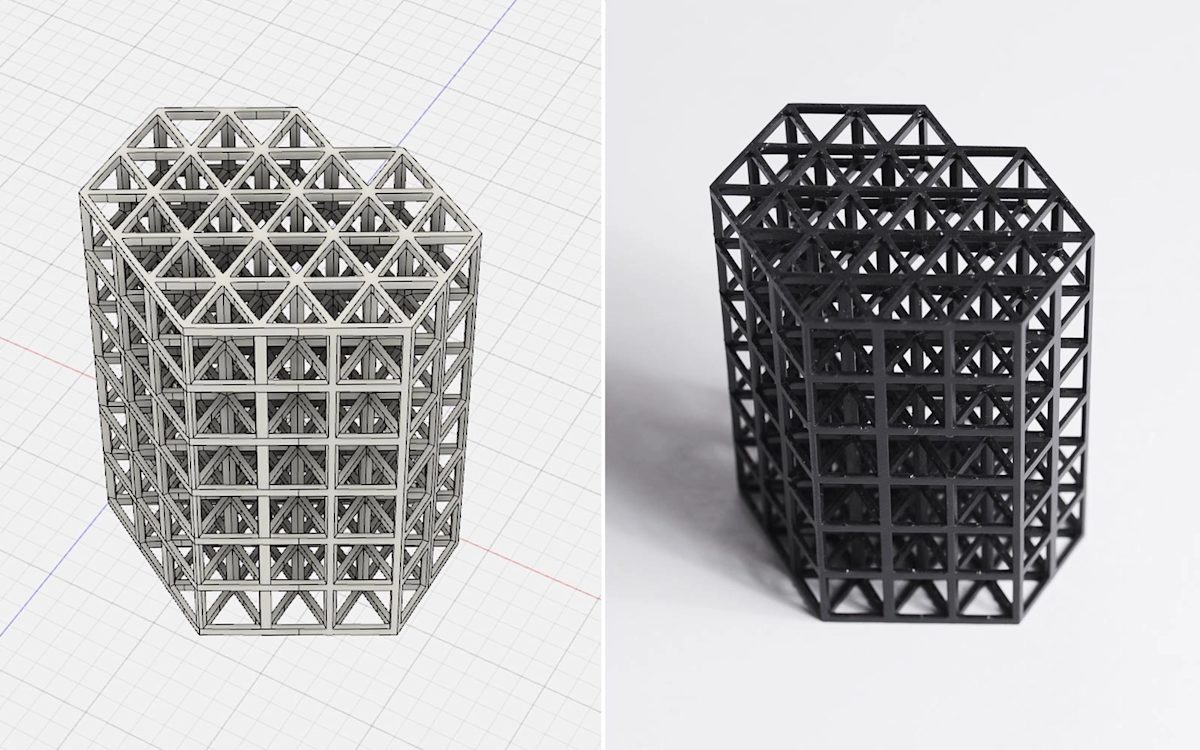
How do you design manufacturable models in CAD?
Producing a digital model is the first step in the additive manufacturing process. The most common method for producing a digital model is by using computer-aided design (CAD). There is an extensive range of free and professional CAD programs that are compatible with additive manufacturing technologies. Reverse engineering can also be used to generate a digital model via 3D scanning.
There are several design considerations that must be evaluated when designing digital models for additive manufacturing. These generally focus on feature geometry limitations and support or escape hole requirements, to name a few. Factors like these tend to vary by technology, so it’s essential to brush up on them.
What are STL conversion and file manipulation?
A critical stage in the additive manufacturing process that varies from traditional manufacturing is the requirement to convert a CAD model into an STL (stereolithography) file. STL uses triangles (polygons) to describe the surfaces of an object. A guide on how to convert a CAD model to an STL file can be found here.
There are several model limitations that should be considered before converting a model to an STL file, including the model’s physical size, water tightness and polygon count.
Once an STL file has been generated, the file is imported into a slicer program. This program takes the STL file and converts it into G-code, a numerical control (NC) programming language. It’s used in computer-aided manufacturing (CAM) to control automated machine tools (including CNC machines and 3D printers). The slicer program also allows the designer to customize the build parameters including supports, layer height, and part orientation.
How do additive machines produce custom parts?
Additive manufacturing machines (3D printers) comprise many small and intricate parts so correct maintenance and calibration are critical to producing accurate prints.
The raw materials used in additive manufacturing often have a limited shelf life and require careful handling. While some processes offer the ability to recycle excess build material, repeated reuse can reduce material properties if not regularly replaced.
Most additive manufacturing machines don’t need to be monitored after the print has begun. The machine will follow an automated process and issues generally only arise when the machine runs out of material or there is an error in the software. An explanation of how each of the different additive manufacturing printers produces parts can be found here.
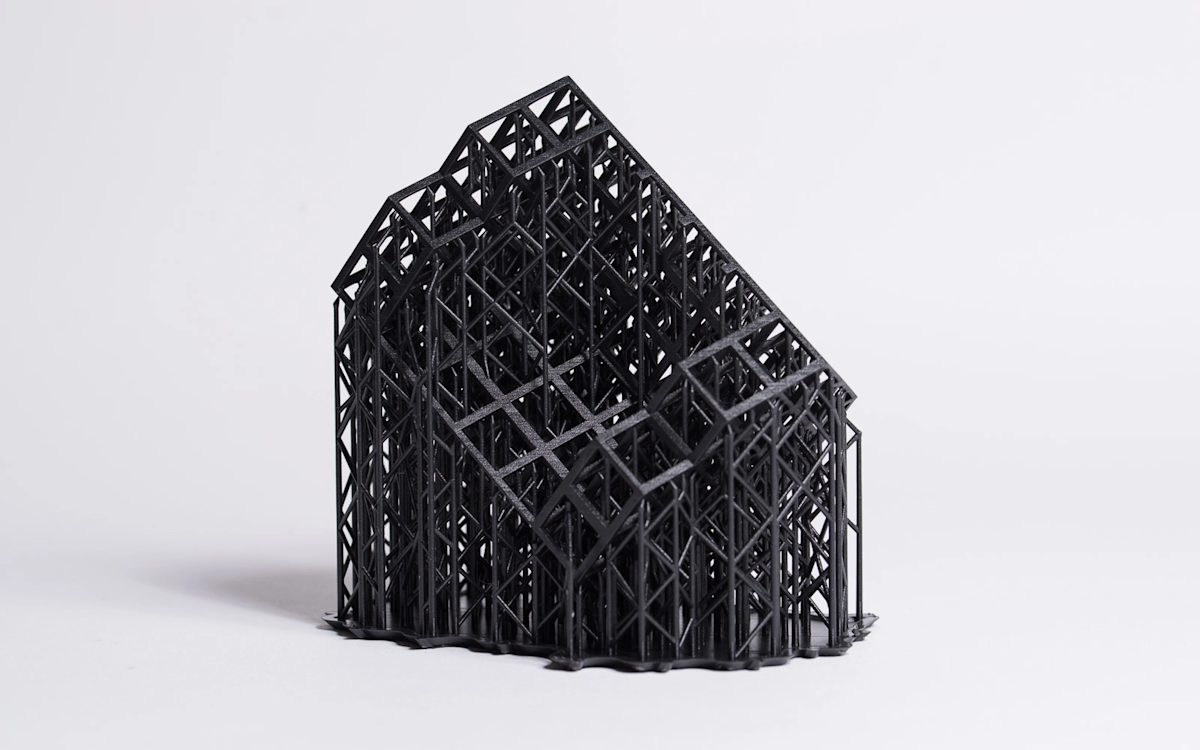
How and when do you remove prints?
For some additive manufacturing technologies removal of the print is as simple as separating the printed part from the build platform. For other more industrial 3D printing methods the removal of a print is a highly technical process involving precise extraction of the print while it is still encased in the build material or attached to the build plate.
These methods require complicated removal procedures and highly skilled machine operators along with safety equipment and controlled environments.
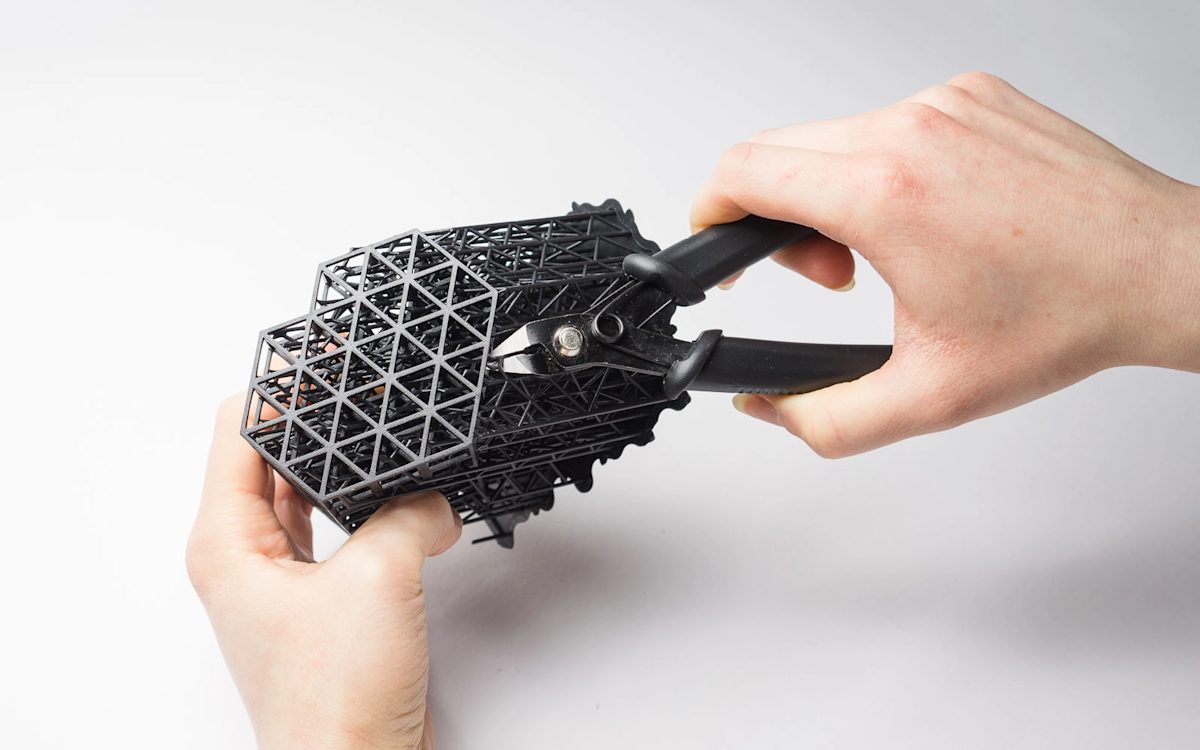
How does post-processing work for additive manufacturing?
Post-processing methods vary by printer technology. SLA printing requires a component to cure under UV before handling, metal parts often need to be stress relieved in an oven while FDM parts can be handled right away. For technologies that utilize support, this is also removed at the post-processing stage. Most 3D printing materials are able to be sanded and other post-processing techniques including tumbling, high-pressure air cleaning, polishing, and coloring are implemented to prepare a print for end use.
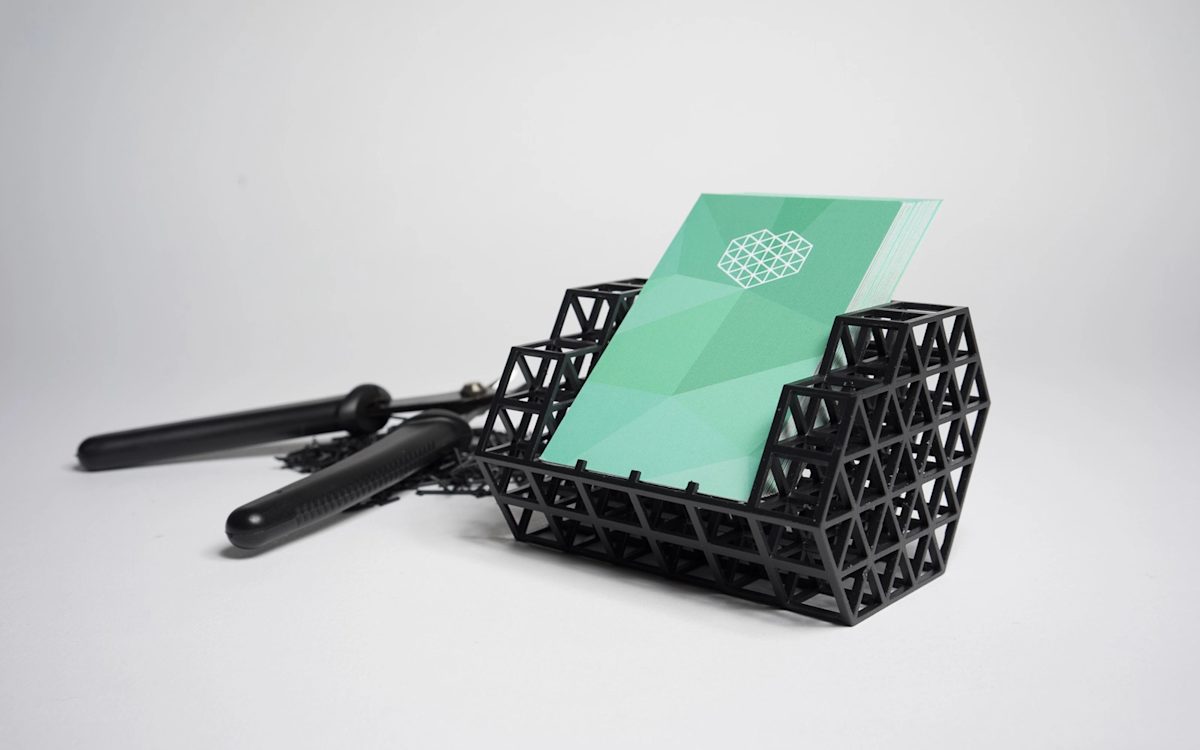
Ready to start 3D printing custom parts?
Frequently asked questions
What are the main additive manufacturing technologies?
There are seven technologies under the additive manufacturing umbrella. These are vat polymerization, material extrusion, material jetting, sheet lamination, directed energy deposition, binder jetting and powder bed fusion.
What’s the difference between additive manufacturing and 3D printing?
The terms additive manufacturing and 3D printing are, for the most part, interchangeable. Both refer to manufacturing processes where parts are built up layer by layer from a CAD design.
Are additive manufacturing and rapid prototyping the same process?
While additive manufacturing and 3D printing are often used interchangeably, rapid prototyping is a related but distinct process. Rapid prototyping refers to the accelerated prototyping stage of product development, with additive manufacturing being a process to support that aim.
Which industries commonly use additive manufacturing?
Additive manufacturing is used across a huge (and growing) range of industries, including aerospace, robotics, consumer electronics and automotive. One industry that’s benefitted immensely from the advent and widespread adoption of additive is medical technology. Historically, most industries have tended to use additive for prototyping, but with more robust technologies coming into the market, companies are turning to additive for end-use parts and higher volume production as well.
What are the advantages of additive manufacturing?
Additive manufacturing comes with many unique advantages. It’s a much more cost-effective way to create prototyping parts than subtractive processes, and it produces less material waste. The cost of entry is quite low and it’s cheaper for smaller and faster for production runs. Additive manufacturing is especially useful if you have to recreate legacy parts that you want to optimize.
What are the common materials used in additive manufacturing?
Additive manufacturing can create custom parts using polymers, metals and, in some cases, ceramics. The most common material you’ll see in additive manufacturing is plastic, especially for prototyping.