From launching satellites and manufacturing autonomous aircraft to fine-tuning flight systems, aerospace teams need parts that perform without compromise. CNC machining powers ideas that are ready for takeoff.
Why use CNC machining for aerospace-grade components?
CNC machining is used by engineers across the globe to produce high-performance aerospace parts because it combines precision, repeatability, and material versatility. In aerospace manufacturing, every micron counts. Whether it's landing gear that withstands dynamic loads, a turbine housing that needs thermal stability, or a UAV bracket that’s got to be featherlight and structurally sound, CNC machining provides the dimensional accuracy and surface finish required in mission-critical applications.
Aerospace components are typically produced in low to medium volumes but demand exceptionally high tolerances and consistent performance. CNC machining bridges this gap, allowing engineers to iterate quickly, qualify parts faster, and scale production while maintaining high part quality.
Here’s why CNC machining is a top choice across key aerospace components:
Extreme precision: Aerospace parts often require tolerances within microns. CNC machining delivers this level of detail with repeatability, which is critical for components like control arms, gear assemblies, and sensor housings.
Material flexibility: From titanium and stainless steel to high-performance aluminum alloys, there are a wide range of metals and plastics that can be CNC machined.
Design complexity: With multi-axis CNC capabilities, complex geometries such as airfoil profiles, mounting features, and pocketed designs can be accurately milled without needing too many changes to the setup.
Tight surface and dimensional control: Surface finishes like roughness average (Ra) less than 1.6 μm and uniform dimensional characteristics are required for effective fluid systems and structural joinery.
Production versatility: Whether it's a one-off prototype, a flight-ready part, or spares for maintenance and repair, CNC machining offers engineers a lot of flexibility.
Check out more CNC aerospace design tips and benefits in this quick video overview.
What makes CNC machining aerospace-grade?
Not all CNC machining is created equal. Aerospace-grade CNC manufacturing must meet strict requirements for safety, performance, and quality control. This includes:
-
Certification to AS9100, the leading quality standard for aerospace manufacturing
-
Material traceability from raw stock to finished part
-
Consistent quality control at every production stage
-
Detailed documentation and inspection reports
Protolabs Network is certified to AS9100, and many of our manufacturing partners are too, ensuring high standards for documentation, traceability, and quality assurance.
What types of aerospace parts can be CNC machined?
Aerospace manufacturers rely on a variety of technologies to build flight-ready parts, and the right process often depends on the part’s geometry, material, performance requirements, and production volume. While some parts, like internal panels or brackets with complex internal channels, may be better suited to injection molding or additive manufacturing, others are a clear match for CNC machining due to the precision, strength, and repeatability it offers. Below are examples of components where CNC is typically the best-fit solution
Engine components: These parts face high heat and pressure, so they’re usually made from strong metals like titanium or stainless steel. CNC machining delivers the precision needed to keep them working reliably.
Airframe brackets and structural parts: These need to be light but strong, often with tricky shapes. Five-axis CNC milling helps shape them accurately while reducing stress points.
Landing gear and control system parts: Because these parts take a beating from constant motion and stress, they need strong materials and extremely tight tolerances. CNC delivers both.
Custom housings and enclosures: Since these parts often hold sensors or electronics, everything needs to line up exactly, which CNC machining can achieve with repeatable accuracy.
Satellite and UAV components: These applications need to be lightweight and perform under extreme conditions. CNC machining gives engineers the control to fine-tune every cut and contour.
Learn more about how our aerospace manufacturing services support complex geometries, lightweight structures, and high-performance alloys.
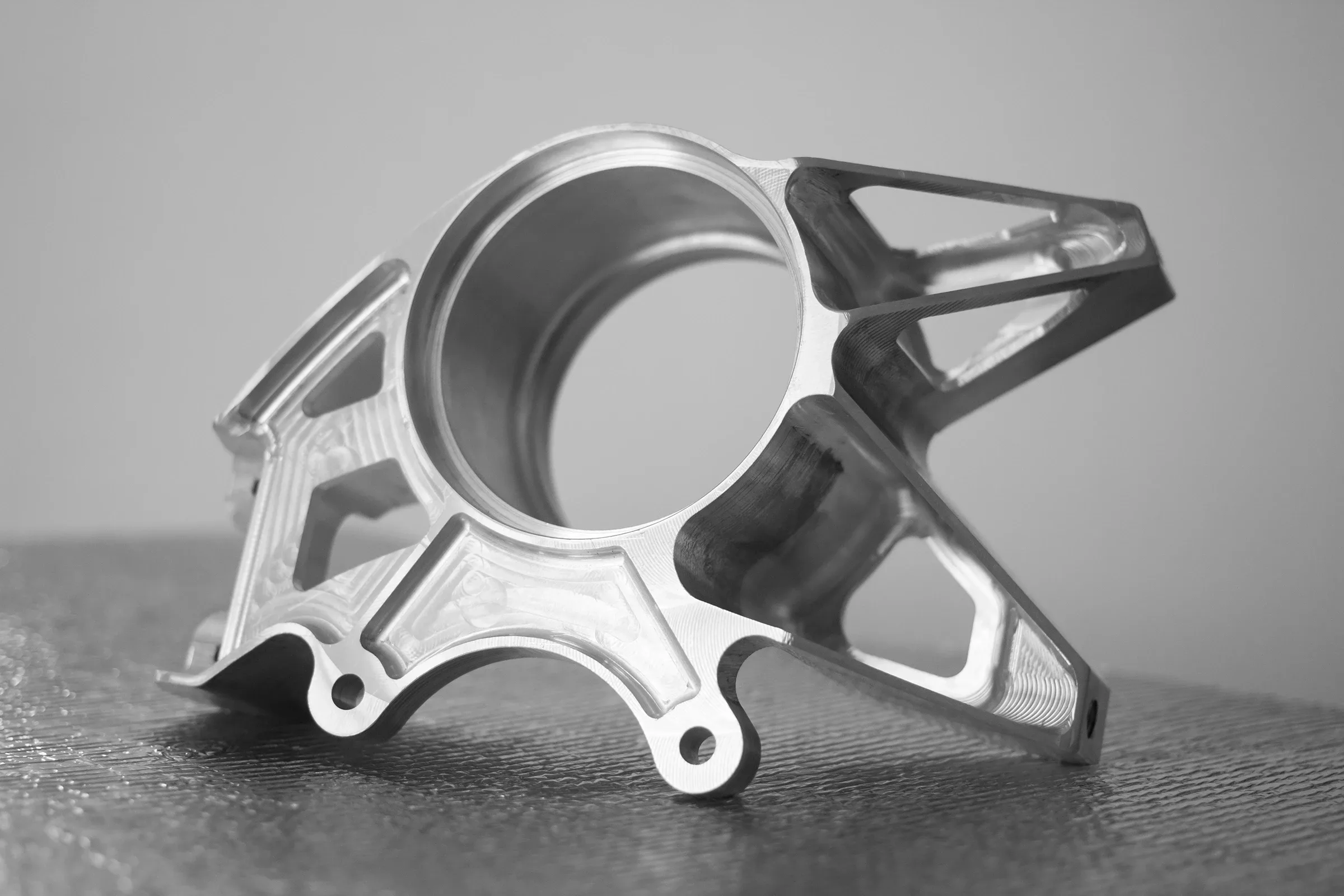
Benefits of on-demand CNC machining for aerospace
On-demand CNC machining is changing how aerospace teams bring parts to life. Instead of waiting weeks for quotes or tooling, engineers can quickly prototype, test, and revise designs in real time. This flexibility is especially valuable in aerospace development, where innovation is fast-paced, requirements can shift quickly, and every component must meet exacting standards. Key benefits of on-demand CNC machining include:
-
Faster design iteration: Engineers can test and revise parts quickly without the delays of traditional tooling and setup.
-
Shorter lead times: Get production-ready parts in days, not weeks, which is great for fast-moving projects or last-minute fixes.
-
Low-volume flexibility: Order only what you need, when you need it, without high minimum order quantities.
-
Easy prototyping-to-production transition: You can easily shift from prototype to pilot runs using the same manufacturing model.
-
Dynamic supply chain support: Fill gaps or manage spikes in demand without adding overhead.
-
Accessible quoting and sourcing: Tap into instant pricing, DFM feedback, and sourcing from a global partner network.
This agile approach is ideal for aerospace applications like drone development, flight system testing, and mission-critical part replacement. Engineers can move faster without compromising on quality or control.
Protolabs Network supports this model with access to a global network of AS9100-certified manufacturing partners—so you get the speed of on-demand production along with aerospace-grade reliability. You also benefit from full IP protection, instant quoting, and a network with near-limitless capacity to support prototyping, validation, and production at scale.
Watch this video on our CNC machining services to see how our global network supports aerospace production.
CNC aerospace parts in action
Here are just a few examples of how aerospace companies are using CNC machining to get their ideas off the ground:
CNC machining was used to produce lightweight, precision aluminum parts for the company's airborne wind energy system prototype.
CNC-machined components helped build modular research platforms designed to operate in microgravity aboard the ISS.
Kepler leveraged CNC machining to accelerate development of a satellite chassis from prototype to space-ready hardware, turning around parts within a single week.
What are the best materials for aerospace CNC machining?
Choosing the right CNC material can make a big difference in how well a part holds up under stress, heat, and vibration. The best material depends on the job—some need to handle high temps, while others need to be lightweight and corrosion resistant. Here's a quick look at the most commonly used materials, grouped by type:
-
Aluminum alloys: Known for high strength-to-weight ratio and excellent machinability, aluminum grades 6061, 2024, 2014, 7050, and 7075 are often used for structural components, housings, and brackets.
-
Titanium grades: Offering corrosion resistance and strength, Grade 5, Grade 2, and Grade 1 are used in turbine components, fasteners, and hydraulic systems. (See how it compares to aluminum).
-
Stainless steel: While all stainless steels offer strength and corrosion resistance, grade 17-4 is especially strong and wear resistant—ideal for landing gear and other structural aerospace parts.
-
High-performance metals: Inconel 718 is widely used for rocket components and engine parts because of its high strength and oxidation resistance in extreme temperatures.
-
Plastics: Many plastics can be CNC machined. Lightweight and resistant to heat and chemicals, Ultem 9085, Glass-Filled Nylon, PEEK, and PTFE (Teflon) are common choices where insulation, weight savings, or chemical resistance is key.
Additional materials and surface finishes may be available depending on your requirements. You can contact networksales@protolabs.com to discuss the options.
What are the best surface finishes for aerospace CNC machining?
Surface finish selection is just as critical as material choice. The right finish can protect against corrosion, improve performance, and meet regulatory or aesthetic requirements.
When choosing a finish, consider:
-
Material compatibility: Some finishes work only with metals (e.g., anodizing for aluminum).
-
Application requirements: Parts exposed to corrosion or chemical environments benefit from coatings.
-
Regulatory standards: Aerospace parts may require traceable finishing processes.
Below is a comparison of common finishes.
Surface finish | Benefit | Common materials | Applications |
---|---|---|---|
As-machined | No additional finish, tolerances held to machining spec | All CNC-compatible metals, plastics | Prototypes, internal brackets, tight-tolerance parts |
Bead blasting | Creates a uniform matte texture and removes minor imperfections | Aluminum, Titanium, Steel | Mounts, housings, cosmetic panels |
Polishing | Smooths surfaces for better aerodynamics or aesthetic finish | Titanium, Stainless Steel | Exterior casings, fluid-flow components |
Anodizing | Corrosion resistance, wear resistance, and color coding for aluminum | Aluminum 6061, 7075, 2024, Titanium | UAV structures, housings, external brackets |
Anodizing Type III | Harder, more wear-resistant coating than Type II for aluminum | Aluminum 6061, 7050, 7075 | Structural parts, brackets |
Chromate conversion coating | Adds corrosion resistance for aluminum/magnesium parts without affecting conductivity | Aluminum alloys | Electrical housings, structural frames |
Electroless Nickel Plating | Corrosion resistance, wear resistance, and uniform thickness | Aluminum, Steel, Inconel 718 | Gears, housings, electronic components |
Black Oxide | Mild corrosion resistance, reduced light reflection | Steel | Tooling, aerospace fixtures |
Brushing + Electropolishing | Smooth, clean finish with reduced contaminants | Stainless steel | Medical and aerospace fasteners |
CNC design tips for aerospace parts
Well-designed parts reduce production time, extend part life, and increase safety in critical aerospace environments. Aerospace engineers face unique constraints—including extreme temperature ranges, vibration, and weight limits—which require careful planning from the earliest stages of part design.
-
Keep it light (but strong): Use pockets, cutouts, and internal channels to reduce weight—just be careful not to compromise strength or increase vibration.
-
Make sure everything is accessible: Design your parts to be as easy to machine as possible. Avoid tricky shapes like deep, narrow cavities that require complex setups.
-
Stick to standard hole sizes: Using consistent fastener sizes and interface points makes parts easier to assemble and swap out.
-
Use rounded internal corners: This reduces tool wear, speeds up machining, and avoids weak points in the design.
-
Tolerance with intention: Only use tight tolerances where absolutely necessary. Over-specifying can make parts harder (and more expensive) to machine.
-
Think about temperature changes: Materials expand and contract with altitude and heat. Design parts to handle that without warping or failing.
-
Keep wall thickness consistent: This helps prevent distortion and improves structural strength.
Get more insights from our collection of articles about designing for CNC machining.
Alternatives to CNC machining in aerospace manufacturing
While CNC machining is essential for high-precision aerospace parts, it’s not the only game in town. Other manufacturing technologies offer advantages depending on part geometry, material, and volume.
-
Carbon DLS (available through Protolabs Europe) is great for lightweight lattice structures, high-performance elastomeric seals and gaskets, and fast-turn prototyping with no tooling required.
-
Additive manufacturing is ideal for producing lightweight, complex shapes without tooling.
-
Direct Metal Laser Sintering (also through Protolabs Europe) can print brackets, housings, and custom mounts in satellites and UAVs.
-
Injection molding is often used for high-volume plastic internal panels, electrical housings, and connectors.
Many aerospace teams combine technologies to get the best results—such as 3D printing a complex form and CNC machining it for final fit and precision. Choosing the right process depends on performance goals, production speed, and budget.
Where to learn more about CNC machining
Explore our Knowledge Base for in-depth CNC resources, or browse our latest case studies for real-world examples.
Ready to manufacture your next aerospace part? Upload your CAD file for instant pricing and DFM feedback.
Get startedHave a custom request or certification requirement? We can certify to AS 9100 D/ ISO 9001:2015. Contact your account manager or networksales@protolabs.com to learn more.