What is simulation software?
Simulation software is a digital sandbox for engineers. Instead of physically testing dozens of prototypes (and likely racking up a hefty bill in the process), you can virtually test how a part or system will behave under real-world conditions. Think of it like your own private lab where you can poke, prod, twist, heat, and cool your designs—all without ever hitting ‘print.’
In additive manufacturing, or 3D printing, simulation software helps you identify where a design might warp, crack, or fail before you commit to building a physical part. That’s essential for busy engineers who need to bring parts to life fast, efficiently, and reliably. By combining physics-based models with material data, simulation software offers a sneak peek into how your component will behave—and whether it’ll live up to your performance requirements.
Types of simulation software used in 3D printing
‘Simulation software’ can mean different things to different engineers. Below is a quick rundown of the most common simulations used in additive manufacturing.
Finite element analysis (FEA)
FEA breaks a part down into a grid (or mesh) and calculates how each small piece of that mesh reacts to forces—like stress, strain, or heat. If you’re designing a load-bearing bracket or an aerospace component with tight safety requirements, FEA is your new best friend.
Computational fluid dynamics (CFD)
CFD is your go-to for evaluating how air or fluid flows around and through a part. It’s especially helpful for designs that involve cooling channels or fluid transfer—such as heat exchangers or pump components—and can reduce drag or optimize airflow in complex geometries.
Multi-physics
Sometimes, one type of analysis isn’t enough. Multi-physics simulation combines several methods—such as thermal, structural, and fluid analyses—to give you the whole picture. Think rocket engines or custom medical implants that experience both mechanical stress and significant temperature changes. If your design involves a lot of moving parts (literally or figuratively), multi-physics can help you juggle them.
How is 3D printing simulation software used by different industries?
3D printing is a popular manufacturing method for everything from aviation components to wearable devices, but each industry harnesses simulation a bit differently.
-
Aerospace: Weight is everything in flight applications—every gram saved translates to performance gains. Simulation finds the balance between strength and mass, often using multi-physics to handle high-temperature environments and extreme stress.
-
Automotive: Automakers love 3D printing for rapid prototyping and even low-volume production of complex parts. Simulation focuses on thermal stresses, like engine components under heat, and vibration analysis, like with suspension components. By using FEA and CFD, automotive engineers can achieve durability while saving on prototyping costs.
-
Medical devices: Medical engineers often use additive manufacturing to create patient-specific implants and other custom devices. Simulation is critical here to ensure biocompatibility and structural integrity. Fluid-flow analyses may also come into play for implants like stents or pump housings.
-
Consumer electronics: In manufacturing, time is money, and that’s doubly true when it comes to consumer products. Every day spent on design tweaks is a day your competitor could be launching a similar product. Simulation helps rapidly validate design changes for everything from wearables to kitchen gadgets.
-
Industrial machinery: Big machines often operate continuously in harsh conditions. Simulation predicts the wear and tear that occurs over extended use. By spotting potential failures early, engineers can design parts that withstand repeated stress, cutting downtime and maintenance.
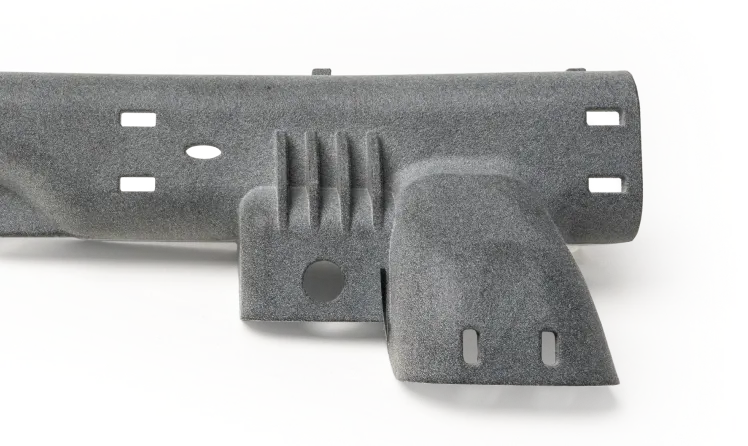
How simulation software enhances design accuracy in additive manufacturing
Simulation helps you validate and refine your design before barreling ahead with a physical build. By catching potential flaws early, you can reduce rework, scrap fewer parts, and make sure your final products meet performance requirements.
-
Predict warping: Warping is a common issue in 3D printing, especially with certain thermoplastics and metals. Simulation lets you see if—and where—warp might occur so you can adjust your design or printing parameters.
-
Optimize geometry: Pinpoint stress concentrations or potential distortions, then tweak wall thickness, lattice structures, or support placement.
-
Validate design readiness: Decide whether a part is ready for printing at all. Confirming geometry, thickness, and basic performance up front reduces the likelihood of major revisions later.
Reducing prototyping costs with simulation software
If you’ve ever had to scrap a half-finished metal part because of a faulty design assumption, you know how expensive mistakes can be. Simulation cuts down on these painful “back to square one” moments by letting you experiment in the digital realm.
-
Fewer physical prototypes: Virtual tests can replace numerous trial prints, saving on both materials and print time.
-
Material selection savings: Compare materials like ABS, nylon, or metal alloys in software. If a less expensive material meets your specs, you skip the cost of pricier alternatives.
-
Minimized trial-and-error: Run stress or thermal simulations so each physical prototype is already vetted, reducing the chance of costly reworks.
Accelerating time-to-market using simulation
When you’re racing to hit product launch dates, here’s how simulation can shave valuable days or even weeks off your timeline:
-
Early issue detection: Spot design flaws in the concept phase rather than halfway through production, preventing last-minute fire drills.
-
Fewer design revisions: Simulation pinpoints problem areas, keeping iteration cycles focused and efficient.
-
Faster approvals: Well-tested designs often pass internal or customer reviews more quickly, getting you to production sooner.
Enhancing manufacturing reliability with simulation tools in additive manufacturing
Simulation isn’t just for the first successful print—it also supports repeatability over time. Whether you’re producing multiple batches or scaling up for high-volume runs, simulation helps maintain consistency:
-
Consistent batch quality: Identify process variables—like residual heat or support placement—that might cause part-to-part deviations.
-
Scaling from prototype to production: A design validated by simulation at low volumes is easier to scale without worrying about unforeseen performance shifts.
-
Quality control checks: Advanced simulations can flag anomalies or potential defects early, heading off problems before they escalate.
Measuring ROI with simulation software
Beyond saving time and money, simulation provides tangible metrics that demonstrate its impact on your bottom line. Consider tracking:
Cost reduction
-
Scrap rate: Fewer failed prints translate to less wasted material and machine time.
-
Labor costs: Every design iteration requires engineering resources—simulation cuts that churn.
Faster time-to-market
-
Lead time: Note how often you finish projects more quickly after adopting simulation.
-
Accelerated launches: Earlier product releases often mean earlier revenue streams.
Improved accuracy
-
Defect rate: Predicting issues like warping or stress concentrations reduces out-of-spec parts.
-
Tolerances achieved: Monitor whether parts consistently hit their dimensional targets post-simulation.
Enhanced reliability
-
Maintenance frequency: Well-designed parts degrade more slowly, requiring fewer repairs.
-
Failure rate: Use simulation data to spot weak points before they lead to unplanned downtime.
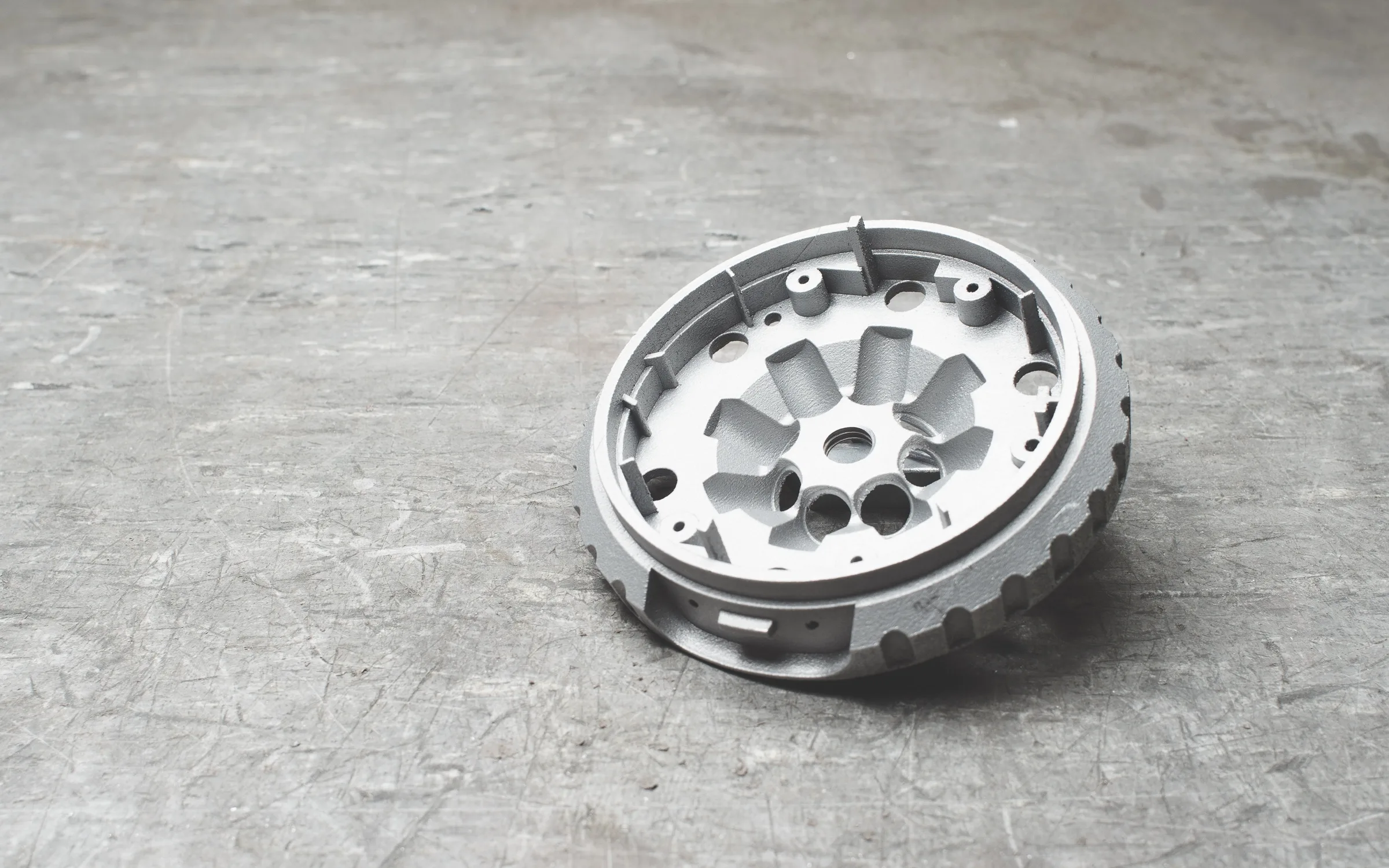
Integrating simulation software in on-demand manufacturing workflows
On-demand manufacturing services—like we offer at Protolabs Network—are all about efficiency. Engineers upload designs, receive instant quotes, and get parts produced on tight timelines. But where does simulation enter the picture?
-
Validate before quoting: Run your digital stress tests, thermal analyses, or flow simulations on your CAD model before uploading to the Protolabs Network portal. By identifying potential problems early—such as areas prone to warping or excessive stress—you minimize the risk of discovering issues only after you’ve placed your order.
-
Streamlined design iterations: Once you’ve received a quote, you can refine your design based on real-world feasibility and cost feedback. Use simulation to see if small tweaks (like changing wall thickness or adding support) can improve mechanical performance without ballooning your budget.
-
DFM checks vs. advanced simulation:Protolabs Network’s quote builder performs design for manufacturability (DFM) checks (e.g., thin walls or impossible overhangs). Pair these with your own advanced simulations (e.g., thermal distortion) for a solid virtual test bench.
-
Smooth data handoff: Many simulation platforms integrate with 3D modeling CAD software, so once your design is simulation-approved, it’s straightforward to export an STL or STEP file. Upload that final file to Protolabs Network, and you’ll have a head start on getting your part produced quickly and accurately.
Innovative trends in simulation software for the future of digital manufacturing
Simulation software is outpacing our expectations, opening new levels of collaboration, automation, and accuracy in additive manufacturing. Here are a few developments on the horizon:
-
Cloud-native ecosystems: Move heavy computations to the cloud, so engineers can collaborate remotely on complex analyses without worrying about local hardware limitations.
-
Generative & AI-driven design: Today’s algorithms go beyond suggesting minor tweaks to generating entire geometries that optimize weight, strength, and material usage. (Topic of interest? Here’s some further reading on the on-going debate about how far AI will push the 3D printing industry forward.)
-
Machine learning-based error detection: Some simulators learn from failed builds and can recommend design or printer adjustments, creating a feedback loop that improves outcomes over time.
-
VR/AR-assisted reviews: Engineers can virtually step inside the printing process, identifying potential problem areas in real time and making on-the-spot adjustments.
-
Closed-loop manufacturing: Post-processing and inspection data automatically loop back into simulations, helping machines and software correct course mid-production for even tighter tolerances and minimal downtime.
-
Digital twins: A digital twin is a virtual replica of a machine or an entire manufacturing process. Real-time sensors feed data back into the simulation, helping predict wear, part defects, and maintenance needs before they happen.
Where to learn more about 3D printing
Looking to build your knowledge base layer by layer? Protolabs Network offers extensive 3D printing design guides, deep dives into how 3D printing works, and advice on choosing the right 3D printing process for your project.
Get a quote
Ready to turn your validated design into a real-world part? Get a free, instant quote now.
Frequently asked questions
How do I pick the right simulation software?
Look at your part’s application, materials, and whether you need advanced features like CFD or multi-physics. If you’re only dealing with structural parts, FEA might suffice.
Do I need a high-powered computer to run simulations?
Not necessarily. Many solutions are cloud-based, offloading the heavy lifting. Complex analyses may benefit from a robust CPU/GPU setup, though.
Is simulation only for metal 3D printing?
Not at all. Simulation benefits plastic and resin parts too, each of which behaves differently. Just make sure your software supports your chosen material properties.
Does simulation replace physical testing entirely?
It can significantly reduce the need for physical tests, but final checks are still crucial—especially in regulated industries like aerospace or medical.