Need a part that fits right, performs reliably, and doesn’t take weeks to produce? CNC machining makes it happen. Engineers count on it for its tight tolerances, wide material compatibility, and fast turnarounds—no tooling required. Whether you’re prototyping or scaling up with production orders, CNC machining gives you full control over geometry, functionality, and surface finish.
Benefits of CNC machining
CNC machining offers engineers a fast and reliable way to go from CAD file to functional parts in just a matter of days. If you're new to the process, check out our overview of CNC machining as a manufacturing technology. Both 3-axis and 5-axis CNC machining have distinct advantages. Three-axis machining is efficient for straightforward geometries, while 5-axis CNC machining allows for greater freedom of movement, faster setups, and access to more complex surfaces. Here's why CNC continues to be one of the most popular manufacturing methods:
-
High accuracy: Operates with tolerances as tight as ±0.005 mm, ideal for high-performance parts.
-
Repeatability: Once programmed, CNC machines can produce the same geometry over and over again.
-
Fast lead times: Compared to tooling-heavy methods like injection molding, CNC machining can deliver parts in just a few days.
-
No tooling required: Great for prototyping or small-batch production where it is hard to justify the cost of molds or dies.
-
Material versatility: Works with metals like aluminum, steel, and titanium, and plastics such as nylon, PEEK, and POM. It can even handle certain composites likeglass-filled nylon andGarolite G-10.→ Need help choosing between aluminum and titanium? This guide breaks it down.
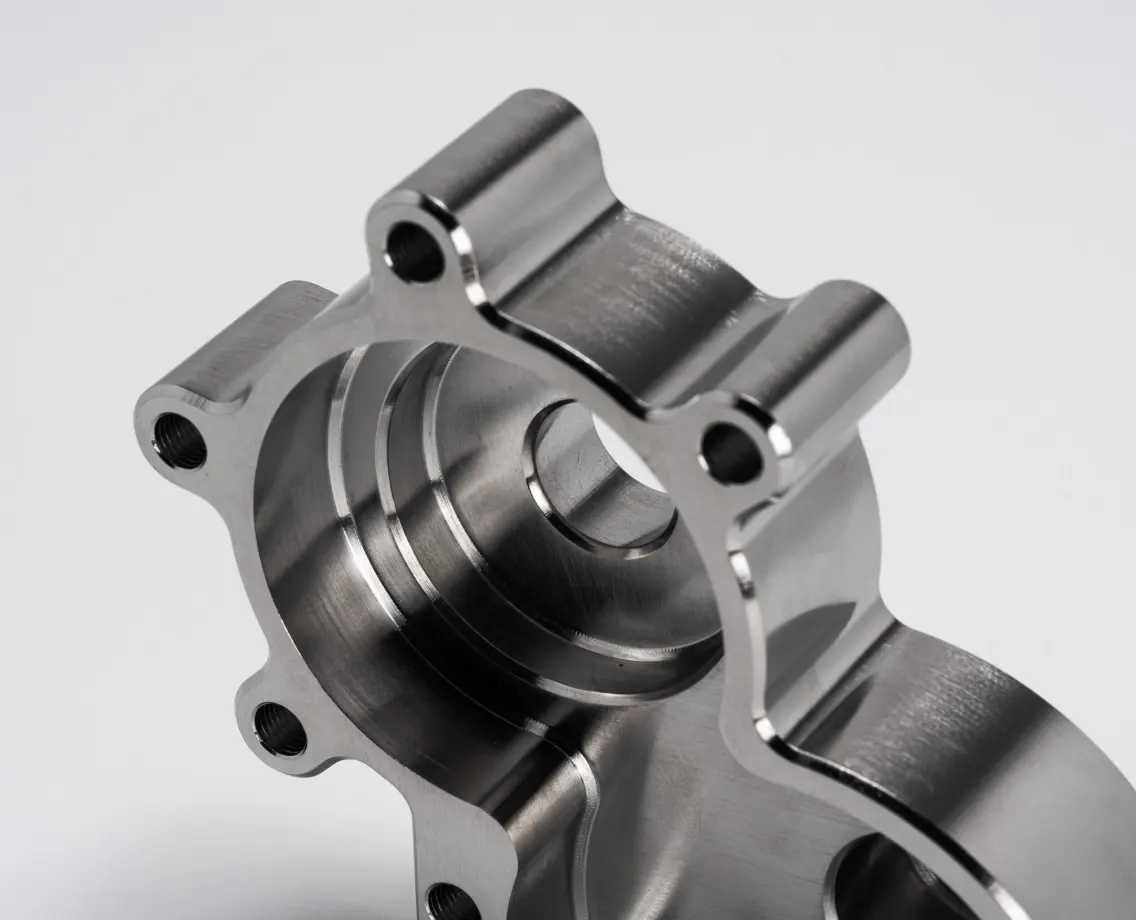
How the technology compares to other manufacturing methods
CNC machining is one of the most versatile manufacturing processes in the product development lifecycle. It’s often the best fit when you need tight tolerances, dimensional stability, and strong materials—especially metals—but don’t want to commit to tooling. As a subtractive process, it works for both functional prototypes and end-use parts. 3D printing typically comes first, during early iterations, for quick changes, and to manufacture complex internal features that would be hard to machine. Injection molding makes more sense for high-volume runs, where the tooling cost is offset by lower per-part pricing. CNC machining slots neatly in between—scalable enough for low-volume production, but precise and fast enough for prototyping, too.
-
If your part needs to be metal, strong, and accurate → CNC machining
-
If your part has internal lattices or organic shapes → 3D printing
-
If you're scaling to high-volume production → injection molding
Quick guide
Material | Strength:weight | Conductivity | Corrosion resistance | Machinability | Cost |
---|---|---|---|---|---|
Titanium | Excellent | Low | Excellent | Poor to Moderate | High |
Copper | Poor | Very high | Good | Excellent | Moderate |
Aluminum | Good | High | Good | Excellent | Low |
Brass | Moderate | Good | Good | Excellent | Moderate |
Stainless steel | Good | Low | Excellent | Moderate | Moderate |
Inconel | Excellent | Low | Excellent | Poor | Very High |
Examples of applications that are CNC machined CNC machining is a top choice when parts need to be strong, precise, and made from high-performance materials. Here are some of the most common part types where CNC outperforms other methods in speed, cost, or capability:
-
Custom brackets: Machined for high strength and stiffness, especially in aerospace and automotive builds.
-
Enclosures and housings: CNC ensures tight fits and smooth finishes to protect sensitive internal components.
-
Gears and drive shafts: These moving parts require perfect alignment and strength—ideal for CNC machining.
-
Heat sinks and optical mounts: Need the excellent thermal conductivity and flatness that CNC machining can provide.
-
Jigs and fixtures for assembly lines: Built to be rigid and custom-fit for repeatable positioning during production.
Use cases by key industries
CNC machining shows up in nearly every industry where parts need to be tough, pinpoint accurate, and built to last.
Aerospace: Engineers rely on CNC for brackets, linkages, housings, and engine parts made from strong, lightweight metals like aluminum and titanium.Airbus used CNC machining to create battery components with ultra-tight tolerances.
Medical: CNC machining is great for making implants, orthopedic tools, surgical jigs, and precision housings. Langefreunde used CNC to develop lightweight, modular wheelchairs.
Automotive: CNC is used for prototyping parts like valve covers, manifolds, and custom mounts. It’s also used in motorsports for end-use components. ETH Zurich’s Formula Student team chose CNC for critical race car parts that needed to be fast, strong, and reliable.
Electronics: Housings, connector blocks, and heat sinks are commonly CNC machined to lock in good thermal and EMI performance. Warwick Acoustics machined high-precision enclosures for their next-generation headphones.
Robotics and automation: CNC is used for arms, mounting plates, grippers, and enclosures with high stiffness and tight mechanical tolerances. Remotion created underwater components for their autonomous marine robots using this versatile process.
CNC machining for end-use parts
CNC is a reliable way to make final parts that need to be strong, consistent, and ready to use. Whether you're scaling up, tweaking a design, or producing a low-volume run, CNC can deliver the results you need.
-
Bridge production: A great solution before committing to injection molding. CNC helps validate your design and fill the gap between prototyping and full-scale production.
-
High-mix, low-volume runs: Need lots of part types in small quantities? CNC makes it easy to switch between designs quickly and affordably—no retooling required.
-
Custom parts: When each part needs slight changes—like in medical devices or robotics—CNC lets you build to spec without compromising precision.
-
Production parts: CNC machining is often used for final-use parts across aerospace, robotics, and medical sectors. These parts need reliable performance and repeatable quality.Here’s how to manufacture parts for production.
Is CNC machining the best process for your part? Upload a CAD file to get a free, instant CNC machining quote.
Get an instant quoteWhen not to use CNC machining
CNC isn’t always your best bet—there are projects that may be better served by a different process due to budget, speed, or design requirements. Here are the most common reasons to choose an alternative:
-
High-volume production: If you’re producing tens of thousands of identical parts, injection molding is usually more cost-efficient.
-
Complex internal geometries: 3D printing may be better for designs with internal channels, undercuts, or organic shapes.
-
Large part sizes: If your part is too big for the standard CNC machines, you’ll probably need to turn to casting or modular sheet metal fabrication.
-
Soft, flexible materials: Extremely elastic or rubber-like materials can be difficult to machine and are better processed through molding or additive techniques.
-
Cosmetic prototypes: If surface appearance is more important than material strength or precision, vacuum casting or finishing a 3D print can provide a polished look.
When CNC machining requires further processing
CNC-machined parts don’t always roll off the machine looking ready for the spotlight. To improve appearance and performance, you can opt for additional surface finishing services. Here are a few of the most popular finishes.
-
Anodizing: Corrosion resistance and optional color for aluminum.
-
Chromate conversion coating: Preserves conductivity in electronics.
-
Powder coating: Durable, colorful surface for metal parts.
Bead blasting: Smooths tool marks to produce a matte finish.
Want to drill deeper? Explore each process in ourCNC machining design guide, orupload your CAD file to see pricing and finishing options instantly.
Frequently asked questions
How precise is CNC machining?
Tolerances typically range from ±0.005 mm to ±0.01 mm, depending on geometry and material.
Is CNC machining only for metal parts?
No—many plastics like POM, nylon, PTFE, and PEEK can be CNC machined.
What are the best materials for CNC machining?
Aluminum, stainless steel, POM, PEEK, titanium, and brass are all popular for their machinability and performance.
What’s the typical lead time?
From 5 business days depending on part complexity, material, and quantity.
Can CNC-machined parts be used as final products?
Absolutely. Many engineers use CNC for end-use applications, especially in aerospace, medical, and robotics.