Subtractive manufacturing removes material from a solid block—also called a blank or workpiece—to form a final shape. As Michelangelo supposedly said of sculpting the David, "I just removed everything that was not David." Today, instead of chisels and marble, engineers use precision tools to shape metals and plastics with the same principle in mind.
Some of the most well-known subtractive methods include CNC milling, CNC turning, drilling, grinding, and laser cutting. While each technique removes material in a different way—milling uses rotating tools, laser cutting uses concentrated beams of light—they all carefully subtract material to match a final design.
This article covers how subtractive manufacturing works, how it compares to additive processes, the most common techniques, and how it's used today.
How does subtractive manufacturing differ from additive?
Subtractive manufacturing works by removing material from a solid block to create a final part, whereas additive manufacturing builds up a part layer by layer using raw material. Additive manufacturing includes a range of technologies—commonly called 3D printing—such as FDM, SLA, SLS, and MJF, each with different strengths depending on the material and geometry.
-
Subtractive manufacturing removes material to shape a part.
-
Additive manufacturing adds material to build a part.
Subtractive methods tend to offer better accuracy and smoother surface finishes for traditional part shapes, especially when tight tolerances or specific materials are needed. But when it comes to speed and cost for one-off parts, additive manufacturing often wins out—especially for intricate or internal geometries. CNC machining can take longer to set up, while a 3D printer might be able to crank out a prototype in just a few hours with minimal prep.
Many manufacturers use both subtractive and additive manufacturing depending on part requirements, cost, and speed. Sometimes they’ll even use both on the same project in hybrid workflows, where additive manufacturing might be used to make a rough form, then CNC machining perfects the final geometry. Imagine you're creating a custom bike stem. You want it to look slick and still be strong enough to meet your requirements. You could 3D print a rough draft, test the ergonomics, and then CNC machine the final part from aluminum to get a polished finish and high structural integrity.
If you want to dive deeper into how additive works, check out our article on additive manufacturing processes.
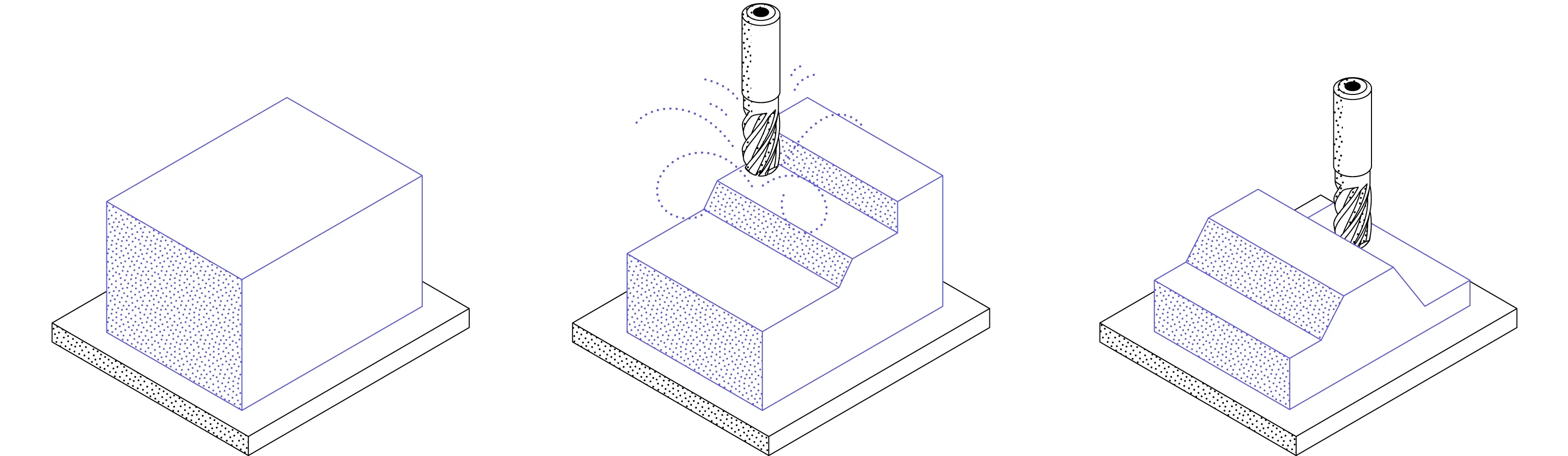
Subtractive manufacturing techniques
There are many types of subtractive manufacturing, but the most common techniques today fall under the umbrella of CNC (Computer Numerical Control). These processes take digital CAD files and convert them into toolpaths that cutting machines follow to create precise parts.
Here are some of the most widely used subtractive methods and how they work:
CNC milling
CNC milling uses rotating cutting tools to remove material from a fixed block. It's the go-to choice for creating complex 3D shapes, pockets, slots, and contoured surfaces. Some machines can move the cutting tool or part in several directions at once—known as multi-axis milling—so they can reach tricky angles and create more detailed shapes in a single run. If you've ever seen a bike frame with intricate metal brackets or a sleek laptop shell, there's a good chance it was made using CNC milling.
CNC turning
In turning, the workpiece spins while a stationary cutting tool shapes it. This process is perfect for producing round parts like shafts, bushings, and couplings. It's used in everything from automotive engine components to furniture fittings.
CNC drilling
CNC drilling creates holes in a workpiece using drill bits. It’s often used alongside milling or turning to add holes for fasteners, fluid passages, or alignment features. Think of the holes in a custom metal bracket or the threaded ports in a hydraulic manifold.
There are quite a few other subtractive methods, such as EDM (Electrical Discharge Machining), laser cutting, water jet cutting, and grinding. These techniques are a little more niche. While they may be better for specific materials or complex shapes, CNC milling and turning are the all stars of modern digital manufacturing.
If you want to learn more about how CNC machines work, head over to our article about What is CNC machining? to read up on the fundamental mechanics of this popular manufacturing method.
Recommended materials for subtractive manufacturing
Subtractive manufacturing supports a broad range of materials, making it one of the most flexible methods for product designers and engineers. Metals and thermoplastics are the materials most commonly used, but composites, foams, soft polymers, woods, and resins can also be machined. The material you should choose depends on how, when, and where you need your part to perform.
Popular material for subtractive manufacturing
Material |
Type |
Notable Properties |
Applications |
Metal |
Lightweight, corrosion-resistant, machinable |
Aerospace, automotive, enclosures |
|
Metal |
Strong, corrosion-resistant, hygienic |
Medical, food, marine |
|
Metal |
High strength-to-weight ratio, biocompatible |
Aerospace, implants, motorsports |
|
Plastic |
Tough, impact-resistant |
Prototypes, housings, fixtures |
|
Plastic |
Low friction, high stiffness |
Gears, bearings, mechanical components |
|
Plastic |
Chemically resistant, slippery surface |
Valves, seals, lab equipment |
Different materials have different machinability, which affects cost, speed, and the level of detail you can achieve. For help choosing the right one, take a look at our guide onselecting the right CNC material.
Common applications
Subtractive manufacturing is popular because it can be used to create strong components with consistent quality. Because it starts with solid blocks, it's also easier to predict how the final part will behave under load, making it a reliable choice for engineers working in demanding applications. Here are a few of the key industries that regularly rely on subtractive manufacturing for part production.
-
Automotive: Prototyping parts and producing low-volume components for custom and high-performance vehicles.
-
Medical: Producing surgical tools and patient-specific components.
-
Aerospace: Creating lightweight structural parts and testing units.
-
Industrial machinery: Making housings, shafts, brackets, and tooling components for heavy-duty production equipment.
-
Robotics and automation: Creating parts for actuators, mounts, end effectors, and sensor brackets.
-
Consumer products: Making functional prototypes and high-end parts.
It’s also common to use subtractive methods to post-process parts made by other technologies. For example, a part might be 3D printed for speed and affordability, then machined to add holes, slots, or threaded features.
Real-world examples of subtractive manufacturing
-
GB MEC used CNC machining to create specialized parts for yachts that would hold up to the volatile stresses and strains of the high seas.
-
Supernode CNC machined aluminum saddles to build components that played a key role in their innovative transmission technology.
-
Hone used CNC machining to craft beautiful, functional metal parts for their premium shaving razors.
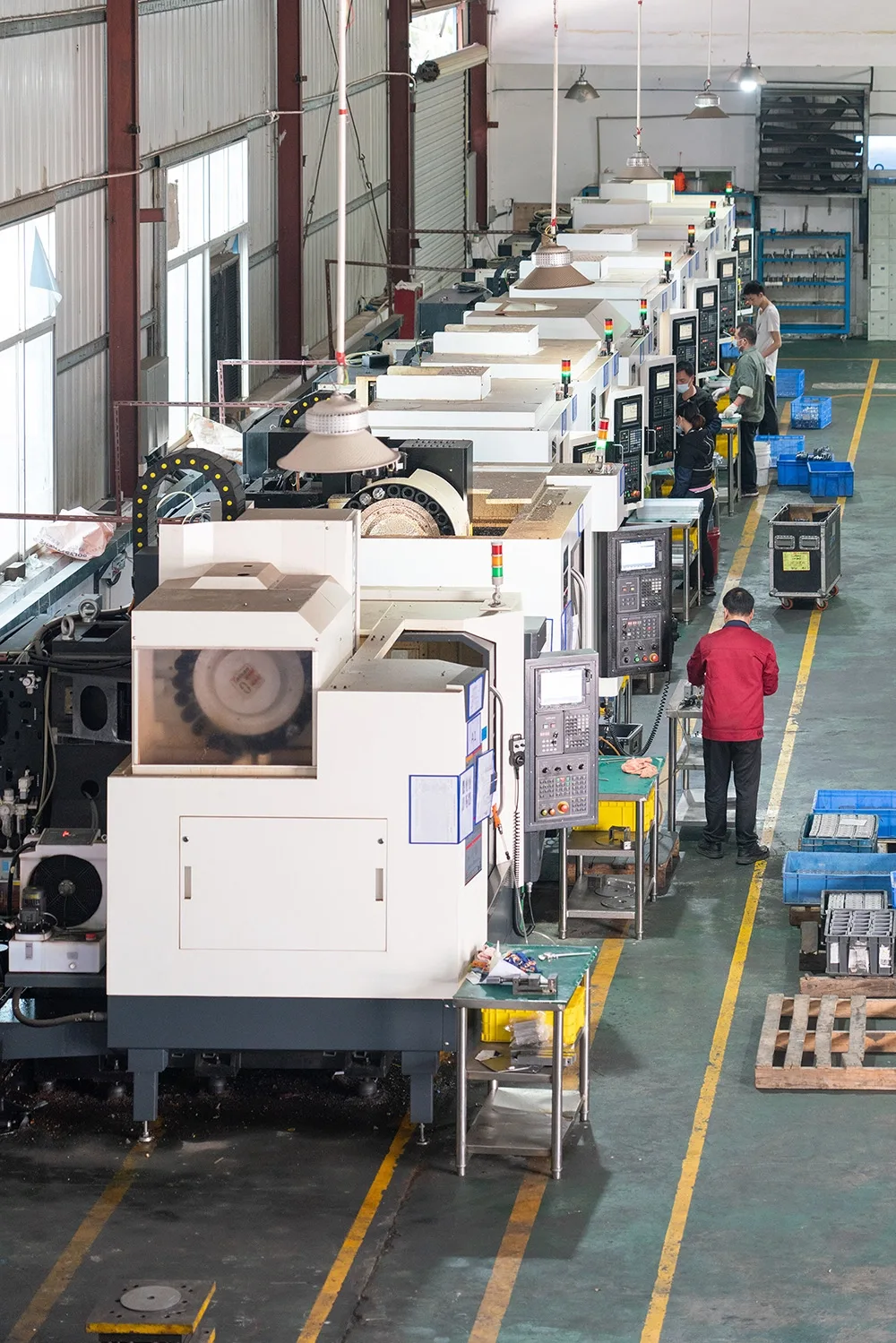
Advantages of subtractive manufacturing
Subtractive manufacturing really shines when you're aiming for parts that need to fit together precisely, perform reliably, and incorporate materials that can handle serious stress.
-
Tolerances: Subtractive processes can achieve excellent repeatability and precision for functional parts.
-
Surface finishes: These methods can produce the smooth surfaces required for cosmetic applications.
-
Material range: Compatible with a wide array of materials, including metals and high-performance plastics.
-
Turnaround speed: Works for fast production of simple to moderately complex parts.
-
Scalability: It is efficient for everything from one-offs to full production runs.
Limitations of subtractive manufacturing
Like any technology, subtractive manufacturing isn’t perfect. It comes with constraints around geometry, material waste, and setup complexity. In most cases, subtractive tools work from the outside in, so they're great for shaping external surfaces but aren’t the best for complex internal features that can't be reached by cutting tools. It’s well-suited for things like brackets, enclosures, or housings, but less ideal for lattice structures or embedded channels.
-
Material waste: Cutting away material generates scrap.
-
Limited geometry: Internal channels and undercuts are difficult or impossible.
-
Tool wear: Machining hard materials means more tool maintenance.
-
Setup costs: High-precision jobs may call for custom fixturing or multiple setups
Where to learn more about CNC machining
Want to drill deeper into subtractive manufacturing? Visit our fullCNC machining Knowledge Base to check out expert articles, design tips, and manufacturing insights. For a practical overview, read our Complete engineering guide to CNC machining to learn all you need to know in 25 minutes or less.
Get a quote
Ready to see how subtractive manufacturing can bring your ideas to life? Upload a CAD file to get a free, instant CNC machining quote.
Frequently asked questions
Is CNC machining the same as subtractive manufacturing?
CNC machining is just one type of subtractive manufacturing. There are many other subtractive processes, including EDM, laser cutting, and grinding.
What are the most common subtractive manufacturing methods?
CNC milling, turning, and drilling are the most commonly used subtractive manufacturing techniques today.
How does subtractive compare to 3D printing?
Subtractive is better for tight tolerances, aesthetic surface finishes, and structural materials. 3D printing, or additive manufacturing, is better for complex internal features and lightweight designs.
Can plastics be machined?
Yes! Engineering plastics like ABS, POM, and PTFE are commonly used in subtractive workflows.